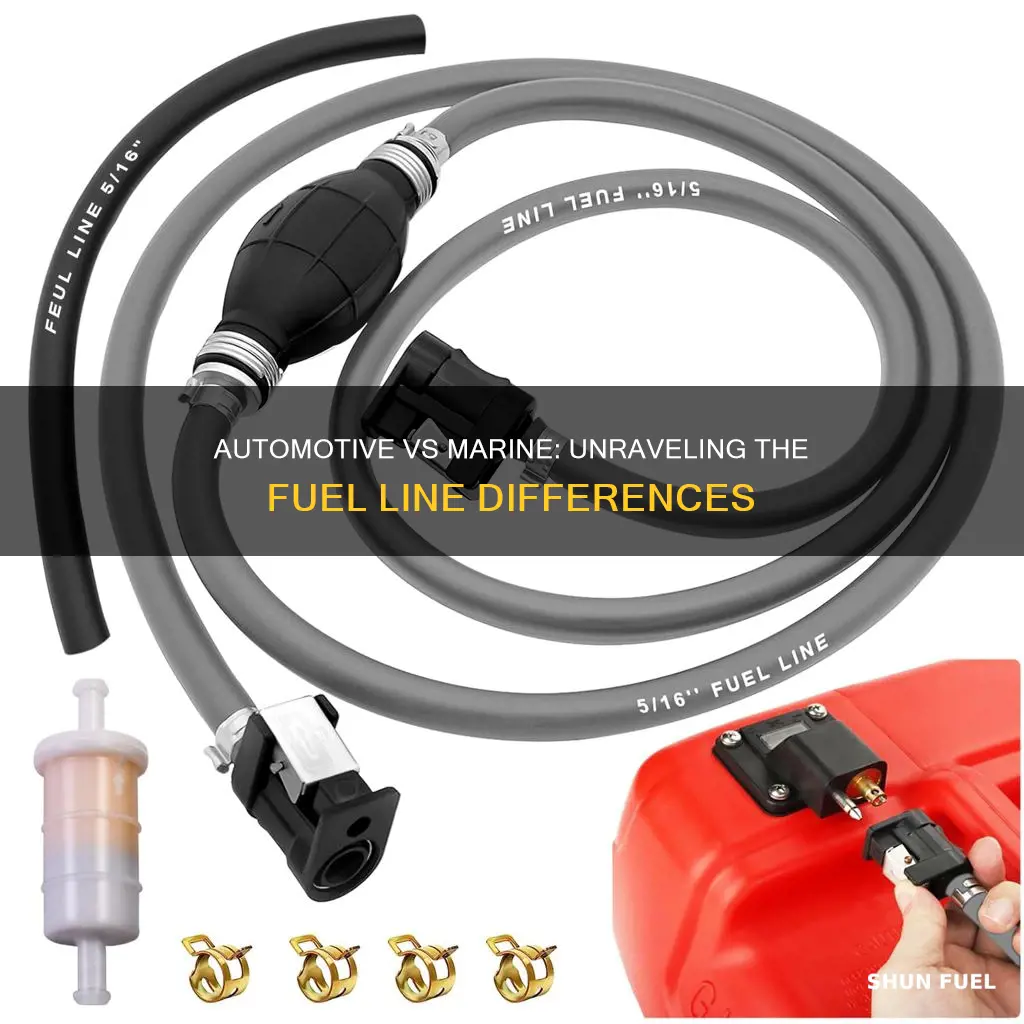
Automotive and marine fuel lines are both essential components in the fuel delivery systems of vehicles and boats, but they differ significantly in their design, construction, and performance. Automotive fuel lines are typically made from flexible materials like rubber or plastic and are designed to withstand the vibrations and temperature fluctuations experienced in a vehicle's engine compartment. They are often shorter and more compact to fit within the limited space available. In contrast, marine fuel lines are generally constructed from more robust materials such as high-density polyethylene or stainless steel to handle the harsh marine environment, including exposure to saltwater and UV radiation. Marine fuel lines are often longer and more flexible to accommodate the movement of the boat and are designed to resist corrosion and degradation over time. Understanding these differences is crucial for ensuring the proper functioning and longevity of fuel systems in both automotive and marine applications.
Characteristics | Values |
---|---|
Material | Automotive fuel lines are typically made from rubber or synthetic rubber compounds, while marine-grade fuel lines often use a combination of rubber and braided stainless steel for added strength and corrosion resistance. |
Flexibility | Automotive lines are designed for flexibility to accommodate engine movement and vibrations, whereas marine-grade lines are more rigid to withstand the harsh marine environment and potential impact from waves. |
Temperature Resistance | Marine-grade fuel lines are often rated for higher temperature ranges, especially in applications with extended sun exposure, whereas automotive lines may have lower temperature limits. |
Pressure Rating | Marine-grade fuel lines can handle higher pressure due to the potential for larger fuel tanks and higher engine power, while automotive lines are designed for standard engine pressure. |
Corrosion Resistance | Marine-grade fuel lines are treated with anti-corrosion materials to prevent fuel degradation, which is a critical factor in marine environments. Automotive lines may not require the same level of corrosion protection. |
Connectors and Fittings | Marine-grade fuel lines often feature specialized connectors and fittings designed for the marine environment, including UV-resistant materials and sealed connections. |
Color and Visibility | Automotive lines are usually black or dark-colored, while marine-grade lines may be bright colors like red or blue for better visibility in the water. |
Cost | Marine-grade fuel lines can be more expensive due to the use of specialized materials and construction, while automotive lines are generally more affordable. |
Application | Automotive fuel lines are used in cars, trucks, and motorcycles, while marine-grade lines are designed for boats, yachts, and other watercraft. |
What You'll Learn
- Material: Automotive lines use rubber or PVC, while marine lines often use braids or stainless steel for durability
- Design: Automotive lines are typically straight, while marine lines may have bends and curves to fit vessel layouts
- Pressure Rating: Marine lines handle higher pressures due to engine demands, requiring stronger materials
- Flexibility: Automotive lines need to withstand temperature changes, while marine lines must resist saltwater corrosion
- Installation: Automotive lines are easier to install, whereas marine lines require specialized fittings and secure mounting
Material: Automotive lines use rubber or PVC, while marine lines often use braids or stainless steel for durability
When it comes to fuel lines, the choice of material is crucial, especially in the context of automotive and marine applications. Automotive fuel lines are typically made from rubber or PVC (polyvinyl chloride). These materials are chosen for their flexibility, which is essential for accommodating the various movements and vibrations experienced in a vehicle's engine bay. Rubber is known for its excellent resistance to heat and chemicals, making it a reliable choice for fuel lines that need to withstand the corrosive nature of gasoline and diesel. PVC, on the other hand, offers a more cost-effective alternative while still providing decent durability and flexibility.
In contrast, marine fuel lines often utilize different materials to meet the unique demands of marine environments. Braided stainless steel is a popular choice for these applications. Stainless steel is renowned for its exceptional strength and corrosion resistance, making it ideal for withstanding the harsh conditions of saltwater and the constant movement of a boat. The braiding technique used in manufacturing these lines provides flexibility, allowing them to navigate around the engine and other components without compromising on structural integrity. This combination of flexibility and strength ensures that marine fuel lines can handle the unique challenges posed by the marine environment.
The choice of material is critical to the performance and longevity of fuel lines. Automotive rubber or PVC lines are suitable for most everyday driving conditions, providing a balance between cost and durability. However, for marine applications, the use of braided stainless steel becomes essential to ensure that the fuel lines can withstand the corrosive effects of saltwater, UV radiation, and the physical demands of a constantly moving vessel.
Additionally, the design and construction of these fuel lines play a significant role in their performance. Automotive lines are often designed with a single layer or a few layers of rubber or PVC, which provides adequate protection against fuel leaks and engine heat. Marine lines, due to their exposure to saltwater and potential impact from waves, may feature thicker braids or multiple layers of stainless steel to enhance their protective capabilities.
In summary, the material used in automotive and marine fuel lines is a critical factor in their performance and suitability for specific environments. Automotive lines rely on rubber or PVC for flexibility and chemical resistance, while marine applications benefit from the strength and corrosion resistance of braided stainless steel. Understanding these material differences is essential for ensuring the reliability and longevity of fuel systems in various settings.
Understanding Impulse Fuel Lines: Powering Chainsaws Efficiently
You may want to see also
Design: Automotive lines are typically straight, while marine lines may have bends and curves to fit vessel layouts
Automotive and marine fuel lines serve distinct purposes and are designed with specific requirements in mind, which often translates into their physical attributes, particularly in terms of design. One of the most noticeable differences is the straightness of the lines. Automotive fuel lines are generally designed to be straight and rigid. This is because vehicles have a fixed structure, and the fuel lines need to run along the frame and body in a linear fashion to ensure efficient and safe fuel delivery to the engine. Straight lines also make it easier to inspect and maintain the system, as any issues can be more easily identified and addressed.
In contrast, marine fuel lines often feature a more dynamic design. Marine vessels, such as boats and ships, have a more complex and flexible layout due to their size and the various components they need to accommodate. As a result, marine fuel lines are often curved and bent to fit the vessel's structure. This design choice allows the lines to navigate around obstacles, such as bulkheads, engines, and other equipment, while still ensuring a secure and efficient fuel supply. The bends and curves in marine lines are carefully engineered to maintain the integrity of the fuel system, even when the vessel is in motion or subjected to external forces.
The design difference is crucial for the overall functionality and safety of the fuel system. Automotive lines, with their straight and rigid nature, are designed to minimize the risk of fuel leaks and ensure a consistent fuel flow. Straight lines also make it easier to install and replace the lines if needed. On the other hand, the curved and flexible design of marine lines allows for better adaptability to the vessel's environment, reducing the risk of damage from movement or impact. This flexibility is essential for the long-term reliability of the fuel system in marine applications.
Additionally, the materials used in these fuel lines can vary. Automotive lines often utilize materials like steel or high-pressure plastic to withstand the demands of the engine and road conditions. Marine lines, due to the harsher environment and potential exposure to saltwater, may require more corrosion-resistant materials, such as stainless steel or specialized polymers.
In summary, the design of automotive and marine fuel lines is a critical aspect of their functionality and performance. Automotive lines prioritize straightness and rigidity for efficient fuel delivery, while marine lines embrace bends and curves to adapt to the unique layout of vessels. These design choices, along with material considerations, ensure that each type of fuel line meets the specific needs of its respective application, contributing to the overall safety and reliability of the fuel system.
Unveiling the 1967 Ford LTD's Fuel Line Route
You may want to see also
Pressure Rating: Marine lines handle higher pressures due to engine demands, requiring stronger materials
When it comes to fuel lines, the difference between automotive and marine-grade lines is crucial, especially when considering the pressure ratings. Marine fuel lines are designed to withstand the higher pressures that marine engines often encounter, which can vary significantly from those in automotive applications. This is primarily due to the unique demands and operating conditions of marine engines.
Marine engines, especially those on larger vessels, generate substantial power and often operate at higher RPMs (revolutions per minute). This results in increased fuel pressure within the system, which can range from 100 to 200 psi or even higher in some cases. In contrast, automotive engines typically operate at much lower pressures, usually around 50 to 100 psi, depending on the vehicle's make and model. The higher pressure in marine applications is a critical factor in the design and material selection of fuel lines.
To handle these elevated pressures, marine-grade fuel lines are constructed with stronger and more robust materials. The inner diameter of these lines is often smaller, which helps to maintain the required pressure. The walls of marine fuel lines are thicker, providing better structural integrity and the ability to withstand the forces exerted by high-pressure fuel. This construction ensures that the fuel lines can remain flexible yet strong, preventing any potential damage or leaks under extreme conditions.
The materials used in marine fuel lines are carefully chosen to be resistant to corrosion and degradation, as they are exposed to harsh marine environments. Common materials include high-density polyethylene (HDPE) and various types of rubber compounds that offer excellent flexibility and durability. These materials are specifically selected to handle the unique challenges posed by the marine environment, including exposure to saltwater, UV radiation, and temperature fluctuations.
In summary, the pressure rating is a critical aspect that distinguishes automotive from marine-grade fuel lines. Marine lines are engineered to handle the higher pressures associated with marine engines, which require stronger materials and a more robust design. This ensures the safe and efficient operation of fuel systems in marine environments, where the demands on the fuel lines are significantly more challenging than those in typical automotive settings. Understanding these differences is essential for selecting the appropriate fuel lines for specific applications.
Houston Fuel Lines: Uncovering Hidden Issues and Solutions
You may want to see also
Flexibility: Automotive lines need to withstand temperature changes, while marine lines must resist saltwater corrosion
The primary distinction between automotive and marine-grade fuel lines lies in their design and material composition, which are tailored to the specific demands of their respective environments. One of the most significant differences is their flexibility, which is crucial for their performance and longevity.
Automotive fuel lines are designed to withstand the wide range of temperatures encountered in a vehicle's operating environment. This includes exposure to extreme heat during summer months and freezing temperatures in winter. To achieve this, automotive fuel lines are typically made from materials like nylon or PVC, which offer excellent flexibility and the ability to maintain their shape even under varying temperatures. This flexibility is essential to accommodate the expansion and contraction of the fuel lines without compromising their structural integrity.
In contrast, marine-grade fuel lines face a unique set of challenges. They must resist the corrosive effects of saltwater, which is a significant concern in marine environments. To combat this, marine fuel lines are often constructed with materials such as stainless steel or special-grade nylon, which provide superior resistance to corrosion. These materials are chosen for their ability to withstand the harsh conditions of saltwater exposure, ensuring the fuel lines remain intact and functional over extended periods.
The flexibility of marine fuel lines is also important, but it serves a different purpose. Marine lines need to be flexible to navigate the intricate routing within a vessel's fuel system, often involving tight bends and turns. This flexibility ensures that the fuel lines can be installed efficiently and maintain their functionality without being damaged by the vessel's movement or structural elements.
In summary, the flexibility of automotive and marine fuel lines is a critical aspect of their design, but it serves distinct purposes. Automotive lines prioritize temperature resistance, ensuring they can handle the extreme conditions of a vehicle's environment. Marine lines, on the other hand, focus on corrosion resistance to combat the unique challenges posed by saltwater exposure, while also maintaining flexibility to navigate the complex fuel systems of vessels.
Kawasaki Engine Fuel Line Diameter: A Comprehensive Guide
You may want to see also
Installation: Automotive lines are easier to install, whereas marine lines require specialized fittings and secure mounting
When it comes to fuel lines, the choice between automotive and marine-grade options can significantly impact the installation process. Automotive fuel lines are designed with simplicity and ease of use in mind, making them a popular choice for vehicle owners. These lines are typically made from flexible materials such as rubber or PVC, which allow for a straightforward installation process. The fittings and connectors used for automotive fuel lines are standardized and widely available, ensuring that installation can be completed without specialized tools or knowledge. This simplicity in design makes automotive fuel lines a convenient option for DIY enthusiasts and professional mechanics alike.
In contrast, marine-grade fuel lines present a more complex installation scenario. Marine environments demand higher standards of reliability and durability, which translates to more intricate fuel line designs. Marine-grade fuel lines often feature specialized fittings and connectors that are engineered to withstand the harsh conditions of marine applications. These fittings may include stainless steel brackets, heavy-duty clamps, or even custom-made adapters to ensure a secure and leak-free connection. The installation process for marine fuel lines requires a higher level of precision and attention to detail, as improper fitting can lead to fuel leaks or system failures.
The complexity of marine fuel line installation is primarily due to the need for secure mounting and protection against corrosion. Marine environments expose fuel lines to saltwater, which can cause rapid deterioration of materials over time. As a result, marine-grade fuel lines are often constructed with corrosion-resistant materials, such as stainless steel or high-density polyethylene (HDPE). The mounting process may involve using specialized brackets or clamps that provide additional support and protection against movement or damage.
For automotive fuel lines, installation is generally a straightforward process. The lines can be easily routed through the engine bay and connected to the fuel pump and injectors using standard fittings. The flexibility of the material allows for easy bending and manipulation, making it simple to navigate around various engine components. Additionally, automotive fuel lines often feature quick-connect fittings, which further simplify the installation process and reduce the risk of errors.
In summary, the installation process for automotive and marine-grade fuel lines differs significantly due to the varying design considerations and environmental demands. Automotive fuel lines prioritize ease of installation and use standardized fittings, making them accessible to a wide range of users. On the other hand, marine-grade fuel lines require specialized fittings and secure mounting to ensure reliability and longevity in harsh marine environments. Understanding these installation differences is crucial for vehicle owners and marine enthusiasts to make informed decisions when selecting and installing fuel lines for their specific applications.
Safe and Effective Methods to Thaw Frozen Car Fuel Lines
You may want to see also
Frequently asked questions
The main distinction lies in the materials used and the design specifications. Automotive fuel lines are typically made from rubber or flexible plastic compounds, designed to withstand the vibrations and temperature fluctuations common in cars. In contrast, marine-grade fuel lines are constructed with more robust materials like high-density polyethylene (HDPE) or stainless steel, ensuring they can handle the harsh marine environment, including exposure to saltwater and varying weather conditions.
While automotive fuel lines might work temporarily, they are not ideal for long-term use in marine settings. Marine environments demand materials that resist corrosion and degradation, which is why dedicated marine-grade fuel lines are preferred. Automotive lines may crack or deteriorate over time when exposed to saltwater and UV radiation.
Marine-grade fuel lines often feature a braided design, using stainless steel braids to reinforce the fuel-carrying tube. This construction provides excellent flexibility while maintaining structural integrity. In contrast, automotive fuel lines usually have a simpler construction with less emphasis on braiding, making them more cost-effective but less durable in harsh conditions.
Using automotive fuel lines in a marine setting is not recommended. Marine applications require materials that can withstand the corrosive effects of saltwater and the dynamic nature of boating. Automotive lines may not meet these standards and could lead to fuel leaks or system failures over time.
Marine-grade fuel lines offer superior durability, resistance to corrosion, and the ability to withstand extreme temperatures and environmental conditions. They are designed to provide a reliable and safe fuel supply for marine vehicles, ensuring optimal performance and longevity of the fuel system.