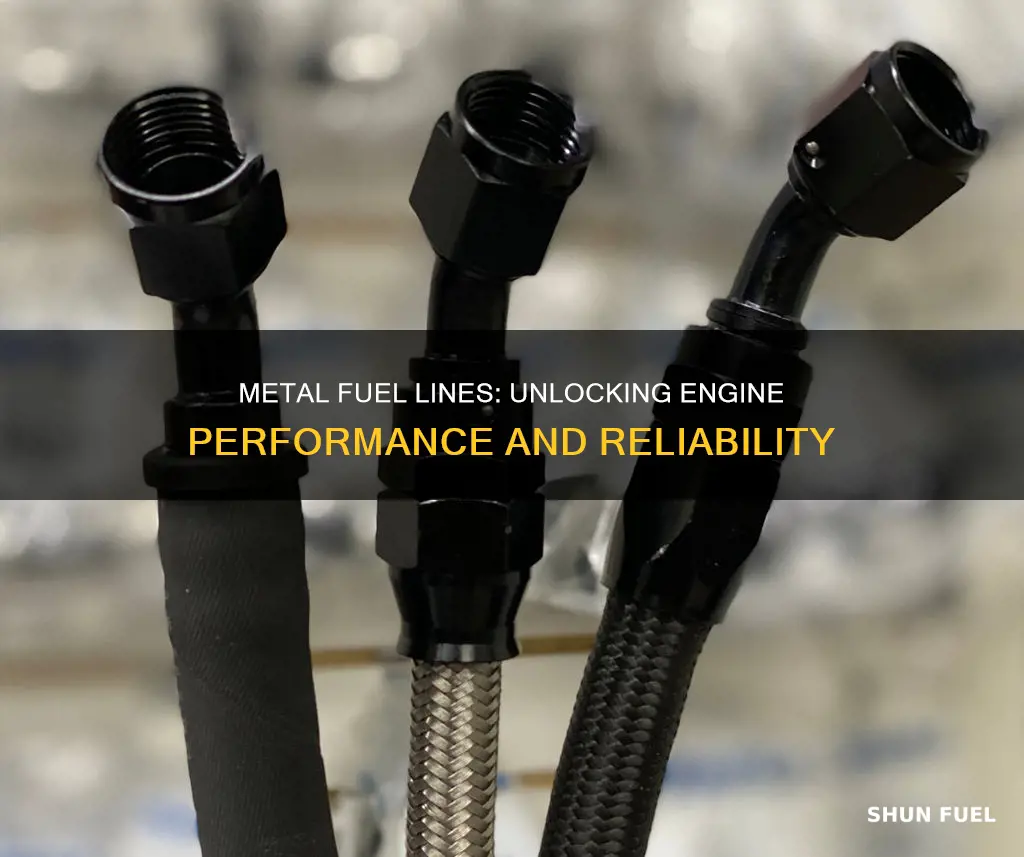
Metal fuel lines, often made from materials like steel or aluminum, offer several advantages over their rubber or plastic counterparts. One significant pro is their superior durability and resistance to heat. Metal fuel lines can withstand extreme temperatures, making them ideal for high-performance vehicles or those operating in harsh environments. This durability reduces the risk of fuel leaks, which can be a critical safety concern, especially in high-speed or high-load applications. Additionally, metal lines are less susceptible to corrosion, ensuring a longer lifespan and maintaining the integrity of the fuel system over time.
Characteristics | Values |
---|---|
Durability | Metal fuel lines are highly durable and can withstand high pressure and temperature, making them less prone to leaks and damage compared to rubber or plastic lines. |
Corrosion Resistance | They are resistant to corrosion, ensuring the fuel remains pure and free from contaminants, which is crucial for engine performance and longevity. |
Flexibility | Despite their strength, metal lines can still offer flexibility, allowing for easy installation and accommodating engine movement without cracking or breaking. |
Longevity | With proper maintenance, metal fuel lines can last much longer than their rubber or plastic counterparts, reducing the need for frequent replacements. |
Compatibility | They are often compatible with a wide range of fuels, including gasoline, diesel, and even ethanol blends, making them versatile for various vehicle types. |
Safety | The use of metal lines can enhance safety by reducing the risk of fuel leaks and potential fires, especially in high-performance or modified vehicles. |
Cost-Effective | In the long run, metal fuel lines can be more cost-effective due to their durability and longevity, as they may require fewer replacements over time. |
What You'll Learn
- Durability: Metal fuel lines are highly durable, resistant to corrosion, and can withstand high temperatures and pressure
- Longevity: These lines have a longer lifespan compared to rubber, reducing replacement costs and maintenance
- Corrosion Resistance: Metal lines prevent fuel contamination and ensure a clean fuel supply, vital for engine performance
- Flexibility: Despite being rigid, they offer some flexibility, accommodating engine movement without cracking or leaking
- Safety: Metal fuel lines are less prone to puncturing or leaking, enhancing overall vehicle safety
Durability: Metal fuel lines are highly durable, resistant to corrosion, and can withstand high temperatures and pressure
Metal fuel lines offer a significant advantage in terms of durability, making them an excellent choice for vehicles that require reliable and long-lasting performance. One of the key benefits is their exceptional resistance to corrosion, which is a common issue with fuel lines made from other materials. Over time, fuel lines can deteriorate due to exposure to fuel, moisture, and environmental factors, leading to leaks and potential engine damage. However, metal fuel lines are designed to combat this problem. The metallic composition creates a protective barrier, preventing corrosion and ensuring that the fuel lines remain intact and functional for an extended period. This is particularly crucial in high-temperature environments or areas with harsh weather conditions, where other materials might fail prematurely.
The durability of metal fuel lines is further enhanced by their ability to withstand high temperatures and pressure. Fuel systems operate under varying thermal conditions, and metal lines are engineered to handle these extremes without compromising their structural integrity. They can resist heat generated by the engine and the fuel itself, ensuring that the fuel remains stable and does not degrade. Additionally, metal fuel lines are built to endure the pressure fluctuations that occur during acceleration and deceleration, providing a consistent and reliable fuel supply to the engine. This level of durability is essential for maintaining optimal engine performance and longevity.
In high-performance vehicles or those used in demanding conditions, the reliability of fuel lines becomes even more critical. Metal fuel lines provide peace of mind, knowing that the fuel delivery system is robust and less prone to failure. This is especially important in racing or off-road applications where fuel lines must handle rapid changes in speed and environmental conditions. The durability of metal lines ensures that the engine receives the necessary fuel without interruptions, contributing to improved performance and efficiency.
Furthermore, the long-term cost-effectiveness of metal fuel lines is a significant advantage. While the initial investment might be higher compared to other materials, the durability and longevity of metal lines result in fewer replacements and repairs over time. This is a crucial consideration for vehicle owners, as it reduces maintenance expenses and ensures a more reliable fuel system. The resistance to corrosion and ability to withstand extreme conditions make metal fuel lines a wise choice for those seeking a robust and durable solution for their fuel delivery needs.
In summary, the durability of metal fuel lines is a compelling reason to choose this material for fuel delivery systems. Their resistance to corrosion and ability to handle high temperatures and pressure make them an ideal component for vehicles requiring reliable performance. By investing in metal fuel lines, vehicle owners can ensure a longer-lasting and more efficient fuel system, ultimately contributing to a smoother and more satisfying driving experience.
Outboard Motor Fuel Line: To Disconnect or Not to Disconnect?
You may want to see also
Longevity: These lines have a longer lifespan compared to rubber, reducing replacement costs and maintenance
Metal fuel lines offer a significant advantage in terms of longevity, which is a crucial factor for vehicle owners and enthusiasts. One of the primary benefits of metal fuel lines is their exceptional durability. Unlike rubber fuel lines, which can degrade over time due to exposure to fuel, heat, and vibration, metal lines are highly resistant to these elements. This resistance ensures that the fuel lines remain intact and functional for an extended period, often outlasting the vehicle itself.
The longevity of metal fuel lines is attributed to their robust construction. These lines are typically made from high-quality materials such as stainless steel or aluminum, both of which possess excellent corrosion resistance. This corrosion resistance prevents the lines from deteriorating when exposed to fuel, which often contains corrosive elements. As a result, metal fuel lines can withstand the harsh conditions within the engine bay, ensuring a reliable and safe fuel supply to the engine.
The durability of metal fuel lines translates into reduced maintenance and replacement costs. Rubber fuel lines may need to be replaced more frequently due to wear and tear, especially in high-performance or modified vehicles. In contrast, metal lines can last for the entire lifespan of the vehicle without showing signs of degradation. This longevity means that vehicle owners can avoid the inconvenience and expense of frequent replacements, saving money in the long run.
Furthermore, the extended lifespan of metal fuel lines contributes to overall vehicle reliability. With metal lines, there is a reduced risk of fuel leaks, which can be dangerous and costly to repair. The consistent performance of metal lines ensures that the fuel system operates efficiently, providing the engine with the necessary fuel for optimal performance. This reliability is particularly important for vehicles that rely on a consistent and efficient fuel supply, such as high-performance cars or those used in racing.
In summary, the longevity of metal fuel lines is a significant advantage, offering a more durable and cost-effective solution compared to rubber lines. The resistance to corrosion and fuel degradation ensures that metal lines remain functional for an extended period, reducing replacement costs and maintenance. This feature is especially beneficial for vehicle owners who prioritize reliability and long-term savings in their automotive choices.
Unleash Engine Power: Understanding Fuel Line Cleaner's Magic
You may want to see also
Corrosion Resistance: Metal lines prevent fuel contamination and ensure a clean fuel supply, vital for engine performance
Metal fuel lines offer a significant advantage in terms of corrosion resistance, which is a critical factor in maintaining a clean and efficient fuel supply for engines. The primary benefit lies in the inherent properties of metal materials, which inherently resist corrosion and oxidation. This is particularly important in the context of fuel lines, as they are exposed to various corrosive elements within the fuel system.
Corrosion can lead to a multitude of issues, including fuel contamination, reduced engine performance, and even potential engine damage. When fuel lines are made of metal, the risk of corrosion is minimized. Metal lines, such as those made from stainless steel or aluminum alloys, form a protective layer on their surface, often referred to as a 'passivation layer'. This layer acts as a barrier, preventing corrosive substances in the fuel, such as water, acids, and fuel additives, from coming into direct contact with the metal. As a result, the metal fuel lines remain stable and do not deteriorate over time.
The resistance to corrosion is further enhanced by the fact that metal lines can withstand high temperatures and pressure fluctuations, which are common in engine operations. Unlike plastic or rubber fuel lines that may degrade or become brittle over time, metal lines maintain their structural integrity and continue to provide a reliable fuel supply. This is especially crucial in high-performance engines or vehicles operating in harsh environments where fuel quality and consistency are essential.
In addition, metal fuel lines contribute to a clean fuel supply. As they resist corrosion, they also prevent the leaching of metal particles into the fuel. This is vital because even small amounts of metal contamination can lead to engine misfires, reduced power, and increased wear and tear. By maintaining a pure fuel supply, metal lines ensure that the engine operates optimally, delivering the best possible performance.
In summary, the corrosion resistance of metal fuel lines is a key advantage in ensuring a clean and reliable fuel supply. It prevents contamination, maintains engine performance, and provides long-lasting reliability, making it an essential consideration for vehicle owners and enthusiasts who value optimal engine operation.
The Strange Sound of Frozen Fuel Lines: A Guide
You may want to see also
Flexibility: Despite being rigid, they offer some flexibility, accommodating engine movement without cracking or leaking
Metal fuel lines, often made from materials like steel or aluminum, have a unique advantage when it comes to flexibility, which is an essential aspect of their design and functionality. While it might seem counterintuitive that rigid metal lines can offer flexibility, this characteristic is a significant benefit in the automotive world.
The flexibility of metal fuel lines is a result of their construction and material properties. These lines are designed with a certain degree of give, allowing them to bend and move with the engine's natural vibrations and movements. This flexibility is crucial in preventing cracks and leaks, which could lead to fuel loss and potential engine issues. When an engine operates, it experiences various stresses and strains, and the fuel lines must be able to adapt to these movements without compromising their structural integrity.
The key to this flexibility lies in the material's ability to withstand deformation without permanent damage. Metal fuel lines are typically made from high-strength alloys, ensuring they can absorb the engine's kinetic energy and return to their original shape. This elasticity is particularly important in high-performance vehicles or those with advanced engine designs, where the engine's movement can be more pronounced.
In contrast to rubber or plastic fuel lines, which may become brittle over time, metal lines maintain their flexibility even in extreme temperatures. This is because metal does not degrade or become soft under heat or cold, ensuring that the fuel lines remain effective and reliable in various environmental conditions. As a result, metal fuel lines provide a consistent level of flexibility, accommodating engine movement without the risk of cracking or leaking, which could lead to costly repairs and potential safety hazards.
Furthermore, the flexibility of metal fuel lines contributes to the overall longevity of the vehicle. By preventing cracks and leaks, these lines ensure that the fuel supply remains stable, reducing the chances of engine misfires or performance issues. This reliability is especially valuable for vehicles that operate in demanding conditions or those that require precise fuel delivery for optimal performance.
Understanding the Role of AV in Fuel Lines
You may want to see also
Safety: Metal fuel lines are less prone to puncturing or leaking, enhancing overall vehicle safety
Metal fuel lines offer a significant advantage in terms of safety, primarily due to their inherent durability and resistance to damage. Unlike their rubber or plastic counterparts, metal fuel lines are less susceptible to puncturing or leaking, which can have severe consequences in a vehicle's engine bay.
The engine compartment is a harsh environment, with potential hazards such as road debris, sharp edges, and even the impact of small animals or insects. Rubber or plastic fuel lines, while flexible, can be easily damaged by these elements. A small puncture or crack can lead to fuel leaks, which not only pose a fire hazard but also release harmful pollutants into the atmosphere. Metal fuel lines, however, are much stronger and more resilient. They can withstand the rigors of the road and the potential impacts without compromising their structural integrity.
The construction of metal fuel lines involves a series of precise processes to ensure their strength and reliability. These lines are typically made from high-quality steel or aluminum alloys, which are then carefully formed and welded to create a seamless and robust structure. The manufacturing process ensures that the fuel lines are free from any weaknesses or vulnerabilities that could lead to leaks or punctures. This level of durability is particularly important in high-performance vehicles or those used in extreme conditions, where the risk of damage is higher.
In the event of a collision or impact, metal fuel lines provide an added layer of protection. Their rigid structure helps to absorb and distribute the force, reducing the likelihood of damage. This is especially crucial in front-impact collisions, where the engine and fuel system are vulnerable to severe damage. By using metal fuel lines, the risk of fuel leaks and subsequent fires is significantly minimized, ensuring the safety of both the vehicle and its occupants.
Furthermore, the longevity of metal fuel lines contributes to overall vehicle safety. These lines are designed to last for the lifetime of the vehicle, providing consistent performance and reliability. Unlike rubber or plastic lines that may degrade over time, metal lines remain robust and effective, reducing the chances of unexpected failures. This long-term durability is a key factor in maintaining a safe and efficient fuel system, especially in older vehicles where the risk of fuel-related issues is higher.
Quick Fix: Temporary Solutions for Leaky Fuel Lines
You may want to see also
Frequently asked questions
Metal fuel lines, typically made from materials like stainless steel or aluminum, offer several benefits. Firstly, they are highly durable and resistant to corrosion, ensuring a longer lifespan compared to rubber or plastic lines. This durability is especially advantageous in harsh environments or for vehicles with high mileage, as it reduces the risk of fuel leaks and potential engine damage. Additionally, metal fuel lines can withstand higher pressure levels, making them suitable for high-performance vehicles or those with larger engines.
The use of metal fuel lines can positively impact engine performance. These lines provide a more direct and efficient fuel delivery system, minimizing fuel pressure drop and ensuring a consistent fuel supply to the engine. This can result in improved engine response, better acceleration, and potentially higher horsepower output. Metal lines also offer a more rigid structure, reducing the chances of fuel line flexing or movement under engine vibration, which can lead to better overall engine operation.
While metal fuel lines are durable, regular maintenance is still essential. Over time, metal lines can develop small cracks or leaks, especially if exposed to extreme temperatures or physical damage. It is recommended to inspect the fuel lines periodically for any signs of wear or damage, especially during routine engine maintenance checks. In the event of a leak, it is crucial to replace the affected metal line promptly to prevent fuel loss and potential engine issues. Proper maintenance ensures the long-term reliability and safety of the fuel system.