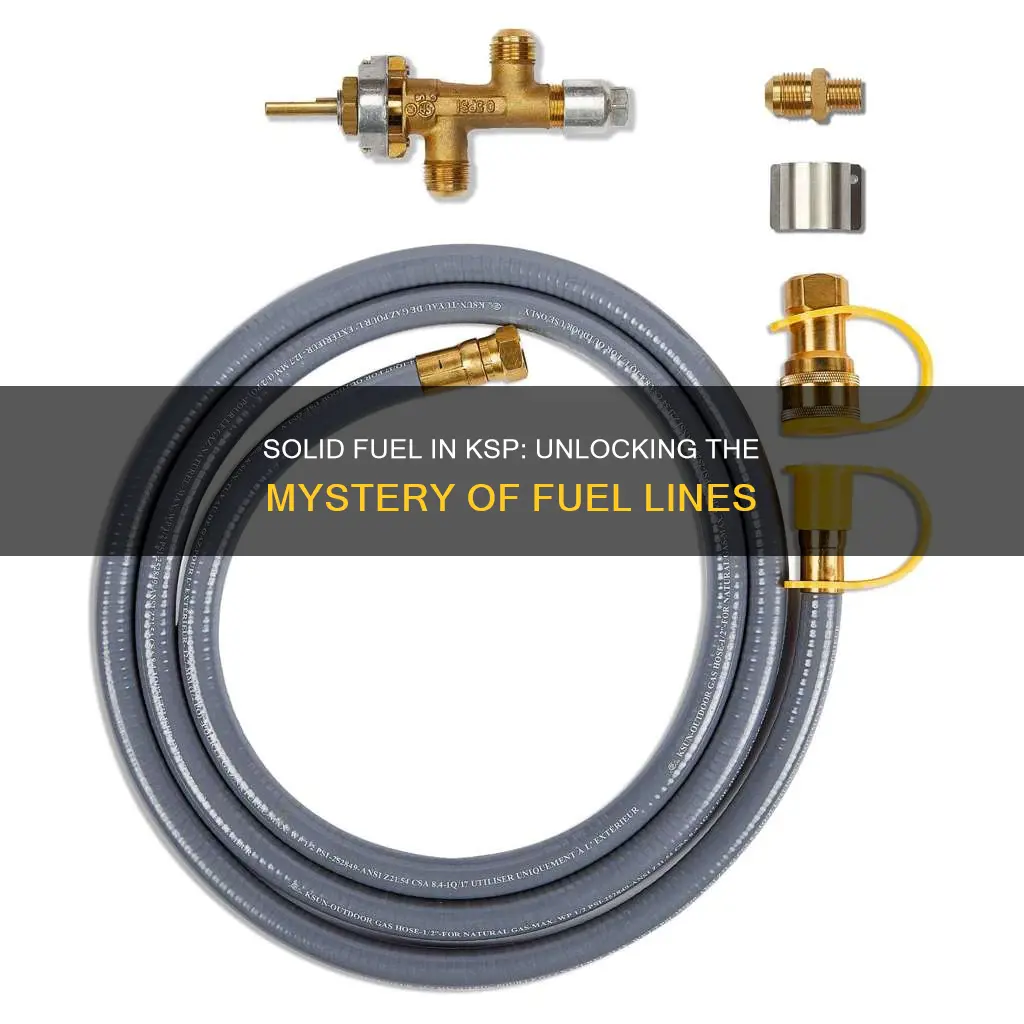
In the context of Kerbal Space Program (KSP), the question of whether solid fuel can be used in fuel lines is an important consideration for spacecraft design. Solid fuel, such as solid rocket boosters or fuel tanks, plays a crucial role in providing the necessary thrust for a spacecraft's ascent and orbital maneuvers. Understanding the compatibility and performance of solid fuel in fuel lines is essential for engineers and players to optimize their spacecraft's fuel systems and ensure successful missions. This paragraph aims to explore the feasibility and potential challenges of incorporating solid fuel into fuel lines within the KSP environment.
Characteristics | Values |
---|---|
Fuel Type | Solid |
Compatibility | Not compatible with fuel lines in KSP |
Storage | Requires special containers or adapters |
Handling | Can be hazardous and may require specialized equipment |
Performance | May not provide efficient thrust or control in KSP's context |
Legal and Safety Considerations | May be restricted or prohibited in certain environments or applications |
What You'll Learn
- Fuel Line Compatibility: Solid fuel compatibility with KSP's fuel lines
- Performance Impact: Solid fuel's performance impact on spacecraft in KSP
- Engine Design: Engine design considerations for solid fuel in KSP
- Safety Measures: Safety protocols for handling solid fuel in KSP's fuel lines
- Fuel Efficiency: Solid fuel efficiency compared to liquid fuel in KSP
Fuel Line Compatibility: Solid fuel compatibility with KSP's fuel lines
When it comes to Kerbal Space Program (KSP), managing fuel lines and ensuring compatibility with different types of fuel is crucial for a successful space mission. While KSP primarily uses liquid fuels, there might be instances where you need to consider solid fuel options, especially if you're experimenting with unique propulsion systems or trying to replicate real-world space programs.
Solid fuels, such as solid rocket boosters or even homemade solid fuel grains, can be a fascinating and powerful addition to your KSP gameplay. However, it's essential to understand the compatibility and potential challenges when using solid fuel in fuel lines. The key consideration is the physical properties of the solid fuel and how it interacts with the fuel lines' internal structure. Solid fuels often have different combustion characteristics and may require specific line sizes and materials to ensure efficient and safe operation.
In KSP, fuel lines are typically designed to handle liquid fuels, which have consistent flow rates and require precise control. Solid fuels, on the other hand, can vary in density and combustion rate, making their integration into fuel lines a complex task. The fuel lines must be able to withstand the pressure and heat generated during the solid fuel's combustion process. Engineers and designers often use specialized materials and designs for solid fuel lines, ensuring they can handle the unique demands of these fuels.
To ensure compatibility, it's crucial to consider the fuel line's diameter and wall thickness. Solid fuels may require larger-diameter lines to accommodate the varying flow rates and to prevent blockages. Additionally, the material of the fuel line should be chosen carefully. Common materials like aluminum or copper alloys might not be suitable due to their potential reactivity with the solid fuel. Instead, materials like stainless steel or specialized composite materials could be considered to ensure longevity and compatibility.
When using solid fuel in KSP, it's essential to test and simulate the system thoroughly. This includes creating detailed models, running simulations, and even building prototypes to understand the fuel's behavior within the fuel lines. Proper planning and understanding of the fuel's properties will ensure a successful and safe space mission, whether you're launching a rocket or exploring the possibilities of solid fuel in KSP.
Inline Fuel Filter Direction: A Comprehensive Guide
You may want to see also
Performance Impact: Solid fuel's performance impact on spacecraft in KSP
The use of solid fuel in Kerbal Space Program (KSP) can significantly impact spacecraft performance, offering both advantages and challenges. Solid fuels, such as those derived from various chemical compounds, provide a unique set of characteristics that can be beneficial for specific missions. One of the primary performance considerations is the specific impulse (Isp), which measures the efficiency of a rocket engine. Solid fuels generally offer lower Isp compared to liquid fuels, but this can be advantageous in certain scenarios. For instance, in the early stages of a spacecraft's journey, where acceleration is crucial, the lower Isp of solid fuel can result in a more powerful initial boost, allowing for quicker escape velocities. This is particularly useful for launching from the Kerbin surface or other low-gravity bodies.
However, the performance impact of solid fuels is not solely about Isp. The fuel's density and combustion characteristics play a vital role in overall spacecraft performance. Solid fuels often have higher energy densities, meaning a given volume of solid fuel can provide more energy than an equivalent volume of liquid fuel. This property can be advantageous for spacecraft requiring high-energy payloads or those designed for deep space missions where fuel efficiency is critical. Additionally, the mechanical properties of solid fuels, such as their strength and structural integrity, are essential considerations. Engineers must ensure that the fuel's physical characteristics do not compromise the spacecraft's structural integrity during the fuel loading and unloading processes.
Another critical aspect is the fuel's combustion behavior. Solid fuels may exhibit different combustion patterns compared to their liquid counterparts, affecting the spacecraft's thrust profile and overall performance. The combustion process can influence the spacecraft's acceleration and deceleration capabilities, as well as its ability to perform precise maneuvers in space. For instance, the combustion of solid fuel might result in a more abrupt change in thrust, requiring careful spacecraft design to manage these dynamics effectively.
In KSP, the performance impact of solid fuels is further influenced by the spacecraft's design and mission objectives. Engineers must consider the fuel's properties when designing the spacecraft's structure, propulsion system, and overall architecture. This includes optimizing the fuel tankage, nozzles, and combustion chambers to maximize efficiency and minimize weight. The choice of solid fuel can also impact the spacecraft's ability to perform maneuvers like orbital adjustments, attitude control, and landing, especially in low-gravity environments.
In summary, solid fuels in KSP offer a unique set of performance characteristics that can be leveraged for specific mission requirements. While they may provide lower Isp, higher energy density, and distinct combustion behaviors, engineers must carefully consider these factors to optimize spacecraft performance. The successful integration of solid fuels into spacecraft design requires a comprehensive understanding of the fuel's properties and their impact on various aspects of the spacecraft's operation in the challenging environment of space.
Fuel Line Freeze: Causes, Symptoms, and Solutions
You may want to see also
Engine Design: Engine design considerations for solid fuel in KSP
When considering the use of solid fuel in Kerbal Space Program (KSP), engine design becomes a critical aspect to ensure optimal performance and safety. Solid fuels, such as solid rocket boosters or grain-based propellants, offer unique advantages and challenges compared to liquid fuels. Here are some key design considerations for incorporating solid fuel into your KSP engine:
Fuel System and Feed Mechanism: Solid fuel requires a robust and efficient feed system to deliver the propellant to the combustion chamber. One common approach is to use a screw feeder or a rotating mechanism to gradually feed the solid fuel into the engine. This design should ensure a consistent and controlled rate of fuel supply, allowing for precise thrust control during different phases of the mission. The feed mechanism should also be designed to handle the specific characteristics of the solid fuel, including its density and particle size.
Combustion Chamber and Nozzle Design: The combustion chamber and nozzle configuration play a vital role in maximizing performance. For solid fuels, a well-designed combustion chamber should promote efficient combustion and mixing of the fuel with oxidizer. This might involve specific shapes and baffles to ensure thorough mixing and prevent fuel accumulation. The nozzle design should be tailored to the solid fuel's exhaust characteristics, ensuring optimal expansion and acceleration of the hot gases.
Thrust Vector Control: Solid fuel engines often exhibit different thrust characteristics compared to liquid-fueled engines. The design should account for potential thrust vector changes, especially during the initial burn when the solid fuel is fed at a higher rate. Implementing a robust thrust vector control system, such as gimbaled nozzles or reaction control systems, can help maintain stability and control during ascent and maneuvering.
Thermal Management: Solid fuel combustion can generate significant heat, so effective thermal management is essential. The engine design should consider heat dissipation methods to prevent overheating, especially in critical components like the combustion chamber and nozzles. This might involve the use of heat-resistant materials, cooling fins, or efficient cooling systems to maintain optimal operating temperatures.
Safety and Reliability: Given the nature of solid fuels, safety measures are crucial. The engine design should incorporate fail-safe mechanisms to prevent fuel leakage or accidental ignition. This includes proper sealing, insulation, and the use of non-combustible materials in critical areas. Additionally, redundancy in the fuel feed system can enhance reliability, ensuring that the engine can operate even if a portion of the fuel supply is compromised.
By carefully considering these design aspects, you can create a solid fuel engine in KSP that is efficient, reliable, and capable of meeting the specific requirements of your spacecraft's mission. Remember that each solid fuel type may have unique properties, so thorough testing and optimization are essential to achieving the desired performance.
Fuel Line Options for 2009 Silverado: Who's the Best Supplier?
You may want to see also
Safety Measures: Safety protocols for handling solid fuel in KSP's fuel lines
When dealing with solid fuel in Kerbal Space Program (KSP), it's crucial to prioritize safety to ensure the well-being of your crew and the integrity of your spacecraft. Here are some essential safety measures and protocols to follow:
Training and Familiarization: Before handling solid fuel, all crew members should undergo comprehensive training. This training should cover the properties of solid fuel, its combustion behavior, and the potential risks associated with its use. Familiarize yourself with the fuel's handling procedures, including proper storage, transportation, and fueling techniques. Understanding the fuel's characteristics will enable you to make informed decisions and respond appropriately to any emergencies.
Personal Protective Equipment (PPE): Always wear appropriate PPE when working with solid fuel. This may include heat-resistant gloves, protective eyewear, and fire-resistant clothing. PPE acts as a barrier, safeguarding your skin, eyes, and body from potential hazards like burns, splashes, or toxic fumes. Ensure that the PPE is properly fitted and maintained to provide optimal protection.
Ventilation and Containment: Solid fuel combustion can produce hazardous gases and fumes. Therefore, it is imperative to work in a well-ventilated area or use a fume hood to prevent the buildup of toxic substances. Contain the fuel and its byproducts to avoid inhalation or accidental release. Consider using a sealed fueling system or a containment vessel to minimize the risk of exposure.
Secure Storage and Transportation: Store solid fuel in a dry, cool, and well-ventilated area, away from ignition sources and flammable materials. Use appropriate containers that are designed to hold the specific type of solid fuel you are using. During transportation, ensure that the fuel is securely packed and sealed to prevent accidental release or mixing with incompatible substances. Follow all relevant regulations and guidelines for the safe handling and transport of hazardous materials.
Pre-Fuel Check and Procedures: Prior to fueling, conduct a thorough inspection of the fuel lines, nozzles, and connectors. Check for any signs of damage, corrosion, or blockages. Ensure that the fueling system is properly grounded to prevent static electricity buildup, which can ignite the fuel. Implement a standardized fueling procedure, including the use of appropriate tools and techniques to minimize the risk of spills or fuel leakage.
Emergency Response Planning: Develop a comprehensive emergency response plan for solid fuel-related incidents. This should include steps for containment, evacuation, and medical treatment. Train your crew on emergency procedures and ensure they know how to respond to various scenarios, such as fuel leaks, fires, or explosions. Regularly review and update the emergency response plan to address any new challenges or risks associated with solid fuel operations.
By adhering to these safety measures and protocols, you can significantly reduce the risks associated with handling solid fuel in KSP's fuel lines, ensuring a safer and more efficient space exploration experience. Remember, safety should always be the top priority in any space-related endeavor.
2001 Plymouth Neon Fuel Line Hose: Size Guide
You may want to see also
Fuel Efficiency: Solid fuel efficiency compared to liquid fuel in KSP
When it comes to Kerbal Space Program (KSP), understanding the fuel efficiency of different types of fuel is crucial for optimizing your spacecraft's performance. In this context, the comparison between solid fuel and liquid fuel is an interesting one, especially considering the unique characteristics of each.
Solid fuel, often associated with traditional rocket engines, offers a distinct advantage in terms of simplicity and reliability. These engines are typically designed with a single, solid propellant that is burned directly, providing a steady and predictable thrust. This simplicity can lead to more efficient fuel usage, as the combustion process is well-controlled and consistent. Solid fuel systems are known for their ability to provide a continuous and stable thrust, which is beneficial for precise maneuvers and controlled ascent.
On the other hand, liquid fuel systems, such as those using liquid oxygen and liquid hydrogen, offer a different set of advantages. These fuels provide a higher specific impulse, which means they can generate more thrust per unit of fuel mass. Liquid fuel engines often have a higher power-to-weight ratio, allowing for more efficient acceleration and maneuverability. However, they can be more complex due to the need for fuel tanks, pumps, and additional systems to manage the liquid state of the propellant.
In KSP, the efficiency of solid fuel can be attributed to its direct and controlled combustion. The solid nature of the fuel allows for precise metering and mixing with oxidizers, ensuring a consistent burn rate. This predictability enables spacecraft designers to calculate and optimize fuel usage more effectively. Additionally, solid fuel systems often have simpler plumbing and fewer potential leak points, reducing the risk of fuel loss during the mission.
Comparing the two, solid fuel efficiency in KSP can be advantageous for specific missions. Its simplicity and reliability make it ideal for low-thrust applications, such as orbital maneuvers and precise adjustments. However, for high-thrust requirements, liquid fuel might be preferred due to its higher specific impulse and power-to-weight ratio. The choice between solid and liquid fuel ultimately depends on the specific mission objectives, spacecraft design, and the overall efficiency goals of the project.
Cub Cadet Kohler Engine Fuel Line Diameter: A Comprehensive Guide
You may want to see also
Frequently asked questions
Yes, solid fuel can be used in fuel lines in KSP. Solid fuel is a type of rocket propellant that can be loaded into tanks and used to power your spacecraft. It is a common choice for beginners due to its simplicity and ease of use.
Solid fuel offers several benefits. It is easy to manage and does not require complex fueling procedures. It also provides a consistent burn rate, making it predictable for mission planning. Additionally, solid fuel can be a cost-effective option for small-scale missions.
While solid fuel has its advantages, it may not be the best choice for all scenarios. It typically has a lower specific impulse compared to liquid fuels, resulting in less efficient performance. Solid fuel is also less flexible in terms of burn time adjustments, as it burns at a constant rate.
Loading solid fuel is straightforward. You can access the fuel lines in the Vehicle Assembly Building (VAB) or Space Plane Hangar. Simply place the solid fuel tanks into the appropriate slots, ensuring they are correctly aligned with the fuel lines. Make sure to secure the tanks and double-check the connections.
KSP allows for fuel mixing, but it is generally recommended to use the same type of fuel for optimal performance. Mixing solid fuel with liquid fuels can lead to complex fueling procedures and may require additional considerations. It's best to stick with solid fuel for simplicity, especially for beginners.