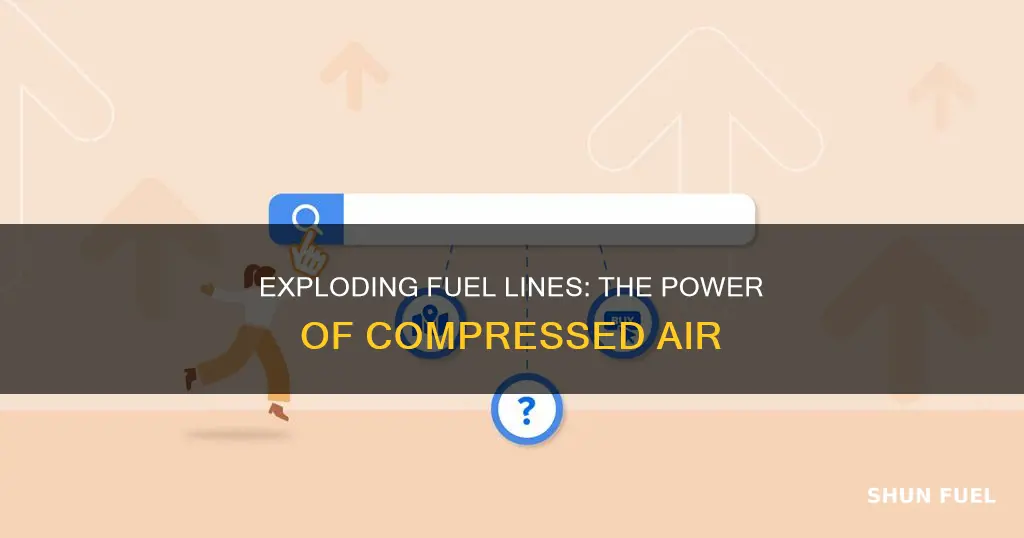
Can you blow out fuel lines with a compressor? It's a question that might spark curiosity, especially for those involved in vehicle maintenance or fuel system repairs. The idea of using a compressor to clear fuel lines might seem unconventional, but it's a technique that can be effective under certain conditions. In this paragraph, we'll explore the concept, the potential benefits, and the considerations one should keep in mind when contemplating this approach.
What You'll Learn
- Fuel Line Material: Different materials react differently to air pressure, affecting blow-out effectiveness
- Fuel Line Diameter: Thicker lines require higher pressure, complicating the blow-out process
- Fuel Line Length: Longer lines may require multiple passes or specialized techniques for complete clearing
- Fuel Line Condition: Cracked or damaged lines may not respond well to air pressure
- Compressor Capacity: The compressor's power determines how effectively it can clear fuel lines
Fuel Line Material: Different materials react differently to air pressure, affecting blow-out effectiveness
When considering the use of a compressor to blow out fuel lines, it's crucial to understand the role that fuel line material plays in the effectiveness of this process. Different materials have distinct properties that influence how they respond to air pressure, which in turn affects the overall success of the blow-out operation. Here's a detailed exploration of this concept:
Metal Fuel Lines: Metal fuel lines, such as those made from steel or aluminum, are commonly used in automotive applications. These materials are known for their durability and ability to withstand high pressure. When subjected to air pressure from a compressor, metal fuel lines can effectively release accumulated fuel vapor and debris. The rigid nature of metal allows for a more forceful expulsion of contaminants, making it ideal for thorough cleaning. However, it's important to note that excessive air pressure might cause minor damage to the fuel line, especially if it is already compromised.
Rubber or Plastic Fuel Lines: In contrast, fuel lines made from rubber or plastic offer flexibility and are often used in modern vehicles. While these materials can withstand moderate air pressure, they may not provide the same level of blow-out effectiveness as metal. Rubber and plastic are more susceptible to deformation under high pressure, which could lead to reduced blow-out efficiency. Additionally, these materials might not be as durable as metal, potentially requiring more frequent replacements.
Considerations for Blow-Out Effectiveness: The choice of fuel line material significantly impacts the blow-out process. Materials with higher elasticity, like rubber, may require more air pressure to achieve the desired effect. On the other hand, stiffer materials like metal can respond more readily to lower air pressure. It is essential to select a compressor with adjustable pressure settings to accommodate different fuel line materials. This ensures that the blow-out process is both effective and safe, minimizing the risk of damage to the fuel system.
Maintenance and Inspection: Regular maintenance and inspection of fuel lines are vital, especially when using a compressor for blow-out. Over time, fuel lines can deteriorate due to various factors, including fuel contamination and the effects of air pressure. Materials like rubber may degrade more quickly, leading to reduced blow-out performance. Therefore, it is recommended to periodically check the condition of fuel lines and replace them if necessary to ensure optimal blow-out effectiveness.
In summary, the material of the fuel lines is a critical factor in determining the success of blowing out fuel lines with a compressor. Understanding the properties of different materials and their responses to air pressure allows for informed decisions regarding the choice of fuel line type and compressor settings, ultimately ensuring a more efficient and safe maintenance process.
Camaro Fuel Line Sizing: 3rd Gen Guide
You may want to see also
Fuel Line Diameter: Thicker lines require higher pressure, complicating the blow-out process
When dealing with fuel lines, especially those with a larger diameter, it's crucial to understand the relationship between the fuel line's thickness and the pressure required for a successful blow-out process using a compressor. Thicker fuel lines, while providing better fuel flow and reduced pressure drop, present a unique challenge.
The primary reason for this challenge is the increased resistance that thicker lines offer. As the diameter of a fuel line increases, the cross-sectional area also increases, which means there is more space for fuel to flow through. While this might seem beneficial, it requires a higher pressure to push the fuel through this larger area. This is because the pressure needs to overcome the increased resistance to ensure efficient fuel delivery.
In the context of a blow-out process, where you are using a compressor to force air or fuel through the lines, the higher pressure requirement becomes a significant factor. The compressor must generate enough force to not only push the air or fuel through the thicker lines but also to maintain a consistent pressure throughout the system. This can be particularly challenging when dealing with older or less efficient compressors, as they may not have the capacity to meet the pressure demands of thicker fuel lines.
To address this issue, one approach is to use a compressor with a higher output capacity or to consider the use of a booster pump. These additional components can help increase the pressure to the required levels, ensuring that the blow-out process is effective. However, it's essential to carefully select the right equipment to avoid causing damage to the fuel lines or the compressor itself due to excessive pressure.
In summary, when working with thicker fuel lines, the blow-out process becomes more complex due to the higher pressure requirements. Understanding this relationship is vital for anyone looking to maintain or repair fuel systems, ensuring that the right equipment and techniques are employed to achieve optimal performance without causing unnecessary strain on the system.
Foxbody Fuel Line Placement: A Step-by-Step Guide to Carburetor Fueling
You may want to see also
Fuel Line Length: Longer lines may require multiple passes or specialized techniques for complete clearing
When dealing with longer fuel lines, the process of clearing them with a compressor can become more complex and may require additional techniques to ensure a thorough cleaning. The length of the fuel lines can make it challenging to reach every section and ensure that contaminants are completely removed. Here's a detailed guide on how to approach this scenario:
In cases where fuel lines are extended, multiple passes with the compressor may be necessary. Start by identifying the entry and exit points of the fuel line. Connect the compressor to the entry point and begin blowing air through the line. Move the compressor along the length of the line, ensuring that you cover the entire distance. For longer lines, you might need to make several passes, gradually moving the compressor back and forth or in a wave pattern to ensure all areas are reached. This methodical approach helps to prevent any contaminants from escaping and getting trapped in hard-to-reach areas.
For particularly long or complex fuel lines, specialized techniques can be employed. One such technique is the use of a 'whip' or 'extension' on the compressor's output. This accessory allows you to direct the compressed air stream more precisely, making it easier to navigate tight turns or hard-to-reach angles within the fuel line. By adjusting the angle and pressure of the air stream, you can ensure that even the most remote sections of the line are thoroughly cleaned.
Another consideration for longer fuel lines is the potential for contaminants to accumulate in low-lying areas or dead ends. In these cases, it's essential to use a technique called 'vacuum and blow' or 'suction and blow.' This involves first using a vacuum to remove any loose contaminants and then immediately following up with a blowing operation to ensure they are completely expelled. This two-step process ensures that no debris remains within the fuel line.
Additionally, when dealing with longer lines, it's crucial to monitor the pressure and air flow rate of the compressor. Adjusting these settings can help you control the force and reach of the compressed air, allowing you to navigate the fuel line's intricacies effectively. Higher pressure may be required for more stubborn blockages, while lower pressure can be used for gentler cleaning to avoid any potential damage.
In summary, longer fuel lines demand a more meticulous approach when using a compressor for cleaning. Multiple passes, specialized accessories, and tailored techniques are essential to ensure that every part of the line is thoroughly cleared of contaminants. By adapting your methods to the unique challenges posed by longer fuel lines, you can effectively maintain the health and performance of the fuel system.
Upgrading Your CB350's Fuel Line: 5mm or Not?
You may want to see also
Fuel Line Condition: Cracked or damaged lines may not respond well to air pressure
When considering the use of compressed air to clear fuel lines, it's crucial to understand the condition of the fuel lines themselves. If the fuel lines are cracked or damaged, the effectiveness of this method can be significantly compromised. Cracks or damage to the fuel lines can lead to several issues that may prevent the lines from responding adequately to air pressure.
One primary concern is the potential for air to enter the fuel system. When compressed air is applied to a damaged line, it can create pathways for air to infiltrate the fuel. This air can then mix with the fuel, leading to a condition known as 'air binding' or 'air lock'. Air binding can cause the fuel to become less dense, which may result in poor engine performance, reduced power, and even stalling. In some cases, the air bubbles can become trapped in the fuel lines, leading to a situation where the fuel flow is intermittent or ceases entirely.
Additionally, damaged fuel lines may have reduced internal diameter or be partially obstructed, which can restrict the flow of fuel. When compressed air is applied to such lines, it may not be able to dislodge the fuel effectively, especially if the damage is significant. The air pressure might not be sufficient to overcome the resistance caused by the damaged section, leading to an incomplete clearing of the fuel lines.
Furthermore, the presence of cracks or damage can also introduce contaminants into the fuel system. Over time, these contaminants can accumulate, leading to a buildup of sludge or deposits within the fuel lines and engine components. This can result in further performance issues and potential long-term damage to the engine.
In summary, while compressed air can be an effective method for clearing fuel lines, it is essential to inspect the fuel lines for any cracks or damage beforehand. If such issues are present, alternative methods or repairs may be necessary to ensure the fuel lines are in optimal condition before attempting to clear them with compressed air. Proper maintenance and regular inspections can help prevent these problems and ensure the longevity of the fuel system.
Polaris Ranger 570 Fuel Line Fittings: A Comprehensive Guide
You may want to see also
Compressor Capacity: The compressor's power determines how effectively it can clear fuel lines
The power of a compressor is a critical factor when considering its ability to clear fuel lines. Compressor capacity refers to the volume of air it can deliver per minute, measured in cubic feet per minute (CFM) or liters per minute (LPM). This capacity directly influences the force and pressure with which the air can be expelled, which is essential for effective fuel line clearing.
A compressor with a higher power output will generate more air pressure, allowing it to push air through the fuel lines more vigorously. This increased pressure can help dislodge and remove contaminants, such as fuel varnish, water, and debris, that may have accumulated in the lines over time. For instance, a 2-stage compressor with a higher horsepower rating can deliver a more substantial volume of air at a higher pressure, making it more effective for fuel line maintenance.
When selecting a compressor for this purpose, it's important to consider the specific requirements of your fuel system. Factors such as the length and diameter of the fuel lines, the type of fuel used, and the presence of any blockages or obstructions will influence the necessary compressor capacity. Longer fuel lines or those with narrower diameters may require a more powerful compressor to ensure adequate air flow and pressure.
Additionally, the compressor's power should be matched to the task at hand. For routine maintenance, a lower-capacity compressor might suffice, but for more severe blockages or extensive fuel line issues, a higher-powered model will be more effective. It's a balance between ensuring sufficient power to clear the lines and avoiding unnecessary overkill, which could lead to potential damage to the fuel system.
In summary, when dealing with fuel line clearing, the compressor's power is a key determinant of its effectiveness. Higher-capacity compressors provide more force and pressure, making them ideal for tackling stubborn blockages and ensuring a thorough cleaning of the fuel lines. Understanding the specific needs of your fuel system and choosing a compressor with the appropriate power output will result in a more efficient and successful maintenance process.
Mastering Fuel Line Sealing: A Comprehensive Guide to Perfect Fittings
You may want to see also
Frequently asked questions
Yes, a compressor can be utilized to blow out fuel lines, but it's important to use it with caution and proper safety measures. Compressors provide compressed air, which can be used to clear debris, remove contaminants, and flush out fuel lines. However, it should be done carefully to avoid any potential damage to the fuel system.
The process typically involves attaching the compressor's output to a high-pressure air source, which is then directed into the fuel lines. This high-pressure air can dislodge any built-up deposits, contaminants, or debris, effectively cleaning the lines. It's crucial to follow manufacturer guidelines and use the appropriate air pressure to ensure the process is safe and effective.
Yes, there are risks involved, especially if not done correctly. High-pressure air can cause damage to fuel line components, such as cracks or punctures. It can also lead to fuel leaks, which pose a fire hazard. Proper safety gear, including eye and ear protection, should be worn, and the process should be carried out in a well-ventilated area to minimize the risk of fuel inhalation.
The frequency of blowing out fuel lines depends on various factors, including the vehicle's age, usage, and maintenance history. As a general guideline, it is recommended to perform this process every 6 to 12 months or as advised by the vehicle manufacturer. Regular maintenance helps ensure optimal fuel system performance and longevity.