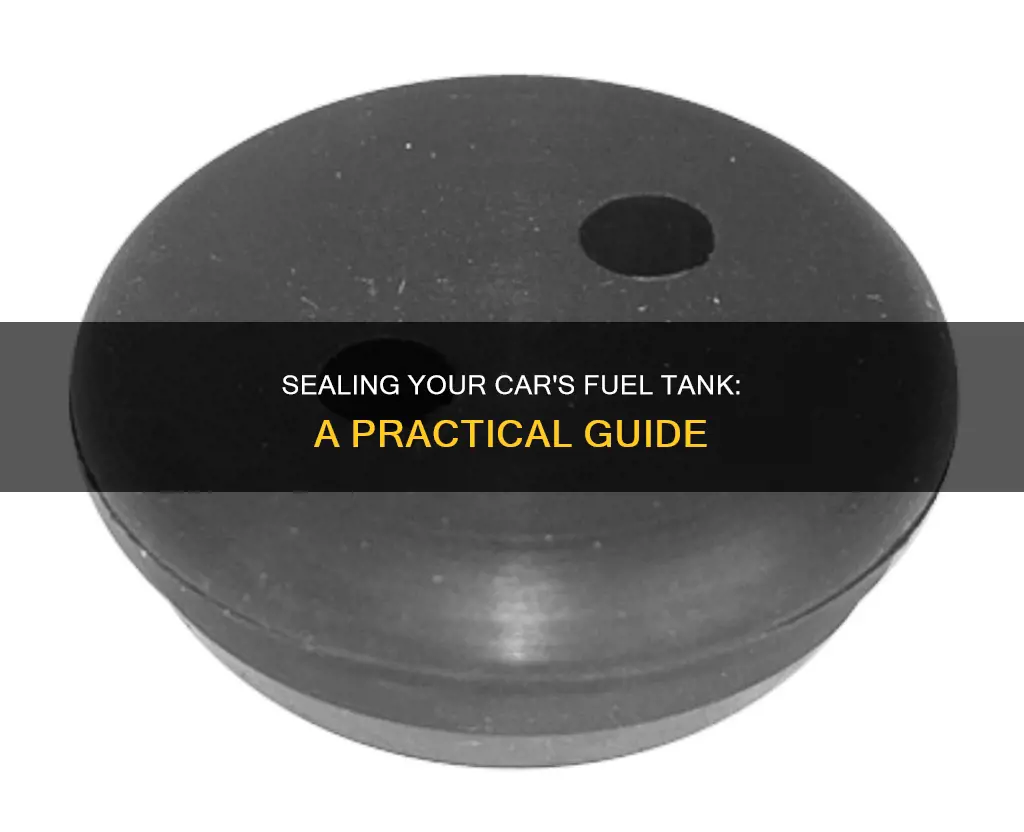
Sealing a fuel tank on a car is a common concern for vehicle owners, especially those who frequently drive in harsh weather conditions or in areas with limited access to fuel stations. The process involves ensuring that the fuel tank is properly sealed to prevent fuel leaks and maintain the integrity of the vehicle's fuel system. This can be achieved through various methods, such as using specialized seals, gaskets, or even professional services that focus on fuel tank maintenance and repair. Understanding the importance of proper sealing and the available options can help car owners make informed decisions to ensure their vehicles remain safe and efficient.
What You'll Learn
- Tank Material: Different materials (e.g., steel, aluminum) affect sealing methods
- Tank Design: Shape and size influence sealing techniques and compatibility
- Sealing Methods: Common methods include welding, bonding, and gaskets
- Fuel Type: Different fuels (gasoline, diesel) require specific sealing considerations
- Regulations: Industry standards and laws dictate acceptable sealing practices
Tank Material: Different materials (e.g., steel, aluminum) affect sealing methods
The material of a fuel tank plays a crucial role in determining the appropriate sealing methods. Different materials have distinct properties that influence how they can be sealed effectively. Here's an overview of how various tank materials impact sealing techniques:
Steel Tanks:
Steel fuel tanks are known for their durability and strength. When sealing steel tanks, the primary focus is on ensuring a tight, leak-proof connection. One common method is the use of welding. Gas welding or arc welding can be employed to join the tank's seams, creating a strong and permanent bond. This process is highly effective for steel tanks due to their ability to withstand high temperatures and pressure. Additionally, steel tanks often feature a protective coating, such as a zinc galvanizing or a specialized paint, which further enhances their resistance to corrosion and provides an additional barrier for sealing.
Aluminum Tanks:
Aluminum fuel tanks offer advantages in terms of weight reduction and corrosion resistance. Sealing aluminum tanks requires a slightly different approach compared to steel. One popular method is the use of adhesives specifically designed for aluminum. These adhesives create a strong bond between the tank and the sealing material, ensuring a tight seal. Aluminum tanks often utilize a process called 'sealing tape' or 'tape sealing,' where specialized adhesive tape is applied to the seams and joints. This tape is engineered to adhere well to aluminum and provide a robust seal. Another technique is the use of mechanical fasteners, such as screws or clips, in conjunction with specialized sealing compounds to secure the tank's components.
Composite or Plastic Tanks:
Composite or plastic fuel tanks are becoming increasingly popular due to their lightweight and corrosion-resistant properties. Sealing these tanks often involves the use of specialized adhesives and sealing materials. The choice of adhesive depends on the specific type of composite or plastic used. For example, epoxy-based adhesives are commonly employed for their ability to bond well with various composite materials. Additionally, heat-shrinkable sleeves or tubes can be used to seal the tank's seams, providing a tight and flexible seal. These sealing methods ensure the integrity of the tank while maintaining its lightweight nature.
In summary, the material of the fuel tank significantly influences the sealing process. Steel tanks often rely on welding and protective coatings, aluminum tanks utilize adhesives and sealing tapes, while composite or plastic tanks may require specialized adhesives and heat-shrinkable solutions. Understanding the material properties and selecting the appropriate sealing methods are essential for ensuring the safety and efficiency of fuel tanks in vehicles.
Unlocking the Mystery: Can You Put True Fuel in Any Car?
You may want to see also
Tank Design: Shape and size influence sealing techniques and compatibility
The design of a fuel tank in a vehicle is a critical aspect of automotive engineering, especially when considering the sealing requirements to ensure safe and efficient fuel storage. The shape and size of the tank play a pivotal role in determining the most suitable sealing techniques and compatibility with various fuel systems. This is particularly important as it directly impacts the overall performance, safety, and longevity of the vehicle.
In the context of sealing, the shape of the fuel tank is a key factor. For instance, a cylindrical tank, which is a common design, offers a smooth and continuous surface for sealing. This shape allows for the use of various sealing methods, such as gaskets or O-rings, which can be easily fitted around the tank's circumference. These seals are designed to create an airtight barrier, preventing fuel evaporation and potential leaks. The cylindrical design also facilitates the use of specialized sealing compounds that can be applied to the tank's interior to further enhance the seal's integrity.
On the other hand, tanks with more complex shapes, such as those with rounded or contoured surfaces, present unique challenges. These designs may require custom-made seals or specialized sealing techniques. For example, a tank with a curved surface might need a sealing solution that can conform to the shape, ensuring a tight seal. This could involve using flexible materials or implementing a sealing system that accounts for the tank's curvature. The goal is to maintain a secure and reliable seal while accommodating the tank's unique geometry.
Size also plays a significant role in tank design and sealing. Larger tanks, often found in heavy-duty vehicles or those with extended travel ranges, require robust sealing mechanisms. The increased volume of fuel necessitates a more substantial seal to prevent fuel loss and ensure the vehicle's overall performance. Engineers must consider the material properties and thickness of the seals to handle the additional pressure and potential fuel expansion. Moreover, larger tanks might require multiple sealing points or a more intricate sealing system to maintain the integrity of the fuel barrier.
In summary, the design of a fuel tank, including its shape and size, significantly influences the sealing techniques employed. Engineers must carefully select sealing methods that can accommodate the tank's geometry while ensuring compatibility with the vehicle's fuel system. This meticulous approach to tank design and sealing is essential for maintaining the quality of the fuel, preventing leaks, and ensuring the overall safety and efficiency of the vehicle's operation. Understanding these design considerations is crucial for anyone involved in the automotive industry, from engineers to manufacturers, to create reliable and safe fuel storage solutions.
Fuel Injector Cleaner: Unlocking Your Car's True Potential
You may want to see also
Sealing Methods: Common methods include welding, bonding, and gaskets
When it comes to sealing a fuel tank on a car, there are several effective methods to ensure a secure and leak-free closure. One of the most common techniques is welding, which involves joining two metal surfaces together using heat and pressure. This method is highly reliable and provides a strong, permanent seal. Welding can be applied to the fuel tank's lid or any other metal components that need to be sealed. It is crucial to use the appropriate welding technique and materials to ensure the integrity of the seal, especially in the presence of fuel, which can be corrosive.
Bonding is another popular sealing method, often used in conjunction with welding. This process involves using specialized adhesives or bonding agents to create a strong, permanent bond between two surfaces. Bonding can be particularly useful when dealing with non-metallic materials or when a more flexible seal is required. The bonding process typically includes surface preparation, application of the adhesive, and careful alignment of the components to be sealed. This method is widely used in the automotive industry and can provide excellent resistance to fuel leaks.
Gaskets are an essential component in sealing fuel tanks, especially when dealing with the fuel tank's lid or other openings. A gasket is a flexible, sealing material that is placed between two surfaces to create a tight seal. It is designed to withstand the pressure and temperature changes that occur in a fuel tank environment. Gasket materials can vary, including rubber, silicone, or even metal, depending on the specific application and requirements. Proper gasket installation is critical to ensure a reliable seal, and it often involves the use of specialized tools to ensure a tight fit.
In addition to these methods, other techniques such as soldering, clamping, and the use of specialized sealing compounds can also be employed. Each method has its advantages and is chosen based on the specific requirements of the fuel tank and the overall vehicle design. It is essential to follow manufacturer guidelines and industry best practices to ensure the safety and reliability of the fuel tank sealing process. Proper sealing not only prevents fuel leaks but also contributes to the overall performance and longevity of the vehicle.
Funny Cars vs. Top Fuel Dragsters: Who's Faster?
You may want to see also
Fuel Type: Different fuels (gasoline, diesel) require specific sealing considerations
When it comes to sealing a fuel tank on a car, the type of fuel used plays a crucial role in determining the appropriate sealing methods. Different fuels, such as gasoline and diesel, have distinct properties that require specific sealing considerations to ensure optimal performance and safety.
Gasoline, a volatile and flammable fuel, demands a meticulous sealing process. The sealing material should be compatible with gasoline to prevent any potential leaks or seepage. Rubber, for instance, is commonly used for gasoline tanks due to its flexibility and ability to withstand the fuel's corrosive nature. The sealing process involves carefully applying a high-quality rubber gasket or O-ring around the tank's opening, ensuring a tight and secure fit. This prevents gasoline from leaking and minimizes the risk of fire hazards.
On the other hand, diesel fuel, being less volatile and more lubricating, requires a slightly different approach. Diesel tanks often utilize sealing materials like rubber or synthetic compounds that offer excellent resistance to compression and abrasion. The sealing process involves creating a robust seal around the tank's opening, ensuring it can withstand the higher pressure and temperature variations associated with diesel fuel. This may include using specialized gaskets or sealing rings designed to handle the unique characteristics of diesel.
It is essential to consider the fuel's properties when selecting sealing materials to ensure compatibility and longevity. For instance, gasoline's corrosive nature may require sealing materials with enhanced chemical resistance, while diesel's higher pressure might necessitate materials with superior compressibility and durability. Proper sealing not only prevents fuel leaks but also maintains the integrity of the fuel system, ensuring efficient combustion and optimal engine performance.
In summary, sealing a fuel tank on a car requires careful consideration of the fuel type. Gasoline and diesel have distinct requirements, and the sealing process should be tailored accordingly. By using appropriate sealing materials and techniques, car owners can ensure the safety and reliability of their fuel systems, ultimately contributing to a smoother and more efficient driving experience.
Urine Power: Could It Fuel Our Future?
You may want to see also
Regulations: Industry standards and laws dictate acceptable sealing practices
The sealing of a fuel tank on a vehicle is a critical aspect of vehicle maintenance and safety, and it is subject to specific regulations and industry standards. These standards ensure that fuel tanks are sealed effectively to prevent leaks, which can have serious environmental and health implications. The regulations governing fuel tank sealing are designed to maintain the integrity of the vehicle's fuel system and to minimize the risk of fuel-related accidents.
Industry standards, such as those set by the Society of Automotive Engineers (SAE) and the American Petroleum Institute (API), provide guidelines for the design, construction, and testing of fuel tanks. These standards ensure that fuel tanks are manufactured to a high level of quality and safety. For example, the SAE J2040 standard specifies the requirements for fuel tank materials, design, and manufacturing processes to ensure structural integrity and prevent leaks. These industry standards are widely adopted and recognized, providing a consistent framework for fuel tank sealing across different vehicle manufacturers.
In addition to industry standards, there are also legal regulations that dictate acceptable sealing practices. These regulations are often set by government agencies and are designed to protect the environment and public health. For instance, the Environmental Protection Agency (EPA) in the United States has established regulations for the design and testing of fuel tanks to minimize the risk of fuel leaks and subsequent environmental contamination. These regulations may include specific requirements for fuel tank materials, sealing methods, and leak detection systems.
Compliance with these regulations is essential for vehicle manufacturers and repair facilities. Non-compliance can result in legal consequences, including fines and penalties, as well as potential liability for any fuel-related incidents. Therefore, it is crucial to adhere to the industry standards and legal requirements when sealing a fuel tank. This ensures that the fuel tank is sealed effectively, providing a safe and reliable fuel system for the vehicle.
Furthermore, the sealing process should be carried out by trained professionals who are familiar with the specific regulations and industry standards. They should use approved sealing materials and techniques to ensure a proper and long-lasting seal. Regular maintenance and inspections of the fuel tank sealing system are also recommended to identify and address any potential issues promptly. By following these regulations and industry practices, vehicle owners can ensure the safety and reliability of their fuel tanks.
Boost Your Car's Fuel Efficiency: Tips and Tricks
You may want to see also
Frequently asked questions
It is not recommended to permanently seal the fuel tank as it is an essential component for the car's operation. The fuel tank is designed to allow the fuel to flow in and out, ensuring the engine receives the required fuel for combustion. Sealing it could lead to fuel buildup, potential engine damage, and safety hazards.
Some car enthusiasts or those with specific modifications might consider sealing the fuel tank to enhance performance or for aesthetic reasons. However, this is generally not a standard practice and may require professional expertise to ensure it is done safely and effectively.
Yes, there are several risks. Firstly, it can lead to fuel pressure buildup, causing the fuel pump to fail or the fuel system to malfunction. Secondly, a sealed tank may result in fuel evaporation, leading to increased emissions and potential environmental concerns. Lastly, it can make it difficult to access the fuel for maintenance or repairs.
Regular maintenance is crucial. Ensure you use the recommended fuel type and keep the fuel tank clean. Check for any leaks or damage, and address any issues promptly. It is also advisable to have the fuel system inspected and serviced by a professional mechanic to ensure optimal performance and longevity.