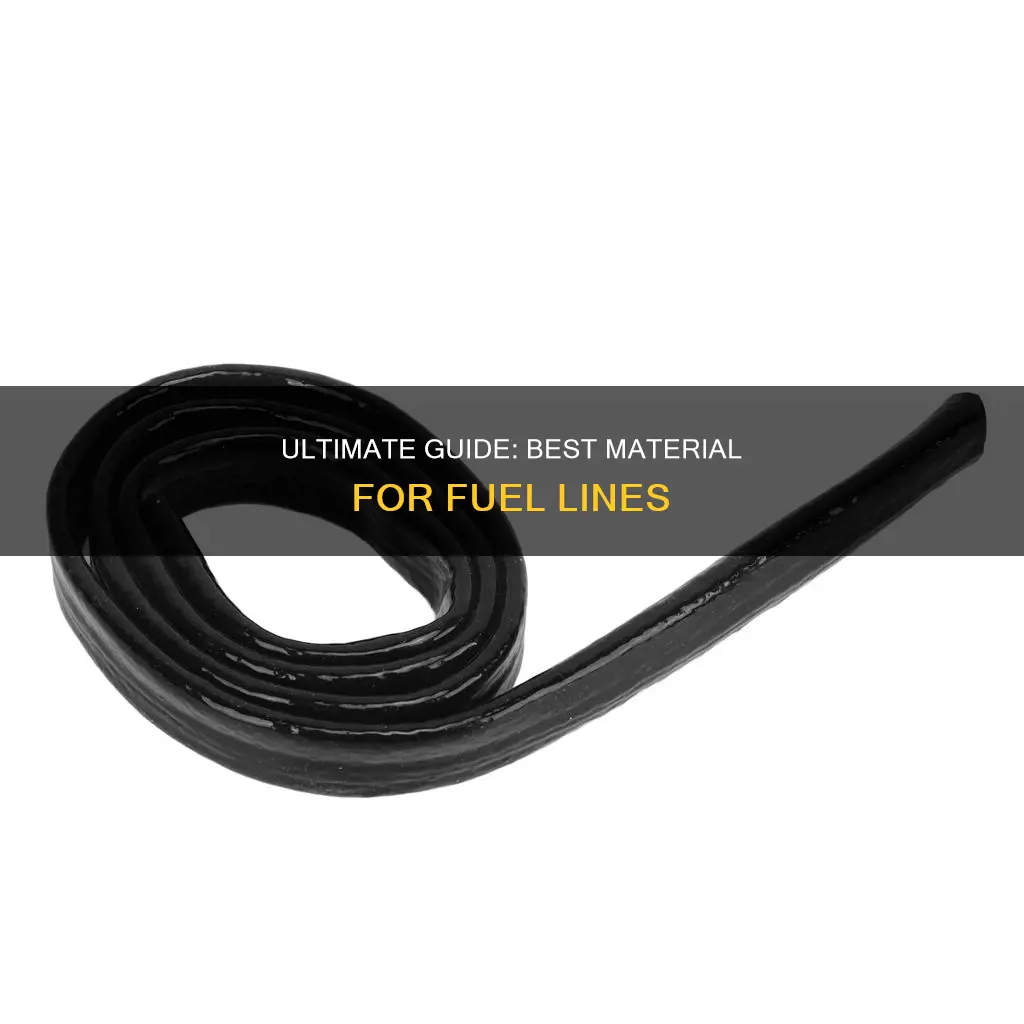
When it comes to choosing the best material for fuel lines, several factors come into play. The ideal material should be durable, resistant to fuel degradation, and capable of withstanding temperature variations without compromising performance. Common options include stainless steel, which offers excellent corrosion resistance and strength, making it a popular choice for high-performance vehicles. However, other materials like brass and aluminum alloys also have their advantages, such as lightweight design and cost-effectiveness. The choice depends on the specific application, environmental conditions, and the type of fuel being used. Understanding these considerations is crucial for selecting the most suitable material to ensure optimal performance and longevity of the fuel system.
What You'll Learn
- Durability: Material must withstand fuel pressure, temperature changes, and chemical resistance
- Flexibility: Fuel lines need to bend and move without cracking or breaking
- Weight: Lighter materials reduce vehicle weight and improve fuel efficiency
- Cost: Affordable options are preferred for mass production
- Compatibility: Materials should not react with fuel, preventing contamination
Durability: Material must withstand fuel pressure, temperature changes, and chemical resistance
When it comes to choosing the best material for fuel lines, durability is a critical factor that cannot be overlooked. Fuel lines are exposed to a variety of harsh conditions, including high fuel pressure, rapid temperature fluctuations, and the presence of corrosive chemicals. Therefore, the material used for these lines must be able to withstand these challenges without compromising performance or safety.
One of the key requirements for durability is the ability to resist fuel pressure. Fuel lines need to handle the force exerted by the fuel as it flows through the system. This pressure can vary depending on the engine's design and operating conditions. Materials that can maintain their structural integrity under high pressure are essential to ensure a reliable and safe fuel supply. For instance, high-density polyethylene (HDPE) and cross-linked polyethylene (PE-X) are known for their excellent pressure resistance, making them popular choices for fuel lines. HDPE, in particular, offers a good balance of strength and flexibility, allowing it to withstand the dynamic nature of fuel pressure without kinking or becoming brittle.
Temperature changes also pose a significant challenge to fuel line durability. Fluctuations in temperature can cause materials to expand or contract, potentially leading to cracks or leaks. Materials with high temperature resistance are crucial to prevent fuel leaks and ensure the longevity of the fuel system. For this purpose, materials like HDPE and certain types of rubber compounds are often used. These materials can handle a wide range of temperatures, from extreme cold to high heat, without losing their flexibility or structural integrity.
In addition to pressure and temperature resistance, chemical resistance is another vital aspect of durability. Fuel contains various additives and impurities that can react with certain materials, leading to degradation or corrosion. The best fuel line materials should be resistant to these chemicals, ensuring that the fuel remains pure and does not contaminate the engine. For example, stainless steel and certain types of rubber, such as EPDM (ethylene propylene diene monomer) rubber, offer excellent chemical resistance, making them suitable for fuel line applications.
Furthermore, the design and construction of the fuel lines also play a role in their durability. The use of flexible braids or reinforcements can enhance the material's ability to withstand pressure and temperature changes. These braids provide additional support and prevent kinking, ensuring a consistent fuel flow. Additionally, the manufacturing process should be meticulous to avoid any weaknesses in the material's joints or connections.
In summary, the durability of fuel lines is a complex consideration, requiring materials that can handle fuel pressure, temperature variations, and chemical exposure. By selecting materials with proven track records, such as HDPE, PE-X, stainless steel, and specific rubber compounds, along with careful design and construction, engineers can ensure that fuel lines meet the demanding requirements of modern engines, providing a reliable and safe fuel supply.
Troubleshooting Fuel Line Issues: Signs and Solutions
You may want to see also
Flexibility: Fuel lines need to bend and move without cracking or breaking
Flexibility is a critical aspect of fuel lines, especially in automotive applications, as it ensures the system can withstand the various movements and vibrations encountered during vehicle operation. The primary goal is to prevent fuel lines from cracking or breaking when the vehicle is in motion, which could lead to fuel leaks and potential safety hazards.
One of the best materials for fuel lines that offers excellent flexibility is rubber. Natural rubber has been traditionally used for this purpose due to its inherent flexibility and resilience. It can absorb vibrations and bend without compromising its structural integrity. Modern fuel lines often utilize synthetic rubbers, such as neoprene or EPDM (Ethylene Propylene Diene Monomer), which provide superior flexibility and durability compared to natural rubber. These synthetic rubbers are designed to withstand a wide range of temperatures and environmental conditions, ensuring that the fuel lines remain flexible even in extreme weather.
In addition to rubber, polyurethane (PU) is another popular choice for fuel lines. PU offers exceptional flexibility and is known for its ability to resist cracking and breaking. It is a versatile material that can be formulated to provide different levels of flexibility, making it suitable for various fuel line applications. The flexibility of PU is achieved through its unique molecular structure, which allows it to deform and return to its original shape without permanent set. This property is crucial for fuel lines, as it ensures that the lines can accommodate the vehicle's movements without compromising the fuel supply.
When designing fuel lines, engineers often consider the specific requirements of the application. For high-performance vehicles or those operating in extreme conditions, materials like PU with added flexibility enhancers might be used. These enhancers can include additives that increase the material's elasticity, making it even more adaptable to movement. The goal is to create fuel lines that can bend and move freely without any risk of cracking, ensuring a reliable and safe fuel supply.
Furthermore, the flexibility of fuel lines is not just about the material but also the construction. Fuel lines are often designed with multiple layers or braids to enhance flexibility. For instance, a braided fuel line uses a metal or synthetic fiber core surrounded by a flexible outer layer, allowing it to bend and move without restricting the flow of fuel. This construction method is particularly useful in high-pressure fuel systems, where flexibility is essential to prevent damage to the fuel lines.
Understanding Dirt Bike Fuel Lines: Metric or Not?
You may want to see also
Weight: Lighter materials reduce vehicle weight and improve fuel efficiency
When it comes to choosing the best material for fuel lines, one of the most critical considerations is weight. Lighter materials are a game-changer in the automotive industry, offering a multitude of benefits that contribute to improved vehicle performance and efficiency. By reducing the weight of fuel lines, engineers can significantly enhance a vehicle's overall fuel efficiency, which is a crucial factor in modern transportation.
The concept of weight reduction in fuel lines is based on the principle of minimizing unnecessary mass. Traditional fuel lines were often made of heavy metals like steel, which, while durable, contributed to the overall weight of the vehicle. Over time, this excess weight could lead to decreased fuel efficiency, as the vehicle had to work harder to accelerate and maintain speed. Lighter materials, such as aluminum alloys or high-density plastics, offer a solution to this problem. These materials provide excellent structural integrity while being significantly less dense, allowing for a more efficient design.
The benefits of using lighter materials in fuel lines extend beyond just weight reduction. Lighter components often result in improved handling and responsiveness, as the vehicle's overall center of gravity is lowered. This can lead to better stability, especially during high-speed maneuvers, and a more dynamic driving experience. Additionally, the reduced weight can contribute to faster acceleration, as the engine doesn't have to work as hard to move the lighter vehicle.
In the pursuit of lighter fuel lines, engineers have explored various materials and designs. One popular choice is the use of aluminum alloys, which offer a high strength-to-weight ratio. These alloys can provide the necessary structural integrity for fuel lines while keeping the weight down. Another innovative approach is the utilization of high-density plastics, which have gained popularity due to their lightweight nature and resistance to corrosion. These materials ensure that fuel lines remain durable and efficient, even in harsh environmental conditions.
Furthermore, the adoption of lighter materials in fuel lines can have a positive environmental impact. Improved fuel efficiency means less fuel consumption, which directly translates to reduced emissions. With a focus on sustainability and eco-friendly practices, the automotive industry is increasingly recognizing the importance of weight reduction in vehicle components. By choosing the right materials, manufacturers can contribute to a greener future, making vehicles more efficient and environmentally friendly.
Fuel Line Removal Guide: Chevy Silverado Edition
You may want to see also
Cost: Affordable options are preferred for mass production
When it comes to choosing the best material for fuel lines, especially for mass production, cost is a significant factor that cannot be overlooked. The primary goal is to find a material that offers both durability and affordability without compromising on performance. This balance is crucial for manufacturers, especially those aiming to produce vehicles or machinery on a large scale.
One of the most commonly used materials for fuel lines is rubber, specifically natural or synthetic rubber compounds. Rubber is an excellent choice due to its flexibility, which allows it to withstand the constant movement and vibration that fuel lines experience. It is also resistant to most fuels, including gasoline and diesel, making it a reliable option. However, the cost of rubber can vary depending on the type and quality, with natural rubber being more expensive than synthetic alternatives. Despite this, rubber remains a popular choice for fuel lines due to its ease of manufacturing and the ability to form complex shapes.
Another affordable and widely used material is nylon. Nylon fuel lines are known for their strength and flexibility, making them suitable for a variety of applications. They are also resistant to abrasion and chemicals, ensuring a long-lasting performance. The cost of nylon is generally lower than that of rubber, especially for high-quality grades, making it an attractive option for mass production. Additionally, nylon fuel lines are less prone to cracking and can handle higher temperatures, further enhancing their suitability for demanding environments.
For those seeking an even more cost-effective solution, PVC (polyvinyl chloride) can be considered. PVC is a lightweight and durable material that is resistant to most fuels and chemicals. It is also easy to install and can be joined using various methods, including welding and adhesives. The affordability of PVC makes it an excellent choice for budget-conscious manufacturers, especially when used in conjunction with other cost-saving techniques during the production process.
In conclusion, while there are various materials available for fuel lines, cost remains a critical consideration for mass production. Rubber, nylon, and PVC are all viable options, each offering unique advantages in terms of durability, flexibility, and resistance to fuels and chemicals. By choosing the right material, manufacturers can ensure that their fuel lines are both reliable and economically feasible, contributing to the overall success of their production endeavors.
Craftsman 316292621 Fuel Line: Size Guide for Optimal Performance
You may want to see also
Compatibility: Materials should not react with fuel, preventing contamination
When it comes to choosing the best material for fuel lines, compatibility is a critical factor that cannot be overlooked. Fuel lines are responsible for transporting fuel from the tank to the engine, and any material used in their construction must be compatible with the fuel being carried to ensure optimal performance and prevent contamination. Incompatible materials can lead to various issues, including fuel degradation, reduced engine efficiency, and even potential safety hazards.
One of the primary concerns regarding compatibility is the potential for chemical reactions between the fuel and the material of the fuel lines. Different fuels, such as gasoline, diesel, or aviation fuel, contain various additives and components that can interact with certain materials. For example, some plastics may react with ethanol-blended fuels, leading to swelling or degradation of the material over time. Similarly, rubber fuel lines might not be suitable for fuels containing certain chemicals, as they can cause the rubber to become brittle or disintegrate.
To ensure compatibility, it is essential to consider the chemical properties of the fuel and the material's resistance to fuel-related degradation. Materials like stainless steel, brass, and certain types of rubber (e.g., natural rubber or EPDM) are often preferred for fuel lines because they exhibit excellent resistance to a wide range of fuels. Stainless steel, for instance, is highly resistant to corrosion and oxidation, making it suitable for various fuel types. Brass, on the other hand, is known for its ability to withstand the effects of gasoline and diesel fuels without compromising its structural integrity.
Additionally, the choice of material should also consider the temperature range and operating conditions of the fuel system. Some materials may be more suitable for high-temperature environments, while others excel in low-temperature applications. For instance, fuel lines used in high-performance engines or racing applications might require materials that can withstand extreme temperatures and provide excellent flexibility.
In summary, compatibility is a key consideration when selecting the best material for fuel lines. The chosen material should not react with the fuel, preventing contamination and ensuring the efficient and safe operation of the fuel system. By understanding the chemical properties of different fuels and the degradation potential of various materials, engineers and enthusiasts can make informed decisions to optimize the performance and longevity of fuel lines in various applications.
E85 Fuel Line: Choosing the Right Option for Your Engine
You may want to see also
Frequently asked questions
The most common material for fuel lines is steel, often in the form of a flexible steel hose. Steel is durable and can withstand high pressure, making it suitable for the demanding conditions of fuel delivery systems.
Yes, a popular choice is stainless steel, which offers excellent corrosion resistance. This is particularly beneficial in environments with varying temperatures and moisture, ensuring the fuel lines remain reliable over time. Additionally, stainless steel can handle higher pressure, making it a preferred option for performance-oriented vehicles.
In some cases, rubber or synthetic materials like polyurethane are used, especially for older vehicles or specific models. These materials are flexible and can absorb vibrations, providing a smoother ride. However, they may not be as durable as steel and can be more susceptible to degradation over time, especially in harsh conditions.