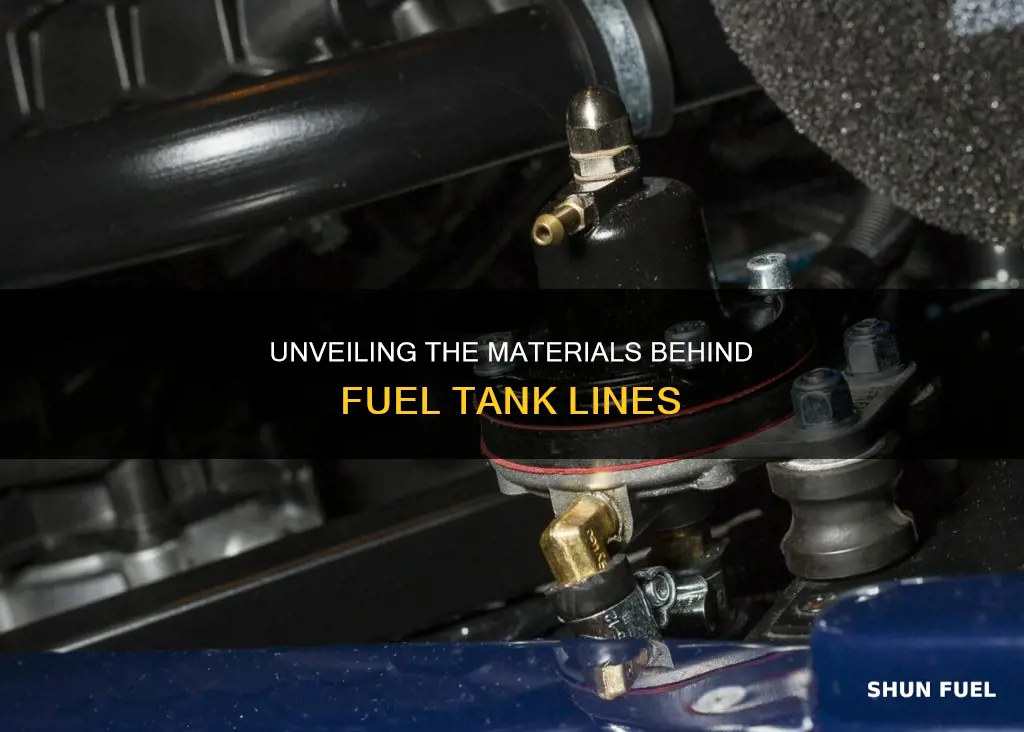
Fuel tank lines are an essential component of a vehicle's fuel system, responsible for transporting fuel from the tank to the engine. These lines are typically made from materials that are durable, flexible, and resistant to corrosion and fuel degradation. Common materials used for fuel tank lines include steel, aluminum, and various types of plastic, such as polyvinyl chloride (PVC) and high-density polyethylene (HDPE). The choice of material depends on factors such as the vehicle's operating conditions, fuel type, and cost considerations.
Characteristics | Values |
---|---|
Material | Typically made from steel, aluminum, or plastic (polyethylene or polypropylene). |
Purpose | To transport fuel from the fuel tank to the engine. |
Design | Often flexible to accommodate engine movement and vibrations. |
Construction | Can be solid or hollow, depending on the application and material. |
Strength | Designed to withstand pressure and temperature changes. |
Corrosion Resistance | Materials like aluminum and certain plastics are chosen for their ability to resist corrosion. |
Flexibility | Allows for easy installation and movement within the vehicle. |
Weight | Lightweight materials are preferred to reduce overall vehicle weight. |
Cost | Varies depending on the material and manufacturing process. |
Compatibility | Specific materials are chosen to ensure compatibility with the vehicle's fuel system. |
Regulatory Compliance | Some materials may need to meet industry standards for fuel system components. |
What You'll Learn
- Materials: Common materials include steel, aluminum, and plastic (like PVC or polypropylene)
- Strength: Tank lines are designed to withstand pressure and temperature changes
- Corrosion Resistance: Materials are chosen to prevent corrosion from fuel and environmental factors
- Flexibility: Some materials offer flexibility to accommodate vehicle movement and vibrations
- Cost: Different materials vary in cost, affecting the overall price of the fuel system
Materials: Common materials include steel, aluminum, and plastic (like PVC or polypropylene)
The materials used for fuel tank lines are carefully chosen to ensure durability, safety, and compatibility with the fuel they carry. Steel, aluminum, and various types of plastic are the most common choices for these components.
Steel: This is a robust and durable material, often used for its strength and resistance to corrosion. Steel fuel tank lines are commonly found in automotive applications, especially for high-performance vehicles or those with specific requirements for fuel containment. The material's ability to withstand pressure and temperature changes makes it ideal for long-term use. However, steel can be heavier and more rigid compared to other options, which might be a consideration for certain vehicle designs.
Aluminum: Lighter than steel, aluminum offers excellent corrosion resistance and a good balance of strength. It is often used in aviation and high-performance automotive applications where weight reduction is crucial. Aluminum fuel tank lines are known for their ability to maintain fuel quality by minimizing the risk of oxidation and contamination. This material is also highly malleable, allowing for easier installation and customization.
Plastic (PVC or Polypropylene): Plastic fuel tank lines are becoming increasingly popular due to their lightweight nature, flexibility, and cost-effectiveness. Polyvinyl chloride (PVC) and polypropylene (PP) are the most commonly used plastics in this application. PVC is known for its strength and chemical resistance, making it suitable for a wide range of fuels. Polypropylene, on the other hand, is lightweight and offers good impact resistance, which is beneficial for vehicles with limited space. These plastic materials are often used in situations where weight reduction is essential, such as in racing or recreational vehicles.
The choice of material depends on various factors, including the specific vehicle requirements, fuel type, and environmental conditions. Each material offers unique advantages, ensuring that fuel tank lines are not only functional but also reliable and safe for use.
Unveiling the Material Mystery: What Fuels Clear Fuel Lines?
You may want to see also
Strength: Tank lines are designed to withstand pressure and temperature changes
The fuel tank lines in vehicles are an essential component of the fuel system, responsible for transferring fuel from the tank to the engine. These lines are designed with a specific focus on strength and durability to handle the demanding conditions they encounter. One of the primary reasons for this emphasis on strength is the need to withstand pressure changes. Fuel tank lines are exposed to varying pressures as the vehicle accelerates, decelerates, and experiences changes in altitude. To ensure reliable performance, these lines are typically constructed from materials that can resist such pressure fluctuations without compromising structural integrity.
In addition to pressure resistance, temperature changes also play a significant role in the design of fuel tank lines. Fluctuations in temperature can cause materials to expand or contract, potentially leading to damage or leaks. To address this, engineers select materials that offer excellent thermal stability. Common choices include high-density polyethylene (HDPE) and polyvinyl chloride (PVC), both of which have proven their effectiveness in maintaining structural integrity across a wide temperature range.
The choice of material is crucial in achieving the required strength. For instance, HDPE is known for its exceptional impact resistance, making it ideal for fuel tank lines as it can absorb shocks and vibrations without breaking. PVC, on the other hand, is valued for its flexibility, which allows the lines to bend and move without cracking, even when subjected to extreme temperatures. These materials are often reinforced with additional layers or compounds to further enhance their strength and durability.
Furthermore, the design of the fuel tank lines themselves is optimized for strength. They are often constructed with a thick-walled design, providing a robust structure that can withstand the internal pressures of the fuel. The lines may also feature a braided or spiral design, which adds flexibility while maintaining structural integrity. This combination of material selection and design ensures that the fuel tank lines can handle the rigors of everyday use.
In summary, the strength of fuel tank lines is a critical aspect of their design, ensuring they can endure pressure and temperature changes without failure. By utilizing materials with superior properties and implementing thoughtful design choices, engineers create fuel tank lines that are both reliable and long-lasting, contributing to the overall performance and safety of the vehicle's fuel system.
Small Engine Fuel Line: Choosing the Right Option for Your Needs
You may want to see also
Corrosion Resistance: Materials are chosen to prevent corrosion from fuel and environmental factors
The choice of materials for fuel tank lines is crucial to ensure the longevity and reliability of a vehicle's fuel system. Corrosion resistance is a key consideration in this context, as it directly impacts the performance and safety of the vehicle. Fuel and environmental factors can cause corrosion, leading to potential issues such as fuel leaks, reduced engine performance, and even system failures. Therefore, selecting appropriate materials is essential to prevent these problems.
One common material used for fuel tank lines is stainless steel. This metal is highly resistant to corrosion due to its unique properties. Stainless steel contains a high percentage of chromium, which forms a protective oxide layer on its surface when exposed to oxygen. This layer acts as a barrier, preventing further corrosion and ensuring the material's durability. Additionally, stainless steel is known for its strength and flexibility, making it suitable for the demanding conditions of fuel tank lines.
Another material often employed is brass, an alloy of copper and zinc. Brass offers excellent corrosion resistance due to its natural resistance to oxidation. It is also lightweight, easy to install, and possesses good thermal conductivity, which helps in maintaining the fuel's temperature. However, brass may not be as strong as stainless steel, so it is often used in combination with other materials or in specific applications where its properties are advantageous.
For fuel tank lines, materials like aluminum and copper alloys are also considered. These materials provide good corrosion resistance and are lightweight, contributing to overall fuel efficiency. However, they may not be as flexible as stainless steel, which is crucial for the intricate routing of fuel lines within a vehicle.
In summary, the selection of materials for fuel tank lines is a critical aspect of vehicle engineering. Materials like stainless steel, brass, aluminum, and copper alloys are chosen for their inherent corrosion resistance, ensuring that fuel tank lines can withstand the harsh conditions of fuel and the environment. These materials contribute to the overall reliability and safety of the vehicle's fuel system.
Duromax Fuel Line Diameter: 2003 Model Specs Revealed
You may want to see also
Flexibility: Some materials offer flexibility to accommodate vehicle movement and vibrations
Flexibility is a crucial aspect of fuel tank lines, especially in the context of vehicle performance and longevity. The primary purpose of these lines is to facilitate the transfer of fuel from the tank to the engine while withstanding the various stresses and movements inherent in a vehicle's operation. This is where the choice of material becomes significant.
In the automotive industry, fuel tank lines are typically constructed from materials that offer a balance of strength and flexibility. Rubber, for instance, is a common choice due to its inherent elasticity. Natural rubber can deform slightly under pressure and return to its original shape, which is essential for absorbing vibrations and minimizing stress on the fuel system. This flexibility is particularly important in high-vibration environments, such as those experienced during acceleration, deceleration, and even on rough roads.
The flexibility of fuel tank lines made from rubber or similar elastic materials is designed to accommodate the natural movement of a vehicle's components. As the engine and fuel system expand and contract with temperature changes, the flexible lines ensure a consistent and secure connection, preventing potential leaks or damage. This is especially critical in older vehicles or those with less advanced fuel systems, where the materials used might not be as durable or flexible as modern alternatives.
Additionally, the flexibility of these lines contributes to the overall reliability of the fuel system. By allowing for some movement, the lines reduce the risk of cracking or breaking due to constant vibration and expansion. This is particularly important in high-performance vehicles or those with aggressive driving conditions, where the fuel system must endure more extreme stresses.
In summary, the flexibility of fuel tank lines is a critical design consideration, ensuring that the lines can withstand the dynamic nature of a vehicle's operation. Materials such as rubber provide the necessary elasticity to absorb vibrations and accommodate movement, contributing to the overall durability and performance of the fuel system. This aspect of material choice is often overlooked but plays a vital role in maintaining the integrity of the vehicle's fuel supply.
Engine's Strange Noises: When Fuel Line Issues Speak
You may want to see also
Cost: Different materials vary in cost, affecting the overall price of the fuel system
The cost of fuel tank lines is an important consideration when designing and installing a fuel system. The material chosen for these lines can significantly impact the overall price, and thus, the final cost of the vehicle. Different materials have varying costs, which can be influenced by factors such as availability, processing requirements, and market demand.
One of the most common materials used for fuel tank lines is steel. Steel is known for its durability and strength, making it a popular choice for automotive applications. However, steel can be more expensive compared to other materials due to its manufacturing process and the need for specialized welding techniques. The cost of steel fuel tank lines can vary depending on the grade and thickness required for the specific vehicle's specifications.
In contrast, plastic fuel tank lines are often more affordable. Materials like high-density polyethylene (HDPE) or polyvinyl chloride (PVC) are commonly used due to their lightweight nature and resistance to corrosion. These plastics are generally less expensive to produce and can be easily molded into the desired shape. The cost-effectiveness of plastic lines makes them a popular choice for cost-sensitive projects or when weight reduction is a priority.
Another factor to consider is the use of aluminum fuel tank lines. Aluminum offers excellent thermal conductivity, which can be beneficial for fuel systems in certain climates. While aluminum is more expensive than steel and plastic, its lightweight properties can contribute to improved fuel efficiency in vehicles. The cost of aluminum lines may be justified by the long-term benefits of reduced fuel consumption and enhanced performance.
Additionally, the cost of fuel tank lines can be influenced by the complexity of the design and the manufacturing process. Customized or intricate designs may require more expensive materials or specialized fabrication techniques, driving up the overall cost. It is essential to balance the desired performance and durability with the budget constraints to make an informed decision when selecting the material for fuel tank lines.
Understanding Fuel Injector Return Lines: A Comprehensive Guide
You may want to see also
Frequently asked questions
Fuel tank lines are typically made from materials such as steel, aluminum, or high-density polyethylene (HDPE). Steel is known for its strength and durability, making it a popular choice for heavy-duty applications. Aluminum offers lightweight properties and excellent corrosion resistance, while HDPE is a flexible and lightweight plastic often used in automotive applications due to its ease of installation and impact resistance.
The material choice is crucial as it directly impacts the performance, safety, and longevity of the fuel system. Materials like steel and aluminum provide structural integrity, ensuring the lines can withstand pressure and temperature changes without compromising fuel quality. HDPE, with its flexibility, is advantageous for easy routing and installation, especially in tight spaces.
Yes, each material has unique benefits. Steel fuel tank lines offer superior strength, making them ideal for high-pressure systems and off-road vehicles. Aluminum lines are lightweight, reducing the overall weight of the vehicle and improving fuel efficiency. HDPE's flexibility and impact resistance make it suitable for vehicles with limited space and those exposed to extreme temperatures.
Material selection influences maintenance and repair processes. Steel lines may require more rigorous welding techniques for repairs, while aluminum and HDPE lines can often be joined using simpler methods. The flexibility of HDPE can also make it easier to replace or repair without extensive disassembly, reducing downtime during maintenance or repairs.