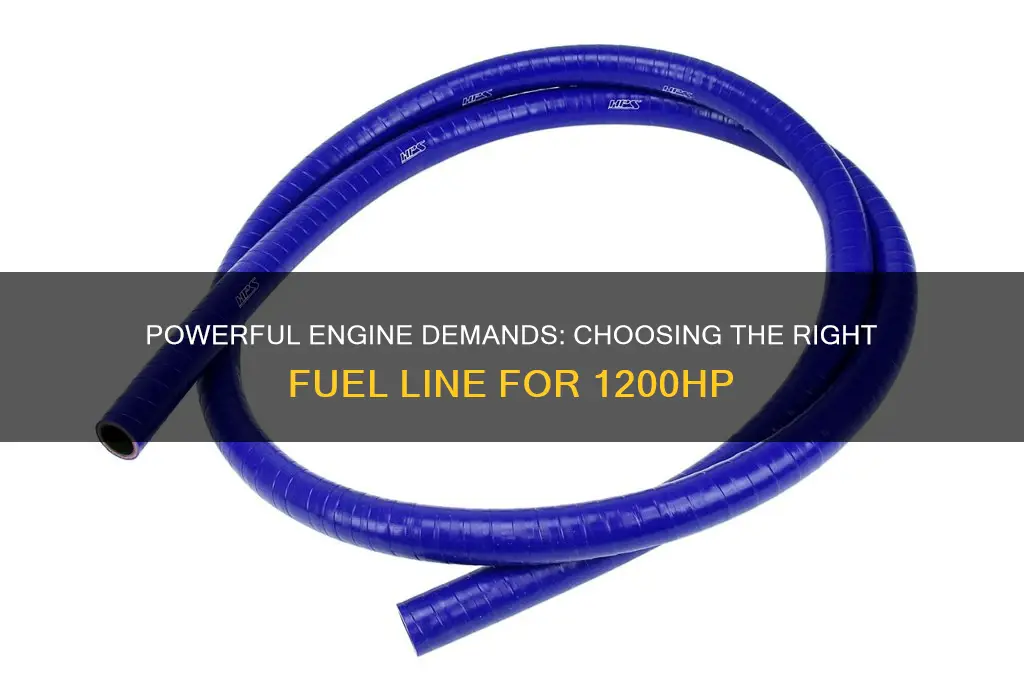
When it comes to high-performance engines, ensuring the right fuel line size is crucial for optimal performance and safety. For a 1200hp engine, the fuel line must be able to handle the high flow rates and pressure required to deliver fuel efficiently. The size of the fuel line is determined by factors such as engine displacement, fuel pump capacity, and desired performance levels. Choosing the correct fuel line size is essential to prevent fuel pressure drops, ensure consistent power delivery, and maintain engine reliability. This guide will provide insights into the recommended fuel line sizes for 1200hp engines, considering various engine configurations and performance goals.
Characteristics | Values |
---|---|
Fuel Line Diameter | 3/8" to 1/2" |
Pressure Rating | 10-15 psi (for high-performance engines) |
Material | High-strength steel or aluminum |
Length | Varies based on engine placement and configuration |
Flexibility | Required for engine movement and vibrations |
Compatibility | Ensure it fits the fuel pump and injectors |
Temperature Resistance | Able to withstand engine operating temperatures |
Flow Rate | Adequate to supply the required fuel volume |
Safety Factor | Typically 1.5 to 2 times the expected pressure |
What You'll Learn
- Engine Displacement: Larger engines require thicker fuel lines to handle higher flow rates
- Fuel Pressure: Higher pressure demands stronger, more flexible fuel lines
- Engine Location: Engine placement affects fuel line routing and required diameter
- Fuel Pump Location: Proximity to the fuel pump determines fuel line size
- Hose Material: Choose fuel line material based on temperature and pressure resistance
Engine Displacement: Larger engines require thicker fuel lines to handle higher flow rates
When it comes to high-performance engines, such as those producing 1200 horsepower, the choice of fuel line size is critical to ensure optimal performance and reliability. One of the key factors to consider is engine displacement, which directly impacts the flow rate of fuel required to power the engine. Larger engines, with higher displacement volumes, demand thicker fuel lines to handle the increased volume of fuel efficiently.
Engine displacement refers to the total volume of the engine's cylinders, and as this volume increases, so does the demand for fuel. A 1200hp engine will require a substantial amount of fuel to operate at its peak performance. Thicker fuel lines are essential to accommodate this higher flow rate, ensuring that the fuel can be delivered to the engine's intake efficiently without any loss or restriction. The increased thickness of the fuel line provides a larger diameter, allowing for a smoother and more rapid flow of fuel, which is crucial for maintaining the engine's power output.
In the context of engine performance, fuel lines act as the arteries that supply the engine's heart with the necessary sustenance. Just as larger arteries in the human body require more robust material to handle increased blood flow, larger engines need thicker fuel lines. This is especially important in high-performance applications where the engine operates at its maximum capacity, requiring a consistent and efficient fuel supply.
The choice of fuel line thickness should be based on the specific requirements of the engine. For a 1200hp engine, engineers and enthusiasts often opt for fuel lines with a diameter of 3/8 inches or larger. This size ensures that the fuel can flow freely, providing the engine with the necessary power and responsiveness. Thicker fuel lines also contribute to better heat dissipation, as they can handle higher temperatures without compromising performance.
In summary, when dealing with powerful engines like those producing 1200 horsepower, engine displacement plays a pivotal role in determining the appropriate fuel line size. Larger engines demand thicker fuel lines to manage the increased fuel flow rates, ensuring optimal performance and reliability. By selecting the right fuel line thickness, enthusiasts can guarantee that their high-performance engines receive the fuel they need to operate at their very best.
Choosing the Right Tubing for Your Fuel Line: A Comprehensive Guide
You may want to see also
Fuel Pressure: Higher pressure demands stronger, more flexible fuel lines
When dealing with high-performance engines, such as a 1200hp powerhouse, the fuel system becomes a critical component that can make or break your engine's performance and longevity. One often overlooked but crucial aspect is the fuel line, which plays a vital role in delivering fuel to the engine under high pressure.
As the name suggests, fuel pressure refers to the force at which fuel is supplied to the engine. In high-performance applications, fuel pressure is typically much higher than in standard vehicles. This increased pressure is necessary to ensure that the engine receives the precise amount of fuel required for optimal combustion, especially during high-load conditions. When the engine demands more power, it requires a higher volume of fuel, and this is where the fuel line's strength and flexibility come into play.
The primary function of a fuel line is to transmit fuel from the fuel pump to the engine's fuel injectors or carburetor. In high-pressure applications, the fuel line must be capable of withstanding this pressure without compromising its structural integrity. Standard fuel lines may not be able to handle the extreme forces, leading to potential issues like fuel leaks, reduced performance, or even engine damage. Therefore, it is essential to choose fuel lines specifically designed for high-pressure applications.
The key to selecting the right fuel line is to consider its diameter and material. For a 1200hp engine, a larger diameter fuel line is generally recommended to accommodate the higher fuel flow rates and pressure. A common rule of thumb is to use a fuel line with a diameter of at least 0.5 inches (12.7 mm) for such powerful engines. Additionally, the material should be flexible yet robust, often a high-quality rubber or synthetic compound that can withstand extreme temperatures and pressure.
In summary, when building or modifying a high-performance engine, paying attention to the fuel line's specifications is crucial. Higher fuel pressure demands a stronger, more flexible fuel line to ensure efficient and reliable fuel delivery. By investing in the right fuel line, you can optimize your engine's performance and ensure it runs smoothly, even under the most demanding conditions. Remember, the fuel system is a critical component, and choosing the right parts will pay dividends in the long run.
VXR Pro 93 Fuel Line: Dimensions and Specifications
You may want to see also
Engine Location: Engine placement affects fuel line routing and required diameter
When dealing with high-performance engines, such as a 1200hp setup, the engine's location and placement play a crucial role in determining the appropriate fuel line size. The engine's position directly influences the routing of the fuel lines and the overall system design. For a 1200hp engine, it is essential to consider the following factors:
Engine Compartment Layout: The physical layout of the engine compartment is a critical aspect. If the engine is mounted in a front-engine configuration, the fuel lines will need to run from the fuel tank, typically located in the rear, to the engine. This routing requires careful planning to ensure the lines are not too long, as excessive length can lead to fuel pressure drops and potential performance issues. On the other hand, a mid-engine or rear-engine layout may offer more flexibility in fuel line routing, allowing for shorter and more direct connections.
Fuel Pump and Line Placement: The placement of the fuel pump is vital. It should be positioned close to the engine to minimize the pressure drop in the fuel lines. For a 1200hp engine, a high-pressure fuel pump is often recommended to ensure efficient fuel delivery. The fuel pump's location will dictate the angle and direction of the fuel lines, affecting the required diameter. Longer lines may require larger diameters to maintain adequate fuel flow and pressure.
Engine Height and Accessibility: Engine height is another consideration. In some cases, the engine's height might limit the available space for fuel lines, especially if the fuel tank is located low. This constraint may necessitate the use of larger-diameter fuel lines to accommodate the necessary length and maintain optimal fuel delivery. Additionally, accessibility for maintenance and potential fuel line replacements should be considered when determining the engine's placement.
Fuel Line Diameter Calculation: Determining the appropriate fuel line diameter involves considering the engine's power output and the desired fuel flow rate. For a 1200hp engine, a larger diameter fuel line might be required to handle the increased fuel demand. The calculation often involves factors such as engine displacement, desired fuel pressure, and the specific fuel requirements of the engine. Consulting manufacturer guidelines or seeking expert advice is essential to ensure the correct diameter is chosen.
In summary, the engine's location significantly impacts fuel line routing and diameter selection. Proper engine placement ensures efficient fuel delivery, considering factors like fuel pump location, line length, and accessibility. By carefully evaluating these aspects, enthusiasts can optimize the fuel system for a 1200hp engine, ensuring reliable performance and addressing potential challenges associated with high-power applications.
Engine's Strange Noises: When Fuel Line Issues Speak
You may want to see also
Fuel Pump Location: Proximity to the fuel pump determines fuel line size
When it comes to fuel systems in high-performance engines, such as those producing 1200 horsepower, the location of the fuel pump is a critical factor in determining the appropriate fuel line size. The proximity of the fuel pump to the engine's fuel requirements plays a significant role in ensuring optimal performance and reliability.
The fuel pump's primary function is to deliver fuel at the required pressure to the engine's injectors or carburetor. When the pump is located close to the engine, it can provide a more direct and efficient supply of fuel. This proximity reduces the length of the fuel line, minimizing potential pressure losses due to the line's resistance. As a result, a shorter fuel line ensures that the fuel reaches the engine at the desired pressure, allowing for precise fuel injection and improved power output.
In contrast, if the fuel pump is positioned farther away from the engine, the fuel line becomes longer, and several challenges arise. Longer fuel lines can lead to increased pressure drop, especially at higher flow rates. This pressure loss may result in reduced fuel pressure at the engine, affecting performance and potentially causing fuel starvation during high-load conditions. To compensate for this, larger-diameter fuel lines might be required to maintain the necessary pressure, but this can introduce other issues, such as increased fuel line weight and potential flexing under acceleration.
To optimize the fuel system, it is recommended to place the fuel pump as close as possible to the engine's fuel requirements. This proximity ensures that the fuel line is of an appropriate length, minimizing pressure losses and maintaining the required fuel pressure. Additionally, considering the pump's capacity and flow rate is essential to match it with the engine's demands, further enhancing the overall performance and reliability of the fuel system.
In summary, the location of the fuel pump significantly impacts the choice of fuel line size for a 1200hp engine. Proximity to the fuel requirements ensures efficient fuel delivery, reduces pressure losses, and promotes optimal engine performance. Proper placement of the fuel pump, along with considering the pump's specifications, is crucial for achieving the desired power output and maintaining the fuel system's integrity.
Ford Focus 2001 Fuel Line Breakdown: Essential Components Explained
You may want to see also
Hose Material: Choose fuel line material based on temperature and pressure resistance
When it comes to fuel lines for high-performance engines, such as those producing 1200 horsepower, the choice of hose material is critical to ensure optimal performance and safety. The fuel line's primary function is to transport fuel efficiently while withstanding the extreme conditions generated by the engine's power output. Therefore, selecting the right material is essential to avoid potential issues like fuel leaks, reduced performance, or even system failure.
The temperature and pressure resistance of the fuel line material are key considerations. High-performance engines generate significant heat, and the fuel line must be able to handle these elevated temperatures without compromising its structural integrity. For instance, rubber hoses are commonly used but may not be suitable for such demanding applications due to their limited temperature range. In contrast, materials like synthetic rubber compounds, such as neoprene or EPDM (ethylene propylene diene monomer), offer improved temperature resistance, making them ideal for high-hp engines. These compounds can withstand temperatures up to 250°F, ensuring the fuel line remains flexible and durable.
Additionally, the pressure resistance of the fuel line material is vital. High-performance engines operate at elevated pressures, and the fuel line must be designed to handle these forces without failure. Materials like nylon or braided steel hoses are often preferred for their superior pressure-bearing capabilities. Nylon hoses, for example, provide excellent flexibility and can withstand pressures up to 250 psi, making them a reliable choice for high-hp applications. Braided steel hoses, on the other hand, offer even higher pressure resistance, ensuring a secure and reliable fuel supply under extreme conditions.
Another factor to consider is the chemical resistance of the hose material. Fuel lines must be compatible with the type of fuel being used, whether it's gasoline, diesel, or a specialized racing fuel. Different fuels have varying compositions and properties, and the hose material should not react with or degrade the fuel over time. For instance, some hoses may be more resistant to ethanol-blended fuels, which are commonly used in high-performance applications, ensuring the fuel line's longevity and performance.
In summary, when selecting fuel line material for a 1200hp engine, it is crucial to prioritize temperature and pressure resistance. Materials like synthetic rubber compounds, nylon, and braided steel hoses offer the necessary durability and flexibility to handle the extreme conditions of high-performance engines. Additionally, considering the chemical compatibility of the hose material with the fuel being used will ensure a reliable and long-lasting fuel supply system.
Ultimate Guide: Best Fuel Line Material for Maximum Performance
You may want to see also
Frequently asked questions
For a 1200hp engine, a fuel line with a diameter of 1/2 inch (0.5 inches) is generally recommended. This size ensures efficient fuel delivery to meet the high power output, providing a smooth and reliable operation.
It is not advisable to use a smaller fuel line, as it may restrict fuel flow, leading to performance issues and potential engine damage. The 0.5-inch diameter is the minimum recommended size to handle the fuel requirements of a 1200hp engine.
Longer fuel lines can introduce additional resistance, which may impact fuel pressure and flow rate. For a 1200hp engine, keeping the fuel line length to a minimum is ideal to ensure optimal performance and fuel efficiency.
Yes, high-performance fuel lines are often made from materials like stainless steel or high-strength rubber compounds. These materials offer better flexibility, durability, and resistance to heat and fuel degradation, making them ideal for high-hp applications.
Engine misfires, reduced power, poor fuel efficiency, and rough idling are common indicators of a clogged or restricted fuel line. Regular maintenance and fuel line inspections are essential to prevent such issues, especially in high-performance engines.