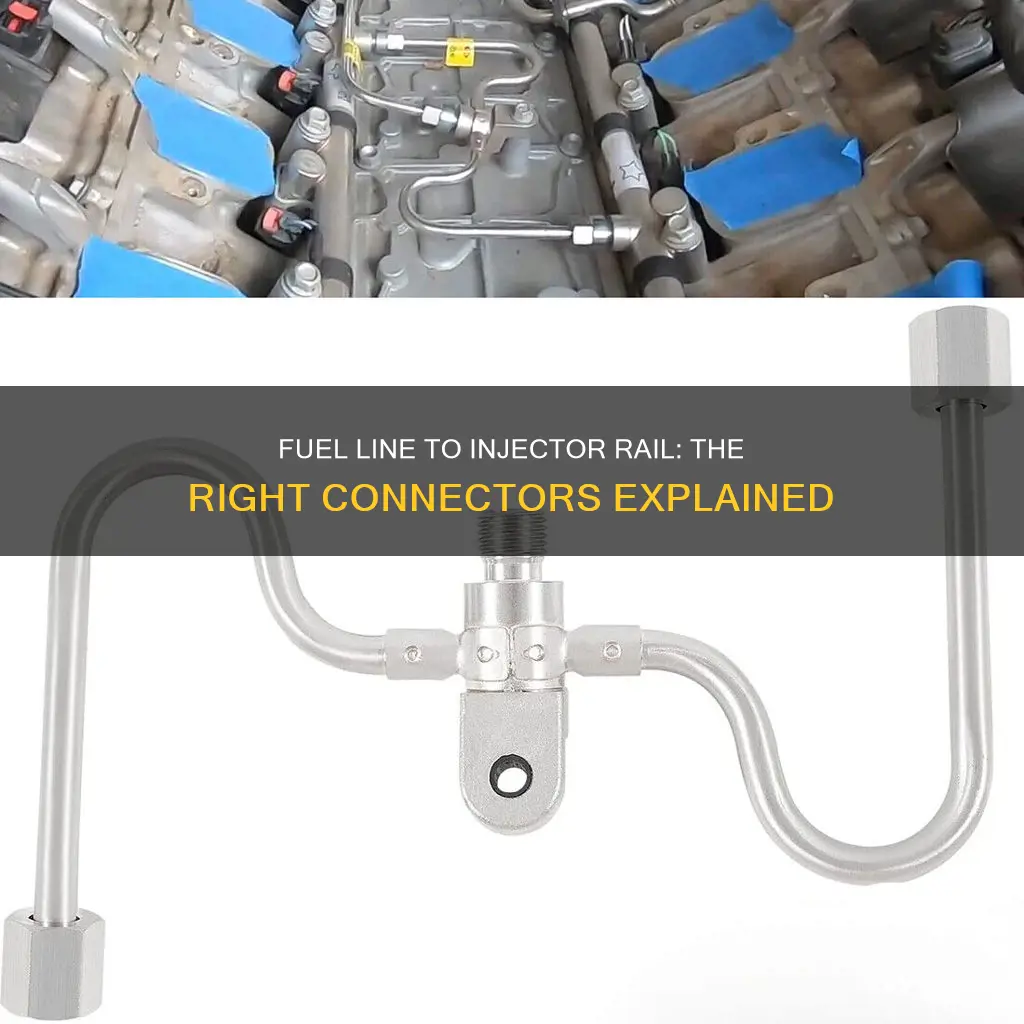
When it comes to connecting the fuel line to the injector rail, various types of connectors are used depending on the vehicle's make and model. These connectors play a crucial role in ensuring a secure and reliable fuel supply to the engine's injectors. Common types of connectors include quick-connect fittings, which are often used for their ease of installation and removal, and specialized fuel rail connectors designed to withstand high pressure and temperature. Understanding the specific connector type required for your vehicle is essential for proper maintenance and troubleshooting.
What You'll Learn
- Fuel Line Material: Connectors are made from materials like steel, brass, or aluminum, chosen for durability and compatibility
- Fitting Types: Common fittings include quick-connect, threaded, and clamp-style, each with unique installation methods
- Pressure Ratings: Connectors must withstand fuel pressure, with ratings varying based on engine type and fuel system design
- Sealing Mechanisms: Gaskets, O-rings, or proprietary seals ensure a tight connection, preventing fuel leaks and engine damage
- Compatibility: Connectors must match the fuel line diameter, thread size, and fuel rail interface for proper installation and performance
Fuel Line Material: Connectors are made from materials like steel, brass, or aluminum, chosen for durability and compatibility
When it comes to connecting fuel lines to the injector rail, the choice of connector material is crucial for ensuring optimal performance and longevity. The connectors play a vital role in maintaining a secure and reliable fuel supply to the engine, especially in high-pressure environments. Here's an overview of the materials commonly used for these connectors:
Steel Connectors:
Steel is a popular choice for fuel line connectors due to its exceptional strength and durability. It offers excellent resistance to corrosion and can withstand the demanding conditions of an engine bay. Steel connectors are often used in high-performance vehicles or applications where extreme temperatures and pressures are present. These connectors provide a robust and reliable connection, ensuring that the fuel lines remain secure even under intense operating conditions.
Brass Connectors:
Brass, an alloy of copper and zinc, is another common material for fuel line connectors. It offers a balance of strength and flexibility, making it highly suitable for this application. Brass connectors are known for their ability to resist corrosion and provide a smooth, non-reactive surface, which is essential for maintaining fuel quality. This material is often preferred for its ease of installation and the ability to form a tight seal, ensuring a leak-free connection.
Aluminum Connectors:
Aluminum connectors are lightweight and offer excellent thermal conductivity, making them ideal for high-performance engines. This material is chosen for its ability to dissipate heat quickly, which can be beneficial in preventing fuel line overheating. Aluminum connectors are often used in racing or high-output applications where weight reduction and heat management are critical factors. Despite its lightweight nature, aluminum provides sufficient strength to handle the fuel pressure and ensure a secure connection.
The choice of connector material depends on various factors, including the specific engine requirements, environmental conditions, and performance expectations. Manufacturers carefully select these materials to ensure compatibility and longevity, ensuring that the fuel system operates efficiently and reliably. Properly designed connectors made from these materials contribute to the overall performance and longevity of the fuel injection system.
Polaris Ranger 570 Fuel Line Fittings: A Comprehensive Guide
You may want to see also
Fitting Types: Common fittings include quick-connect, threaded, and clamp-style, each with unique installation methods
When it comes to connecting the fuel line to the injector rail, several types of connectors are commonly used, each with its own unique installation process. These fittings ensure a secure and reliable connection, allowing for efficient fuel delivery to the engine. Here's an overview of the three primary fitting types:
Quick-Connect Fittings:
These fittings are designed for a fast and easy installation process. Quick-connect fittings typically feature a male end with a threaded or bayonet-style connector, which is inserted into a female port on the injector rail. The key advantage is the ability to quickly attach and detach the fuel line without the need for tools. A simple push-on action is usually sufficient to create a tight seal. This type of fitting is popular in applications where frequent fueling changes are required, such as in racing or mobile fuel systems.
Threaded Fittings:
Threaded connectors are a more traditional approach to connecting fuel lines. These fittings consist of a male or female thread, which must be carefully aligned and screwed onto the corresponding port on the injector rail. The process requires precise threading and sealing to ensure a leak-free connection. Threaded fittings are often used in applications where a more permanent and secure connection is desired. They provide excellent reliability and are commonly found in automotive fuel systems. When installing, it's crucial to use the correct thread pitch and ensure a tight seal with a gasket or sealing compound.
Clamp-Style Fittings:
As the name suggests, clamp-style fittings secure the fuel line using a clamp mechanism. This type of fitting typically has a male connector with a threaded or barbed end, which is inserted into the female port on the injector rail. Once connected, a clamp is tightened around the fuel line and fitting, creating a secure hold. Clamp-style fittings are known for their simplicity and ease of installation. They are often used in applications where accessibility and a quick installation process are essential. It's important to ensure that the clamp is tightened evenly to avoid damaging the fuel line or creating a weak connection.
Each of these fitting types offers a distinct advantage, catering to various fuel system requirements. The choice of fitting depends on factors such as the application's specific needs, the level of accessibility required, and the desired installation speed. Understanding the unique installation methods of each fitting type is essential for ensuring a proper and secure connection between the fuel line and injector rail.
Understanding Fuel Line Seals: A Comprehensive Guide
You may want to see also
Pressure Ratings: Connectors must withstand fuel pressure, with ratings varying based on engine type and fuel system design
When it comes to connecting fuel lines to the injector rail, the choice of connector is crucial, especially when considering the pressure ratings required to ensure a reliable and safe fuel system. The pressure within a fuel system can vary significantly depending on the engine type and its specific fuel system design. For instance, high-performance engines with turbochargers or superchargers often operate at much higher fuel pressures compared to naturally aspirated engines.
The pressure ratings of connectors are typically specified in terms of the maximum pressure they can withstand without failing or leaking. These ratings are essential because they determine the connector's ability to handle the fuel pressure at the injector rail. If a connector is not rated for the specific pressure in the fuel system, it may fail, leading to potential fuel leaks, reduced engine performance, or even dangerous situations like fuel fires.
Engineers and designers must carefully select connectors that meet or exceed the required pressure ratings for the particular engine and fuel system in question. This involves considering the engine's power output, the type of fuel used, and the overall design of the fuel injection system. For example, a connector used in a high-pressure direct injection system for a racing car will have different pressure requirements compared to a fuel line connector in a low-pressure, carbureted motorcycle engine.
In addition to pressure ratings, other factors such as temperature, vibration, and chemical resistance should also be considered when choosing connectors. Some fuels, especially those with higher alcohol content, can be more corrosive and may require connectors with specific materials to withstand these challenges. Proper connector selection ensures that the fuel system operates efficiently and safely, contributing to the overall performance and reliability of the vehicle.
In summary, the pressure ratings of connectors are a critical aspect of connecting fuel lines to injector rails. Engineers must carefully evaluate the specific requirements of the engine and fuel system to select connectors that can withstand the anticipated fuel pressures. This attention to detail is essential for maintaining the integrity of the fuel system and ensuring the safe operation of the vehicle.
Understanding Ford's Fuel Line Valve: A Comprehensive Guide
You may want to see also
Sealing Mechanisms: Gaskets, O-rings, or proprietary seals ensure a tight connection, preventing fuel leaks and engine damage
When it comes to connecting the fuel line to the injector rail, ensuring a secure and leak-free connection is crucial for optimal engine performance and reliability. This is where sealing mechanisms play a vital role, utilizing various components to create a tight seal and prevent any unwanted fuel leaks.
One common sealing mechanism is the use of gaskets. Gaskets are typically made of materials like rubber or silicone and are designed to create a flexible seal between two surfaces. In the context of fuel lines and injector rails, gaskets can be used to seal the connection points, ensuring that fuel is directed correctly and preventing any potential leaks. These gaskets are often made with a specific shape and size to fit the unique contours of the fuel line and injector rail, providing a reliable seal.
O-rings are another type of sealing component commonly employed in fuel system connections. O-rings are circular seals with a cross-sectional shape resembling a 'O'. They are inserted into grooves or channels to create a tight seal. The flexibility of O-rings allows them to adapt to slight variations in the connection, ensuring a secure fit. This design makes O-rings ideal for fuel line connectors, as they can accommodate any minor misalignments while maintaining a tight seal, thus preventing fuel from escaping.
In some cases, manufacturers may use proprietary seals, which are custom-designed seals that are specific to their fuel injection systems. These seals are tailored to the exact dimensions and requirements of the fuel line and injector rail connection. Proprietary seals often incorporate advanced sealing materials and designs, ensuring a superior level of tightness and leak prevention. They may include unique features like multiple sealing points or specialized sealing compounds to enhance their performance.
The choice of sealing mechanism depends on various factors, including the specific engine design, fuel pressure, and environmental conditions. Gaskets, O-rings, and proprietary seals all serve the critical function of maintaining a secure connection between the fuel line and injector rail. By utilizing these sealing mechanisms, engineers can ensure that fuel is delivered efficiently and safely, minimizing the risk of engine damage caused by fuel leaks. Proper installation and regular inspection of these seals are essential to maintain the overall health and longevity of the fuel injection system.
Understanding Fuel Pickup Lines for Outboard Motors: A Comprehensive Guide
You may want to see also
Compatibility: Connectors must match the fuel line diameter, thread size, and fuel rail interface for proper installation and performance
When it comes to connecting the fuel line to the injector rail, compatibility is key. The connectors used must be designed to match the specific dimensions and requirements of the fuel line and fuel rail interface. This ensures a secure and reliable connection, allowing for efficient fuel delivery to the injectors.
One crucial aspect of compatibility is the fuel line diameter. Different fuel lines have varying diameters, and the connectors need to accommodate these sizes. For example, a fuel line with a 3/8-inch inner diameter requires a connector with a corresponding 3/8-inch port. Using a connector with an incompatible diameter can result in a poor seal, leading to fuel leaks and potential engine performance issues.
Thread size is another critical factor. Fuel lines often feature specific thread sizes, such as 1/4-20 or 5/16-24. The connectors must match these thread sizes precisely. Mismatched threads can lead to difficult installation, reduced sealing, and potential fuel loss. It is essential to refer to the manufacturer's specifications or consult technical resources to identify the correct thread size for your application.
Additionally, the fuel rail interface plays a significant role in connector compatibility. The injector rail may have unique mounting holes, fittings, or ports that the connector must align with. These interfaces ensure that the fuel line is positioned correctly and securely attached to the rail. Using a connector that does not match the fuel rail interface can result in an improper installation, leading to fuel delivery issues and potential engine damage.
To ensure proper installation and performance, it is recommended to consult the vehicle's service manual or seek guidance from automotive experts. They can provide specific information regarding the fuel line and injector rail compatibility for your particular make and model. By choosing the correct connectors that match the fuel line diameter, thread size, and fuel rail interface, you can guarantee a reliable fuel delivery system, optimizing engine performance and longevity.
Clogged Fuel Return Line: Engine Performance and Safety Risks
You may want to see also
Frequently asked questions
The connectors used for this purpose are usually specialized fuel rail connectors, often made of durable materials like aluminum or brass. These connectors are designed to securely attach the fuel line to the injector rail, ensuring a tight seal to prevent fuel leaks.
Yes, it is crucial to use connectors that are compatible with the specific fuel rail and engine system. Different engine manufacturers may have unique connector designs or requirements, so it's essential to consult the vehicle's manual or seek professional advice to ensure the correct connectors are used.
These connectors play a vital role in maintaining the integrity of the fuel flow. They provide a reliable connection point, allowing for precise fuel delivery to the injectors. Properly connected fuel lines ensure that the fuel is delivered at the correct pressure and quantity, optimizing engine performance and efficiency.
While it is possible to replace fuel rail connectors yourself, it is recommended to have professional experience or guidance. Fuel system work can be complex, and improper installation may lead to fuel leaks or engine performance issues. It is always a good idea to consult a qualified mechanic or refer to detailed repair manuals before attempting any fuel system modifications.