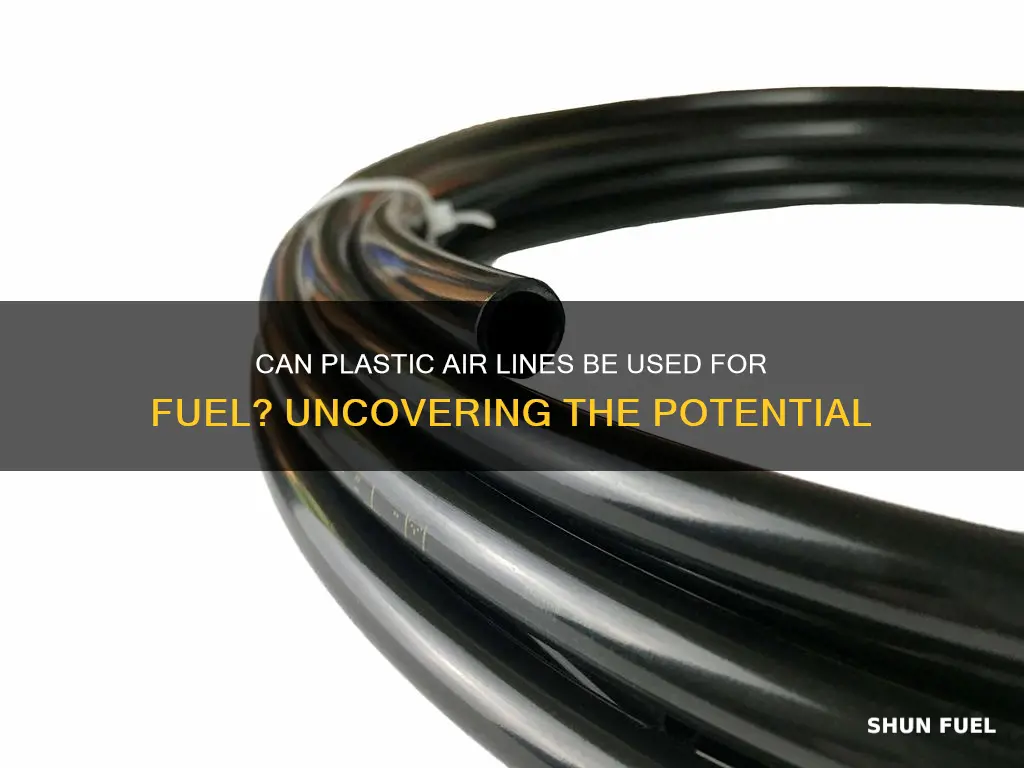
The use of plastic air lines for fuel is a topic that has sparked interest and debate in various industries. While plastic materials have traditionally been associated with non-structural applications, recent advancements have led to the exploration of their potential in fuel delivery systems. This paragraph aims to introduce the concept by highlighting the unique properties of plastic air lines and their potential advantages over traditional metal or rubber alternatives. It will discuss the benefits of using plastic, such as its lightweight nature, corrosion resistance, and cost-effectiveness, which could make it an attractive option for fuel lines in certain applications. Additionally, it will mention the ongoing research and development efforts to ensure the safety and reliability of plastic air lines for fuel use, addressing any concerns related to material compatibility and performance.
What You'll Learn
- Material Compatibility: Plastic airline materials may not be compatible with fuel, leading to degradation
- Pressure and Temperature: High pressure and temperature in fuel systems can affect plastic pipeline performance
- Leakage and Safety: Plastic pipelines may leak fuel, posing safety risks and environmental concerns
- Corrosion Resistance: Plastic's corrosion resistance is crucial for long-term fuel pipeline reliability
- Regulatory Compliance: Plastic fuel lines must meet industry standards and regulations for safe operation
Material Compatibility: Plastic airline materials may not be compatible with fuel, leading to degradation
The compatibility of plastic airline materials with fuel is a critical consideration in aviation. Plastic components, such as air lines, are often used in aircraft systems due to their lightweight and cost-effectiveness. However, when it comes to fuel, the compatibility of these materials becomes a significant concern.
Plastic materials, particularly those commonly used in aviation, such as polyvinyl chloride (PVC) and polypropylene (PP), may not be compatible with the chemicals present in aviation fuels. Aviation fuels often contain additives and blends that can cause degradation in plastic materials over time. This degradation can lead to several issues, including reduced material strength, brittleness, and even material failure. For instance, the presence of certain fuel additives, such as antioxidants and stabilizers, can accelerate the breakdown of plastic, leading to a loss of structural integrity.
The degradation of plastic air lines due to fuel compatibility issues can have serious consequences. It may result in reduced performance, increased maintenance requirements, and potential safety hazards. In extreme cases, the degradation could lead to the failure of critical components, causing aircraft malfunctions or even accidents. Therefore, it is essential to carefully select and test plastic materials to ensure their compatibility with aviation fuels.
To address this challenge, manufacturers and researchers are exploring alternative materials and designs that offer better compatibility with aviation fuels. This includes the development of specialized plastics that are more resistant to fuel degradation, as well as the use of hybrid materials that combine the benefits of different polymers. Additionally, proper maintenance and regular inspections of plastic components can help identify and mitigate any compatibility issues that may arise.
In summary, the compatibility of plastic airline materials with fuel is a critical aspect of aviation safety and performance. While plastic components offer advantages in terms of weight and cost, the potential for degradation due to fuel incompatibility cannot be overlooked. By understanding the specific challenges and implementing appropriate solutions, the aviation industry can ensure the safe and reliable operation of aircraft systems that utilize plastic materials.
Fuel Line Reversal: Signs and Solutions for Engine Issues
You may want to see also
Pressure and Temperature: High pressure and temperature in fuel systems can affect plastic pipeline performance
The use of plastic pipelines for fuel transportation is an intriguing concept, especially in the aviation industry, where lightweight and cost-effective solutions are always sought after. However, the performance of these plastic lines under high pressure and temperature conditions is a critical aspect that requires careful consideration. When fuel is transported through plastic pipelines, the internal pressure and temperature can significantly impact the material's integrity and overall system efficiency.
High-pressure environments in fuel systems can lead to several challenges for plastic pipelines. Firstly, the increased pressure may cause the plastic material to deform or even rupture, especially if the pipeline is not designed to withstand such forces. This can result in fuel leaks, which are not only dangerous but also environmentally detrimental. Secondly, the pressure can affect the flow rate and distribution of fuel, potentially leading to uneven fuel supply to different parts of an aircraft's engine. Ensuring consistent and precise fuel delivery is crucial for optimal engine performance.
Temperature also plays a pivotal role in this context. Fuel systems often operate under varying temperatures, and these temperature fluctuations can cause thermal expansion and contraction of the plastic pipeline. If the pipeline material is not compatible with the fuel's temperature range, it may lead to material degradation, cracking, or even failure. For instance, certain plastics might not be suitable for fuels with high-temperature components, as they could soften or become brittle, compromising the pipeline's structural integrity.
To address these challenges, engineers must carefully select plastic materials that can withstand the specific pressure and temperature conditions of the fuel system. This involves considering factors such as the fuel's chemical composition, operating temperatures, and the maximum pressure the pipeline will encounter. Additionally, implementing proper design and installation practices, such as using flexible joints and pressure-resistant fittings, can help mitigate the risks associated with high pressure and temperature.
In summary, while plastic pipelines offer advantages in terms of weight and cost, their application in fuel systems demands rigorous consideration of pressure and temperature effects. By understanding and managing these factors, engineers can ensure the safe and efficient operation of plastic pipelines for fuel transportation, contributing to the overall reliability of aviation systems. This knowledge is essential for the development of innovative and sustainable solutions in the aviation industry.
Smoking Fuel: A Guide to Identifying and Fixing Issues
You may want to see also
Leakage and Safety: Plastic pipelines may leak fuel, posing safety risks and environmental concerns
The use of plastic pipelines for fuel transportation has been a subject of interest and concern, especially regarding its potential leakage and associated safety risks. While plastic materials have been widely utilized in various industries due to their lightweight and cost-effectiveness, their application in fuel transportation systems requires careful consideration. Plastic pipelines, when used for carrying fuel, can present significant challenges and potential hazards that need to be addressed to ensure the safety of both personnel and the environment.
One of the primary concerns with plastic pipelines is the possibility of fuel leakage. Plastic materials, such as those commonly used in fuel lines, may not be as robust or resistant to fuel degradation as metal alternatives. Over time, fuel can cause plastic pipelines to deteriorate, leading to cracks, brittleness, and ultimately, leaks. These leaks can occur at various points along the pipeline, including connections, joints, and fittings. When fuel escapes, it poses immediate safety risks, including the potential for fire, explosions, and environmental contamination.
The consequences of fuel leakage from plastic pipelines can be severe. In the event of a leak, fuel can rapidly spread, creating hazardous conditions. Plastic fuel lines may not have the same inherent strength and flexibility as metal lines, making them more susceptible to damage during installation, maintenance, or in the event of an accident. A small breach can quickly escalate, leading to significant fuel loss and potential environmental disasters. Moreover, the release of fuel into the environment can have detrimental effects on ecosystems, wildlife, and local communities.
To mitigate these risks, it is crucial to implement strict safety measures and adhere to industry standards. Regular inspections and maintenance routines should be established to identify and repair any potential weaknesses or damage to the plastic pipelines. Using high-quality, fuel-resistant plastic materials and ensuring proper installation techniques can also reduce the likelihood of leaks. Additionally, implementing backup safety systems, such as pressure relief valves or emergency shut-off mechanisms, can help minimize the impact of potential leaks and provide an additional layer of protection.
In summary, while plastic pipelines offer advantages in terms of cost and weight, their use in fuel transportation systems should be approached with caution. The potential for fuel leakage and the associated safety and environmental risks cannot be overlooked. By recognizing these challenges and implementing appropriate safety protocols, the industry can work towards minimizing the hazards posed by plastic pipelines and ensuring the safe and responsible transportation of fuel.
Fuel Line for Power Steering: A Viable Option?
You may want to see also
Corrosion Resistance: Plastic's corrosion resistance is crucial for long-term fuel pipeline reliability
The use of plastic air lines for fuel transportation is an innovative concept that has gained traction in various industries. While the idea of utilizing plastic for fuel lines might seem unconventional, it offers several advantages, especially when considering the critical aspect of corrosion resistance. Corrosion is a natural process that can significantly impact the longevity and reliability of fuel pipelines, and this is where the unique properties of plastics come into play.
Plastics, such as certain types of polyolefins and polyvinylidene chloride, exhibit excellent corrosion resistance, making them ideal candidates for fuel pipeline applications. These materials are inherently resistant to the corrosive effects of fuels, including gasoline, diesel, and aviation fuels. Unlike traditional metal pipelines, which can suffer from internal corrosion over time, plastic fuel lines provide a more durable and reliable solution. The resistance to corrosion is particularly important in fuel systems, as it ensures the integrity of the fuel and prevents contamination, which could lead to engine performance issues.
One of the key advantages of using plastic for fuel lines is the ability to maintain the purity of the fuel. Corrosion in metal pipelines can lead to the leaching of metals and other contaminants into the fuel, affecting its quality. Plastics, being non-reactive, ensure that the fuel remains uncontaminated, thus preserving its performance and combustion characteristics. This is especially crucial in aviation, where fuel quality is critical for aircraft safety and performance.
Furthermore, the corrosion resistance of plastics contributes to the overall longevity of the fuel pipeline system. Plastic lines are less susceptible to degradation and cracking, which are common issues with metal pipelines over time. This means that plastic fuel lines can withstand the rigors of fuel transportation and storage without compromising their structural integrity. As a result, the maintenance and replacement costs associated with fuel pipelines can be significantly reduced, making it a cost-effective solution for long-term fuel management.
In summary, the use of plastic air lines for fuel transportation is a promising approach, especially when considering the critical factor of corrosion resistance. Plastics offer a reliable and durable solution for fuel pipelines, ensuring the purity and integrity of the fuel while providing long-term cost savings. With their excellent corrosion-resistant properties, plastics are well-suited to meet the demanding requirements of fuel systems, making them a valuable consideration in the design and implementation of fuel infrastructure.
Nylon's Fuel Line: A Reliable Choice for Your Engine?
You may want to see also
Regulatory Compliance: Plastic fuel lines must meet industry standards and regulations for safe operation
The use of plastic fuel lines in vehicles and machinery is a topic that requires careful consideration, especially when it comes to regulatory compliance and safety. Plastic materials, such as those commonly used for air lines, have been utilized in various automotive and industrial applications due to their lightweight, flexibility, and cost-effectiveness. However, when it comes to fuel lines, the regulatory landscape is stringent, and adhering to industry standards is paramount.
Regulatory bodies and industry organizations have established guidelines and standards to ensure the safe operation of vehicles and equipment. These standards are in place to minimize the risks associated with fuel leaks, fires, and other potential hazards. For plastic fuel lines, specific requirements must be met to ensure their integrity and performance. One of the key aspects is the material's compatibility with the fuel being transported. Plastic fuel lines should be designed and manufactured using materials that are resistant to the chemicals present in different types of fuels, such as gasoline, diesel, or biofuels. This compatibility ensures that the plastic material does not degrade, become brittle, or release harmful substances over time.
Industry standards often specify the use of approved materials and manufacturing processes to guarantee the quality and reliability of plastic fuel lines. These standards may include guidelines for material selection, design considerations, and testing procedures. For instance, the Society of Automotive Engineers (SAE) and the American Society for Testing and Materials (ASTM) provide standards for fuel system components, including plastic lines. Compliance with these standards ensures that the fuel lines can withstand the operating conditions, temperature variations, and pressure differentials encountered in real-world applications.
Regulatory compliance also involves proper installation and maintenance practices. Fuel lines must be installed correctly, ensuring secure connections and minimizing the risk of leaks. Regular inspections and maintenance are essential to identify and replace any damaged or worn-out plastic fuel lines. Industry regulations often mandate specific inspection intervals and procedures to ensure the ongoing safety and reliability of the fuel system.
In summary, when considering the use of plastic air lines for fuel, it is crucial to understand and adhere to the regulatory compliance requirements. Plastic fuel lines must meet industry standards to ensure safe operation, compatibility with fuels, and reliable performance. By following these guidelines, manufacturers and users can minimize risks, maintain compliance, and ensure the longevity and safety of their fuel systems.
Understanding the 3 Gas Lines: Marine Fuel Pump Basics
You may want to see also
Frequently asked questions
Yes, plastic air lines, also known as fuel lines, can be used for fuel delivery in aircraft. These lines are typically made from materials like polyetheretherketone (PEEK) or polyimide, which offer excellent resistance to fuel contaminants and provide a reliable and safe fuel supply system.
Plastic fuel lines have several advantages over metal ones. They are lightweight, reducing the overall weight of the aircraft, and offer better flexibility, making installation and maintenance easier. Additionally, plastic lines are less susceptible to corrosion and can withstand higher temperatures, ensuring a longer lifespan and improved performance.
Absolutely! The plastic material used for fuel lines must meet strict industry standards and regulations. It should have superior chemical resistance to withstand various aviation fuels, including jet fuel and avgas. The material should also be able to operate within a wide temperature range, ensuring flexibility in cold climates and preventing brittleness in hot environments.
Plastic fuel lines are designed with materials that resist fuel absorption and minimize the risk of contamination. The smooth interior surface of these lines helps maintain fuel quality by preventing the leaching of plasticizers or other additives. This ensures that the fuel remains clean and free from potential impurities that could affect engine performance.