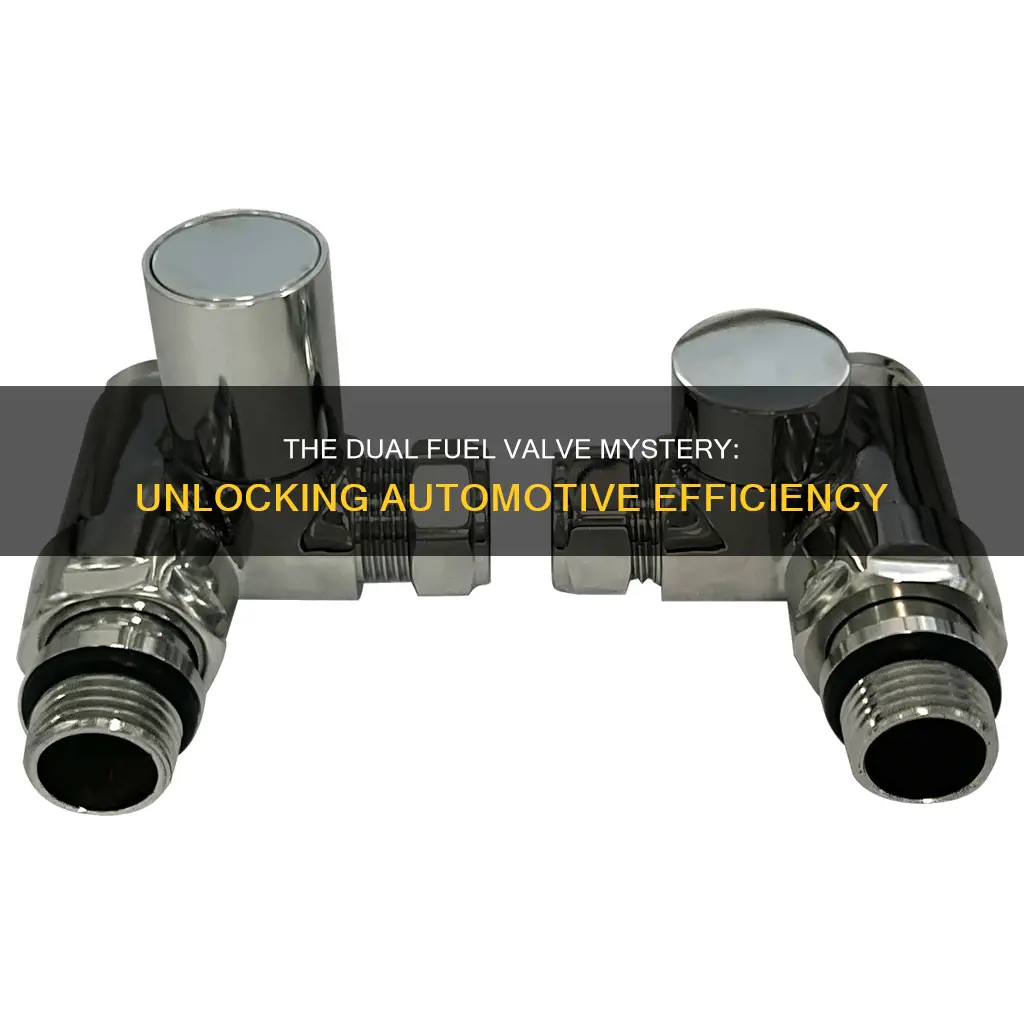
Cars are equipped with two fuel valves for a specific reason: to ensure efficient and safe fuel delivery. The primary function of the fuel valves is to regulate the flow of gasoline from the fuel tank to the engine. One valve, often referred to as the main fuel valve, is responsible for controlling the overall fuel supply to the engine, allowing the driver to start the vehicle and maintain steady operation. The second valve, typically a smaller one, is used for fuel pressure regulation. This secondary valve helps maintain optimal fuel pressure within the engine, ensuring that the fuel-air mixture is correctly balanced for efficient combustion. By having two fuel valves, car manufacturers can provide precise control over fuel delivery, enhance engine performance, and prevent potential issues related to fuel pressure and flow, ultimately contributing to a more reliable and safe driving experience.
What You'll Learn
- Engine Design: Two valves ensure efficient fuel distribution for optimal combustion
- Performance Enhancement: Multiple valves improve power output and engine response
- Safety Measures: Redundant valves prevent fuel leaks and potential hazards
- Fuel Efficiency: Dual valves optimize fuel usage, reducing emissions and costs
- Historical Context: Early engines used two valves for better control and reliability
Engine Design: Two valves ensure efficient fuel distribution for optimal combustion
The concept of having two fuel valves in a car's engine is an intriguing design choice that significantly impacts performance and efficiency. This design is not merely a random feature but a carefully considered engineering solution to optimize fuel distribution and combustion. The primary purpose of these two valves is to ensure that the fuel-air mixture is precisely controlled and delivered to the engine's cylinders at the right time and in the correct proportions.
In the internal combustion engine, the process of fuel injection and combustion is a delicate balance. The engine requires a precise ratio of fuel to air for efficient combustion, which is crucial for optimal power output and fuel efficiency. Here's where the dual-fuel valve system comes into play. The first valve, often referred to as the low-pressure valve, is responsible for the initial injection of fuel into the engine. This valve operates at a lower pressure, allowing for a more controlled and precise injection of fuel into the intake manifold or directly into the combustion chamber. By doing so, it ensures that the fuel is introduced at the optimal point in the engine's cycle, promoting efficient combustion.
The second valve, typically a high-pressure valve, takes over the task of fine-tuning the fuel-air mixture. This valve operates at a higher pressure, enabling it to inject a more significant amount of fuel into the engine. Its primary function is to adjust the fuel-air ratio, ensuring that the mixture is neither too rich (excessive fuel) nor too lean (insufficient fuel). This adjustment is critical for maintaining optimal combustion, as it directly impacts the engine's power output and fuel consumption. The high-pressure valve's precision in controlling the fuel-air mixture contributes to better engine performance and reduced emissions.
Engine designers have implemented this dual-fuel valve system to address the challenges of achieving efficient combustion. By having two valves, the engine can better manage the fuel injection process, ensuring that the fuel is distributed in the correct ratio for each cylinder. This design approach allows for more accurate control over the combustion process, resulting in improved engine performance, reduced fuel consumption, and enhanced overall efficiency. Moreover, this system contributes to the engine's ability to adapt to varying driving conditions and loads, providing a consistent and reliable power output.
In summary, the presence of two fuel valves in a car's engine is a strategic design element that facilitates efficient fuel distribution and optimal combustion. This design ensures that the engine operates at its peak performance while maintaining fuel efficiency and minimizing emissions. The dual-fuel valve system is a testament to the intricate engineering that goes into modern vehicle design, where every component plays a vital role in achieving the desired performance and reliability.
Understanding Fuel Transportation Rules: What You Need to Know
You may want to see also
Performance Enhancement: Multiple valves improve power output and engine response
The concept of multiple fuel valves in engines is an intriguing one, especially when considering the performance enhancements it brings. While it might seem counterintuitive to have multiple valves for a single function, the design is a strategic move to optimize engine performance. The primary reason for having two fuel valves is to improve power output and engine response, ensuring a more efficient and responsive driving experience.
In a typical engine, the role of the fuel valve is to control the flow of fuel into the combustion chamber. With a single valve, this task is straightforward, but it presents limitations in terms of performance. Multiple fuel valves, often referred to as sequential valves, offer a more nuanced approach to fuel injection. By having two valves, one can be positioned to inject fuel at the start of the compression stroke, while the other is used for the later stages. This sequential injection strategy allows for a more precise and controlled fuel delivery process.
The performance benefits are twofold. Firstly, the early injection of fuel by the first valve ensures that the combustion process begins promptly, resulting in a rapid rise in engine speed. This is particularly advantageous during acceleration, as it provides an immediate power boost, making the car more responsive to driver input. Secondly, the later injection by the second valve contributes to a more efficient combustion process. By the time the second valve activates, the engine has already reached a higher compression level, allowing for a more complete and efficient burn of the fuel-air mixture. This leads to increased power output and improved engine performance overall.
The design of these sequential fuel valves is a testament to the engineering prowess required to optimize engine functionality. It showcases how multiple valves can work in harmony to enhance performance, rather than just serving as a redundant system. This approach ensures that the engine can deliver power efficiently, especially under varying load conditions, making it a crucial aspect of modern engine design.
In summary, the use of two fuel valves in an engine is a strategic design choice to enhance performance. By allowing for sequential fuel injection, the engine can optimize power output and engine response, ensuring a more dynamic and efficient driving experience. This is a prime example of how automotive engineering continually strives to improve the capabilities of internal combustion engines.
Fuel Pump Testing: A Step-by-Step Guide for DIY Mechanics
You may want to see also
Safety Measures: Redundant valves prevent fuel leaks and potential hazards
The presence of two fuel valves in a car's engine is a safety feature designed to prevent fuel leaks and potential hazards. This design is a result of the understanding that a single fuel valve might fail or malfunction, leading to dangerous consequences. By having two valves, the system provides a level of redundancy that is crucial for the overall safety of the vehicle and its occupants.
One of the primary safety measures is the prevention of fuel leaks. Fuel is a highly flammable substance, and any leak can pose a significant fire hazard. With two fuel valves, the system ensures that even if one valve fails to close properly, the other valve can still effectively control the fuel flow. This redundancy minimizes the risk of fuel escaping into the engine compartment, where it could ignite and cause a fire.
In the event of a malfunction, the second fuel valve acts as a backup, ensuring that the fuel supply can be controlled or shut off. This is particularly important during engine operation, as a malfunctioning valve could lead to an over-rich fuel mixture, which can cause the engine to run poorly or even stall. By having a second valve, the system can maintain the correct fuel-air ratio, ensuring the engine operates efficiently and safely.
Additionally, the dual-valve system provides an extra layer of protection against potential hazards associated with fuel. For instance, in the case of a fuel pump failure, the second valve can still allow for the controlled release of fuel, preventing a dangerous accumulation of fuel pressure. This is especially critical in preventing fuel-related explosions, which could occur if a single valve malfunctioned and allowed fuel to build up in the system.
The design of having two fuel valves is a testament to the automotive industry's commitment to safety. It demonstrates a proactive approach to potential risks, ensuring that vehicles are equipped with robust systems that can handle various failure scenarios. This level of redundancy is a critical component of modern vehicle safety, contributing to the overall reliability and security of the transportation system.
Mastering the Art of Filling Up: A Guide to Gas Station Fueling
You may want to see also
Fuel Efficiency: Dual valves optimize fuel usage, reducing emissions and costs
The concept of dual fuel valves in automobiles is an innovative approach to enhancing fuel efficiency and reducing environmental impact. This design feature, often found in modern engines, is a strategic solution to optimize fuel consumption and minimize waste. By employing two fuel valves, engineers have created a system that allows for precise control over the fuel-air mixture, leading to improved performance and reduced emissions.
In the pursuit of fuel efficiency, the dual-valve system plays a crucial role. When a car's engine operates, it requires a precise balance of fuel and air to ensure efficient combustion. The primary function of the two valves is to manage this process. One valve is responsible for delivering fuel to the engine, while the other controls the intake of air. This separation of duties enables a more controlled and efficient fuel injection process. By having dedicated valves for fuel and air, the system can fine-tune the mixture, ensuring that the engine receives the optimal amount of each component. This precision results in better combustion, where fuel is burned more completely, leaving less unburned fuel in the exhaust.
The benefits of this design become evident in the form of reduced emissions. With a well-regulated fuel-air mixture, the engine can produce fewer harmful byproducts, such as carbon monoxide and nitrogen oxides, which are major contributors to air pollution. Lower emissions not only help the environment but also contribute to better engine performance and longevity. Additionally, this efficient combustion process leads to improved fuel economy, allowing vehicles to travel farther on a single tank of fuel, which is a significant advantage for drivers.
Furthermore, the dual-valve system contributes to cost savings for vehicle owners. By optimizing fuel usage, cars equipped with this technology can achieve higher mileage, reducing the frequency of fuel refills. This not only saves money but also decreases the overall environmental impact associated with fuel extraction and transportation. Over time, the efficient combustion and reduced emissions can lead to lower maintenance costs, as engines tend to operate more smoothly and experience less wear and tear.
In summary, the implementation of dual fuel valves in automobiles is a strategic engineering solution that significantly enhances fuel efficiency. This design optimizes fuel usage, reduces emissions, and contributes to cost savings for drivers. With its ability to precisely manage the fuel-air mixture, this system plays a vital role in making modern vehicles more environmentally friendly and economically viable. Understanding and appreciating such technological advancements can further emphasize the importance of continued research and development in the automotive industry.
Manual Transmission: The Secret to Better Fuel Economy
You may want to see also
Historical Context: Early engines used two valves for better control and reliability
The concept of using two fuel valves in internal combustion engines has its roots in the early days of automotive engineering, and it was a crucial innovation for the development of reliable and efficient engines. This design choice was a direct response to the challenges engineers faced in controlling the fuel-air mixture and ensuring optimal combustion.
In the late 19th and early 20th centuries, engine designers aimed to improve the performance and efficiency of internal combustion engines, which were the primary power source for early automobiles. One of the critical aspects of engine design was the valve mechanism, which controlled the intake and exhaust of air and fuel. Initially, engines used a single valve for both intake and exhaust, but this design had limitations. The single-valve system struggled to provide precise control over the fuel-air mixture, leading to inefficient combustion and reduced engine performance.
Engineers addressed this issue by introducing a more sophisticated valve configuration. The idea was to separate the intake and exhaust processes, allowing for better control over the fuel-air mixture. This led to the development of two valves: one for the intake (or induction) of air and fuel, and another for the exhaust of burned gases. By having two valves, engineers could fine-tune the engine's performance, ensuring that the fuel-air mixture was precisely controlled and that the combustion process was efficient and reliable.
This design change brought several advantages. Firstly, it allowed for better control over the engine's power output, making it more responsive and adaptable to different driving conditions. Secondly, the two-valve system improved the engine's overall reliability by reducing the likelihood of engine knock and misfires, which were common issues with earlier single-valve designs. The separation of intake and exhaust processes also contributed to better engine breathing, ensuring that the engine could breathe efficiently and maintain optimal performance.
The historical context of early engine design highlights the importance of innovation in valve technology. The transition from a single valve to two valves was a significant milestone, as it paved the way for more advanced engine architectures and improved the overall driving experience. This evolution in engine design continues to influence modern automotive engineering, where the pursuit of efficiency, control, and reliability remains a driving force for innovation.
Troubleshooting: Driving with a Fuel Pump Issue
You may want to see also
Frequently asked questions
The presence of two fuel valves, often referred to as a dual-fuel system, is a design choice made to optimize engine performance and efficiency. One valve is responsible for supplying fuel to the engine during idling and low-load conditions, ensuring a steady and controlled flow of fuel. The second valve is used for higher engine speeds and loads, allowing for a more precise and efficient fuel injection process. This dual-fuel system enables the engine to maintain optimal performance across various operating conditions.
The dual-fuel valve system offers several advantages. Firstly, it enhances engine responsiveness by providing a quick and accurate fuel supply during acceleration. The second valve can adjust the fuel-air mixture more precisely, allowing for better engine control and improved power output. Additionally, this design reduces the risk of engine misfires and promotes better fuel economy, as the engine can maintain optimal combustion even under varying loads.
While the dual-fuel valve setup offers numerous benefits, it can also introduce some complexities. The additional valve and associated plumbing can lead to increased manufacturing costs and potential maintenance challenges. In some cases, the system may require more frequent maintenance to ensure optimal performance. However, these drawbacks are often outweighed by the performance advantages and improved engine efficiency that a dual-fuel system provides.