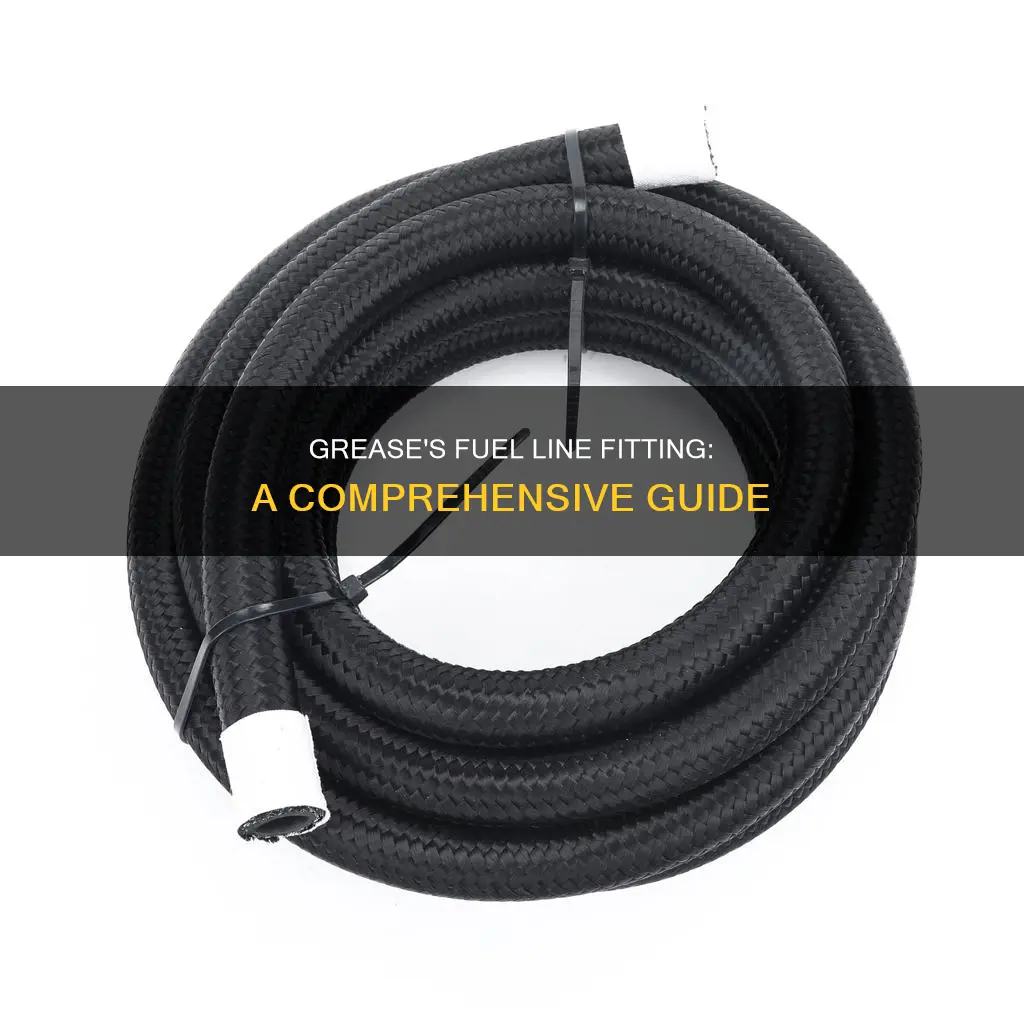
Grease plays a crucial role in fuel line fittings, ensuring optimal performance and longevity. It serves as a protective barrier, preventing fuel leaks and corrosion while maintaining flexibility and durability. This introduction aims to explore the specific applications and benefits of using grease in fuel line fittings, highlighting its importance in maintaining the integrity of fuel systems.
What You'll Learn
- Material Compatibility: Grease types compatible with fuel line materials (rubber, plastic) to prevent damage
- Temperature Tolerance: Grease that performs well in fuel line temperatures (-40°F to 250°F)
- Viscosity: Choosing the right grease viscosity for smooth operation and leak prevention
- Corrosion Resistance: Grease that protects against corrosion in fuel lines exposed to moisture
- Application Techniques: Methods for applying grease to fuel line fittings for optimal performance
Material Compatibility: Grease types compatible with fuel line materials (rubber, plastic) to prevent damage
When it comes to fuel line fittings, the choice of grease is crucial to ensure optimal performance and longevity of the system. The compatibility of the grease with the materials used in fuel lines, such as rubber and plastic, is essential to prevent damage and potential system failures. Here's an overview of the key considerations:
Rubber Fuel Lines: Rubber is a common material for fuel lines due to its flexibility and durability. However, it is sensitive to certain types of grease. The ideal grease for rubber fuel lines should be non-corrosive and have a high degree of stability. Silicone-based greases are often recommended as they provide excellent lubrication without compromising the integrity of the rubber. These greases are resistant to heat and chemicals, ensuring that the fuel lines remain protected against potential damage from the fuel itself. Additionally, look for greases that are specifically designed for automotive applications, as they are formulated to withstand the unique challenges of the fuel system.
Plastic Fuel Lines: Plastic fuel lines are lightweight and offer good resistance to corrosion. However, they can be more susceptible to damage from certain greases. It is crucial to choose a grease that is compatible with the specific type of plastic used. For instance, polyetherimide (PEI) or polyphenylene sulfide (PPS) plastics require greases that are non-reactive and do not promote degradation. Grease with a low-temperature flexibility is essential to accommodate the expansion and contraction of plastic materials without causing cracks or leaks. Again, automotive-specific greases are ideal, as they are engineered to meet the rigorous demands of fuel systems.
In both cases, the goal is to select a grease that provides long-lasting lubrication while maintaining the structural integrity of the fuel lines. Incompatible greases can lead to accelerated wear, cracking, or even failure of the fuel lines, resulting in potential engine damage. Therefore, it is essential to consult manufacturer guidelines or seek expert advice to ensure the right grease is used for the specific fuel line materials.
Furthermore, regular maintenance and inspection of fuel lines are recommended to identify any signs of grease degradation or fuel contamination. This proactive approach will help prevent unexpected failures and ensure the overall reliability of the fuel system. By understanding the compatibility of different greases with fuel line materials, vehicle owners and mechanics can make informed decisions to optimize the performance and longevity of their fuel systems.
Honda CR-V '98 Fuel Line Cut-Off: Causes and Fixes
You may want to see also
Temperature Tolerance: Grease that performs well in fuel line temperatures (-40°F to 250°F)
When it comes to fuel line fittings, the choice of grease is crucial to ensure optimal performance and longevity. The temperature range in fuel lines can vary significantly, from extremely cold environments to high-temperature conditions, making it essential to select a grease that can withstand these diverse temperature extremes.
For fuel line fittings, a grease with excellent temperature tolerance is ideal. This type of grease should remain stable and functional across a wide thermal spectrum, from as low as -40°F to a maximum of 250°F. Such a grease will not only maintain its consistency but also provide effective lubrication and protection against wear and tear, even in the harshest conditions.
The key to achieving this is to look for greases that contain specific additives and base oils. These additives can include extreme pressure agents, anti-wear compounds, and antioxidants, which collectively enhance the grease's ability to resist thermal degradation. Base oils, such as synthetic esters or polyalkylene glycols, offer better stability and viscosity control over a wide temperature range.
In the context of fuel lines, a grease with these characteristics will ensure that the fittings remain lubricated and protected, even when exposed to extreme cold or high temperatures. This is particularly important in applications where fuel lines are subject to rapid temperature fluctuations, such as in aircraft or high-performance vehicles.
Furthermore, the grease should also exhibit good resistance to fuel-related chemicals, ensuring that it does not break down or become ineffective over time. This combination of temperature tolerance and chemical stability is essential for the long-term reliability of fuel line fittings.
Fuel Line Flaring: A Double-Edged Decision
You may want to see also
Viscosity: Choosing the right grease viscosity for smooth operation and leak prevention
When it comes to fuel line fittings, the choice of grease is crucial for ensuring optimal performance and longevity. One of the most critical factors to consider is viscosity, which plays a pivotal role in maintaining smooth operation and preventing leaks. Grease viscosity refers to its resistance to flow and is typically measured in grades such as ISO (International Standard Organization) viscosity grades or the more commonly used SAE (Society of Automotive Engineers) grades. These grades indicate the grease's consistency and its ability to withstand various operating conditions.
For fuel line fittings, the ideal grease viscosity is often a balance between providing sufficient lubrication to reduce friction and ensuring that the grease remains stable under high-temperature and pressure conditions. Too little viscosity might lead to inadequate lubrication, causing excessive wear and potential leaks. On the other hand, excessive viscosity can hinder the movement of components, leading to increased friction and potential damage over time.
The choice of grease viscosity depends on several factors, including the operating temperature range, the speed of the machinery, and the specific requirements of the fuel system. For high-temperature applications, a lower viscosity grease is generally preferred to ensure easy flow and prevent thickening. This is especially important in fuel lines, where heat can cause grease to become more fluid, making it less effective. In contrast, for low-temperature environments, a higher viscosity grease is recommended to maintain its consistency and prevent leakage.
In the context of fuel line fittings, a common practice is to use a grease with a viscosity grade of around 700 to 1000 on the ISO scale or a similar grade on the SAE scale. This range provides a good balance, ensuring the grease remains stable under various conditions while still offering adequate lubrication. However, it's essential to consult the manufacturer's specifications and guidelines for the specific fuel system in question.
Additionally, considering the operating environment and potential exposure to contaminants is vital. In dirty or dusty conditions, a thicker grease might be necessary to provide better protection against wear and tear. Conversely, in clean environments, a thinner grease could be more suitable to minimize the risk of attracting and retaining contaminants. Ultimately, the goal is to select a grease viscosity that ensures smooth operation, reduces friction, and provides reliable leak prevention, contributing to the overall efficiency and longevity of the fuel line system.
Sugar's Sweet Secret: Uncovering Its Impact on Fuel Lines
You may want to see also
Corrosion Resistance: Grease that protects against corrosion in fuel lines exposed to moisture
When it comes to fuel line fittings, the choice of grease is crucial to ensure optimal performance and longevity. One of the primary concerns in these applications is corrosion, especially when fuel lines are exposed to moisture. Corrosion can lead to various issues, including reduced fuel flow, engine performance degradation, and even system failures. To combat this, specialized greases are formulated to provide excellent corrosion resistance, ensuring the protection of fuel lines and the overall integrity of the fuel system.
The key to achieving corrosion resistance lies in the composition of the grease. These greases typically contain a combination of base oils and additives that create a protective barrier on the metal surfaces of the fuel lines. One common additive is a corrosion inhibitor, which works by forming a stable film that prevents the metal from coming into direct contact with moisture and oxygen. This film acts as a shield, inhibiting the electrochemical reactions that cause corrosion.
In the context of fuel lines, where moisture is often present due to condensation or fuel vaporization, the right grease becomes even more critical. Moisture can accelerate corrosion processes, leading to the formation of rust and oxide layers on the metal surfaces. By applying a corrosion-resistant grease, you create a barrier that not only prevents moisture absorption but also helps to neutralize any existing corrosive elements. This ensures that the fuel lines remain in optimal condition, maintaining the efficiency and reliability of the fuel supply.
The benefits of using corrosion-resistant grease in fuel line fittings are numerous. Firstly, it extends the lifespan of the fuel lines by preventing premature degradation. This is particularly important in harsh environments or when using fuels with varying moisture content. Secondly, it reduces the risk of fuel contamination, as corrosion can lead to the leaching of metal particles into the fuel, affecting its quality and performance. Lastly, it minimizes the chances of fuel leaks, which can be costly and dangerous, especially in high-pressure fuel systems.
In summary, when dealing with fuel line fittings, selecting a grease with superior corrosion resistance is essential. This ensures that the fuel lines remain protected, even in moist environments, thereby maintaining the overall health and efficiency of the fuel system. With the right grease application, you can safeguard against potential issues caused by corrosion, ensuring a reliable and safe fuel supply for various applications.
Craftsman Chainsaw Fuel Line Sizes: A Comprehensive Guide
You may want to see also
Application Techniques: Methods for applying grease to fuel line fittings for optimal performance
When it comes to applying grease to fuel line fittings, there are several techniques that can ensure optimal performance and longevity. The goal is to create a protective layer that reduces friction and corrosion while maintaining flexibility. Here are some detailed methods to achieve this:
- Brush Application: This is a straightforward and effective method. Take a high-quality grease specifically formulated for fuel systems. Dip a clean, soft-bristled brush into the grease and apply it generously to the fuel line fittings. Ensure you cover all surfaces, including the threads and any O-rings or gaskets. This method allows for precise control, making it easy to reach tight spaces and ensure an even coating. After application, wipe off any excess grease to prevent attracting dirt and moisture.
- Spray Application: Using a grease spray can be convenient and provides a quick coverage. Hold the spray can upright and apply a steady, even stream of grease onto the fittings. This method is particularly useful for larger fuel lines or when accessing the fittings is challenging. Ensure you follow the manufacturer's instructions for the spray angle and distance to achieve optimal coverage. Allow the grease to penetrate for a few seconds before wiping off any excess to avoid over-greasing.
- Rope or Wire Application: For hard-to-reach areas, using a grease-impregnated rope or wire can be beneficial. Cut a piece of rope or wire to the desired length and dip it in the grease. Carefully guide the rope or wire through the fuel line, ensuring it comes into contact with the fittings. This method is especially useful for replacing or maintaining existing fittings without removing the fuel line. After application, inspect the area to ensure complete coverage.
- Penetrating Oil and Grease Combination: In some cases, a penetrating oil can be used before applying grease. Penetrating oils work by loosening any built-up deposits, making it easier to apply grease effectively. Apply the oil to the fittings and allow it to work for a few minutes. Then, use a brush or spray to apply the grease, ensuring it penetrates the metal surfaces. This combination method can provide excellent lubrication and protection.
Remember, when applying grease, it's crucial to use the right type for your specific fuel system. Different greases have varying properties, and using the appropriate one will ensure compatibility and optimal performance. Additionally, always follow the manufacturer's guidelines for application rates and techniques to avoid over-greasing, which can lead to performance issues. Regular maintenance and reapplication of grease are key to keeping fuel line fittings in excellent condition.
Fram G3727 Inline Fuel Filter: Compatibility and Benefits
You may want to see also
Frequently asked questions
For fuel line fittings, a specific type of grease known as "fuel line grease" or "fuel-resistant grease" is ideal. This grease is designed to withstand the corrosive effects of fuel and provide a protective barrier against leaks. It is typically a synthetic grease with a high viscosity to ensure it remains in place and offers long-lasting lubrication.
Fuel lines carry gasoline, diesel, or other fuels, which can be highly corrosive and damaging to rubber or plastic components. Regular grease may not provide sufficient protection against fuel degradation, leading to potential leaks and system failures. Specialized fuel line grease ensures a reliable seal and prevents fuel from deteriorating the fittings, thus maintaining the integrity of the fuel system.
When selecting grease for fuel line fittings, consider the following: look for a product specifically labeled for fuel lines or engine applications. Check the grease's temperature range to ensure it can handle the operating conditions of your vehicle. Additionally, choose a grease with a consistent viscosity to ensure it doesn't become too runny or thick over time. Consulting the vehicle's manual or seeking advice from automotive experts can also guide you in making the right choice.