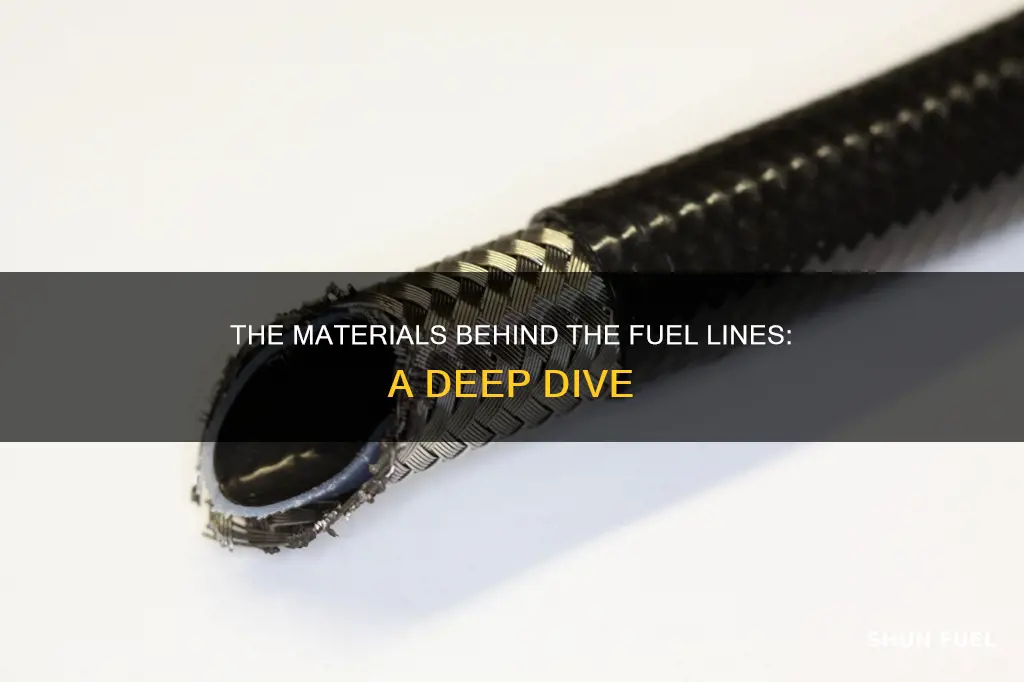
Fuel lines are an essential component of any vehicle's fuel system, responsible for transporting fuel from the tank to the engine. These lines are typically made from a variety of materials, each chosen for its specific properties and ability to withstand the demands of the fuel system. Common materials include rubber, which is known for its flexibility and resistance to fuel degradation, and steel, which offers strength and durability. Other materials, such as plastic and aluminum, may also be used depending on the application and the specific requirements of the vehicle's fuel system. Understanding the composition of fuel lines is crucial for ensuring proper maintenance and longevity of the vehicle's fuel system.
Characteristics | Values |
---|---|
Material | Typically made of steel, aluminum, or brass |
Flexibility | Flexible to accommodate engine movement |
Strength | Able to withstand high pressure and temperature |
Corrosion Resistance | Resistant to corrosion from fuel and engine components |
Durability | Long-lasting and resistant to wear and tear |
Compatibility | Compatible with different types of fuel and engine systems |
Temperature Range | Operates effectively in a wide range of temperatures |
Pressure Rating | Designed to handle the pressure of the fuel system |
Connectors | Often includes specialized connectors for secure attachment |
Color | Usually black or blue to distinguish from other engine components |
What You'll Learn
- Metal Alloys: Common materials include steel, aluminum, and copper alloys for durability and heat resistance
- Rubber and Plastic: Flexible materials like rubber and plastic are used for their flexibility and resistance to corrosion
- Braided Hose: Braided hoses offer strength and flexibility, often made from synthetic fibers
- Reinforced Materials: Some fuel lines use reinforced materials like nylon or polyester for added strength
- Composite Materials: Advanced composites provide lightweight, durable alternatives for high-performance applications
Metal Alloys: Common materials include steel, aluminum, and copper alloys for durability and heat resistance
Fuel lines are an essential component of any vehicle's fuel system, responsible for transporting fuel from the tank to the engine. The choice of material for these lines is crucial, as it directly impacts the performance, safety, and longevity of the vehicle. Traditionally, fuel lines were made from various materials, each offering unique advantages and disadvantages.
One of the most common materials used for fuel lines is steel. Steel is known for its exceptional strength and durability, making it an ideal choice for applications that require withstanding high pressure and temperature. It is often used in heavy-duty vehicles, such as trucks and construction equipment, where the fuel system needs to handle large volumes of fuel and potential vibrations during operation. However, steel fuel lines can be heavy and rigid, which might not be ideal for certain vehicle designs.
Aluminum is another popular choice for fuel lines, especially in the automotive industry. This metal is lightweight, offering a significant advantage in terms of reducing the overall weight of the vehicle. Aluminum fuel lines are also known for their excellent heat resistance, which is crucial in engines where fuel temperatures can vary significantly. The lightweight nature of aluminum also contributes to better fuel efficiency, making it an attractive option for modern vehicles. Additionally, aluminum's natural corrosion resistance further enhances its suitability for fuel lines.
Copper alloys are less common but still valuable in specific applications. Copper provides excellent heat conductivity, which can be beneficial in certain engine designs. However, copper is more expensive and less durable than steel or aluminum, making it less common for general-purpose fuel lines. Copper alloys are often used in high-performance vehicles or in specialized applications where heat dissipation is critical.
In recent years, advancements in materials science have led to the development of new alloys and composite materials for fuel lines. These innovative materials aim to combine the best properties of traditional metals with improved flexibility, weight reduction, and corrosion resistance. For instance, some manufacturers are now using high-strength, lightweight alloys that offer superior durability without compromising on fuel efficiency.
When selecting the material for fuel lines, engineers and designers must consider various factors, including the vehicle's intended use, engine requirements, and environmental conditions. Each material has its advantages and trade-offs, and the choice ultimately depends on finding the right balance between strength, weight, heat resistance, and cost. Modern vehicles often utilize a combination of these materials to optimize the fuel system's performance and ensure a reliable and efficient power delivery.
Unveiling the Material Secrets of Car Fuel Lines
You may want to see also
Rubber and Plastic: Flexible materials like rubber and plastic are used for their flexibility and resistance to corrosion
The choice of material for fuel lines is crucial in ensuring the efficient and safe operation of a vehicle's fuel system. Among the various materials used, rubber and plastic stand out for their unique properties, making them ideal for this application. These materials offer a combination of flexibility and resistance to corrosion, which are essential characteristics for fuel lines.
Rubber, a natural or synthetic polymer, is renowned for its flexibility. It can easily bend and conform to the vehicle's contours, making installation and maintenance more accessible. This flexibility is particularly important in fuel lines as it allows for movement and adjustment without compromising the structural integrity of the fuel system. Additionally, rubber has excellent resistance to corrosion, which is vital for fuel lines. It can withstand the corrosive effects of fuel, preventing degradation and ensuring the longevity of the fuel system. This resistance is further enhanced by the ability of rubber to form a protective layer around the fuel, reducing the risk of leaks and contamination.
Plastic, another versatile material, is also commonly used in fuel lines. It offers similar advantages to rubber, including flexibility and corrosion resistance. Plastic fuel lines are lightweight, making them easier to install and manage. The flexibility of plastic allows it to accommodate the natural movement of the vehicle's components, ensuring a secure and reliable connection. Moreover, plastic's resistance to corrosion is particularly useful in fuel lines, as it can protect against the harmful effects of fuel, such as oxidation and degradation.
The use of rubber and plastic in fuel lines is a practical choice, considering the demanding environment in which these lines operate. The flexibility of these materials enables them to navigate the intricate network of pipes and hoses within a vehicle without becoming brittle or fragile. This flexibility is crucial for maintaining a secure and reliable fuel supply, especially during the vehicle's operation, where vibrations and movements are common.
In summary, rubber and plastic are the preferred materials for fuel lines due to their inherent flexibility and corrosion resistance. These properties ensure that fuel lines can withstand the rigors of the vehicle's environment, providing a reliable and efficient fuel supply. The choice of these materials is a testament to the importance of material science in automotive engineering, where functionality and durability are paramount.
Unleash the Power: Breaking Fuel Lines: A Quarry Decision
You may want to see also
Braided Hose: Braided hoses offer strength and flexibility, often made from synthetic fibers
Braided hoses are an excellent choice for fuel lines due to their unique properties and performance advantages. These hoses are constructed with a braided design, which sets them apart from traditional rubber hoses. The key feature of braided hoses lies in their composition; they are typically made from synthetic fibers, such as polyester or nylon. This material choice provides several benefits that make braided hoses ideal for fuel line applications.
One of the primary advantages of braided hoses is their exceptional strength. The synthetic fibers used in their construction offer a high level of tensile strength, ensuring that the hose can withstand the pressure and forces encountered in fuel systems. This strength is crucial for maintaining the integrity of the fuel lines, especially in high-performance vehicles or those with demanding operating conditions. The braided design also provides flexibility, allowing the hose to navigate through tight spaces and bends without compromising its structural integrity.
The flexibility of braided hoses is particularly beneficial for fuel lines, as it enables easy installation and routing. These hoses can conform to the vehicle's layout, making them suitable for various engine configurations. Additionally, the flexibility reduces the risk of damage during installation or removal, ensuring a longer lifespan for the fuel lines.
Another advantage of braided hoses is their resistance to fuel-related chemicals. Synthetic fibers are often treated to enhance their chemical resistance, ensuring that the hose can withstand the corrosive effects of different fuel types. This property is essential for maintaining the performance and longevity of the fuel system, especially in vehicles with specialized or high-octane fuels.
In summary, braided hoses, made from synthetic fibers, offer a superior solution for fuel lines. Their strength, flexibility, and chemical resistance make them an ideal choice for ensuring efficient and reliable fuel delivery in various automotive applications. When considering fuel line materials, braided hoses provide a robust and adaptable option that meets the demands of modern vehicles.
Unveiling the 1967 Ford LTD's Fuel Line Route
You may want to see also
Reinforced Materials: Some fuel lines use reinforced materials like nylon or polyester for added strength
Reinforced materials play a crucial role in the construction of fuel lines, ensuring they can withstand the demanding conditions of fuel transport. One common choice for reinforcement is nylon, a synthetic polymer known for its exceptional strength and durability. Nylon fuel lines are often preferred due to their ability to resist wear and tear, making them ideal for high-pressure applications. The material's inherent flexibility allows it to conform to the vehicle's contours, ensuring a secure and reliable fit. Additionally, nylon's resistance to chemicals and temperature variations makes it a versatile option for various fuel types and environmental conditions.
Polyester, another reinforced material, is also utilized in fuel line manufacturing. This material offers excellent tensile strength and flexibility, making it highly suitable for fuel lines. Polyester's ability to maintain its structural integrity under pressure and temperature changes is particularly advantageous. It is often used in combination with other materials to create a composite fuel line, providing a lightweight yet robust solution. The use of polyester in fuel lines ensures a long-lasting and reliable connection between the fuel tank and engine, minimizing the risk of leaks or failures.
The reinforcement of fuel lines with these materials is a strategic approach to enhance their performance and longevity. By incorporating nylon or polyester, manufacturers can create fuel lines that are more resistant to abrasion, impact, and the corrosive effects of fuel. This reinforcement is especially critical in high-performance vehicles or those operating in harsh environments, where fuel lines are subjected to increased stress and potential damage.
Furthermore, the use of reinforced materials contributes to the overall safety of the vehicle. Strong and durable fuel lines reduce the chances of fuel leaks, which can lead to hazardous situations. The reinforced construction ensures that the fuel lines can handle the pressure and temperature fluctuations associated with engine operation, preventing potential failures that could result in fuel spills or engine damage.
In summary, reinforced materials like nylon and polyester are essential components in the design of fuel lines, providing the necessary strength and flexibility to withstand the rigors of fuel transportation. These materials offer a reliable solution for maintaining a secure and efficient connection between the fuel source and the engine, ensuring optimal performance and safety in various vehicle applications.
Understanding Fuel Lines: The Vital Link in Your Engine's Fuel Supply
You may want to see also
Composite Materials: Advanced composites provide lightweight, durable alternatives for high-performance applications
Composite materials have revolutionized the automotive and aerospace industries by offering exceptional properties that traditional materials struggle to match. When it comes to fuel lines, these advanced composites have emerged as a game-changer, providing a lightweight yet robust solution for high-performance applications.
The primary challenge with fuel lines is ensuring they can withstand the demanding conditions of high-performance engines while maintaining flexibility and durability. Composite materials, such as carbon fiber-reinforced polymers, offer a unique combination of strength and lightness. These materials are engineered to provide an exceptional strength-to-weight ratio, making them ideal for fuel lines that need to transmit fuel efficiently without adding excessive weight to the vehicle. By utilizing carbon fiber composites, engineers can create fuel lines that are not only lightweight but also highly resistant to fatigue and corrosion, ensuring a longer lifespan and improved performance.
One of the key advantages of composite fuel lines is their ability to provide structural integrity while maintaining flexibility. Composite materials can be designed with specific orientations and reinforcements to create a material that is both stiff and malleable. This flexibility is crucial for fuel lines, as it allows them to navigate through tight spaces and complex engine architectures without compromising on strength. The composite material's ability to absorb and distribute stress evenly ensures that the fuel lines remain intact even under extreme conditions, such as rapid acceleration or high-speed maneuvers.
Furthermore, the use of advanced composites in fuel lines enables manufacturers to achieve superior performance and efficiency. Composite materials can be tailored to have low thermal expansion coefficients, ensuring that the fuel lines maintain their shape and functionality even when exposed to extreme temperatures. This property is particularly important in high-performance engines where temperature fluctuations can be significant. By combining lightweight construction with thermal stability, composite fuel lines contribute to improved fuel efficiency and reduced weight, ultimately enhancing the overall performance of the vehicle.
In summary, composite materials offer a compelling solution for fuel line applications in high-performance vehicles. Their lightweight nature, combined with exceptional strength and flexibility, makes them an ideal choice for engineers seeking to optimize vehicle performance and efficiency. As technology advances, we can expect to see even more innovative uses of composite materials in the automotive and aerospace sectors, further pushing the boundaries of what is possible in terms of fuel line design and functionality.
Pipe Thread Sealant: Essential for Fuel Line Maintenance?
You may want to see also
Frequently asked questions
Fuel lines are typically made from materials like steel, aluminum, or high-density polyethylene (HDPE) plastic. These materials are chosen for their durability and ability to withstand the pressure and temperature variations associated with fuel systems.
Fuel lines play a critical role in delivering fuel from the tank to the engine. They are designed to ensure a consistent and precise fuel supply, allowing for efficient combustion and optimal engine performance. The material used directly impacts the line's flexibility, strength, and resistance to corrosion, which are essential factors in maintaining a reliable fuel system.
The choice of material depends on the specific requirements of the vehicle's fuel system. Steel fuel lines are known for their strength and ability to withstand high pressure, making them suitable for high-performance engines. Aluminum lines are lightweight and offer good heat resistance, while HDPE plastic is flexible, lightweight, and resistant to corrosion, making it ideal for modern fuel systems.
Yes, fuel lines can be constructed from a single material or a combination of materials to enhance their performance and durability. For instance, a steel core with an outer layer of HDPE plastic can provide the strength of steel while offering flexibility and corrosion resistance. This composite approach ensures the fuel lines can handle various operating conditions effectively.