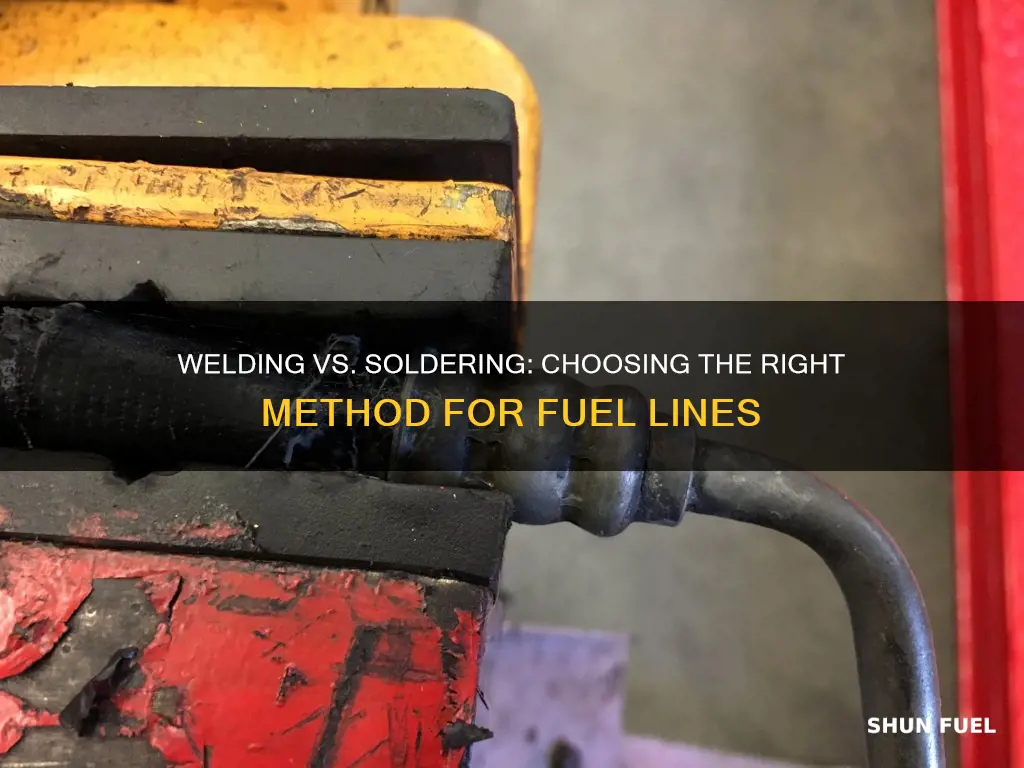
When it comes to working with fuel lines, it's crucial to understand the difference between welding and soldering. Welding is a process that joins two metal pieces together using heat and pressure, creating a strong and permanent bond. On the other hand, soldering involves using a metal alloy with a low melting point to create a joint between two metal surfaces. While both methods can be used to repair or modify fuel lines, it's essential to choose the right technique based on the specific requirements of the project. In this paragraph, we'll explore the pros and cons of welding and soldering fuel lines, as well as provide guidelines on when to use each method.
What You'll Learn
- Welding: Techniques for joining fuel lines using heat and pressure
- Soldering: Process of melting a metal alloy to join fuel lines
- Safety: Precautions to prevent fires and explosions during fuel line work
- Materials: Compatibility of welding and soldering materials with fuel
- Tools: Essential equipment for welding and soldering fuel lines
Welding: Techniques for joining fuel lines using heat and pressure
Welding fuel lines is a specialized process that requires precision and skill to ensure a secure and leak-free connection. This method is often employed when traditional soldering techniques are insufficient or when a more robust joint is needed. The process involves applying heat and pressure to the fuel lines to create a strong bond, which can be particularly useful for thicker or more robust fuel lines.
One common technique is gas welding, which utilizes a gas flame to heat the fuel lines. The welder must carefully control the flame to ensure the lines are heated evenly and to the correct temperature. This process requires a steady hand and a keen eye to avoid overheating or burning the surrounding materials. The heated lines are then brought together, and a filler material, often a compatible metal alloy, is added to create a strong joint. This method is effective for joining larger fuel lines and can provide a durable connection.
Another approach is oxy-fuel welding, which employs a mixture of oxygen and fuel gas to produce a high-temperature flame. This technique is advantageous for working with thinner fuel lines, as it allows for more precise control over the heat. The welder must carefully manage the gas flow and flame intensity to avoid damaging the lines. After heating, the lines are aligned and clamped together, ensuring a tight fit. This method is often used in automotive applications where fuel lines need to withstand high pressure and temperatures.
Welding fuel lines also requires the use of specialized welding rods or filler metals. These materials are carefully selected to ensure compatibility with the fuel lines and the surrounding components. The welder must consider factors such as the type of fuel, operating temperatures, and the overall system design when choosing the appropriate filler metal. Proper preparation of the fuel lines, including cleaning and removing any contaminants, is crucial to ensure a strong bond.
In addition to the welding process, post-weld inspections are essential. After the joint is made, it should be thoroughly examined for any signs of defects, such as porosity, cracks, or insufficient fusion. Non-destructive testing methods, such as ultrasonic or radiographic testing, can be employed to ensure the integrity of the weld. This step is critical to guarantee the safety and reliability of the fuel line connection.
Cummins Fuel Injection Lines: Unraveling the Mystery of Uniform Lengths
You may want to see also
Soldering: Process of melting a metal alloy to join fuel lines
Soldering is a precise and effective method to join fuel lines, offering a strong and durable connection. This process involves melting a metal alloy, typically a solder, to create a bond between two metal surfaces. When applied to fuel lines, soldering provides a reliable and leak-free connection, ensuring the safe and efficient transfer of fuel.
The process begins with preparing the fuel lines. Clean the surfaces where the connection is required, removing any dirt, corrosion, or old solder residue. This step is crucial as it ensures a strong bond. Then, apply a flux to the surfaces. Flux is a substance that helps to remove oxidation and provides a clean, smooth surface for the solder to adhere to. Common fluxes include rosin-based or acid-based types, each with its own advantages.
Next, select the appropriate solder. Solder is a metal alloy, usually a combination of lead and tin, with a lower melting point than the base metals. The choice of solder depends on the specific application and the materials of the fuel lines. For example, a 60/40 lead-tin solder is commonly used for joining copper or brass fuel lines.
To solder the fuel lines, heat the joint until the solder melts and flows. This is typically done using a soldering iron, a tool designed to provide controlled heat and precision. The iron's tip should be dipped into the solder, allowing it to melt and form a bead. Then, apply the solder to the joint, ensuring it comes into contact with both the base metals. As the solder melts, it creates a strong bond, fusing the two surfaces together.
After the solder has cooled and solidified, the joint can be tested for leaks. If no leaks are detected, the soldered connection is secure and ready for use. Soldering fuel lines requires skill and precision, but it is a valuable technique for creating long-lasting and reliable connections. It is an essential skill for anyone working with fuel systems, ensuring the safety and efficiency of the system.
Mastering VW Fuel Line Clip Removal: A Step-by-Step Guide
You may want to see also
Safety: Precautions to prevent fires and explosions during fuel line work
When working with fuel lines, safety is paramount to prevent fires and explosions, which can be catastrophic. Here are some essential precautions to follow:
Personal Protective Equipment (PPE): Always wear appropriate PPE, including heat-resistant gloves, safety goggles, and a respirator. Fuel lines often contain volatile substances, and any sparks or heat can ignite them. Protecting your skin and eyes is crucial, and a respirator ensures you don't inhale harmful fumes.
Ventilation: Ensure the work area is well-ventilated to disperse any potential fumes and prevent their accumulation. Working in a confined space without proper ventilation can lead to a dangerous buildup of flammable gases.
Fire Extinguishers: Keep a fire extinguisher nearby, specifically rated for fuel or flammable liquid fires. In the event of an accident, a quick response can prevent a minor incident from becoming a major fire.
No Open Flames: The most critical rule is to avoid any open flames or sparks in the vicinity. Never use a cigarette lighter, torch, or any heat source near the fuel line. Even a small spark can ignite the fuel, leading to an explosion.
Careful Handling: When welding or soldering, exercise extreme caution. Use only the necessary tools and equipment, and ensure they are in good condition. Avoid applying excessive force or pressure, as it can cause fuel to leak and create a hazardous situation. Always follow the manufacturer's guidelines for the specific fuel line material.
Additionally, it is essential to inspect the fuel lines regularly for any signs of damage or wear. Cracks, holes, or corrosion can lead to fuel leaks, which, when combined with sparks or heat, pose a significant fire hazard. Regular maintenance and prompt repairs are key to ensuring the safety of your vehicle and those around it.
Troubleshooting Clogged Fuel Lines: Common Causes and Solutions
You may want to see also
Materials: Compatibility of welding and soldering materials with fuel
When it comes to working with fuel lines, the choice of materials is crucial to ensure safety and efficiency. Welding and soldering techniques can be employed to join fuel lines, but the materials used must be compatible with the fuel to prevent any adverse reactions. The primary concern is to avoid any potential corrosion or degradation of the fuel line material that could lead to fuel leaks or contamination.
Welding, in this context, typically involves the use of heat and pressure to fuse two pieces of metal together. The materials commonly used for welding fuel lines include stainless steel, aluminum, and copper alloys. Stainless steel is a popular choice due to its excellent corrosion resistance and ability to withstand high temperatures. It is important to ensure that the welding process is carried out with the appropriate filler metal, which should also be compatible with the fuel to prevent any adverse chemical reactions. Aluminum and copper alloys are also used, but they may require specific welding techniques and filler materials to ensure a strong and durable joint.
Soldering, on the other hand, involves the use of a soldering iron to melt a solder alloy, which then creates a bond between two materials. Lead-based solder is commonly used for its ease of use and flow characteristics. However, lead is not ideal for fuel lines due to its potential health risks. Alternative solders, such as those based on brass or bronze, can be used, but they may not provide the same level of corrosion resistance as lead-based solder. It is essential to choose a solder that is compatible with both the fuel and the base metal to ensure a reliable joint.
The compatibility of welding and soldering materials with fuel is a critical aspect to consider. For example, some fuels, like gasoline, contain volatile organic compounds (VOCs) that can react with certain metals, leading to corrosion or the formation of harmful substances. Therefore, it is crucial to select materials that are resistant to corrosion and have a low tendency to react with the fuel. This may involve using materials with a protective coating or a specific alloy composition.
In summary, when working with fuel lines, it is essential to choose welding and soldering materials that are compatible with the fuel to ensure safety and performance. The selection of appropriate materials, such as corrosion-resistant alloys and compatible filler metals, is vital to prevent any potential issues related to fuel leaks or contamination. Proper preparation and understanding of the fuel's properties will also contribute to a successful and reliable fuel line repair or installation.
Exploring Rubber Fuel Line Hose Sizes: A Comprehensive Guide
You may want to see also
Tools: Essential equipment for welding and soldering fuel lines
When it comes to working with fuel lines, whether you're welding or soldering, having the right tools is crucial for a safe and effective job. Here's an overview of the essential equipment you'll need:
Welding Equipment:
- Welding Torch: A high-quality welding torch is the primary tool for joining fuel lines. Look for a torch with adjustable flame settings, allowing you to control the heat for different materials. Opt for a torch with a long handle for better control and reach, especially when working in tight spaces.
- Welding Shield: Eye protection is essential. A welding shield with a clear lens will protect your eyes from the intense light and heat generated during the welding process. Ensure it fits comfortably and provides a wide field of view.
- Welding Gloves: Heat-resistant gloves are vital to protect your hands from the torch's heat and sparks. Choose gloves with a good grip to maintain control while welding.
- Welding Mask: For more advanced welding, a welding mask with a shade suitable for the type of welding you're doing (e.g., shade 10-12 for mild steel) will provide additional protection and visibility.
Soldering Equipment:
- Soldering Iron: A soldering iron is the key tool for soldering fuel lines. Select one with a fine, non-magnetic tip for precise soldering. Adjust the temperature control to suit the material you're working with.
- Soldering Flux: This chemical agent helps create a strong bond between the fuel line and the solder. It also prevents oxidation, ensuring a clean connection.
- Solder: Use a high-quality, low-temperature solder designed for fuel line applications. It should melt at a temperature that won't damage the fuel line material.
- Heat Shield: A heat shield can be useful to protect nearby components from the soldering iron's heat.
- Wire Cutters and Strippers: These tools are essential for preparing the fuel line and solder for the soldering process.
Additionally, ensure you have a good supply of fuel line repair tape or clamp to temporarily secure the joint while it cools and hardens. It's also a good practice to have a fuel leak detector to verify the integrity of your work. Remember, when working with fuel, safety should always be the top priority. Proper ventilation and personal protective equipment (PPE) are essential to minimize the risks associated with fuel and heat.
Understanding the Differences: Diesel vs. Gas Fuel Lines
You may want to see also
Frequently asked questions
It is not recommended to use welding or soldering for joining fuel lines. Welding and soldering introduce heat, which can cause the fuel line material to degrade and become brittle over time. This can lead to cracks and leaks, potentially causing fuel leaks, which are dangerous and can lead to fires. It's best to use specialized fuel line connectors or crimping techniques for a secure and safe connection.
Applying heat to a fuel line connection can be risky. The high temperatures involved can cause the fuel line material to melt or become damaged, leading to potential fuel leaks. Additionally, the heat can affect the integrity of the fuel, causing it to degrade or become volatile, which is a fire hazard. It's crucial to use methods that do not involve heat to ensure the safety and reliability of the fuel line connection.
Yes, there are several alternative methods to join a fuel line. One common method is using specialized fuel line connectors, which are designed to create a secure and leak-proof connection without the need for heat. Crimping techniques, where the fuel line is compressed onto a fitting using a crimping tool, are also widely used. These methods ensure a reliable and safe connection without the risks associated with welding or soldering.