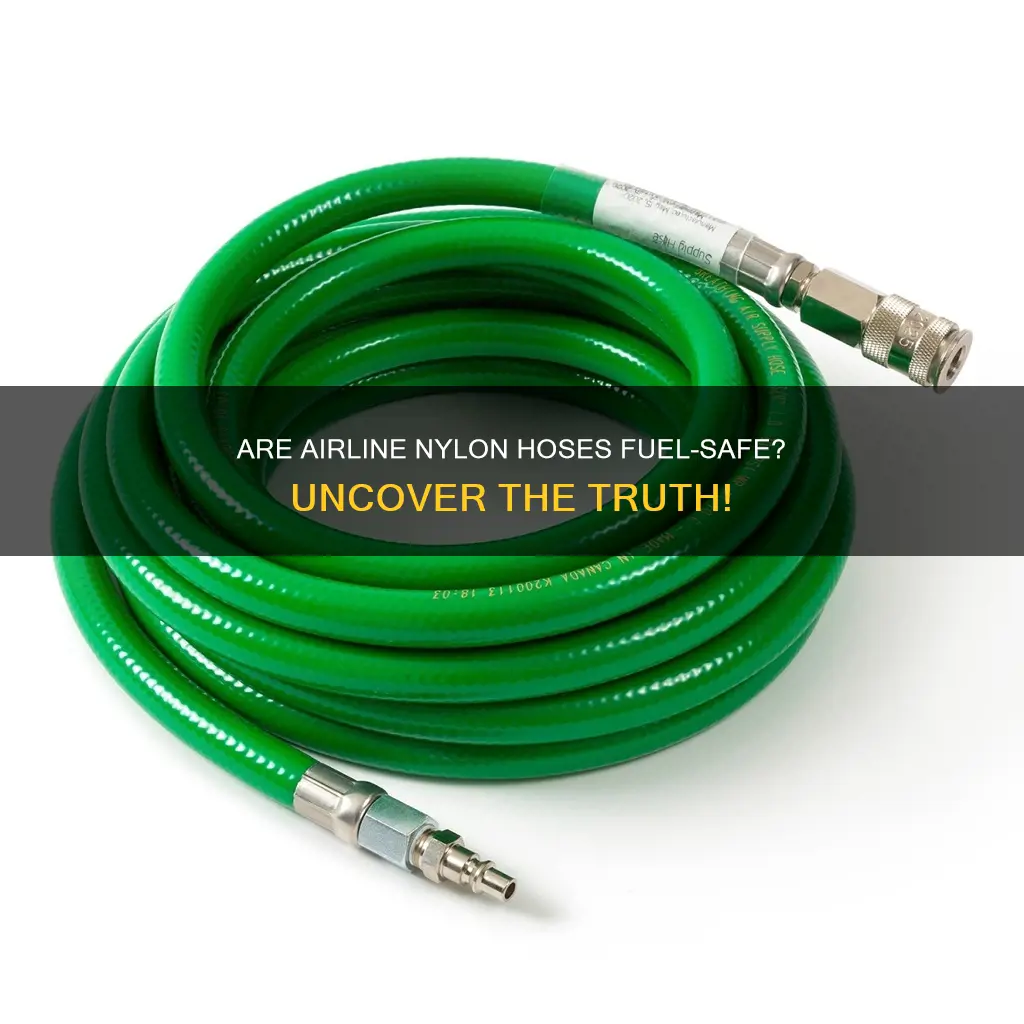
Are airline nylon hoses fuel safe? This question is crucial for aviation safety and maintenance. Nylon hoses are commonly used in aircraft fuel systems, but their safety and compatibility with aviation fuels are essential considerations. The hoses must withstand the corrosive nature of aviation fuels, maintain flexibility over a wide temperature range, and not contribute to fuel contamination. This introduction sets the stage for a detailed exploration of the factors that determine the safety and suitability of airline nylon hoses for fuel transport in aircraft.
Characteristics | Values |
---|---|
Material | Nylon |
Temperature Range | -40°F to 212°F (-40°C to 100°C) |
Pressure Rating | Up to 250 psi (pounds per square inch) |
Flexibility | High flexibility for easy installation and movement |
Chemical Resistance | Resistant to most fuels, acids, and bases |
UV Resistance | Good UV resistance for outdoor use |
Color | Typically black or white |
Diameter | Varies, commonly 1/4", 3/8", 1/2" |
Length | Customizable, available in various lengths |
Connection Type | Male or female threads, quick-connect fittings |
Application | Fuel delivery systems, aircraft, boats, and industrial machinery |
Safety | Meets or exceeds industry standards for fuel hose safety |
Compliance | UL listed, FM approved, and meets DOT requirements |
What You'll Learn
- Material Compatibility: Nylon hoses must be compatible with aviation fuels to prevent degradation
- Pressure Rating: Hoses should meet or exceed fuel system pressure requirements for safe operation
- Flexibility: Nylon's flexibility ensures hoses can withstand aircraft movement without cracking
- Temperature Tolerance: Hoses must handle fuel temperature variations without becoming brittle or leaking
- Fire Resistance: Nylon hoses should resist fire to prevent fuel ignition and ensure passenger safety
Material Compatibility: Nylon hoses must be compatible with aviation fuels to prevent degradation
Nylon hoses are commonly used in aviation fuel systems due to their lightweight and flexibility, making them an attractive choice for aircraft manufacturers and operators. However, the compatibility of these hoses with aviation fuels is a critical aspect that requires careful consideration. Nylon, being a synthetic polymer, has specific properties that need to be evaluated when used in fuel-carrying applications.
When it comes to material compatibility, nylon hoses must be designed and selected to withstand the corrosive nature of aviation fuels. These fuels often contain additives and blends that can accelerate the degradation of certain materials, including nylon. The primary concern is the potential for fuel to cause chemical reactions with the hose material, leading to cracking, swelling, or softening over time. This degradation can result in fuel leaks, reduced hose performance, and potential safety hazards.
To ensure compatibility, manufacturers and aviation professionals should refer to material data sheets and technical specifications provided by hose suppliers. These resources offer detailed information on the compatibility of different nylon types with various aviation fuels. For instance, some nylon compounds may be more resistant to aliphatic and aromatic hydrocarbons commonly found in aviation fuels, ensuring longer-lasting performance. It is essential to choose the appropriate nylon grade that can withstand the specific fuel composition and operating conditions.
Regular inspections and maintenance are also crucial in maintaining the integrity of nylon hoses. Over time, even with compatible materials, hoses may show signs of wear and tear due to the harsh environment. Inspecting hoses for cracks, brittleness, or any signs of fuel infiltration is essential. Replacing hoses that show signs of degradation can prevent potential failures and ensure the safety of the aviation fuel system.
In summary, while nylon hoses offer advantages in terms of weight and flexibility, their compatibility with aviation fuels is a critical factor. Proper material selection, based on technical specifications, and regular maintenance can ensure that nylon hoses remain safe and reliable in fuel-carrying applications. Adhering to these guidelines will contribute to the overall safety and efficiency of aircraft fuel systems.
Crafting Your Own Fuel Line: A Step-by-Step Guide
You may want to see also
Pressure Rating: Hoses should meet or exceed fuel system pressure requirements for safe operation
When considering the safety of using air line nylon hoses for fuel systems, one critical aspect is the pressure rating of the hoses. The pressure rating is a fundamental specification that ensures the hose can withstand the operating conditions and pressures within the fuel system without compromising safety. Here's why this is essential:
Meeting Pressure Requirements: Fuel systems, especially in aviation and automotive applications, operate under varying pressure conditions. The pressure rating of the hose must match or exceed the maximum expected pressure in the system. This ensures that the hose can handle the fuel's force without failing, which could lead to dangerous situations such as fuel leaks or even explosions. For instance, if a hose with an inadequate pressure rating is used, it might burst under high pressure, causing fuel to spray and potentially igniting, resulting in a fire hazard.
Safety and Performance: Hoses with appropriate pressure ratings are designed to maintain a secure connection between the fuel source and the engine or other components. They prevent fuel from escaping the system due to pressure differentials. Over time, a hose with a lower pressure rating might degrade, leading to reduced performance and potential safety risks. Therefore, it is crucial to select hoses that meet or exceed the manufacturer's recommended pressure requirements.
Longevity and Maintenance: Properly rated hoses contribute to the longevity of the fuel system. They help prevent premature wear and tear, ensuring that the system remains reliable over extended periods. Regular maintenance and inspections should include checking the pressure rating and overall condition of the hoses to identify any signs of deterioration or damage.
Compliance and Standards: Adhering to industry standards and regulations is essential for fuel system safety. Many countries and aviation authorities have specific guidelines regarding hose pressure ratings for fuel systems. By selecting hoses that meet or exceed these standards, you ensure compliance and enhance the overall safety of the fuel delivery system.
In summary, the pressure rating of air line nylon hoses is a critical factor in determining their safety for fuel systems. It ensures that the hoses can handle the operating pressures, maintain a secure connection, and contribute to the overall performance and longevity of the fuel system. When using these hoses, always refer to the manufacturer's specifications and industry standards to ensure safe and efficient fuel delivery.
The Release of 'Frontline: Fuel of War' in 2008
You may want to see also
Flexibility: Nylon's flexibility ensures hoses can withstand aircraft movement without cracking
Nylon hoses are an essential component in aviation, particularly in the fuel supply system of aircraft. One of the key advantages of using nylon hoses in this context is their remarkable flexibility. This flexibility is a critical feature that ensures the hoses can withstand the various movements and vibrations experienced during flight without compromising their structural integrity.
The ability of nylon hoses to flex is attributed to the material's inherent properties. Nylon is a synthetic polymer known for its exceptional elasticity, allowing it to deform and return to its original shape without permanent distortion. This characteristic is vital in the dynamic environment of an aircraft, where hoses need to accommodate the movement of the plane's engines, wings, and other components.
In the context of fuel safety, flexibility is crucial. Aircraft fuel systems are subject to constant motion and stress, especially during takeoff and landing. If the hoses were rigid, they might crack or break under the pressure, potentially leading to fuel leaks or even fires. Nylon hoses, however, can absorb and distribute these stresses evenly, ensuring that the fuel supply remains secure and uninterrupted.
The flexibility of nylon hoses also contributes to their durability. Over time, the constant flexing and movement can take a toll on other materials, leading to wear and tear. Nylon's resilience ensures that the hoses maintain their structural integrity, providing long-lasting performance. This is particularly important in aviation, where reliability and safety are paramount.
Furthermore, the flexibility of nylon hoses allows for easier installation and maintenance. The hoses can be routed around various aircraft components without the risk of damage or restriction. This ease of installation and maintenance is a significant advantage, ensuring that the fuel system remains efficient and safe throughout the aircraft's operational life.
Foxbody Fuel Line Placement: A Step-by-Step Guide to Carburetor Fueling
You may want to see also
Temperature Tolerance: Hoses must handle fuel temperature variations without becoming brittle or leaking
Nylon hoses, when used for fuel lines, must be designed to withstand a wide range of temperature variations to ensure safety and reliability. The temperature tolerance of these hoses is a critical factor, especially in automotive and aviation applications where fuel temperatures can fluctuate significantly.
Extreme temperatures, both hot and cold, can have detrimental effects on the performance and integrity of fuel hoses. In high-temperature environments, such as during prolonged engine operation or in certain climates, the fuel can reach temperatures that are close to or exceed the boiling point. At these temperatures, the fuel hoses must remain flexible and resistant to heat degradation to prevent cracking, brittleness, or melting. This is particularly important to maintain a secure connection and avoid fuel leaks, which could lead to dangerous situations.
On the other hand, low temperatures can also pose challenges. When fuel hoses are exposed to freezing temperatures, they must retain their flexibility to prevent the fuel from becoming too thick and difficult to pump. Hoses that become brittle in cold conditions may crack or split, resulting in fuel leaks and potential engine damage. Therefore, the material and construction of the hose must be carefully chosen to ensure it can handle the full temperature spectrum without compromising its structural integrity.
To achieve optimal temperature tolerance, manufacturers often use specialized materials and additives in the hose construction. These materials can include flexible, high-temperature-resistant polymers that provide the necessary elasticity and durability. Additionally, hoses may be reinforced with layers of fabric or braids to enhance their strength and ability to withstand temperature extremes.
In summary, for air line nylon hoses to be considered fuel-safe, they must be engineered to handle the dynamic temperature variations associated with fuel systems. This involves selecting appropriate materials, ensuring proper reinforcement, and testing the hoses to confirm their performance within the specified temperature range. By meeting these requirements, the hoses can effectively transport fuel while maintaining their structural integrity and safety.
Mastering the Art: A Guide to Removing Fuel Lines from Compression Nuts
You may want to see also
Fire Resistance: Nylon hoses should resist fire to prevent fuel ignition and ensure passenger safety
Nylon hoses, commonly used in aviation and industrial applications, are an essential component in ensuring the safety and efficiency of fuel systems. When it comes to fire resistance, these hoses play a critical role in preventing fuel ignition and maintaining passenger safety. The primary concern with fuel systems is the potential for fire ignition, which can have catastrophic consequences. Nylon hoses are designed to withstand high temperatures and resist fire, making them an ideal choice for fuel lines.
The fire resistance of nylon hoses is a result of their chemical composition and construction. Nylon, a synthetic polymer, has inherent flame-retardant properties. It contains additives that further enhance its fire-resistant characteristics, making it suitable for fuel transportation. These hoses are engineered to maintain their structural integrity and functionality even when exposed to intense heat. In the event of a fire, nylon hoses can withstand the extreme temperatures, preventing fuel from igniting and minimizing the risk of a fire spreading.
Furthermore, the design and flexibility of nylon hoses contribute to their fire resistance. The hoses are typically constructed with multiple layers, including an inner layer that comes into direct contact with the fuel. This design ensures that even if the outer layer is compromised, the inner layer remains intact, maintaining the hose's functionality. Additionally, the flexibility of nylon allows for easy routing and installation, making it adaptable to various aircraft and vehicle designs.
In aviation, where fuel safety is paramount, nylon hoses are a preferred choice. They are used in aircraft fuel systems to connect tanks, pumps, and engines. The ability of nylon hoses to resist fire ensures that in the unlikely event of a fire onboard, the fuel system remains intact, preventing fuel ignition and potential explosions. This level of fire resistance is crucial for passenger safety and the overall reliability of the aircraft.
In summary, nylon hoses are a vital component in fuel safety, particularly in fire-resistant applications. Their ability to withstand high temperatures and resist fire ignition makes them an excellent choice for fuel lines in aviation and industrial settings. By utilizing nylon hoses, the risk of fuel-related fires is significantly reduced, ensuring the well-being of passengers and the efficient operation of fuel systems.
The Ultimate Guide to Choosing Lubricant for Rubber Fuel Lines
You may want to see also
Frequently asked questions
Yes, air line nylon hoses can be used for fuel transfer, but it's important to choose the right type and ensure compatibility with the fuel type. Look for hoses specifically designed for fuel applications, as they will have the necessary features like resistance to fuel degradation and flexibility.
To determine if a nylon hose is fuel-safe, check for certifications and labels indicating its suitability for fuel use. Look for hoses that meet industry standards and are approved for fuel applications. Additionally, consider the hose's material, construction, and additives to ensure it can withstand the chemicals in the fuel without leaching or degradation.
Yes, aviation fuel is a specialized type of fuel that can be safely transferred using nylon hoses. However, it's crucial to select hoses designed explicitly for aviation or fuel transfer applications. These hoses should be able to handle the unique properties of aviation fuel, including its volatility and temperature variations.
Nylon hoses offer several benefits for fuel lines. They are lightweight, flexible, and resistant to abrasion, making them easy to install and route. Nylon hoses also have good chemical resistance, which is essential for fuel applications, as they can withstand various fuel types and additives. Additionally, they are often more cost-effective than other materials while maintaining performance and durability.