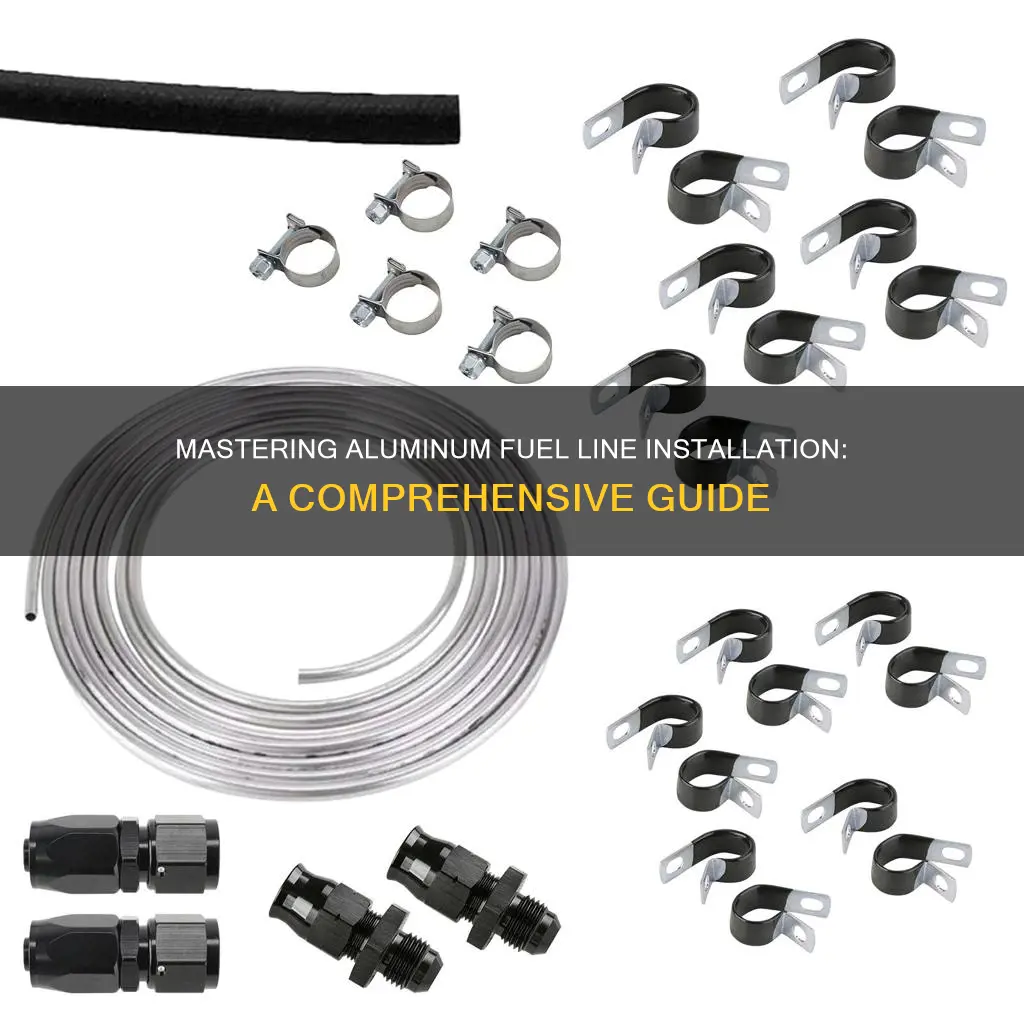
Installing an aluminum fuel line is a crucial step in ensuring the safety and efficiency of your vehicle's fuel system. This process involves replacing the traditional rubber or plastic fuel lines with a lightweight, durable aluminum alternative, which can improve performance and reduce the risk of leaks. The installation process requires careful planning and execution to ensure a secure and reliable connection. This guide will provide a step-by-step overview of the installation process, including the necessary tools, safety precautions, and tips for a successful and long-lasting fuel line upgrade.
What You'll Learn
- Prepare Tools: Gather necessary tools like wrenches, pipe cutters, and fuel line connectors
- Inspect Vehicle: Ensure compatibility and check for any existing damage or leaks
- Cut and Prepare: Measure and cut the aluminum fuel line to the desired length
- Connect Fittings: Attach fittings securely, ensuring a tight and leak-free seal
- Test and Inspect: Verify the installation by checking for leaks and proper functionality
Prepare Tools: Gather necessary tools like wrenches, pipe cutters, and fuel line connectors
Before you begin the installation process, it's crucial to have the right tools at hand to ensure a smooth and efficient job. Here's a detailed guide on preparing the necessary tools for installing an aluminum fuel line:
Wrenches: Invest in a set of wrenches with various sizes and types. You'll need both adjustable and fixed-size wrenches to accommodate different fuel line fittings. Wrenches are essential for tightening and loosening connections, ensuring a secure and tight fit. Look for a set that includes metric and imperial sizes to cover a wide range of fuel line standards.
Pipe Cutters: Accurate and sharp pipe cutters are indispensable for cutting aluminum fuel lines to the desired length. When purchasing, opt for a high-quality model with a sturdy cutting wheel. This tool will allow you to make clean and precise cuts, ensuring a professional finish. It's important to have a reliable pipe cutter to avoid any potential leaks or damage during the installation.
Fuel Line Connectors: Gather a variety of fuel line connectors suitable for aluminum lines. These connectors come in different types, such as compression fittings, quick-connect couplings, or crimp-on fittings. Ensure you have the appropriate connectors for your specific fuel line application. Each type may require different tools for installation, so having a selection will allow you to choose the right one for the job.
Additionally, consider having some pipe dope or tape, which can be used for sealing connections, and a source of fuel to test the system once installed. Having these tools and connectors ready will streamline the installation process and help you complete the task efficiently. Remember, having the right tools makes all the difference in ensuring a successful and leak-free fuel line installation.
Lawn Mower Fuel Line Fix: A Step-by-Step Guide
You may want to see also
Inspect Vehicle: Ensure compatibility and check for any existing damage or leaks
Before you begin the installation of an aluminum fuel line, it's crucial to inspect your vehicle to ensure compatibility and identify any potential issues. This step is essential to guarantee a successful and safe installation process. Here's a detailed guide on how to inspect your vehicle for this specific task:
- Compatibility Check: Begin by confirming that the aluminum fuel line you intend to install is compatible with your vehicle's fuel system. Different vehicles may have unique fuel line requirements, and using the wrong size or type can lead to installation difficulties and potential safety hazards. Check the manufacturer's specifications or consult the vehicle's service manual to ensure the fuel line's dimensions, fittings, and materials match your car's system.
- Visual Inspection: Inspect the vehicle's fuel system for any visible signs of damage or wear. Look for existing fuel lines that may be cracked, corroded, or damaged. Check for any leaks or drips around the fuel tank, fuel pump, and existing fuel lines. These areas are critical, as leaks can lead to dangerous situations, including fire hazards. Inspect the engine bay and under the vehicle for any signs of fuel contamination or damage to the fuel system.
- Check for Leaks: Leaks can occur at various points in the fuel system, including the fuel tank, fuel pump, and connections. Inspect all connections and fittings for any signs of leakage. Use a soapy water solution to create a foam and apply it to the connections to identify any areas where fuel is escaping. Even small leaks can be a safety concern and may require immediate attention.
- Inspect for Existing Damage: Examine the vehicle's interior and exterior for any existing damage that could affect the fuel line installation. Look for any holes, tears, or damage to the fuel tank or surrounding areas that could compromise the integrity of the fuel system. Ensure that there are no obstacles or potential interference points that might cause issues during the installation process.
- Document and Repair: If any issues are identified during the inspection, document them and address them before proceeding with the installation. This may involve repairing or replacing damaged components, ensuring that the fuel system is in optimal condition. Properly addressing any existing problems will make the installation process smoother and safer.
By thoroughly inspecting your vehicle and ensuring compatibility, you can proceed with the installation of the aluminum fuel line with confidence, knowing that you've taken the necessary precautions to maintain a safe and efficient fuel system.
E85 Fuel Line Maintenance: What to Flush and Why
You may want to see also
Cut and Prepare: Measure and cut the aluminum fuel line to the desired length
When preparing to install an aluminum fuel line, accurate measurements and precise cutting are crucial steps to ensure a proper fit and functionality. Here's a detailed guide on how to measure and cut the aluminum fuel line to your desired length:
Measuring the Required Length: Begin by carefully examining the vehicle's fuel system layout and identifying the specific section where the new aluminum fuel line will be installed. Measure the distance between the fuel source (such as the fuel pump or tank) and the destination (e.g., the engine or fuel injectors). Take into account any bends or turns the line might need to make along the way. It's essential to get an accurate measurement to ensure the line is long enough to connect the two points without excessive slack or tight bends that could compromise performance.
Using the Right Tools: You'll need a sharp utility knife or a pair of tin snips for cutting aluminum. Ensure the cutting tool is sharp to make clean, precise cuts. If you're using a knife, hold the line firmly and carefully cut along the measured length, ensuring you don't cut too deep and risk damaging the surrounding components. For tin snips, place the line on a flat surface, align the cutting edge with your measured mark, and apply firm pressure to make a clean cut.
Safety Precautions: When cutting, work in a well-ventilated area and wear appropriate safety gear, including gloves and eye protection, to avoid any potential injuries from sharp edges. It's also a good practice to mark the cut line with a pencil or a piece of tape to ensure you cut to the correct length.
Cutting Technique: Make a single, clean cut along the measured length. For a more professional finish, you can use a file to smooth any sharp edges, especially if you're using a knife. Ensure the cut ends are straight and even to facilitate a proper connection later.
Final Check: After cutting, double-check the length to ensure it meets your requirements. If it's too short, you can carefully trim a little more; if it's too long, you might need to consider other options or adjust the installation points.
Fuel Vent Line Disconnect: A Step-by-Step Guide for 2008 Chevy Owners
You may want to see also
Connect Fittings: Attach fittings securely, ensuring a tight and leak-free seal
When it comes to installing an aluminum fuel line, one of the most critical steps is connecting the fittings securely to ensure a tight and leak-free seal. This process requires attention to detail and the right tools to achieve a professional finish. Here's a step-by-step guide to help you master this task:
Prepare the Fittings and Hose: Before you begin, ensure that all the fittings and the aluminum fuel line are clean and free from any debris or contaminants. Use a hose or a high-pressure water jet to rinse the fittings and the hose, removing any dirt or old sealant. This step is crucial to ensure a proper bond between the fittings and the fuel line.
Apply Sealant: Fittings require a reliable sealant to create an airtight connection. Choose a high-quality silicone or epoxy sealant suitable for fuel lines. Apply a thin, even layer of sealant to the interior of the fittings, ensuring full coverage. Take care not to overapply, as excess sealant can lead to leaks. Allow the sealant to cure according to the manufacturer's instructions, which is typically a few hours.
Attach the Fittings: Now, it's time to connect the fittings to the fuel line. Start by inserting the male end of the fitting into the female port of the fuel line. Ensure that the fitting is aligned correctly and that the threads are properly engaged. Use a wrench to tighten the fitting securely, but be careful not to overtighten, as this can damage the fuel line. The goal is to achieve a firm, yet gentle, connection.
Check for Leaks: After attaching the fittings, it's essential to inspect the connections for any signs of leaks. Turn on the fuel line and check for any drips or seepage around the fittings. If you notice any leaks, tighten the fittings further or reapply sealant. Ensure that all connections are secure and leak-free before proceeding.
Secure the Assembly: To prevent any movement or vibration-induced leaks, secure the entire assembly. Use appropriate clamps or ties to fasten the fuel line and fittings to the vehicle's frame or any nearby structural components. This step provides additional support and ensures that the fuel line remains in place during operation.
By following these steps, you can ensure that the fittings are securely attached, creating a reliable and leak-free aluminum fuel line installation. Remember, taking the time to prepare, apply the right sealants, and double-check for leaks will result in a professional-grade fuel system.
Saito 180 Fuel Line: Size Guide for Optimal Performance
You may want to see also
Test and Inspect: Verify the installation by checking for leaks and proper functionality
After completing the installation of the aluminum fuel line, it is crucial to thoroughly test and inspect the system to ensure its reliability and safety. This step is often overlooked, but it is an essential part of the process to guarantee that the fuel line is secure and functioning correctly. Here's a detailed guide on how to verify the installation:
Leak Testing: Begin by applying a small amount of diesel fuel or a suitable sealant along the entire length of the aluminum fuel line. This step is critical as it simulates a real-world scenario where fuel pressure might cause leaks. Use a soapy water solution as a leak detector. If there are any leaks, the soap solution will form bubbles, indicating the presence of a potential issue. Inspect the entire length of the line, paying close attention to any connections, bends, or fittings. Even a small crack or improper sealing can lead to significant problems, so ensure that all components are tightly secured and properly sealed.
Pressure Testing: To further ensure the integrity of the fuel line, perform a pressure test. This can be done using a fuel pressure gauge and a small hand pump or a dedicated fuel pressure testing kit. Attach the gauge to the fuel line and pump up the pressure to a level recommended by the manufacturer or a safe, controlled level. Check for any drops in pressure, which could indicate a leak or an issue with the fuel pump or regulator. This test is especially important if the fuel line is running under high pressure, as it helps identify potential weaknesses.
Functionality Check: Once the system has been leak-tested and pressure-tested, it's time to ensure it functions as intended. Start the vehicle's engine and monitor the fuel gauge. Check for any unusual behavior, such as rapid fuel level drops or erratic readings. Listen for any unusual noises coming from the fuel line, as this could indicate a problem with the installation. Additionally, check for proper fuel flow by using a fuel flow meter to measure the rate of fuel delivery. This step helps identify any blockages or restrictions in the line.
Visual Inspection: While testing, also perform a visual inspection of the entire fuel line system. Look for any signs of damage, corrosion, or deformation. Check for proper alignment and ensure that all components are securely attached. Pay attention to any areas where the line might be susceptible to damage, such as under the vehicle or near moving parts. Any visible damage should be addressed immediately, as it could lead to fuel leaks or system failure.
By following these testing and inspection procedures, you can ensure that the aluminum fuel line installation is secure, leak-free, and functioning optimally. This step is vital for the overall safety and performance of the vehicle's fuel system. It is always better to identify and rectify issues during the installation process rather than dealing with them after the vehicle is on the road.
Understanding Fuel Line Capacity: Gallons and More
You may want to see also
Frequently asked questions
Aluminum fuel lines are often preferred for fuel delivery systems due to their lightweight, flexibility, and resistance to corrosion. They are commonly used in high-performance vehicles, marine applications, and racing cars where weight reduction and durability are essential.
While it is possible for experienced DIY enthusiasts to install aluminum fuel lines, it is generally recommended to have a professional mechanic handle the installation. The process requires precision and knowledge of fuel system components to ensure a safe and proper fit.
Before installation, ensure all fuel lines are clean and free of debris. Inspect the lines for any damage or bends that might affect their performance. It is also advisable to lubricate the lines to facilitate a smooth installation process.
You will require basic automotive tools such as wrenches, pliers, and a fuel line cutter/stripper. Additionally, have a fuel line primer, fuel-resistant tape, and a fuel line connector kit ready for the installation. Ensure you have the appropriate safety gear, including gloves and eye protection.
Yes, safety is crucial. Always work in a well-ventilated area to avoid inhaling fuel vapors. Wear protective clothing to prevent skin contact with fuel. Be cautious when handling sharp tools, and ensure you are familiar with the fuel system's location and components to avoid any accidents or damage.