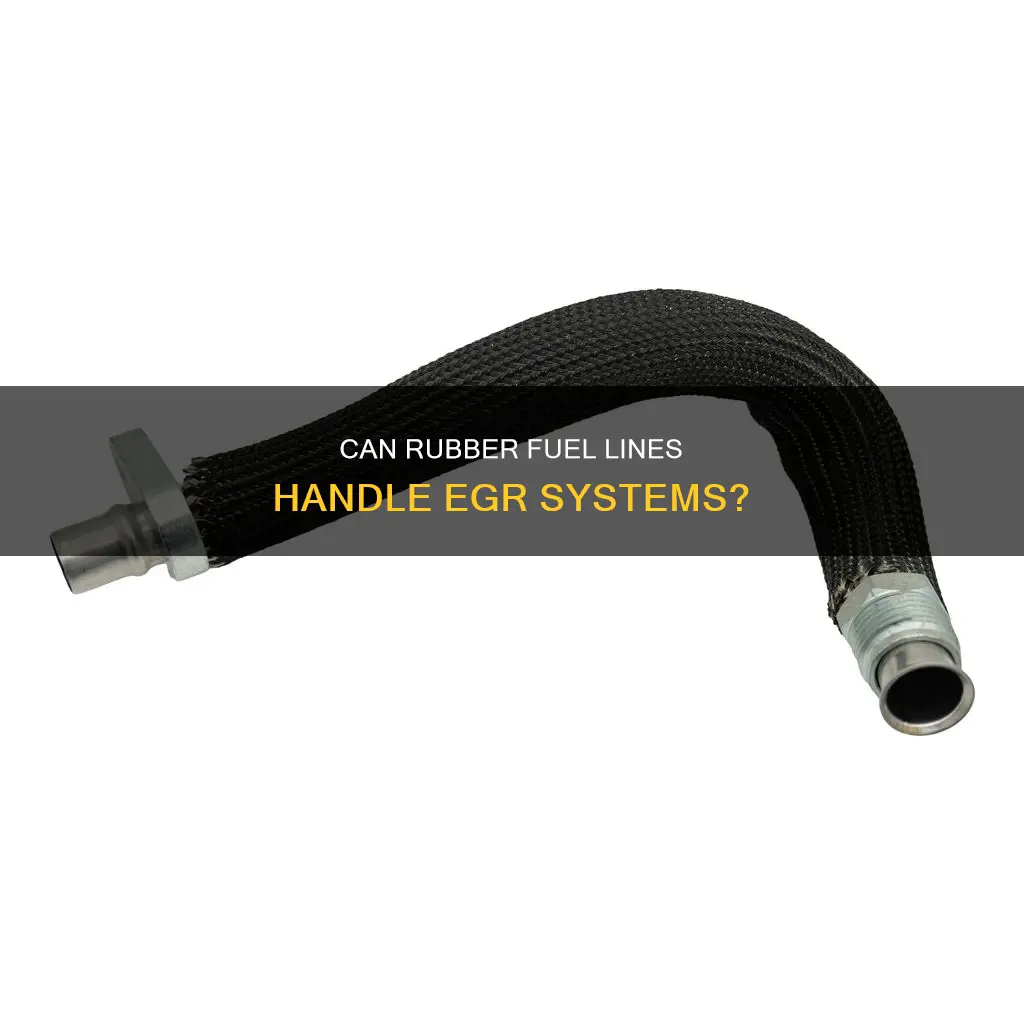
Can rubber fuel lines be used for EGR (Exhaust Gas Recirculation)? This is a common question among vehicle owners and mechanics, especially those looking to upgrade or modify their vehicle's fuel system. Rubber fuel lines are a popular choice for fuel delivery systems due to their flexibility and durability. However, when it comes to EGR systems, which recirculate exhaust gases back into the engine to reduce emissions, the choice of fuel line material becomes crucial. Rubber fuel lines are generally not recommended for EGR applications due to their potential to degrade over time when exposed to high temperatures and corrosive exhaust gases. This degradation can lead to fuel leaks, reduced engine performance, and potential safety hazards. Therefore, it's essential to consider the specific requirements of your EGR system and choose the appropriate fuel line material accordingly.
Characteristics | Values |
---|---|
Material | Rubber |
Compatibility | EGR (Exhaust Gas Recirculation) system |
Temperature Range | Typically -40°F to 250°F (-40°C to 121°C) |
Flexibility | High flexibility for easy installation |
Durability | Resistant to aging, oil, and fuel |
Color | Black, white, or other colors available |
Diameter | Varies, commonly 3/8" to 1/2" |
Length | Customizable, available in various lengths |
Installation | Easy to install and replace |
Cost | Generally affordable compared to other materials |
Availability | Widely available in automotive stores |
Maintenance | Low maintenance required |
What You'll Learn
- Material Compatibility: Rubber fuel lines can withstand EGR system chemicals
- Durability: Rubber is durable, resisting EGR system vibrations and temperatures
- Flexibility: Rubber fuel lines adapt to EGR system movement and angles
- Installation: Rubber fuel lines are easy to install in EGR systems
- Maintenance: Regular inspection and replacement of rubber fuel lines in EGR systems
Material Compatibility: Rubber fuel lines can withstand EGR system chemicals
The compatibility of rubber fuel lines with the chemicals used in Exhaust Gas Recirculation (EGR) systems is a critical consideration when designing and maintaining these systems. Rubber, a versatile and widely used material, offers several advantages for fuel lines in automotive applications. Its inherent flexibility and resilience make it ideal for withstanding the dynamic nature of fuel lines, especially in the presence of varying temperatures and pressure fluctuations.
In the context of EGR systems, the compatibility of rubber with the chemicals used is essential. EGR systems introduce exhaust gases back into the engine's intake system to reduce nitrogen oxide (NOx) emissions. This process involves various chemicals, including acids and bases, which can be corrosive to certain materials. Rubber, however, is known for its chemical resistance, making it a suitable choice for fuel lines in EGR systems. The material's ability to resist degradation from exposure to these chemicals is a key factor in ensuring the longevity and reliability of the system.
The chemical composition of rubber, particularly its resistance to acids and bases, is a result of its molecular structure. Natural rubber, for instance, contains a double bond in its polymer chain, which contributes to its flexibility and durability. This double bond also makes it less susceptible to chemical attacks, ensuring that the fuel lines remain intact and functional over time. Additionally, the addition of reinforcing agents and fillers in the rubber formulation can further enhance its chemical resistance, making it even more suitable for EGR applications.
When selecting rubber fuel lines for EGR systems, it is crucial to consider the specific chemicals and their concentrations present in the system. Some EGR systems may use more aggressive chemicals, requiring rubber with higher levels of chemical resistance. In such cases, specialized rubber compounds, such as those containing antioxidants and reinforcing fillers, can be employed to ensure optimal performance and longevity.
In summary, rubber fuel lines are well-suited for use in EGR systems due to their material compatibility with the chemicals involved. The inherent chemical resistance of rubber, coupled with its flexibility and durability, makes it an excellent choice for withstanding the corrosive effects of EGR system chemicals. By carefully selecting the appropriate rubber compounds, engineers can ensure that the fuel lines remain reliable and efficient, contributing to the overall performance and emissions control of the vehicle.
Mastering the Art: Fuel Line Removal Guide for 05 WRX
You may want to see also
Durability: Rubber is durable, resisting EGR system vibrations and temperatures
The use of rubber fuel lines in an EGR (Exhaust Gas Recirculation) system is a practical consideration for vehicle manufacturers, especially when it comes to durability. Rubber is a material renowned for its resilience and ability to withstand harsh conditions, making it an ideal choice for this application. One of the primary concerns in an EGR system is the potential for vibrations and temperature fluctuations, which can significantly impact the performance and longevity of the components.
Rubber's inherent durability makes it an excellent solution to these challenges. It possesses the necessary flexibility to absorb and dampen vibrations, ensuring that the fuel lines can withstand the dynamic nature of the EGR system without compromising their structural integrity. This is particularly crucial in high-performance vehicles where the EGR system operates under intense conditions.
Furthermore, rubber's temperature resistance is a key factor in its suitability for EGR applications. The EGR system often involves high-temperature exhaust gases, and rubber can maintain its shape and functionality even when exposed to such extreme heat. This resistance to temperature changes ensures that the fuel lines remain effective and reliable over a wide range of operating temperatures, contributing to the overall efficiency and longevity of the vehicle's EGR system.
In summary, the durability of rubber is a significant advantage when considering its use in EGR systems. Its ability to resist vibrations and temperature variations makes it a robust choice, ensuring that the fuel lines can endure the demanding conditions of an EGR setup without degradation in performance. This feature is essential for maintaining the efficiency and reliability of the entire vehicle system.
Understanding Fuel Line Sizes for Your Long 460 Engine
You may want to see also
Flexibility: Rubber fuel lines adapt to EGR system movement and angles
The Engine Exhaust Gas Recirculation (EGR) system is a crucial component in modern vehicle engines, designed to reduce harmful emissions by recirculating a portion of the exhaust gas back into the engine's intake. This system often involves complex plumbing, including fuel lines, which must be flexible and adaptable to accommodate the various movements and angles within the engine bay. Rubber fuel lines are an ideal choice for this application due to their inherent flexibility, making them a preferred option over rigid metal lines.
The EGR system's design often includes multiple pipes and hoses that need to navigate through tight spaces and changing angles. Rubber fuel lines excel in this scenario as they can easily bend and conform to these challenging routes. This flexibility is essential to ensure that the fuel lines remain intact and functional, even when the EGR system moves during engine operation or when the vehicle is subjected to various driving conditions.
In contrast, rigid metal fuel lines would be more susceptible to damage due to their lack of flexibility. They might become kinked or even break if they need to follow a curved path or adjust to the EGR system's movement. Rubber, with its elastic properties, can absorb the stress and strain caused by these movements, providing a more durable and reliable connection.
Furthermore, the adaptability of rubber fuel lines allows for easier installation and maintenance. Technicians can route the lines efficiently, ensuring a neat and secure setup. This flexibility also simplifies any necessary repairs or replacements, as the lines can be adjusted without causing additional strain on the EGR system.
In summary, the flexibility of rubber fuel lines is a critical advantage when integrating them into the EGR system. It ensures the system's longevity, reliability, and ease of maintenance, making rubber an excellent choice for fuel line material in modern vehicle engines. This adaptability is a key factor in the successful operation of the EGR system, contributing to reduced emissions and improved engine performance.
Torquing Stages: Mini Cooper Fuel Line Secrets Unveiled
You may want to see also
Installation: Rubber fuel lines are easy to install in EGR systems
The use of rubber fuel lines in Exhaust Gas Recirculation (EGR) systems is a practical and cost-effective solution for vehicle owners and mechanics alike. While the primary purpose of EGR is to reduce harmful emissions by recirculating a portion of the exhaust gas back into the engine, the system can be complex, especially when it comes to the fuel lines. Rubber fuel lines offer a flexible and durable alternative to traditional metal lines, making them an ideal choice for EGR installations.
Installation of rubber fuel lines in EGR systems is a straightforward process that can be completed by both professionals and DIY enthusiasts. Here's a step-by-step guide to ensure a successful and efficient installation:
- Preparation: Begin by gathering the necessary tools and materials, including the rubber fuel lines, fittings, and any required adapters. Ensure that the EGR system is properly prepared and all components are accessible. It is crucial to inspect the existing fuel lines and connections to identify any potential issues or damage that might require replacement.
- Routing the Lines: Carefully plan the path of the rubber fuel lines to ensure they are not subjected to excessive stress or damage. Rubber lines are flexible, allowing for some movement, but it's essential to avoid sharp bends or kinks that could affect performance. Route the lines away from moving parts and heat sources to prevent potential damage over time.
- Fitting and Connection: Use the appropriate fittings and connectors designed for rubber fuel lines. These fittings should be securely tightened to ensure a tight seal. When connecting the lines, ensure that the ends are properly aligned and that the connections are free from any obstructions. It is recommended to use a lubricant on the fittings to facilitate a smooth connection.
- Testing and Inspection: After the installation, it is crucial to test the system thoroughly. Start the engine and listen for any unusual noises, ensuring that the fuel lines are not rubbing against other components. Check for any leaks at the connections and verify that the EGR system is functioning correctly. Inspect the rubber lines for any signs of damage or wear, especially in areas where they are routed close to the engine or under the vehicle.
- Maintenance and Care: Regular maintenance is essential to ensure the longevity of the rubber fuel lines. Keep the lines clean and free from debris, and regularly inspect them for any signs of deterioration or cracking. Proper care will help prevent leaks and ensure the EGR system operates efficiently.
By following these installation steps, you can effectively integrate rubber fuel lines into your EGR system, providing a reliable and flexible solution for fuel delivery. This method of installation is particularly advantageous for those seeking a more affordable and customizable approach to EGR system upgrades.
Exploring Nickel Copper Wire for Fuel Delivery: A Practical Option?
You may want to see also
Maintenance: Regular inspection and replacement of rubber fuel lines in EGR systems
Regular maintenance of the Exhaust Gas Recirculation (EGR) system is crucial to ensure optimal performance and longevity, especially when it comes to the rubber fuel lines within this system. These fuel lines play a vital role in directing fuel from the fuel tank to the engine, and their condition directly impacts the efficiency and reliability of the EGR system. Over time, rubber fuel lines can degrade due to various factors, including exposure to heat, fuel contaminants, and the natural aging process of the material.
The inspection process should be thorough and routine. Start by visually examining the fuel lines for any signs of damage, cracks, or brittleness. Rubber fuel lines can become brittle and crack over time, especially if they have been exposed to high temperatures or fuel leaks. Look for any discolored or hardened areas, as these could indicate the presence of fuel degradation or the formation of harmful compounds. It is essential to check for any visible signs of wear and tear, as rubber fuel lines are susceptible to cracking and splitting, which can lead to fuel leaks and potential engine issues.
In addition to visual inspections, it is recommended to use a flexible probe to check the interior of the fuel lines for any blockages or debris. This ensures that the fuel flow remains unobstructed, allowing for efficient operation of the EGR system. If any blockages are found, they should be cleared promptly to prevent potential engine performance issues. Regularly cleaning the fuel lines can also help maintain their integrity and ensure optimal fuel delivery.
The replacement of rubber fuel lines is a task that should be undertaken by qualified professionals. When replacing these lines, it is crucial to use high-quality, compatible rubber fuel lines to ensure a proper fit and optimal performance. Old fuel lines should be removed carefully to avoid any damage to the surrounding components. During the installation process, ensure that all connections are secure and properly sealed to prevent any fuel leaks.
In summary, regular maintenance of rubber fuel lines in EGR systems is essential for the overall health and performance of the vehicle. By conducting thorough inspections and promptly replacing damaged or worn-out fuel lines, you can ensure that the EGR system operates efficiently, contributing to improved engine performance and reduced emissions. It is a simple yet critical aspect of vehicle care that should not be overlooked.
Toro Snowblower Fuel Line Sizes: A Comprehensive Guide
You may want to see also
Frequently asked questions
Yes, rubber fuel lines can be used for EGR systems, but it's important to choose the right type of rubber and ensure proper installation. EGR systems require fuel lines that can withstand high temperatures and pressure, so using a high-temperature-rated rubber material is crucial.
Rubber fuel lines offer flexibility, which is beneficial for the EGR system's complex routing. They can accommodate the various angles and bends in the exhaust system. Additionally, rubber is a cost-effective material, making it an attractive option for vehicle manufacturers.
Absolutely! Rubber fuel lines for EGR should be designed to resist heat and chemicals. The rubber should be able to withstand the high temperatures generated by the engine and the exhaust gases. It's also essential to use a rubber compound that is resistant to the chemicals present in the fuel and exhaust, ensuring long-term durability.
Proper installation is critical to the performance and longevity of the EGR system. Start by cleaning the fuel lines and ensuring they are free of any debris. Use the correct fittings and clamps designed for rubber fuel lines. Ensure a tight seal at all connections to prevent any leaks. Regularly inspect the fuel lines for any signs of damage or wear, especially in high-stress areas.