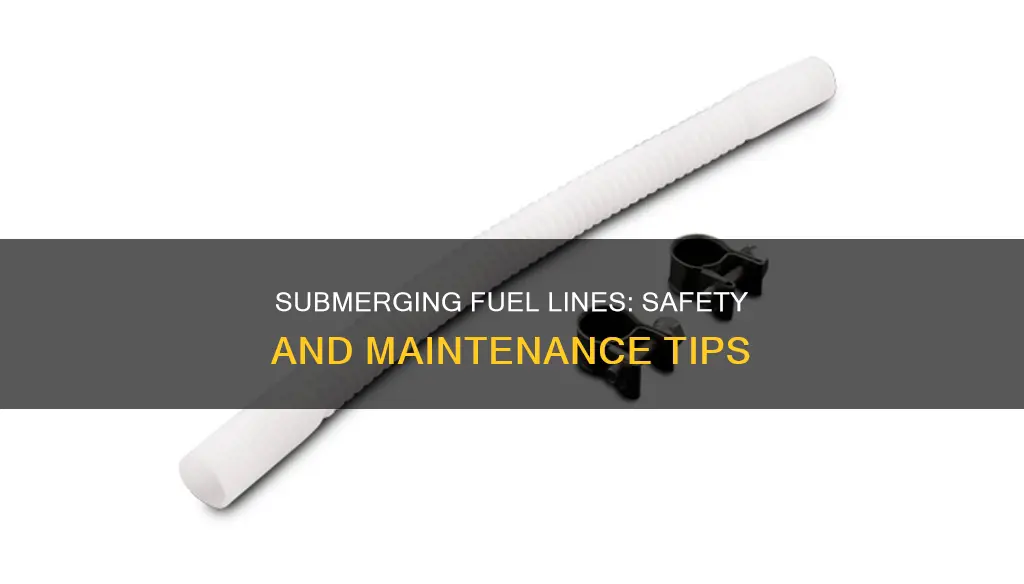
When it comes to vehicle maintenance, understanding the proper handling of fuel components is crucial. One common question that arises is whether the fuel line can be submerged in fuel. This inquiry delves into the compatibility and safety considerations of placing a fuel line directly in the fuel reservoir. By exploring this topic, we can ensure that vehicle owners and mechanics make informed decisions to maintain optimal performance and prevent potential issues.
Characteristics | Values |
---|---|
Submersion in Fuel | Generally not recommended. Fuel lines are designed to withstand specific conditions, but submerging them in fuel can lead to potential issues. |
Material Compatibility | Fuel lines are typically made of materials like rubber, plastic, or metal, which may not be suitable for long-term contact with fuel. |
Corrosion and Degradation | Submerging a fuel line in fuel can cause corrosion and degradation of the material, leading to leaks or failure over time. |
Pressure and Temperature | Fuel lines are designed to handle specific pressure and temperature ranges. Submerging them in fuel may exceed these limits, causing damage. |
Safety and Maintenance | Submerging fuel lines in fuel can be a safety hazard and may require additional maintenance to ensure proper functioning. |
Manufacturer's Guidelines | Always refer to the manufacturer's guidelines and recommendations for fuel line installation and maintenance. |
What You'll Learn
- Fuel Line Material Compatibility: Different materials react differently when submerged in fuel
- Fuel Line Diameter and Submersion Depth: Thicker lines can handle deeper submersion
- Fuel Line Length and Submersion: Longer lines may require additional support
- Fuel Line Flexibility and Submersion: Flexible lines can adapt to submersion without damage
- Fuel Line Insulation and Submersion: Insulated lines can withstand fuel submersion without degradation
Fuel Line Material Compatibility: Different materials react differently when submerged in fuel
The compatibility of fuel lines with the fuel they carry is a critical aspect of vehicle maintenance, especially for those with high-performance engines or those operating in extreme conditions. When it comes to the question of whether a fuel line can be submerged in fuel, the answer is not a simple yes or no. It depends on the material of the fuel line and the type of fuel being used. Different materials have varying levels of compatibility with different fuels, and understanding these differences is essential to ensure the longevity and reliability of your vehicle's fuel system.
One of the most common materials used for fuel lines is rubber, which is known for its flexibility and durability. Rubber fuel lines are often used in standard vehicles and can withstand the corrosive effects of most conventional fuels. However, it's important to note that rubber can degrade over time, especially when exposed to certain types of fuel, such as ethanol-blended fuels, which are becoming more common in some regions. When submerged in fuel, rubber fuel lines may experience swelling or softening, leading to potential leaks or reduced performance over time.
Another popular material for fuel lines is vinyl, which is lightweight and offers good resistance to fuel degradation. Vinyl lines are commonly used in high-performance vehicles and racing applications. While vinyl is generally compatible with a wide range of fuels, it is more susceptible to damage from certain chemicals present in fuel, such as antioxidants and stabilizers. Prolonged submersion in fuel can cause vinyl to become brittle and crack, leading to fuel leaks and potential engine issues.
Braided steel fuel lines are often used in high-temperature and high-pressure environments, such as racing or off-road applications. These lines are known for their strength and resistance to heat and pressure. When submerged in fuel, braided steel lines can withstand the corrosive effects of most fuels without significant degradation. However, it's important to choose the right type of braided steel for the specific fuel being used, as some types of steel may react differently with certain fuels.
In contrast, plastic fuel lines, such as those made from polyvinyl chloride (PVC) or polypropylene, are generally not recommended for submersion in fuel. Plastic lines can become brittle and crack when exposed to fuel, especially over time. The chemicals in fuel can cause plastic lines to degrade, leading to potential fuel leaks and engine performance issues. It is best to use plastic fuel lines only in non-fuel-carrying applications or with specialized fuels that are less corrosive.
In summary, the compatibility of fuel lines with fuel depends on the material of the line and the type of fuel being used. Rubber, vinyl, and braided steel lines have varying levels of compatibility, while plastic lines are generally not suitable for submersion in fuel. Understanding these material-specific considerations is crucial for maintaining a reliable and safe fuel system in your vehicle. Always consult the manufacturer's guidelines and recommendations for the best fuel line materials and practices for your specific application.
FASS Fuel Line: Unlocking the Power of Your Engine
You may want to see also
Fuel Line Diameter and Submersion Depth: Thicker lines can handle deeper submersion
When considering the submersion of a fuel line in fuel, the diameter of the line plays a crucial role in determining its ability to withstand the depth of submersion. Thicker fuel lines, typically those with larger diameters, offer several advantages in this context.
One of the primary benefits of using thicker fuel lines is their increased strength and structural integrity. As the diameter of a fuel line increases, the wall thickness also increases, providing more material to withstand external forces and pressure. This added strength is particularly important when the fuel line is submerged, as it needs to resist the potential pressure changes and mechanical stresses that occur within the fuel system. Thicker lines can better handle the physical demands of being partially or fully submerged, ensuring a more reliable and secure connection between the fuel tank and the engine.
Additionally, thicker fuel lines often have a higher capacity to carry fuel at higher rates. This is especially relevant in applications where rapid fuel delivery is required, such as in high-performance engines or racing vehicles. The larger diameter allows for a smoother flow of fuel, reducing the likelihood of pressure drops and ensuring a consistent supply to the engine. This is a critical factor in maintaining optimal engine performance and responsiveness.
In terms of submersion depth, thicker fuel lines provide a more robust solution. When a fuel line is submerged, the pressure inside the line can vary depending on the depth and temperature of the fuel. Thicker lines can better accommodate these pressure variations, reducing the risk of fuel line collapse or damage. This is particularly important in situations where the fuel line may be exposed to varying levels of submersion, such as during off-road adventures or when navigating through water bodies.
Furthermore, the use of thicker fuel lines can contribute to improved safety and longevity of the fuel system. By choosing a line with a larger diameter, you are selecting a component that is less prone to punctures, leaks, or damage from external factors. This can lead to a more reliable fuel system, reducing the chances of fuel leaks, engine misfires, or other issues caused by compromised fuel line integrity.
In summary, when dealing with submersion in fuel, thicker fuel lines offer enhanced strength, improved flow capacity, and better pressure resistance. These factors make thicker lines a preferred choice for applications requiring deeper submersion, ensuring a secure and efficient fuel supply to the engine. It is essential to consider the specific requirements of your vehicle or equipment and select fuel lines accordingly to ensure optimal performance and safety.
The Ultimate Guide to Thread Sealants for Fuel Lines
You may want to see also
Fuel Line Length and Submersion: Longer lines may require additional support
When it comes to fuel lines, the length and submersion in fuel are critical factors to consider for optimal performance and safety. Longer fuel lines, while providing certain advantages, can present unique challenges that require careful attention to detail. One of the primary concerns with extended fuel lines is the potential for excessive flexing and movement, especially during acceleration, deceleration, and turns. This can lead to various issues, including fuel starvation, reduced engine performance, and even potential damage to the fuel line itself.
To address these challenges, it is essential to provide additional support for longer fuel lines. This can be achieved through the use of specialized brackets, hangers, or even custom-made support structures. These supports act as a rigid framework, minimizing the movement and potential damage caused by the fuel line's natural flexing. Properly securing the fuel line helps maintain a consistent fuel flow, ensuring that the engine receives the required amount of fuel for optimal operation.
In addition to the physical support, it is crucial to consider the material and construction of the fuel line itself. Longer lines may require the use of high-quality, flexible materials that can withstand the rigors of extended use without compromising fuel flow. The fuel line should be designed to handle the pressure and temperature variations associated with fuel, especially in high-performance applications.
Furthermore, when submerging a fuel line in fuel, it is imperative to ensure that the line is properly sealed and protected. This is particularly important for lines that are exposed to varying fuel levels, as submerging can lead to potential issues with corrosion or fuel contamination. Using fuel-resistant materials and implementing effective sealing techniques can help prevent these problems.
In summary, while longer fuel lines offer certain benefits, they demand careful consideration and additional support to ensure optimal performance and longevity. By addressing the potential challenges associated with length and submersion, engineers and enthusiasts can create robust fuel systems that deliver reliable power and peace of mind. Proper support structures, high-quality materials, and effective sealing techniques are key to achieving these goals.
Fuel Line Removal Guide: 2005 Ford Ranger
You may want to see also
Fuel Line Flexibility and Submersion: Flexible lines can adapt to submersion without damage
The concept of submerging a fuel line in fuel is an important consideration for vehicle owners and mechanics, especially when it comes to ensuring the longevity and reliability of the fuel system. While it might seem counterintuitive, the answer to whether a fuel line can be submerged in fuel is a nuanced one, and the flexibility of the fuel line plays a crucial role.
Flexible fuel lines are an essential component of modern vehicle fuel systems. These lines are designed to withstand the rigors of the automotive environment, including temperature fluctuations, vibrations, and, in some cases, submersion in fuel. The key to understanding this capability lies in the construction and material of these flexible lines. Typically, they are made from high-quality rubber or synthetic materials that are resistant to degradation from fuel exposure. These materials are carefully selected to ensure they can withstand the corrosive nature of fuel over time.
When it comes to submersion, flexible fuel lines offer a unique advantage. Unlike rigid lines, flexible lines can adapt to their environment without compromising their structural integrity. This flexibility allows them to conform to the shape of the fuel tank and surrounding components, reducing the risk of damage during vehicle movement or when the tank is filled. Additionally, the material's resilience ensures that the line can withstand the pressure and potential expansion of fuel when it is submerged, preventing leaks and potential engine issues.
In the event of accidental submersion, the flexibility of the fuel line becomes a critical safety feature. If a vehicle is driven through water or experiences a fuel leak that results in the line being partially submerged, the flexible line can absorb the impact without breaking. This is particularly important in preventing fuel contamination and potential engine damage that could occur if a rigid line were to rupture.
However, it's essential to note that while flexible fuel lines are designed to handle submersion, proper maintenance and regular inspections are still necessary. Over time, fuel lines can degrade, and regular checks can help identify any signs of wear or damage. Ensuring that the fuel system is regularly maintained will contribute to the overall reliability and performance of the vehicle.
In summary, flexible fuel lines are engineered to adapt to submersion in fuel without sustaining damage, thanks to their specialized construction and materials. This feature, combined with regular maintenance, ensures that vehicle owners can have peace of mind knowing that their fuel system is reliable and capable of withstanding various environmental conditions.
Quick Fix: Temporarily Patching a Fuel Line for Emergency Use
You may want to see also
Fuel Line Insulation and Submersion: Insulated lines can withstand fuel submersion without degradation
When it comes to fuel systems, ensuring the integrity and reliability of components is crucial for safe and efficient operation. One common concern is whether fuel lines can be submerged in fuel without causing any issues. The answer is yes, but it depends on the type of fuel line and its insulation. Insulated fuel lines are specifically designed to withstand submersion in fuel without degradation, making them a reliable choice for various applications.
Insulated fuel lines are constructed with multiple layers of protective materials. The inner layer is typically made of a flexible, high-quality rubber or synthetic material that is resistant to fuel chemicals. This inner layer ensures that the fuel line can withstand the corrosive nature of different fuels. The next layer is an insulating material, often made of foam or a similar lightweight, durable substance. This insulation provides thermal protection, preventing the fuel from freezing in cold temperatures and maintaining its flow even in extreme conditions. The outer layer is usually a protective sheath, made of materials like rubber or plastic, which shields the line from external damage and provides additional insulation.
The key to withstanding submersion is the quality and thickness of the insulation. Insulated fuel lines are engineered to maintain their structural integrity even when partially or fully submerged. The insulation acts as a barrier, preventing the fuel from directly contacting the inner material of the line, which could lead to degradation over time. This is particularly important in applications where fuel lines are exposed to varying environmental conditions, such as in marine or outdoor settings.
In addition to insulation, the choice of materials plays a significant role. High-quality, fuel-resistant materials are used to ensure longevity. For example, some fuel lines use a unique blend of synthetic rubbers that are inherently resistant to fuel degradation, making them ideal for long-term submersion. These specialized materials can withstand the chemical properties of various fuels, including gasoline, diesel, and aviation fuels, without compromising their performance.
When selecting fuel lines, it is essential to consider the specific requirements of your application. Insulated lines are a reliable option for those seeking to ensure the longevity and performance of their fuel systems, especially in challenging environments. By choosing the right insulated fuel line, you can have peace of mind knowing that your fuel system is protected against the potential issues caused by fuel submersion.
Unclogging the Jeep Cherokee: A Guide to Removing the Fuel Line
You may want to see also
Frequently asked questions
Yes, it is common for fuel lines to be submerged in fuel, especially in vehicles with fuel tanks located lower than the engine. This is a standard design practice to ensure that the fuel lines are protected and do not come into contact with air, which can cause fuel degradation and potential engine issues.
If the fuel line is not submerged, it may be exposed to air, leading to several problems. Air in the fuel can cause phase separation, where the fuel and vapor separate, resulting in poor engine performance. Additionally, air bubbles can be drawn into the engine, causing knocking, reduced power, and potential engine damage.
Fuel lines should be routed in a way that keeps them submerged in the fuel as much as possible. This can be achieved by using flexible hoses with a slight slope from the fuel tank to the engine. Proper routing ensures that the fuel line remains filled with fuel, preventing air ingestion and maintaining optimal engine operation.