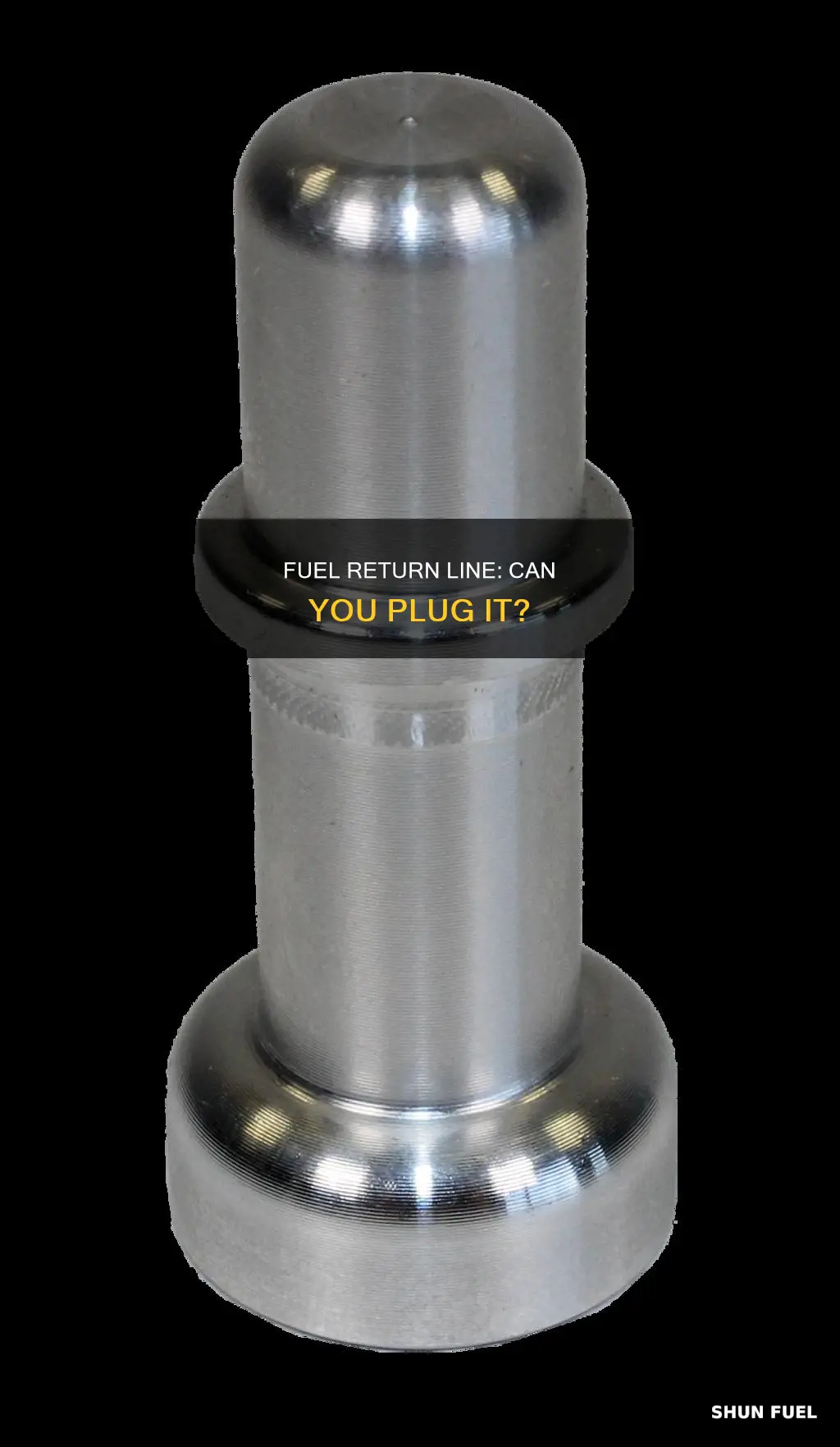
Can you plug a fuel return line? is a common question that arises when dealing with fuel systems in vehicles. This query often pertains to the maintenance and troubleshooting of fuel lines, which are crucial components in the fuel delivery process. When a fuel return line becomes damaged or leaks, it can lead to various issues, including reduced engine performance, increased fuel consumption, and potential safety hazards. Understanding how to properly plug or repair a fuel return line is essential for vehicle owners and mechanics alike to ensure optimal engine operation and prevent costly repairs.
What You'll Learn
- Fuel Return Line Basics: Understanding fuel return lines, their function, and common issues
- Diagnosing Leaks: Identifying fuel return line leaks through visual inspection and pressure testing
- Repair Techniques: Methods for repairing or replacing damaged fuel return lines
- Fuel System Compatibility: Ensuring the fuel return line fits the vehicle's fuel system
- Safety Precautions: Safety measures to take when working with fuel return lines
Fuel Return Line Basics: Understanding fuel return lines, their function, and common issues
Fuel return lines are an essential component of any fuel system, especially in vehicles and machinery that rely on efficient fuel management. These lines play a crucial role in ensuring that fuel is directed back to the fuel tank when it is not needed by the engine, thus optimizing fuel usage and preventing wastage. Understanding the basics of fuel return lines is vital for vehicle owners and operators to maintain their machines effectively and avoid potential issues.
The primary function of a fuel return line is to facilitate the flow of unused fuel from the engine back to the fuel tank. When the engine is not operating or during periods of low demand, excess fuel that would otherwise accumulate in the engine's lines and injectors is redirected through the return line. This process ensures that the fuel system remains clean and prevents the buildup of contaminants, which could lead to reduced engine performance and potential damage over time.
These lines are typically made of durable materials such as rubber or plastic, designed to withstand the pressure and temperature variations within the fuel system. They are often flexible, allowing them to navigate around various engine components without restricting fuel flow. The lines are connected to the engine's fuel injectors and the fuel tank, forming a closed loop that ensures efficient fuel management.
Common issues related to fuel return lines include clogs, leaks, and damage. Clogs can occur due to the accumulation of dirt, debris, or fuel contaminants, leading to restricted flow and potential engine performance problems. Leaks may develop at connections or due to worn-out gaskets, resulting in fuel wastage and potential safety hazards. Damage to the line, such as punctures or tears, can also cause fuel to leak and may require replacement. Regular maintenance and inspections are essential to identify and address these issues promptly.
In summary, fuel return lines are a critical part of the fuel system, ensuring efficient fuel management and preventing wastage. Understanding their function and potential issues is crucial for vehicle owners and operators to maintain their machines effectively. Regular maintenance and attention to these lines can help ensure optimal engine performance and longevity.
Unveiling the Causes: Why Fuel Line Leaks Happen
You may want to see also
Diagnosing Leaks: Identifying fuel return line leaks through visual inspection and pressure testing
When it comes to diagnosing leaks in fuel return lines, a systematic approach is essential to ensure an accurate diagnosis. Visual inspection is often the first step and can reveal a lot about the condition of the fuel return line. Start by examining the line for any visible signs of damage, such as cracks, punctures, or corrosion. Look for discolored or contaminated fuel, which could indicate a breach in the line. Inspect the connections and fittings for tightness and signs of leakage. If you notice any of these issues, it's crucial to address them promptly.
Pressure testing is a more advanced method to identify leaks. This process involves applying pressure to the fuel system and monitoring for any drops in pressure, which could indicate a leak. You can use a mechanical gauge or a specialized fuel pressure tester for this. Start by ensuring the engine is off and the fuel system is cool. Then, connect the pressure gauge to the fuel return line and apply a steady pressure. Observe the gauge for any fluctuations, as a steady pressure reading indicates a sealed system. If the pressure drops, it's a strong indicator of a leak, and further investigation is required.
To perform a pressure test, you can also use a method called the 'pressure decay test'. This involves sealing the fuel system and measuring the pressure over time. A drop in pressure indicates a leak. It's important to note that this test should be conducted in a controlled environment to ensure accurate results. Additionally, always follow safety protocols when working with fuel systems to prevent any accidents.
In some cases, a visual inspection combined with a pressure test can provide a comprehensive diagnosis. For instance, if a visual inspection reveals a potential issue near a fitting, a pressure test can confirm whether it's a leak or a tight connection. This two-pronged approach ensures a more accurate and efficient diagnosis. Remember, when dealing with fuel systems, it's crucial to be thorough and methodical to avoid missing any potential issues.
Mastering the Art: A Step-by-Step Guide to Removing Fuel Line Connectors from Nylon Hoses
You may want to see also
Repair Techniques: Methods for repairing or replacing damaged fuel return lines
Fuel return lines are an essential component of a vehicle's fuel system, responsible for directing excess fuel from the injectors or carburetor back to the fuel tank. Over time, these lines can become damaged due to various factors such as corrosion, clogs, or physical damage. When this happens, it's crucial to address the issue promptly to prevent further complications and ensure optimal engine performance. Here are some repair techniques to consider for damaged fuel return lines:
- Cleaning and Debris Removal: In some cases, the damage might be minimal, such as small clogs or debris buildup. A simple and effective method to repair this is by using a fuel line cleaner and a high-pressure air gun. Start by disconnecting the fuel return line from the fuel injectors or carburetor. Then, use the air gun to blow out any debris or clogs from the line. Ensure you work in a well-ventilated area and follow the manufacturer's instructions for the cleaner. After cleaning, reassemble the line and check for improved fuel flow.
- Cracked or Leaking Lines: If the fuel return line has developed cracks or leaks, it's best to replace it entirely. Start by draining the fuel system to avoid any spills during the repair. Locate the damaged line and carefully cut it a few inches away from the leak. Measure and mark the new line's length required for replacement. Purchase a replacement line with the appropriate fittings and connectors. Slide the new line into place, ensuring a tight fit. Secure it with the provided clamps or brackets, making sure it is properly aligned and taut.
- Soldering for Permanent Repairs: For more severe damage, such as a completely severed line, soldering can be an effective repair method. This technique is best suited for experienced individuals. Start by cleaning the ends of the fuel line and the fitting using a wire brush. Apply a flux to the fitting and the line, ensuring a good bond. Heat the fitting and line with a soldering iron, applying the solder in a continuous bead around the fitting. Allow it to cool and tighten the fitting securely. This method provides a strong and permanent repair but requires precision and skill.
- Professional Assistance: If the damage is extensive or you're unsure about performing the repairs yourself, it's advisable to seek professional help. Automotive mechanics have the expertise and tools to diagnose and fix fuel system issues accurately. They can use specialized equipment to pressure test the fuel lines, identify leaks, and make necessary replacements. Additionally, professionals can ensure that the repair is done safely and in compliance with vehicle manufacturer guidelines.
Remember, when dealing with fuel lines, it's crucial to prioritize safety and follow manufacturer recommendations. Always wear protective gear, work in a well-ventilated area, and dispose of fuel properly. If you're unsure about any step, consult a professional to ensure a successful and safe repair.
Mastering the Art of Removing Metal Clip Push Locks on Fuel Lines
You may want to see also
Fuel System Compatibility: Ensuring the fuel return line fits the vehicle's fuel system
When dealing with fuel systems, ensuring compatibility is crucial, especially when considering the installation or replacement of a fuel return line. This component plays a vital role in the overall functionality and safety of a vehicle's fuel system. The fuel return line is responsible for directing excess fuel from the fuel tank back to the engine or fuel pump, ensuring efficient fuel management and preventing wastage. However, it's essential to approach this task with careful consideration to avoid potential issues.
The first step in ensuring compatibility is to identify the specific make and model of the vehicle you are working on. Different vehicles have varying fuel system designs, and the fuel return line must be tailored to fit the unique requirements of each car. Consulting the vehicle's manual or manufacturer's guidelines is essential to gather accurate information about the fuel system's specifications. This includes understanding the type of fuel pump, the location of the fuel tank, and the diameter and routing of the existing fuel lines.
Once you have the necessary specifications, you can begin the process of selecting the appropriate fuel return line. It is crucial to choose a line that matches the internal diameter of the existing fuel lines to ensure a proper fit. Mismatched diameters can lead to fuel leaks, reduced performance, and potential safety hazards. Additionally, consider the length of the fuel return line. It should be sufficient to reach from the fuel tank to the desired connection point, typically the fuel pump or engine. Measure the distance accurately to avoid any unnecessary modifications or adjustments.
During the installation process, it is imperative to follow a step-by-step approach. Start by disconnecting the fuel lines from the fuel tank, ensuring you label or mark the connections for easy reattachment. Carefully route the new fuel return line, allowing for any necessary bends or adjustments to fit the vehicle's anatomy. Ensure that the line is securely attached to the fuel pump or engine using the appropriate clamps or fittings. Double-check all connections to guarantee a tight and leak-free seal.
After installation, it is essential to test the fuel system to ensure proper functionality. Start the vehicle and monitor for any signs of fuel leaks or unusual noises. Check for proper fuel flow and pressure to confirm that the fuel return line is functioning as intended. This testing phase is critical to identifying any potential issues before the vehicle is put back into service. By following these detailed steps and focusing on fuel system compatibility, you can ensure a successful and safe fuel return line installation.
Dodge Demon Fuel Line: Size Matters for Optimal Performance
You may want to see also
Safety Precautions: Safety measures to take when working with fuel return lines
When working with fuel return lines, it is crucial to prioritize safety to prevent accidents and ensure the well-being of both yourself and those around you. Here are some essential safety precautions to keep in mind:
Personal Protective Equipment (PPE): Always wear appropriate PPE when handling fuel return lines. This includes gloves to protect your hands from potential hazards and eye protection, such as safety goggles, to shield your eyes from any splashes or spills. Additionally, consider wearing a respirator mask to avoid inhaling harmful fumes, especially when working in enclosed spaces.
Ventilation and Work Area Preparation: Ensure that your work area is well-ventilated to minimize the risk of inhaling fuel vapors. If working in a confined space, use a fume hood or ensure proper ventilation to maintain a safe air quality. Clear the area of any potential trip hazards and make sure there are no open flames or sparks nearby, as fuel is highly flammable.
Fuel Handling and Transfer: When plugging or working with fuel return lines, handle the fuel with care. Avoid creating sparks or open flames, as this can ignite the fuel. Use non-sparking tools and ensure that any equipment you use is compatible with the fuel type. Always transfer fuel using approved containers and follow the manufacturer's guidelines to prevent overflow or spillage.
Leak Detection and Prevention: Prioritize leak detection and prevention to avoid hazardous situations. Inspect the fuel return lines regularly for any signs of damage, cracks, or leaks. If you notice any issues, address them promptly. Keep a supply of leak-detection solutions or indicators nearby to quickly identify any fuel leaks. In the event of a leak, have a plan to contain and clean up the spill, and ensure you have the necessary safety equipment, such as fire extinguishers, readily available.
Training and Awareness: Ensure that all personnel working with fuel return lines are properly trained and aware of the potential risks. Provide comprehensive training on safety procedures, including emergency response protocols. Encourage a culture of safety where employees feel empowered to report any hazards or concerns. Regularly review and update safety protocols to stay informed about best practices and any new developments in fuel handling and maintenance.
Chevy Cobalt Fuel Line Dimensions: A Comprehensive Guide
You may want to see also
Frequently asked questions
A fuel return line is a component in a vehicle's fuel system that allows excess fuel to be returned from the fuel tank to the engine's fuel supply. This line is crucial for maintaining proper fuel levels and ensuring efficient fuel management.
Plugging a fuel return line is generally not recommended and can lead to various issues. The primary purpose of this line is to facilitate the flow of fuel, and plugging it can result in fuel starvation, reduced engine performance, and potential damage to the fuel system.
Plugging the fuel return line can cause the fuel tank to become overfilled, leading to potential fuel spillage and safety hazards. It can also result in air entering the fuel system, causing engine misfires and reduced power. Additionally, it may lead to fuel pump issues and increased engine wear.
Plugging the fuel return line is typically not a recommended practice and should only be done in specific circumstances, such as during fuel system maintenance or when temporarily disconnecting the fuel tank for repairs. However, it's essential to follow proper procedures and consult a professional mechanic to ensure the work is done safely and effectively.