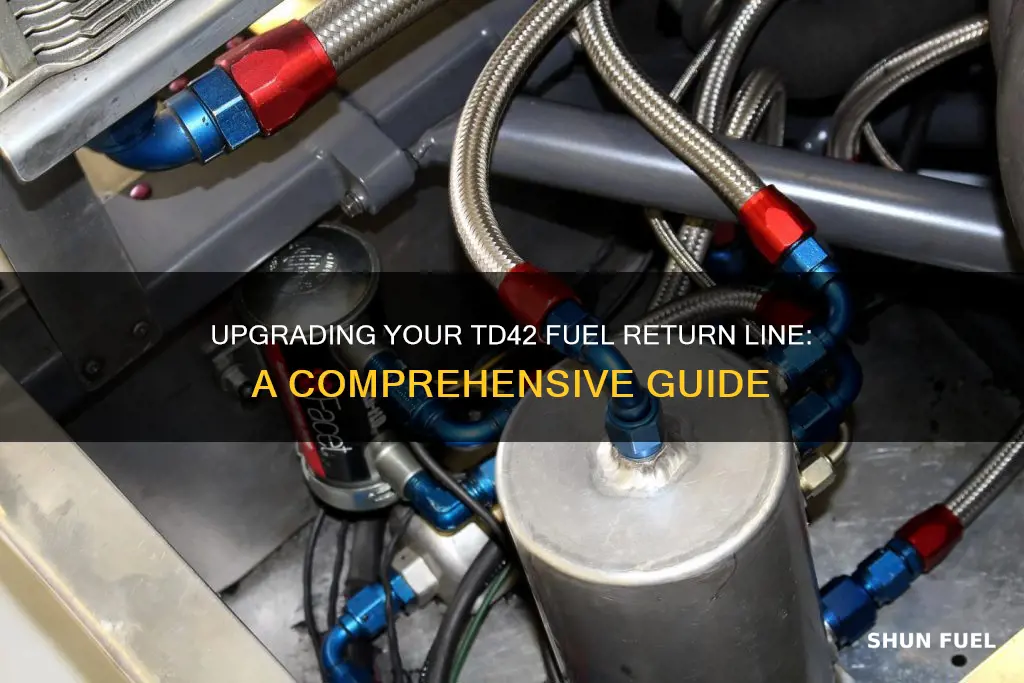
The topic of Can you change TD 42 fuel return line setup delves into the intricacies of modifying the fuel return line configuration in a TD 42 engine. This discussion is particularly relevant for vehicle enthusiasts and mechanics who aim to optimize engine performance and fuel efficiency. By exploring the potential changes and their implications, this topic offers valuable insights into the customization and maintenance of automotive systems, providing a comprehensive understanding of the technical aspects involved.
Characteristics | Values |
---|---|
Fuel System Type | TD 42 |
Line Setup | Fuel Return Line |
Modifications | Can be changed |
Purpose | To control fuel flow and pressure |
Compatibility | Vehicle-specific |
Materials | Metal, rubber, or composite |
Length | Varies based on vehicle design |
Fitting | Requires specialized tools and knowledge |
Maintenance | Regular checks and replacements may be needed |
Performance | Improved fuel efficiency and engine performance |
Safety | Proper setup is crucial to prevent fuel leaks and engine damage |
What You'll Learn
- Fuel Line Routing: Explore different paths for the 42-series TD fuel return line to optimize flow and minimize pressure drops
- Fittings and Connections: Focus on choosing the right fittings and connections to ensure a secure and leak-free setup
- Pressure Regulation: Discuss methods to regulate fuel pressure in the return line for optimal engine performance
- Material Selection: Evaluate various materials for the fuel line to ensure compatibility and durability
- Testing and Inspection: Outline procedures for testing and inspecting the fuel return line setup for leaks and functionality
Fuel Line Routing: Explore different paths for the 42-series TD fuel return line to optimize flow and minimize pressure drops
When it comes to optimizing the fuel return line setup for the 42-series TD engine, routing the fuel lines is a critical aspect that can significantly impact performance and efficiency. The primary goal is to ensure smooth and efficient fuel flow while minimizing pressure drops, which can lead to improved engine operation and reduced fuel consumption. Here's an exploration of various routing options:
Direct Routing: One of the most straightforward approaches is to route the fuel return line directly from the fuel tank to the engine's fuel return port. This method ensures a short and direct path for the fuel, reducing the chances of contamination and maintaining a consistent fuel pressure. By minimizing the length of the line, you can also reduce the potential for pressure losses, especially in high-flow scenarios. This direct routing is often preferred in high-performance applications where every second counts.
Loop Routing: Another strategy is to create a loop in the fuel return line, especially if the engine bay has limited space. This loop can be designed to follow a specific path, allowing for better organization and clearance. The loop can start from the fuel tank, run along the side of the engine, and then connect back to the fuel return port. This method provides a more flexible routing option, accommodating various engine bay layouts. However, it's crucial to ensure that the loop doesn't introduce unnecessary bends or kinks, as these can restrict flow and cause pressure drops.
Underground Routing: For engines installed in areas with limited accessibility, routing the fuel return line underground can be a practical solution. This method involves running the line through the engine bay floor or any available voids, ensuring it remains out of the way and protected from potential damage. Underground routing requires careful planning to avoid interference with other components and to maintain a consistent fuel pressure throughout the line. It's an excellent option for hidden or compact engine installations.
Consideration of Engine Bay Layout: The engine bay layout plays a crucial role in determining the best fuel line routing. Engineers should consider the placement of other components, such as the engine block, transmission, and exhaust system, to find optimal spaces for the fuel return line. In some cases, a combination of routing methods might be employed to navigate around obstacles and ensure a clean, efficient setup.
Testing and Optimization: After selecting a routing method, it's essential to test the fuel system thoroughly. This includes pressure testing, flow rate measurements, and engine performance evaluations. By doing so, you can identify any pressure drops or flow restrictions caused by the chosen routing and make adjustments as necessary. Optimization might involve slight modifications to the line's path or the use of specialized fuel line materials to enhance performance.
Fuel Pressure Line: Can You Suck Through It?
You may want to see also
Fittings and Connections: Focus on choosing the right fittings and connections to ensure a secure and leak-free setup
When dealing with fuel return line setups, especially for a TD 42 engine, the choice of fittings and connections is critical to ensure optimal performance and prevent leaks. The fuel return line is responsible for directing excess fuel back to the tank, and any compromise in its setup can lead to fuel wastage, engine performance issues, and potential safety hazards. Here's a detailed guide on how to approach this task:
Understanding the Components: Begin by familiarizing yourself with the specific fittings and connections required for the TD 42 fuel return line. This includes understanding the types of hoses, clamps, and fittings that are compatible with the engine's design. Different engines may have unique requirements, so it's essential to consult the manufacturer's guidelines or seek expert advice. For instance, you might need specific types of fuel lines, such as high-pressure or low-pressure hoses, each with its own set of fittings.
Material Selection: The choice of materials is crucial for durability and compatibility. Common materials for fuel lines include rubber, silicone, or nylon, each offering different advantages. Rubber is known for its flexibility and resistance to fuel degradation, while silicone provides excellent heat resistance. Nylon, on the other hand, is lightweight and offers good chemical resistance. Select the material that best suits the engine's operating conditions and the type of fuel used.
Fitting Types: There are various types of fittings available, such as quick-connect couplings, compression fittings, and crimp fittings. Quick-connect couplings are convenient for rapid assembly and disassembly but may not provide the tightest seal. Compression fittings offer a secure connection by compressing a ferrule around the hose, ensuring a leak-free seal. Crimp fittings are used for hoses with a metal reinforcement and provide a reliable connection. Choose the fitting type that aligns with your engine's requirements and your personal preference for ease of maintenance.
Clamps and Securing: Properly securing the fuel return line is essential to prevent leaks and ensure a tight fit. Use high-quality clamps designed for fuel line applications. These clamps should be made of durable materials and have a secure grip to hold the fittings and hoses in place without causing damage. Ensure that the clamps are tightened to the manufacturer's recommended specifications to achieve a snug fit.
Leak Testing: After assembling the fuel return line setup, conduct thorough leak testing. This step is critical to identify any potential issues before putting the engine into operation. Use a soapy water solution or a specialized fuel line leak detector to check for any leaks at the connections. Even a small leak can lead to significant problems over time, so ensure that all fittings and connections are secure and tight.
Understanding Touareg Fuel Filter: Input vs. Output Lines
You may want to see also
Pressure Regulation: Discuss methods to regulate fuel pressure in the return line for optimal engine performance
The fuel return line setup in a TD 42 engine is a critical component that ensures efficient fuel delivery and optimal engine performance. Proper pressure regulation within this system is essential to maintain the delicate balance of fuel and air required for combustion. Here's an overview of methods to regulate fuel pressure in the return line:
One common approach to pressure regulation is the use of a fuel pressure regulator. This component is typically located along the fuel return line and acts as a governor, controlling the fuel pressure to a predetermined set point. The regulator consists of a spring-loaded diaphragm or a solenoid-based mechanism that adjusts the fuel flow rate accordingly. When the engine demands more power, the regulator opens to allow additional fuel, ensuring the engine receives the required amount. Conversely, during low-load conditions, it restricts fuel flow to maintain optimal combustion efficiency. Regular maintenance and periodic checks of the fuel pressure regulator are crucial to guarantee its effectiveness.
Another method to regulate pressure is through the use of a fuel pump with a built-in pressure relief valve. This design allows for automatic pressure control, ensuring the fuel system operates within safe limits. The pump's internal valve opens and closes based on the engine's demand, releasing excess pressure when necessary. This setup provides a dynamic and responsive fuel pressure regulation system, adapting to varying engine loads. It is important to note that the fuel pump's capacity and efficiency should be considered to match the engine's requirements.
Additionally, implementing a fuel pressure gauge can offer valuable insights into the system's performance. This gauge provides real-time feedback on the fuel pressure, allowing for manual adjustments if needed. By monitoring the pressure, technicians can fine-tune the fuel return line setup, ensuring it meets the engine's specifications. Regular calibration and adjustment of the gauge in conjunction with the fuel pressure regulator can lead to improved engine response and overall performance.
In summary, regulating fuel pressure in the return line is vital for TD 42 engine optimization. Employing fuel pressure regulators, fuel pumps with internal relief valves, and utilizing fuel pressure gauges are effective methods to maintain the desired pressure levels. Each of these techniques contributes to efficient fuel delivery, combustion, and ultimately, enhanced engine performance. Proper maintenance and regular inspections of these components will ensure the engine operates at its peak potential.
Unleash Your Potential: Understanding Your Unique Fuel Line
You may want to see also
Material Selection: Evaluate various materials for the fuel line to ensure compatibility and durability
When it comes to selecting the right material for a TD 42 fuel return line setup, several factors must be considered to ensure optimal performance and longevity. The primary goal is to choose a material that can withstand the harsh conditions of fuel transport, including temperature variations, pressure fluctuations, and chemical exposure.
One of the most commonly used materials for fuel lines is stainless steel. This material offers excellent corrosion resistance, making it ideal for fuel systems that operate in diverse environments. Stainless steel is known for its ability to resist oxidation and maintain its structural integrity over time. It is also relatively flexible, allowing for easy installation and routing within the engine compartment. However, it is important to note that stainless steel can be more expensive than other options, so a balance between cost and performance must be considered.
Another popular choice is braided steel, which combines the strength of steel with the flexibility of a braided design. This material is often used in high-pressure fuel lines due to its ability to handle tight bends and maintain its shape. Braided steel is also resistant to fuel degradation, ensuring that the fuel remains stable and does not break down over time. Its durability makes it a reliable option for fuel return lines, especially in applications where the line may be subjected to frequent vibrations or mechanical stress.
For those seeking a more lightweight and cost-effective solution, PVC (polyvinyl chloride) can be a viable alternative. PVC is widely used in fuel lines due to its affordability and ease of installation. It offers good chemical resistance, which is crucial for fuel systems, and it can withstand moderate temperature variations. However, PVC may not be as durable as stainless steel or braided steel, and it can become brittle over time, especially in low-temperature conditions. Therefore, it is essential to consider the specific operating environment and temperature range when choosing PVC.
In addition to these traditional materials, some manufacturers are exploring the use of synthetic materials like fluoropolymers. These materials offer exceptional chemical resistance and can withstand extreme temperatures, making them suitable for high-performance fuel systems. Fluoropolymers are known for their flexibility and ability to resist fuel degradation, ensuring long-term reliability. However, they can be more expensive and may require specialized installation techniques.
In conclusion, selecting the right material for a TD 42 fuel return line setup involves a careful evaluation of various factors. Stainless steel provides excellent corrosion resistance, braided steel offers strength and flexibility, PVC is cost-effective but may lack durability, and synthetic materials like fluoropolymers provide advanced performance. The choice depends on the specific requirements of the application, including environmental conditions, temperature range, and budget constraints. It is crucial to consider these factors to ensure the fuel line's compatibility and long-term durability.
GSXR 750 Fuel Line Leaks: Normal or Cause for Concern?
You may want to see also
Testing and Inspection: Outline procedures for testing and inspecting the fuel return line setup for leaks and functionality
When it comes to testing and inspecting the fuel return line setup for the TD 42 engine, a systematic approach is essential to ensure optimal performance and safety. Here's an outline of the procedures to follow:
Preparation and Safety Measures: Before beginning the inspection, ensure that the vehicle is parked on a level surface and the engine is cool to the touch. Engage the parking brake for added safety. Wear appropriate personal protective equipment (PPE) to protect against potential fuel spills. Gather the necessary tools, including a fuel pressure gauge, a leak detection kit, and a container for collecting samples.
Visual Inspection: Start by visually examining the fuel return line setup. Look for any visible signs of damage, corrosion, or debris accumulation. Check for cracks, kinks, or bends in the lines that could compromise their integrity. Inspect all connections, fittings, and valves for tightness and potential leaks. Pay close attention to areas where lines are routed near hot surfaces or under heavy stress.
Leak Testing: This is a critical step to ensure the system's integrity. Start by disconnecting the fuel return line from the engine and the tank. Use the leak detection kit to apply a small amount of dye or a suitable indicator to the line. Observe the system for any signs of dye leakage over a specified period. If leaks are detected, identify the source and address any issues, such as faulty fittings or damaged lines.
Fuel Pressure Check: Connect the fuel pressure gauge to the fuel return line and measure the pressure. Compare the reading with the manufacturer's specifications. Low pressure may indicate a restriction or leak in the system. If the pressure is within the acceptable range, proceed to the next step. If not, investigate potential causes, such as clogged filters or damaged pumps.
Functionality Testing: To ensure the fuel return line setup functions correctly, simulate various driving conditions. Start the engine and monitor the fuel flow. Check for any unusual noises or vibrations that could indicate issues with the lines or associated components. Test the fuel pump's operation by applying pressure and observing the flow rate. Ensure that the system can handle the expected fuel demands during different driving scenarios.
Documentation and Reporting: Document all findings, including any issues identified during the inspection. Create a detailed report outlining the condition of the fuel return line setup, any repairs or replacements made, and the test results. This documentation is crucial for maintenance records and future reference.
WRX Fuel Line: Discover the Perfect OEM Size
You may want to see also
Frequently asked questions
The TD 42 fuel return line setup is a crucial component in fuel management systems, particularly for engines. It is designed to ensure efficient and controlled fuel flow, allowing for optimal combustion and performance. This setup typically includes a fuel return line that connects the fuel tank to the engine, enabling the engine to draw fuel as needed while maintaining a consistent fuel level in the tank.
Yes, it is possible to modify the TD 42 fuel return line setup, but it should be done with caution and careful consideration. Modifying this system can impact engine performance, fuel efficiency, and overall reliability. Any changes should be made by experienced professionals or based on specific requirements and recommendations provided by the engine manufacturer. Common modifications may include adjusting the line length, using different materials, or adding filters to improve fuel quality.
Changing the fuel return line setup can offer several advantages. One benefit is improved fuel management, allowing for better control over fuel flow and potentially enhancing engine performance. Modified lines can also help reduce fuel pressure fluctuations, leading to smoother operation and increased efficiency. Additionally, custom setups can be tailored to specific engine requirements, ensuring optimal fuel delivery and combustion.
The TD 42 fuel return line setup may encounter various issues over time. Common problems include fuel leaks, which can be caused by damaged lines or improper connections. Clogging or blockages in the line can also occur, leading to reduced fuel flow and potential engine performance issues. Regular maintenance and inspections are essential to identify and address these problems promptly.