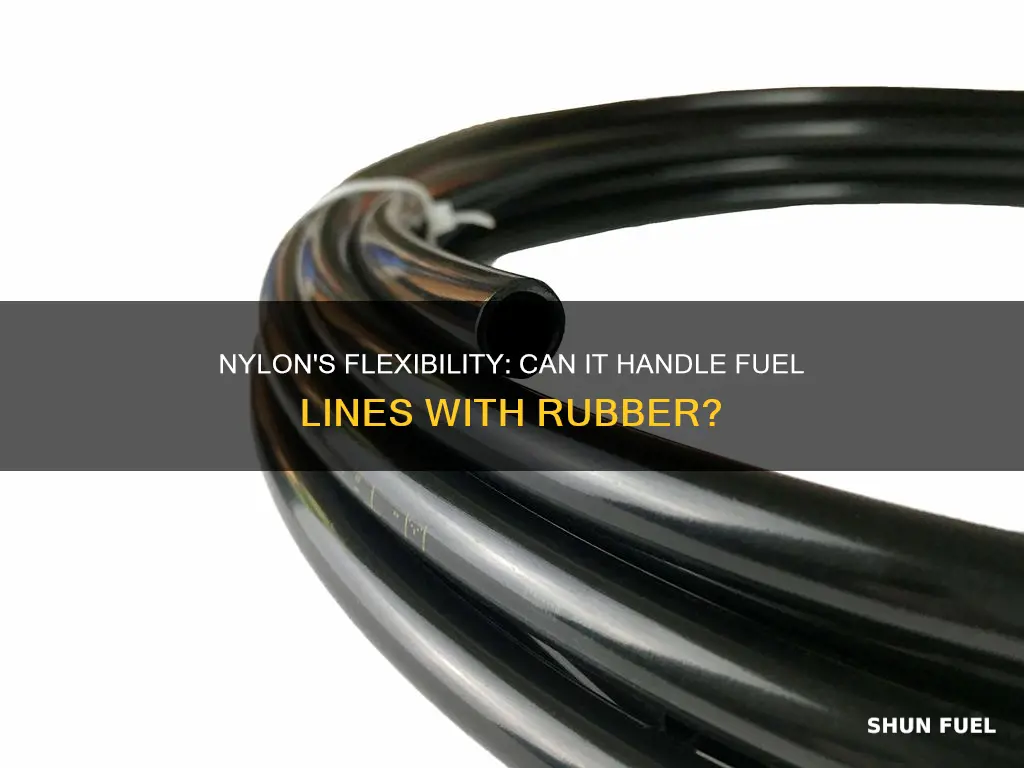
Nylon and rubber are commonly used materials in fuel lines, but their compatibility can vary depending on the specific types and conditions. Nylon, known for its strength and flexibility, is often preferred for its ability to withstand high temperatures and pressures. However, when paired with rubber, there are considerations to be made. Rubber can be susceptible to degradation when exposed to certain fuels, and the combination of nylon and rubber may not always provide the best solution for fuel line applications. Understanding the properties and compatibility of these materials is crucial to ensure the longevity and reliability of fuel lines in various automotive and industrial settings.
What You'll Learn
- Nylon's Strength: Nylon can withstand fuel line pressures and temperatures, offering durability
- Flexibility: Its flexibility allows nylon to bend and move with the fuel line, reducing stress
- Chemical Resistance: Nylon resists fuel degradation, ensuring long-term performance
- Durability: Nylon's robust structure prevents cracking and leaks in fuel lines
- Installation: Easy installation process for nylon fuel lines, compatible with rubber components
Nylon's Strength: Nylon can withstand fuel line pressures and temperatures, offering durability
Nylon is an excellent choice for fuel lines due to its exceptional strength and durability. When it comes to fuel lines, the material must be able to withstand the pressures and temperatures associated with fuel transport and delivery. Nylon, a synthetic polymer, possesses unique properties that make it highly suitable for this application.
One of the key advantages of nylon is its ability to handle high-pressure environments. Fuel lines often experience significant pressure, especially in high-performance vehicles or aircraft. Nylon's inherent strength and flexibility allow it to resist deformation and maintain its structural integrity under these demanding conditions. This ensures that the fuel lines remain intact and functional, preventing potential leaks or failures that could be hazardous.
Additionally, nylon's temperature resistance is another critical factor. Fuel lines are exposed to varying temperatures, from extreme cold during winter to high temperatures in engines. Nylon can withstand these temperature fluctuations without compromising its performance. It maintains its flexibility and structural stability, ensuring a reliable fuel supply even in the most challenging environments. This temperature resistance is particularly important in applications where fuel lines are exposed to rapid temperature changes, such as in racing or aviation.
The durability of nylon is further enhanced by its chemical resistance. Fuel lines often come into contact with various chemicals, including fuels, lubricants, and additives. Nylon's resistance to these chemicals prevents degradation and ensures long-term reliability. This property is crucial in maintaining the integrity of the fuel system and reducing the risk of fuel contamination or system failure.
In summary, nylon's strength, flexibility, temperature resistance, and chemical resistance make it an ideal material for fuel lines. Its ability to withstand high pressures and temperatures, coupled with its durability, ensures a reliable and safe fuel supply. When considering fuel line materials, nylon provides an excellent solution that meets the demanding requirements of various industries, including automotive, aviation, and racing.
Choosing the Right Fuel Line: Size Matters!
You may want to see also
Flexibility: Its flexibility allows nylon to bend and move with the fuel line, reducing stress
Nylon, a versatile synthetic polymer, offers a unique advantage when it comes to fuel line construction, particularly in its ability to provide flexibility. This characteristic is essential for ensuring the longevity and reliability of fuel lines in various applications, from automotive to industrial settings. The flexibility of nylon allows it to accommodate the natural movement and expansion of fuel lines, which is often an overlooked but critical aspect of their performance.
In the context of fuel lines, flexibility is key to preventing stress and potential damage. Fuel lines are subjected to various forces, including vibrations from the engine, temperature changes, and the pressure of the fuel itself. When a fuel line is rigid and inflexible, these forces can lead to cracks, leaks, or even complete failure. Nylon, with its inherent flexibility, acts as a buffer, absorbing and distributing these stresses evenly. This property is especially crucial in high-vibration environments, where the fuel line must constantly adjust to the engine's movements.
The flexibility of nylon is a result of its molecular structure, which allows the material to deform without breaking. This elasticity enables the fuel line to bend and twist without permanent deformation, ensuring that it can follow the path of the vehicle's movement. As the engine operates, the fuel line will naturally expand and contract, and the nylon's flexibility allows it to do so without putting excessive strain on the material. This is particularly important in high-temperature environments, where other materials might become brittle and fail.
Furthermore, the flexibility of nylon contributes to the overall durability of the fuel line. By reducing the stress on the material, it minimizes the risk of cracks and tears, which can lead to fuel leaks and potential safety hazards. This is especially relevant in older vehicles or those with modified engines, where the fuel line may need to navigate complex routes and experience more movement than standard designs. Nylon's flexibility ensures that the fuel line remains intact and functional over time.
In summary, the flexibility of nylon is a critical factor in its suitability for fuel lines. It allows the material to adapt to the dynamic nature of fuel line usage, reducing stress and potential failure points. This property is essential for maintaining the integrity of the fuel system, ensuring safe and efficient operation, and providing peace of mind to vehicle owners and operators. With its flexibility, nylon fuel lines offer a reliable solution for a wide range of applications.
Copper's Role in Diesel Fuel Lines: A Comprehensive Guide
You may want to see also
Chemical Resistance: Nylon resists fuel degradation, ensuring long-term performance
Nylon, a versatile synthetic polymer, has proven to be an excellent choice for fuel lines in various applications, especially when considering its chemical resistance properties. One of its key advantages is its ability to withstand the corrosive effects of fuels, ensuring long-term performance and reliability. This is particularly crucial in the automotive and aviation industries, where fuel lines are exposed to a variety of chemicals and substances.
The chemical resistance of nylon is attributed to its molecular structure. Nylon's amide groups are resistant to hydrolysis, which means it can resist the breakdown of its chemical bonds when exposed to fuels. This property is essential as it prevents the degradation of the material, ensuring that the fuel lines maintain their structural integrity over time. Unlike some other materials, nylon does not readily absorb or dissolve in fuels, making it highly suitable for fuel containment.
In the context of fuel lines, chemical resistance is vital to prevent fuel leakage and contamination. When a fuel line is exposed to various chemicals present in different fuels, it can lead to deterioration and potential failure. Nylon's resistance to fuel degradation means it can handle the harsh conditions without compromising its performance. This is especially important in high-temperature environments, where some fuels can accelerate the breakdown of materials, making nylon an ideal choice.
Furthermore, nylon's chemical resistance contributes to its durability and longevity. It can withstand the constant friction and movement associated with fuel lines, reducing the risk of wear and tear. This durability ensures that the fuel lines remain effective and safe over extended periods, even in challenging operating conditions. As a result, nylon fuel lines are often preferred in applications where reliability and long-term performance are critical.
In summary, nylon's chemical resistance is a significant factor in its suitability for fuel lines. Its ability to resist fuel degradation ensures that the material maintains its structural integrity, providing long-lasting performance. This property, combined with nylon's durability, makes it an excellent choice for fuel containment, offering a reliable solution for various industries. Understanding and utilizing these characteristics can lead to improved safety and efficiency in fuel-related applications.
Volvo VNL Fuel Line Sizing: Expert Guide
You may want to see also
Durability: Nylon's robust structure prevents cracking and leaks in fuel lines
Nylon's exceptional durability makes it an ideal material for fuel lines, offering a robust solution to prevent the common issues associated with fuel line wear and tear. Its inherent strength and flexibility are key to ensuring a long-lasting and reliable fuel delivery system. The material's ability to withstand the rigors of fuel transportation and distribution is a significant advantage.
The structure of nylon is designed to be highly resistant to cracking, a common problem with other materials used in fuel lines. Cracks can lead to fuel leaks, which are not only costly but also environmentally detrimental. Nylon's molecular structure is such that it can absorb and distribute the stress and pressure associated with fuel flow, preventing any micro-tears or fractures that could compromise the integrity of the fuel line. This is particularly important in high-pressure fuel systems, where the material must be able to handle the force without failing.
In addition to its strength, nylon's flexibility is another crucial factor in its suitability for fuel lines. It can easily bend and conform to the various shapes and angles of the fuel system, ensuring a secure and snug fit. This flexibility also allows for easy installation and replacement, making it a practical choice for both new fuel line installations and repairs. The material's adaptability ensures that it can accommodate the natural expansion and contraction of the fuel line, further reducing the risk of damage and leaks.
Furthermore, nylon's resistance to chemicals is a significant benefit. Fuel lines are often exposed to various chemicals, including those in gasoline and diesel, which can degrade other materials over time. Nylon, however, remains stable and resistant to these chemicals, ensuring that the fuel line's performance and longevity are not compromised. This chemical resistance also contributes to the overall safety of the fuel system, reducing the risk of fuel contamination and potential engine damage.
In summary, nylon's durability is a critical factor in its ability to handle fuel lines effectively. Its robust structure, combined with flexibility and chemical resistance, ensures that fuel lines remain intact and functional over extended periods. This makes nylon an excellent choice for fuel line applications, providing a reliable and long-lasting solution for the transportation and distribution of fuels.
Choosing the Right Fuel Line: A Comprehensive Guide
You may want to see also
Installation: Easy installation process for nylon fuel lines, compatible with rubber components
Nylon fuel lines are a popular choice for vehicle owners seeking an upgrade to their fuel delivery systems, especially when paired with rubber components. The compatibility of nylon with rubber is a key advantage, as it ensures a reliable and efficient fuel supply. When installing these nylon fuel lines, the process is straightforward and can be completed with some basic tools and a methodical approach.
The first step is to gather the necessary tools and materials. You will need a pair of fuel line connectors, which are typically made of nylon or a compatible material, and a set of rubber O-rings or seals. These components are designed to create a secure and leak-free connection between the nylon fuel lines and the surrounding rubber parts. Additionally, have a fuel line cutter, a hose clamp, and a cleaning agent ready for the installation.
Start by cutting the nylon fuel line to the desired length, ensuring it is slightly longer than the required length to allow for any adjustments. Clean the ends of the fuel line and the corresponding rubber components with the cleaning agent to remove any dirt or debris. This step is crucial to ensure a proper seal. Then, insert the nylon fuel line into the connector, pushing it until it is fully seated. The connector should have a secure locking mechanism to hold the line in place.
Next, place the rubber O-ring or seal over the fuel line, ensuring it covers the entire diameter of the line. This rubber component creates a flexible and durable seal. Slide the hose clamp onto the fuel line and tighten it securely, but be careful not to overtighten, as it may damage the rubber. The clamp should hold the fuel line in place while also providing a tight seal against the connector.
Finally, test the installation by checking for any leaks. Run the fuel line under pressure or use a soapy water solution to identify any potential leaks around the connections. If no leaks are found, your nylon fuel line installation is complete. This process ensures a reliable fuel supply while also providing the flexibility and durability that rubber components offer. Remember, proper cleaning and the use of compatible materials are essential for a successful and long-lasting installation.
The Mysterious Motive: Eugene's Fuel Line Fiasco
You may want to see also
Frequently asked questions
Yes, nylon can be a suitable material for fuel lines in vehicles, especially when combined with rubber components. Nylon is known for its strength, flexibility, and resistance to wear and tear, making it a popular choice for fuel lines. When used in conjunction with rubber, it can provide a durable and reliable solution.
Nylon fuel lines with rubber components offer several benefits. The rubber parts can provide flexibility and cushioning, allowing for slight movements and vibrations without compromising the integrity of the fuel line. Nylon's strength ensures it can withstand the pressure and temperature variations associated with fuel, making it a long-lasting and reliable option.
When installing nylon fuel lines with rubber, it's important to ensure proper alignment and secure connections. Rubber components should be protected from excessive heat and sharp edges during installation to prevent damage. Regular inspections and maintenance are recommended to identify any signs of wear or damage, ensuring the fuel system's overall safety and performance.