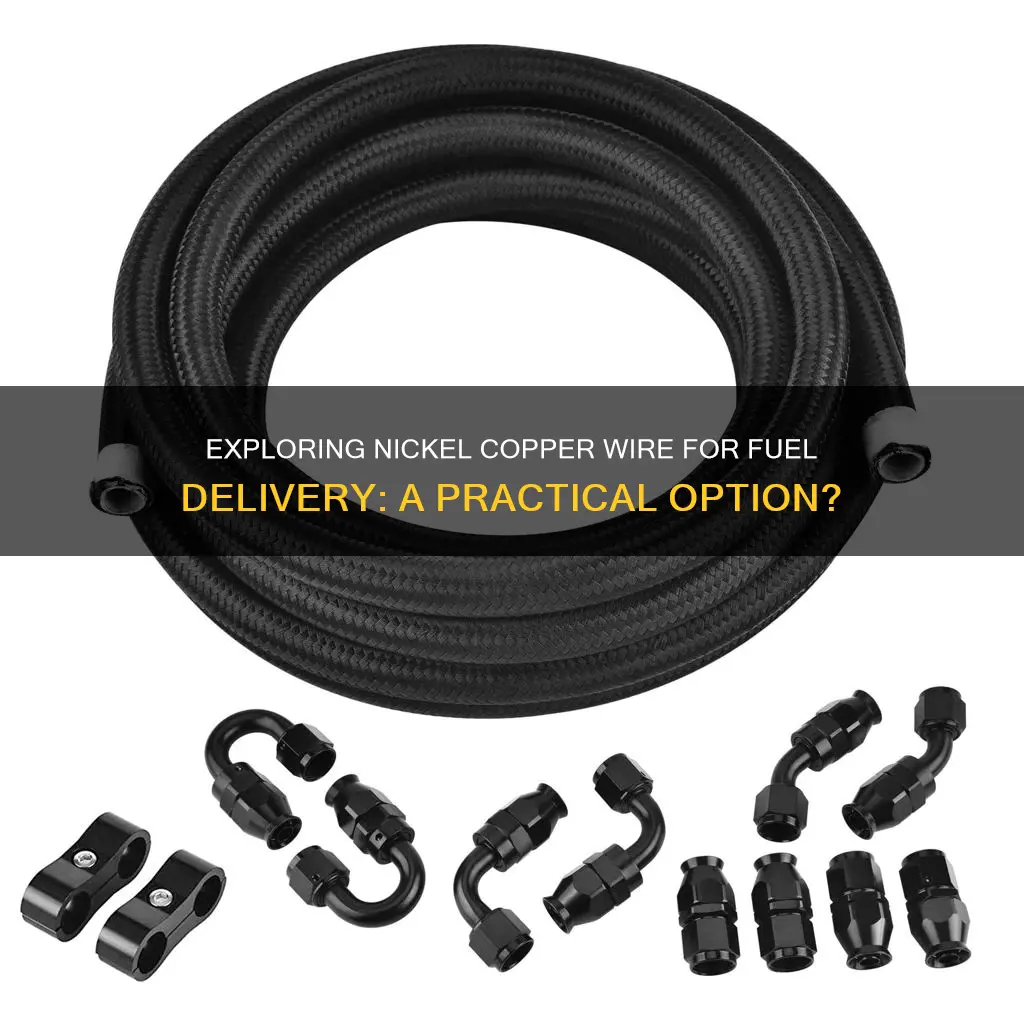
Can I use nickel-copper lines for fuel? This is an intriguing question that delves into the realm of material science and engineering. Nickel-copper lines, typically used for electrical conductivity and heat transfer, are not designed for fuel storage or transportation. The properties of these materials, such as their high melting point and resistance to corrosion, make them unsuitable for the volatile and corrosive nature of fuels. However, the question opens up a discussion on the potential for innovative material solutions in the energy sector, where researchers and engineers are constantly exploring new ways to harness and utilize energy more efficiently and sustainably.
What You'll Learn
- Material Compatibility: Nickel-copper lines can be used for fuel if compatible with the fuel type
- Corrosion Resistance: Nickel-copper alloys offer excellent resistance to corrosion in fuel environments
- Temperature Tolerance: These lines can withstand high temperatures, making them suitable for fuel transport
- Flexibility and Durability: Nickel-copper lines are flexible and durable, ensuring reliable fuel transmission
- Regulatory Compliance: Adherence to fuel industry standards is essential for nickel-copper line usage
Material Compatibility: Nickel-copper lines can be used for fuel if compatible with the fuel type
When considering the use of nickel-copper lines for fuel systems, material compatibility is a critical factor to ensure the safety and efficiency of the setup. Nickel-copper alloys, known for their excellent corrosion resistance and mechanical properties, can indeed be utilized for fuel lines if they are compatible with the specific fuel type. This compatibility is essential to prevent any adverse reactions that could compromise the integrity of the fuel system.
The compatibility of nickel-copper lines with fuel depends on several factors, including the type of fuel, its chemical composition, and the operating conditions. For instance, some fuels, such as gasoline, may not react with nickel-copper alloys, making them suitable for fuel lines. However, other fuels, like ethanol blends or certain types of biofuels, could potentially cause corrosion or degradation of the nickel-copper material over time. Therefore, it is crucial to conduct thorough research and testing to ensure that the chosen nickel-copper alloy is compatible with the intended fuel.
To determine compatibility, one should consider the following: First, the nickel-copper alloy should be resistant to the chemical components of the fuel, including any additives or impurities. Second, the operating temperature and pressure of the fuel system must be within the capabilities of the nickel-copper material to avoid any stress-related failures. Third, the alloy's mechanical properties, such as tensile strength and ductility, should be suitable for the expected fuel line applications.
In the case of gasoline, nickel-copper alloys like N04400 (Monel 400) or N06455 (Inconel 625) are often used due to their excellent resistance to corrosion and oxidation. These alloys can withstand the harsh environment of gasoline fuel systems, ensuring long-term compatibility. However, for other fuels, alternative materials or specific surface treatments might be required to achieve the necessary compatibility.
In summary, while nickel-copper lines offer numerous advantages for fuel systems, their use should be carefully evaluated based on material compatibility with the fuel type. Proper selection and testing of the nickel-copper alloy will ensure a reliable and safe fuel system, minimizing the risk of fuel contamination, corrosion, or system failure. This approach is essential for maintaining the performance and longevity of the fuel infrastructure.
Dorman Fuel Line Sizes: A Comprehensive Guide for 55240
You may want to see also
Corrosion Resistance: Nickel-copper alloys offer excellent resistance to corrosion in fuel environments
The use of nickel-copper alloys in fuel systems is a critical consideration due to their exceptional corrosion resistance, making them ideal for environments where fuel is present. These alloys are specifically designed to withstand the corrosive effects of various fuels, ensuring the longevity and reliability of the system.
One of the key advantages of nickel-copper alloys is their ability to resist pitting corrosion, a common issue in fuel systems. Pitting corrosion can lead to localized damage and eventual failure, but these alloys have a unique microstructure that prevents such attacks. The presence of nickel, a noble metal, and copper, both of which are highly resistant to corrosion, creates a protective layer on the surface, known as an oxide film. This film acts as a barrier, preventing the fuel from coming into direct contact with the metal and thus inhibiting corrosion.
In fuel environments, where fuels like gasoline, diesel, and aviation fuel are present, the corrosive nature of these substances is well-documented. Nickel-copper alloys excel in these conditions due to their inherent resistance to oxidation and the formation of stable, protective oxide layers. This resistance ensures that the alloys maintain their structural integrity over time, even when exposed to fuels with varying chemical compositions and properties.
Furthermore, the mechanical properties of these alloys are also noteworthy. They possess excellent tensile strength, ductility, and toughness, ensuring that the material can withstand the demands of fuel systems without compromising its structural integrity. This combination of corrosion resistance and mechanical strength makes nickel-copper alloys a preferred choice for fuel lines, pipes, and other components that require long-term reliability.
In summary, nickel-copper alloys are an excellent solution for fuel systems due to their superior corrosion resistance. Their ability to form protective oxide layers and withstand the corrosive nature of fuels makes them a reliable choice for ensuring the safety and efficiency of fuel-related infrastructure. This makes them a valuable consideration for engineers and designers working on fuel-related projects.
Mastering the Quick Connect Swap: Nylon Fuel Line Guide
You may want to see also
Temperature Tolerance: These lines can withstand high temperatures, making them suitable for fuel transport
The ability of nickel-copper lines to withstand high temperatures is a critical factor in their suitability for fuel transport. These materials possess excellent thermal stability, allowing them to maintain their structural integrity and performance even under extreme conditions. This is particularly important in the context of fuel transportation, where temperatures can vary significantly depending on the environment and the specific application.
Nickel-copper alloys, such as Monel or Inconel, are known for their exceptional resistance to heat. They can tolerate temperatures ranging from extremely low to very high, often exceeding 1000°C (1832°F). This temperature tolerance is essential for fuel transport systems, as it ensures the safety and reliability of the infrastructure. For instance, in the case of a fuel pipeline, the lines must be able to withstand the heat generated during the transportation process, especially when dealing with high-pressure and high-temperature fuels like natural gas or oil.
The high-temperature resistance of nickel-copper lines is attributed to their unique microstructure and the presence of elements like nickel and copper. These elements form a strong bond, creating a material with exceptional strength and durability. This strength enables the lines to resist deformation and maintain their shape even when exposed to intense heat, preventing potential leaks or failures in the transportation system.
Furthermore, the temperature tolerance of these lines is not limited to just the material itself but also includes its ability to handle temperature changes over time. Nickel-copper alloys can undergo thermal cycling without compromising their structural integrity. This is crucial for fuel transport applications, as temperatures may fluctuate during the transportation process, especially in outdoor environments.
In summary, the temperature tolerance of nickel-copper lines is a key advantage that makes them an ideal choice for fuel transport. Their ability to withstand high temperatures and handle temperature variations ensures the safe and efficient transportation of fuels, contributing to the overall reliability of the energy infrastructure. This property, combined with their corrosion resistance and mechanical strength, makes nickel-copper alloys a preferred material for various fuel transport systems.
Braided Fuel Line Heat Resistance: Unraveling the Truth
You may want to see also
Flexibility and Durability: Nickel-copper lines are flexible and durable, ensuring reliable fuel transmission
The use of nickel-copper lines for fuel transmission offers a unique combination of flexibility and durability, making it an ideal choice for various applications. These lines are specifically designed to withstand the challenges of fuel transportation, ensuring a reliable and efficient process.
One of the key advantages of nickel-copper lines is their flexibility. This material is engineered to be pliable, allowing it to navigate through tight spaces and bends without compromising its structural integrity. When compared to traditional rigid pipes, nickel-copper lines provide a more adaptable solution, especially in complex fuel distribution systems. This flexibility is crucial in installations where space is limited or where the line needs to accommodate various angles and curves.
Additionally, the durability of nickel-copper lines is a significant factor in their suitability for fuel transmission. These lines are constructed with a robust composition, ensuring they can withstand the corrosive nature of fuels and the harsh environmental conditions they may encounter. The material's resistance to abrasion and impact means that the lines can endure the rigors of fuel transportation, including potential vibrations and temperature fluctuations. This durability is essential for maintaining the integrity of the fuel and ensuring a continuous and reliable supply.
The flexibility and durability of nickel-copper lines contribute to the overall reliability of fuel transmission. These lines can adapt to the unique demands of different fuel types and environments, providing a consistent and dependable performance. Whether it's a residential fuel supply or an industrial fuel distribution network, nickel-copper lines offer a versatile solution that can be tailored to specific requirements.
In summary, the flexibility and durability of nickel-copper lines make them an excellent choice for fuel transmission. Their ability to navigate tight spaces, combined with their resistance to corrosion and environmental factors, ensures a reliable and efficient fuel distribution system. This makes nickel-copper lines a valuable asset in various industries, providing a flexible and long-lasting solution for fuel transportation needs.
Blue Uerathyane Fuel Line: Safe for Ethanol Gasoline?
You may want to see also
Regulatory Compliance: Adherence to fuel industry standards is essential for nickel-copper line usage
The use of nickel-copper lines for fuel transportation and distribution is a specialized application that requires strict adherence to industry regulations and standards. These lines are designed to handle specific types of fuels, and their installation and maintenance must comply with relevant guidelines to ensure safety, efficiency, and environmental protection. Regulatory compliance is a critical aspect of this process, as it ensures that the infrastructure meets the necessary criteria for fuel handling.
In the fuel industry, standards are set to govern the materials, construction, and performance of pipelines, especially those used for hazardous substances like fuels. Nickel-copper lines, being a composite material, must be evaluated against these standards to determine their suitability for fuel transport. Regulatory bodies often provide guidelines for material selection, ensuring that the lines can withstand the corrosive nature of fuels, especially those containing sulfur or other aggressive chemicals. Compliance with these standards is essential to prevent leaks, ensure product quality, and maintain the integrity of the fuel supply chain.
One of the key regulatory considerations is the material's resistance to corrosion and its ability to maintain structural integrity over time. Nickel-copper alloys are chosen for their superior corrosion resistance, especially in environments where fuels may contain impurities or aggressive chemicals. However, the specific grade and composition of the nickel-copper line must be approved by relevant authorities to ensure it meets the required performance standards. This includes testing for factors like tensile strength, ductility, and resistance to stress corrosion, which are critical for the safe operation of fuel lines.
Industry standards also dictate the design and installation practices for nickel-copper lines. This includes specifications for pipe thickness, welding procedures, and the use of appropriate fittings and valves. Compliance with these standards ensures that the lines are built to withstand the pressures and temperatures associated with fuel transportation and can operate reliably over their expected lifespan. Additionally, regulations may require regular inspections and maintenance to identify and rectify any issues promptly, further emphasizing the importance of adhering to industry standards.
Furthermore, regulatory compliance is essential for insurance and liability purposes. Fuel companies and transportation providers must demonstrate that their infrastructure, including nickel-copper lines, meets or exceeds industry standards. This documentation can help in obtaining and maintaining insurance coverage, which is crucial for financial protection against potential accidents or environmental incidents. Adherence to regulations also facilitates the certification process, allowing businesses to operate legally and safely within the fuel industry.
Mastering Fuel Line Maintenance: Quick Release Connector Removal Tips
You may want to see also
Frequently asked questions
Yes, nickel-copper wire is often used for fuel lines due to its excellent corrosion resistance and durability. It can withstand the harsh conditions of fuel transport and is commonly employed in automotive and marine applications.
This material offers superior resistance to corrosion, especially in the presence of fuel, which helps ensure the longevity of the fuel system. It also has good flexibility and can be easily installed, making it a practical choice for fuel line applications.
Absolutely! Nickel-copper wire is known for its ability to handle high-pressure environments, making it ideal for fuel lines that require increased pressure. Its mechanical strength and resistance to fatigue make it a reliable option for such applications.