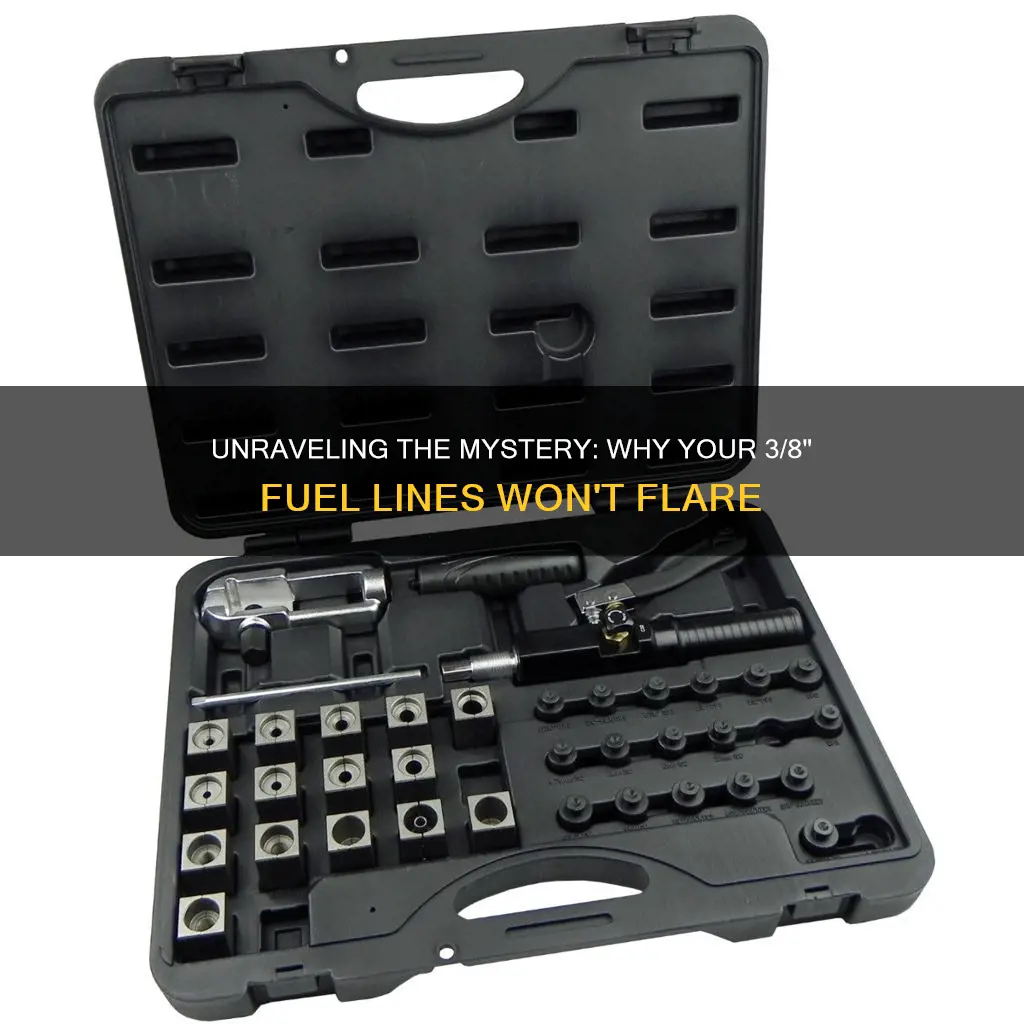
If you're struggling with why your 3/8 steel fuel lines won't flare, you're not alone. Many DIY enthusiasts and mechanics encounter this issue when working with fuel lines. The problem often stems from the material's inherent brittleness and the difficulty in creating a tight, secure flare. This can lead to leaks or reduced fuel flow, which can be a serious concern for any vehicle's performance and safety. Understanding the causes and potential solutions to this issue is crucial for anyone looking to improve their fuel line installation or repair.
Characteristics | Values |
---|---|
Material | Steel |
Diameter | 3/8 inches |
Flare Type | Male or Female |
Temperature Range | Varies by manufacturer, typically -40°F to 250°F |
Pressure Rating | 150-300 psi (depending on thickness and design) |
Flexibility | Moderate to high, depending on wall thickness |
Corrosion Resistance | Good, especially with proper coatings |
Common Applications | Fuel systems, plumbing, automotive |
Flare Tool Compatibility | Standard flare tools (e.g., flare nut, die, and mandrel) |
Common Issues | Hardness, cracking, or poor flare quality |
Solutions | Using the correct tools, proper preparation, and following manufacturer guidelines |
What You'll Learn
- Material Compatibility: Ensure steel fuel lines are compatible with fuel type and temperature
- Flare Design: Check flare design and size for proper fit
- Tool Quality: Use high-quality tools for consistent flare results
- Torque Settings: Follow manufacturer's torque settings for optimal flare
- Line Thickness: Verify fuel line thickness matches flare requirements
Material Compatibility: Ensure steel fuel lines are compatible with fuel type and temperature
When it comes to fuel lines, material compatibility is a critical factor that can significantly impact the performance and longevity of your fuel system. In the context of 3/8-inch steel fuel lines, ensuring compatibility with the fuel type and temperature is essential to avoid potential issues.
Different fuels have varying chemical compositions and properties, and using the wrong material for fuel lines can lead to problems. For instance, gasoline and diesel have different octane levels and additives, and these factors can affect the material's performance. Steel, a common choice for fuel lines, may not be suitable for all fuel types. For example, gasoline can be more corrosive to steel compared to diesel, leading to potential degradation and failure of the fuel lines over time. Therefore, it is crucial to consider the specific fuel type your vehicle uses and choose the appropriate material accordingly.
Temperature is another critical factor to consider. Fuel lines need to withstand the temperature variations experienced during different driving conditions. Extreme temperatures can cause materials to expand or contract, leading to potential damage or failure. Steel, being a metal, can be susceptible to temperature-related issues. If the fuel lines are exposed to high temperatures, such as those found in a hot engine bay, the steel may become brittle or even melt, resulting in a complete failure of the fuel system. On the other hand, low temperatures can cause the fuel to thicken or gel, making it difficult for the engine to start. In such cases, using a material with better temperature resistance, like a specialized fuel line compound, might be necessary.
To ensure compatibility, it is recommended to consult the vehicle's manual or seek professional advice. Manufacturers often provide specific guidelines regarding the type of fuel lines required for their vehicles. These recommendations are based on extensive testing and research to ensure optimal performance and safety. Using the correct material for fuel lines will not only prevent potential issues but also ensure the longevity of your fuel system, saving you from costly repairs and replacements.
In summary, when dealing with 3/8-inch steel fuel lines, understanding and addressing material compatibility is vital. By considering the fuel type and temperature, you can make informed decisions to ensure the fuel lines function correctly and reliably, providing a safe and efficient fuel supply to your vehicle's engine.
Understanding the Car's Fuel Line: A Comprehensive Guide
You may want to see also
Flare Design: Check flare design and size for proper fit
When dealing with fuel lines, ensuring a proper fit is crucial for optimal performance and safety. One common issue that many DIY enthusiasts and mechanics encounter is the difficulty of flaring 3/8-inch steel fuel lines. This problem often stems from the flare design and size not being compatible with the fuel line's specifications.
The flare design refers to the shape and structure of the end of the fuel line where it connects to a fitting. Different types of flares exist, such as compression, crimp, or union flares, each requiring specific tools and techniques for installation. For 3/8-inch fuel lines, the most common flare type is the compression flare, which involves compressing the fuel line material to create a secure connection. However, if the flare design doesn't match the fuel line's internal diameter, it can lead to an improper fit.
To ensure a proper fit, it's essential to check the flare design and size. Start by examining the fuel line's specifications, including the internal diameter and the required flare type. Most fuel lines have a standard internal diameter of 3/8-inch, but the flare design can vary depending on the manufacturer and application. For example, some fuel lines might use a 1/2-inch flare, while others might have a 3/8-inch flare with a different angle or shape.
When purchasing flare tools, ensure they are compatible with the flare design you need. Different flare tools are designed for specific flare angles and sizes. For instance, a 3/8-inch compression flare tool might have a different angle and pressure requirements compared to a 1/2-inch flare tool. Using the wrong tool can result in an improper flare, leading to leaks or reduced performance.
Additionally, consider the material of the fuel line and the fitting. Steel fuel lines require specific flare tools and techniques to ensure a secure connection. If the flare design doesn't match the fuel line's specifications, it can lead to an improper fit, causing the fuel line to pull out of the fitting or not seal properly. Always refer to the manufacturer's guidelines and recommendations for the best results.
Chevy Fuel Tank: Understanding the Lines and Connections
You may want to see also
Tool Quality: Use high-quality tools for consistent flare results
When it comes to working with fuel lines, especially those made of 3/8-inch steel, using the right tools is crucial for achieving a secure and reliable flare connection. The quality of your tools directly impacts the consistency and durability of your work. Here's why investing in high-quality tools is essential:
Precision and Consistency: High-quality tools, such as flares and crimping machines, are designed with precision in mind. They provide accurate measurements and consistent force application, ensuring that your fuel lines are flared to the correct specifications. This precision is vital to maintain the structural integrity of the fuel lines and prevent potential leaks or damage. Cheaper alternatives might lack this level of accuracy, leading to inconsistent flares and potential issues down the line.
Durability and Longevity: Fuel lines are subjected to various environmental factors and mechanical stresses. Using durable tools that can withstand these conditions is essential. High-quality tools are often made from robust materials, ensuring they don't wear out quickly or become damaged during the flaring process. This longevity means you won't need to replace tools frequently, saving you time and money in the long run.
Safety and Reliability: Flare connections that are not properly executed can lead to safety hazards. High-quality tools are designed with safety in mind, ensuring that the flaring process is secure and controlled. They minimize the risk of errors, such as over-tightening or under-tightening, which could compromise the connection's integrity. This reliability is crucial when working with fuel lines, as any compromise in the connection could lead to dangerous situations.
Professional Results: The appearance and finish of your work matter, especially in professional settings. High-quality tools produce clean, precise flares with a professional finish. This not only enhances the overall aesthetics of your project but also demonstrates your attention to detail and commitment to quality. Whether you're a mechanic, a DIY enthusiast, or a professional installer, using top-notch tools will elevate the standard of your work.
In summary, investing in high-quality tools for flaring 3/8-inch steel fuel lines is a wise decision. It ensures consistent and reliable results, promotes safety, and provides a professional finish. While it may require a higher initial investment, the long-term benefits of using top-tier tools are undeniable, making it a valuable choice for anyone working with fuel lines.
Unveiling the Material Secrets of Micro Fuel Lines
You may want to see also
Torque Settings: Follow manufacturer's torque settings for optimal flare
When working with fuel lines, especially those made of 3/8-inch steel, achieving a secure flare connection is crucial for maintaining the integrity of your fuel system. One of the most critical aspects of this process is adhering to the manufacturer's torque settings. These settings are not arbitrary; they are carefully calculated to ensure that the flare connection is tight enough to provide a reliable seal without causing damage to the fuel line or the fitting.
The torque specifications for flare connections are typically provided by the manufacturer of the fuel line or the fitting. These values are determined through extensive testing and are designed to optimize the connection's strength and longevity. Using the correct torque ensures that the flare is neither too tight, which could lead to cracking or damage, nor too loose, which could result in an inadequate seal.
To follow the manufacturer's torque settings, you should consult the documentation that comes with your fuel lines or fittings. This documentation will specify the exact torque value required for the particular size and type of flare connection you are working with. It is essential to use a torque wrench to apply the correct amount of force, as an imprecise measurement can compromise the quality of the connection.
Over-tightening can cause the steel fuel line to distort or even break, while under-tightening can lead to a poor seal, potentially causing fuel leaks. Therefore, precision is key. By using the recommended torque settings, you ensure that the flare is formed correctly, creating a tight, reliable connection that can withstand the pressures and temperatures of the fuel system.
In summary, adhering to the manufacturer's torque settings is a fundamental practice in ensuring the quality and longevity of your fuel line connections. It is a simple yet critical step that can prevent potential issues and ensure the safe and efficient operation of your vehicle's fuel system. Always refer to the provided instructions and specifications to achieve the best results.
Best Fuel Line to Prevent Vapor Lock: Expert Recommendations
You may want to see also
Line Thickness: Verify fuel line thickness matches flare requirements
When working with fuel lines, ensuring the correct thickness is crucial for a successful flare connection. The thickness of the fuel line should match the specifications provided by the manufacturer or the flare requirements. This is an essential step to guarantee a secure and reliable connection. Here's a detailed guide on how to verify the line thickness:
Start by examining the fuel line you intend to flare. Measure the thickness at multiple points along the length of the line to ensure consistency. Use a caliper or a micrometer to get precise measurements. Compare these measurements against the manufacturer's guidelines or the flare specifications. Different fuel lines may have varying thickness requirements, so it's important to refer to the correct documentation. For example, a 3/8-inch fuel line might have a specific thickness range that needs to be adhered to for a proper flare.
If you're working with a set of fuel lines, it's a good practice to check each line individually. This ensures that all lines meet the required thickness, especially if they are meant for a specific application or vehicle. Consistency in thickness is vital to avoid potential issues during the flaring process.
When flaring, the goal is to create a smooth and continuous connection between the fuel line and the fitting. If the line is too thick, it may not flare properly, leading to an incomplete or weak connection. Conversely, if it's too thin, the flare may not provide the necessary strength and durability. Therefore, accurate measurements and careful comparison with the specifications are key to success.
Additionally, consider the material of the fuel line. Steel fuel lines, for instance, may have different thickness requirements compared to other materials. The flare process might vary depending on the material, so it's essential to be aware of these differences. Always refer to the manufacturer's instructions or seek guidance from experts to ensure you are using the correct techniques for your specific fuel line material.
Toyota Corolla Fuel Line Location: 1989 Model Guide
You may want to see also
Frequently asked questions
Flare fitting issues can be caused by several factors. Firstly, ensure that the fuel lines and fittings are clean and free of any debris or contaminants. Over time, fuel lines can accumulate dirt and corrosion, which can interfere with the flare process. Cleaning and deburring the lines and fittings before attempting to flare them is essential. Secondly, check the quality and condition of the flare tools. Worn-out or damaged tools may not provide the necessary pressure and precision for a successful flare. Consider replacing or sharpening the tools if they are not functioning optimally.
Proper preparation is key to successful flaring. Start by cutting the fuel lines to the desired length, ensuring a straight and clean cut. Use a pipe cutter or a sharp blade to achieve this. Then, deburr the ends of the lines by using a deburring tool or a file to remove any sharp edges. This step is crucial to prevent damage to the fittings and ensure a tight connection. Additionally, inspect the fittings for any defects or damage and replace them if necessary.
Flaring 3/8" steel fuel lines requires a careful approach. Begin by inserting the line into the fitting, ensuring it is centered. Then, use the flare tool to apply pressure and create the flare. Start with a gentle force and gradually increase it while rotating the tool. The goal is to form a smooth, rounded bend without kinking the line. Practice and patience are essential, as flaring can be a delicate process. Consider watching online tutorials or seeking guidance from experienced professionals for better results.
If the flare doesn't form correctly, it may be due to several reasons. Check for any obstructions or interference that might prevent the line from bending properly. Ensure that the flare tool is aligned correctly and that you are applying the right amount of force. Sometimes, the issue could be with the fitting itself, so inspect it for any defects. If the problem persists, consider seeking advice from a professional mechanic or a specialist in fuel system repairs.
Yes, there are alternative methods to consider if flaring is not feasible. One option is to use compression fittings, which involve inserting the fuel line into a fitting and then compressing it to create a secure connection. Another method is soldering, where you melt a solder material onto the line and fitting, creating a strong bond. However, it's important to note that these methods may require additional tools and skills, and the choice of method should be based on the specific requirements of your fuel system and local regulations.