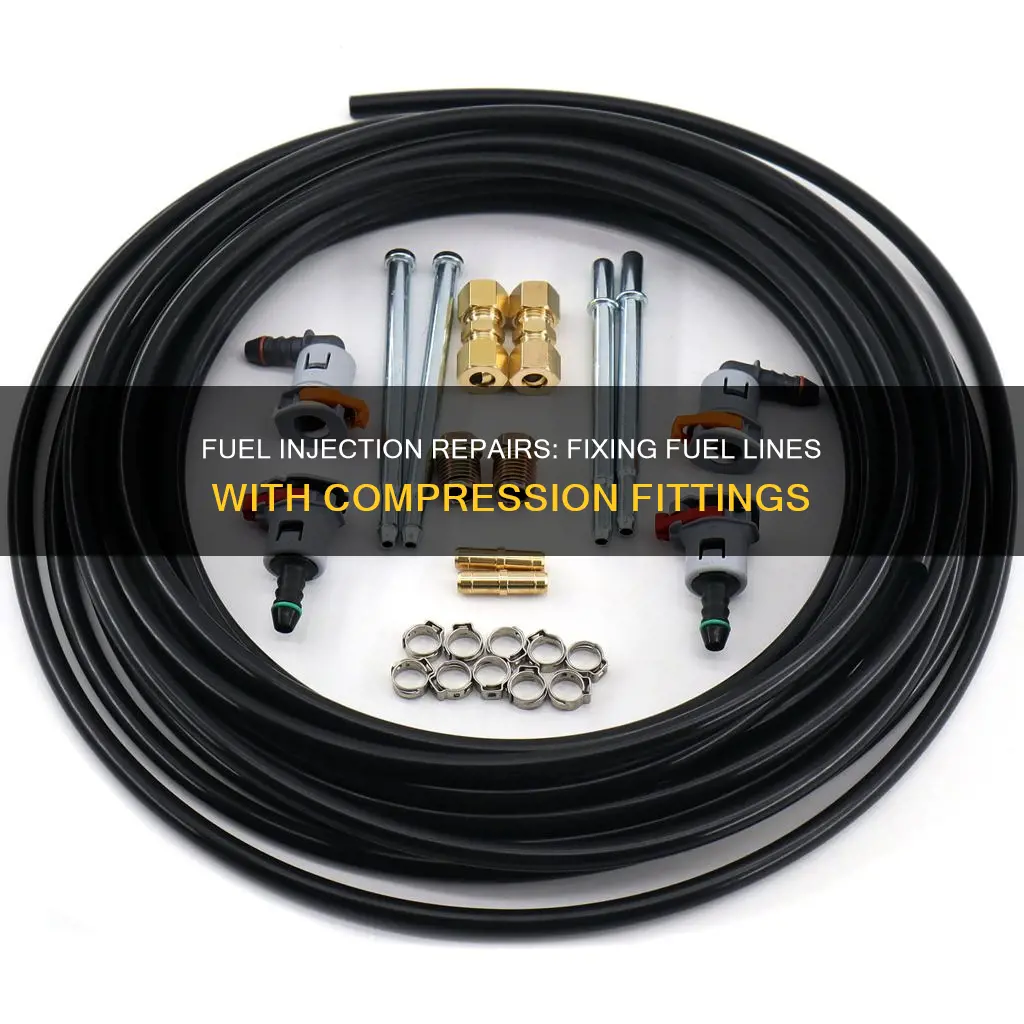
Fuel injection systems in vehicles rely on precise fuel delivery to the engine, and a crucial component in this process is the fuel line. Over time, these lines can develop leaks or become damaged, requiring repair or replacement. One common method to address this issue is by using a compression fitting, which provides a secure and reliable connection between the fuel line and the fuel injectors. This technique involves compressing the fitting onto the fuel line, creating a tight seal that prevents fuel leakage. By understanding the process of using compression fittings to fix fuel injection fuel lines, vehicle owners and mechanics can ensure optimal engine performance and longevity.
What You'll Learn
- Fuel Line Material: Choose the right material for the fuel line, considering compatibility and durability
- Compression Fitting Types: Understand different compression fitting styles for secure fuel line connections
- Fuel Injection System: Familiarize yourself with the fuel injection system's components and their roles
- Fuel Line Routing: Properly route the fuel line to avoid damage and ensure optimal flow
- Fuel Filter Maintenance: Regularly clean or replace fuel filters to prevent contamination
Fuel Line Material: Choose the right material for the fuel line, considering compatibility and durability
When it comes to choosing the right material for your fuel line, it's crucial to consider compatibility and durability to ensure optimal performance and longevity. The fuel line is a critical component in any fuel-injected engine, as it transports fuel from the tank to the engine's fuel injectors. Using the wrong material can lead to fuel leaks, engine misfires, and even potential fire hazards. Here's a detailed guide to help you make the right choice:
Compatibility with Fuel Type: Different types of fuel, such as gasoline, diesel, or ethanol blends, have varying chemical compositions. It's essential to select a fuel line material that is compatible with the specific fuel you are using. For example, rubber fuel lines are commonly used for gasoline engines due to their flexibility and resistance to gasoline solvents. However, for diesel engines, you might need a material like nylon or a reinforced rubber line that can withstand the higher pressure and temperature of diesel fuel.
Resistance to Fuel Components: Fuel lines should be able to resist the corrosive effects of various fuel components. Ethanol, for instance, can be harsh on certain materials, leading to degradation over time. Look for fuel lines made from materials like nylon, which offers excellent resistance to ethanol and other fuel additives. Similarly, if your fuel contains additives like detergents or corrosion inhibitors, ensure the chosen material can withstand these chemicals without compromising its integrity.
Durability and Flexibility: Fuel lines need to be durable enough to withstand the rigors of the engine environment, including temperature fluctuations, vibration, and mechanical stress. A good fuel line material should offer a balance between flexibility and rigidity to accommodate engine movement without cracking or breaking. Reinforced rubber or nylon lines often provide the necessary strength and flexibility. Additionally, consider the operating temperature range of your engine and select a material that can handle those conditions without becoming brittle or soft.
Standard Sizes and Fittings: Ensure that the fuel line material you choose is compatible with the standard sizes and fittings used in your engine. Different engine manufacturers may have specific requirements for fuel line diameters, bends, and connections. Using the correct fittings and ensuring a proper fit is essential for a reliable fuel supply.
Testing and Quality Control: When selecting a fuel line supplier or manufacturer, inquire about their testing procedures and quality control measures. Reputable companies will conduct rigorous testing to ensure their fuel lines meet industry standards and can withstand real-world conditions. This includes pressure testing, flexibility testing, and material compatibility assessments.
Remember, the fuel line is a safety-critical component, and using the right material is essential for the proper functioning of your fuel-injected engine. Always consult the vehicle's manual or seek advice from automotive experts to ensure you make the best choice for your specific application.
Unveiling the Car Fuel Line: Visual Guide
You may want to see also
Compression Fitting Types: Understand different compression fitting styles for secure fuel line connections
When it comes to repairing fuel injection systems, compression fittings are a popular and effective solution for securing fuel lines. These fittings provide a reliable and tight seal, ensuring that fuel is delivered efficiently without any leaks. Understanding the various types of compression fittings available is crucial for making the right choice and ensuring a successful repair.
One common type is the barbed compression fitting. This fitting features a barbed end, which is designed to grip the fuel line securely. The barbs are typically made of a durable material, such as brass or stainless steel, ensuring a strong and reliable connection. When installing, the fuel line is inserted into the fitting, and the barbed end is compressed around the line, creating a tight seal. This type is widely used due to its ease of use and ability to withstand high fuel pressures.
Another variation is the compression fitting with a ferrule. Here, a metal or plastic ferrule is crimped or compressed around the fuel line and the fitting. The ferrule acts as a mechanical seal, providing a tight grip. This style is often preferred for its versatility and ability to accommodate different fuel line diameters. It is important to ensure that the ferrule is properly installed and compressed to create an effective seal.
Compression fittings with a compression nut and sleeve are also available. This design involves a nut that tightens around the fitting, compressing it against the fuel line. The sleeve, typically made of a durable material, provides a smooth surface for the fuel line to slide into. This type offers a secure connection and is often used in high-pressure applications. Proper torque specifications should be followed during installation to ensure a tight seal without damaging the fuel line.
Lastly, compression fittings with a compression ring are designed with a ring-shaped compression surface that grips the fuel line. This style is known for its simplicity and reliability. The fuel line is inserted, and the compression ring is tightened, creating a secure seal. These fittings are commonly used in automotive applications and are appreciated for their durability.
In summary, understanding the different types of compression fittings is essential for successful fuel line repairs. Each style offers unique advantages, and choosing the right one depends on factors such as fuel line diameter, pressure, and the specific requirements of the vehicle's fuel injection system. With the right compression fitting, you can ensure a secure and efficient fuel delivery system.
Step-by-Step Guide: Removing the Fuel Line on Your 2007 Chevy Suburban
You may want to see also
Fuel Injection System: Familiarize yourself with the fuel injection system's components and their roles
The fuel injection system is a complex network of components that work together to deliver the right amount of fuel to the engine's cylinders, ensuring optimal performance and efficiency. Familiarizing yourself with its key components and their functions is essential for anyone working on a vehicle with this system. Here's an overview:
Fuel Pump and Reservoir: The fuel pump is a critical component located within the fuel tank or close to it. It draws fuel from the reservoir and pressurizes it to create a consistent flow. The reservoir stores the fuel and often has a strainer to filter out any contaminants. This system ensures a steady supply of fuel to the engine, which is crucial for its operation.
Fuel Injectors: These are the heart of the fuel injection system. Fuel injectors are small, precise devices that spray a fine mist of fuel into the engine's intake manifold or directly into the combustion chamber. Each cylinder typically has its own injector, and they are controlled by the engine's electronic control unit (ECU). The ECU calculates the exact fuel amount required based on engine speed, load, and other parameters, ensuring efficient combustion.
Intake Manifold and Throttle Body: The intake manifold is a crucial part of the air-fuel mixture preparation process. It receives fuel from the injectors and mixes it with air drawn through the throttle body. The throttle body controls the airflow into the engine, and its position is adjusted by the ECU to regulate the air-fuel ratio. This process ensures the engine receives the correct fuel-air mixture for optimal performance.
Electronic Control Unit (ECU): Often referred to as the 'brain' of the fuel injection system, the ECU is a sophisticated computer that monitors and controls various engine functions. It receives input from various sensors, such as the mass airflow sensor and oxygen sensors, to determine the engine's operating conditions. The ECU then sends signals to the fuel injectors, adjusting the fuel injection timing and amount to maintain the desired air-fuel ratio. This real-time feedback loop ensures the engine runs efficiently and within emissions regulations.
Understanding these components and their interactions is vital for diagnosing and repairing fuel injection issues. When dealing with fuel lines, especially those involving compression fittings, it's essential to inspect the system for any blockages, leaks, or damage. Compression fittings are commonly used to secure fuel lines, and proper installation and maintenance can prevent issues like fuel leaks or reduced performance.
Mastering the Art of Fuel Line Removal: A Step-by-Step Guide for Lawn Mowers
You may want to see also
Fuel Line Routing: Properly route the fuel line to avoid damage and ensure optimal flow
When it comes to fuel line routing, proper placement is crucial to ensure the longevity of your vehicle's fuel system and optimal performance. The fuel line is responsible for transporting fuel from the tank to the engine, and any damage or restriction can lead to fuel delivery issues and potential engine problems. Here's a comprehensive guide to help you navigate the process:
- Identify the Route: Begin by locating the fuel tank and the engine's fuel injection system. The fuel line typically runs from the tank, often located at the rear of the vehicle, to the engine compartment. Visualize the path and identify any potential obstacles or areas where the line might be susceptible to damage. Common routes include running along the frame, under the vehicle, or through the engine bay.
- Avoid Heat Sources: One of the critical aspects of routing is protecting the fuel line from heat sources. The fuel line should be kept away from hot exhaust pipes, manifolds, and engine components. Prolonged exposure to high temperatures can cause the fuel line to degrade, leading to cracks or leaks. Ensure there is sufficient insulation or a protective covering to safeguard the line.
- Secure and Support: Properly secure the fuel line to prevent movement and potential damage. Use appropriate ties or clips to keep the line in place, especially in areas where it might rub against other components. Avoid tight bends or kinks, as these can restrict fuel flow and cause long-term damage. Consider using a flexible fuel line with built-in support to maintain its shape and integrity.
- Consider Engine Movement: Take into account the natural movement of the engine during operation. The fuel line should be routed in a way that accommodates this movement to prevent excessive stress on the line. Avoid routing it directly over or under components that may move or vibrate intensely. This ensures a smooth and continuous flow of fuel.
- Regular Inspection: Regularly inspect the fuel line for any signs of wear, damage, or leaks. Look for cracks, brittleness, or any discolouration, especially in areas where the line is exposed to the elements. Promptly address any issues to prevent further complications. It is also beneficial to check for any signs of fuel contamination, as this can lead to engine performance problems.
By following these guidelines, you can ensure that your fuel line is properly routed, providing optimal fuel flow and protecting your vehicle's engine from potential issues caused by improper placement. Remember, a well-maintained fuel system is essential for the overall performance and reliability of your car.
Locating the Fuel Line: A Guide to Finding the 2002 Pontiac GM Fuel Line
You may want to see also
Fuel Filter Maintenance: Regularly clean or replace fuel filters to prevent contamination
Maintaining a clean and well-functioning fuel filter is crucial for the optimal performance and longevity of your vehicle's fuel injection system. Over time, fuel filters can become clogged with contaminants, such as dirt, rust, and debris, which can lead to reduced engine performance and potential damage. Regular maintenance and timely replacement of fuel filters are essential to ensure a clean fuel supply and prevent any issues related to contamination.
The primary function of a fuel filter is to strain impurities from the fuel before it reaches the engine. As fuel passes through the filter, it captures and removes contaminants, ensuring that only clean fuel enters the system. However, this process can lead to the accumulation of debris, especially in older vehicles or those with high mileage. Regular cleaning or replacement of the fuel filter is necessary to maintain its effectiveness.
To maintain your fuel filter, it is recommended to follow a routine maintenance schedule. This typically involves checking the filter for any signs of contamination or excessive dirt accumulation. If you notice any blockages or if the filter appears discolored, it may be an indication that it needs cleaning or replacement. In some cases, you can clean the filter by removing it and using a filter cleaning solution to remove any built-up contaminants. However, if the filter is severely clogged or shows signs of wear and tear, it is best to replace it with a new one.
When replacing the fuel filter, ensure you use the correct type and size recommended by the vehicle manufacturer. Improperly sized filters may not provide adequate filtration, leading to potential engine issues. It is also essential to follow the manufacturer's guidelines for installation to ensure a proper seal and prevent any fuel leaks. Regularly scheduled fuel filter maintenance can help extend the life of your engine and maintain optimal performance.
In summary, keeping your fuel filter clean and well-maintained is vital for the overall health of your fuel injection system. By regularly checking and cleaning or replacing the filter, you can prevent contamination, improve engine performance, and avoid potential costly repairs. Remember, proper fuel filter maintenance is a simple yet effective way to care for your vehicle and ensure its reliable operation.
Unclogging Boat Fuel Lines: A Step-by-Step Guide to Getting Your Engine Running Again
You may want to see also
Frequently asked questions
A compression fitting is a type of connector used to join two fuel lines together. It works by compressing the fuel line material around the fitting, creating a tight seal. This method is commonly used for fuel injection systems as it provides a secure and reliable connection, ensuring no fuel leaks.
Yes, compression fittings are an effective way to repair fuel lines. If a fuel line has a small hole or tear, you can cut the damaged section and insert the compression fitting to seal the gap. This method is often preferred over welding or soldering, as it is less invasive and allows for easier disassembly if needed.
Compression fittings offer several advantages for fuel injection systems. They provide an airtight seal, preventing fuel evaporation and potential engine performance issues. These fittings are also durable and can withstand high fuel pressures, ensuring a reliable connection. Additionally, they are easy to install and can be used with various fuel line materials.
Yes, you will need a few essential tools to install a compression fitting. These include a fuel line cutter or a pair of sharp scissors to cut the fuel line, a fuel line crimper to create the compression, and a fuel line cleaner to ensure a proper seal. It is also recommended to have a fuel pressure gauge to check the system's integrity after installation.
Yes, compression fittings can be reused if they are in good condition. However, it is important to inspect the fitting for any signs of damage or wear before reuse. Ensure that the threads and sealing surfaces are intact. If the fitting shows signs of deterioration, it is best to replace it to maintain the system's performance and reliability.