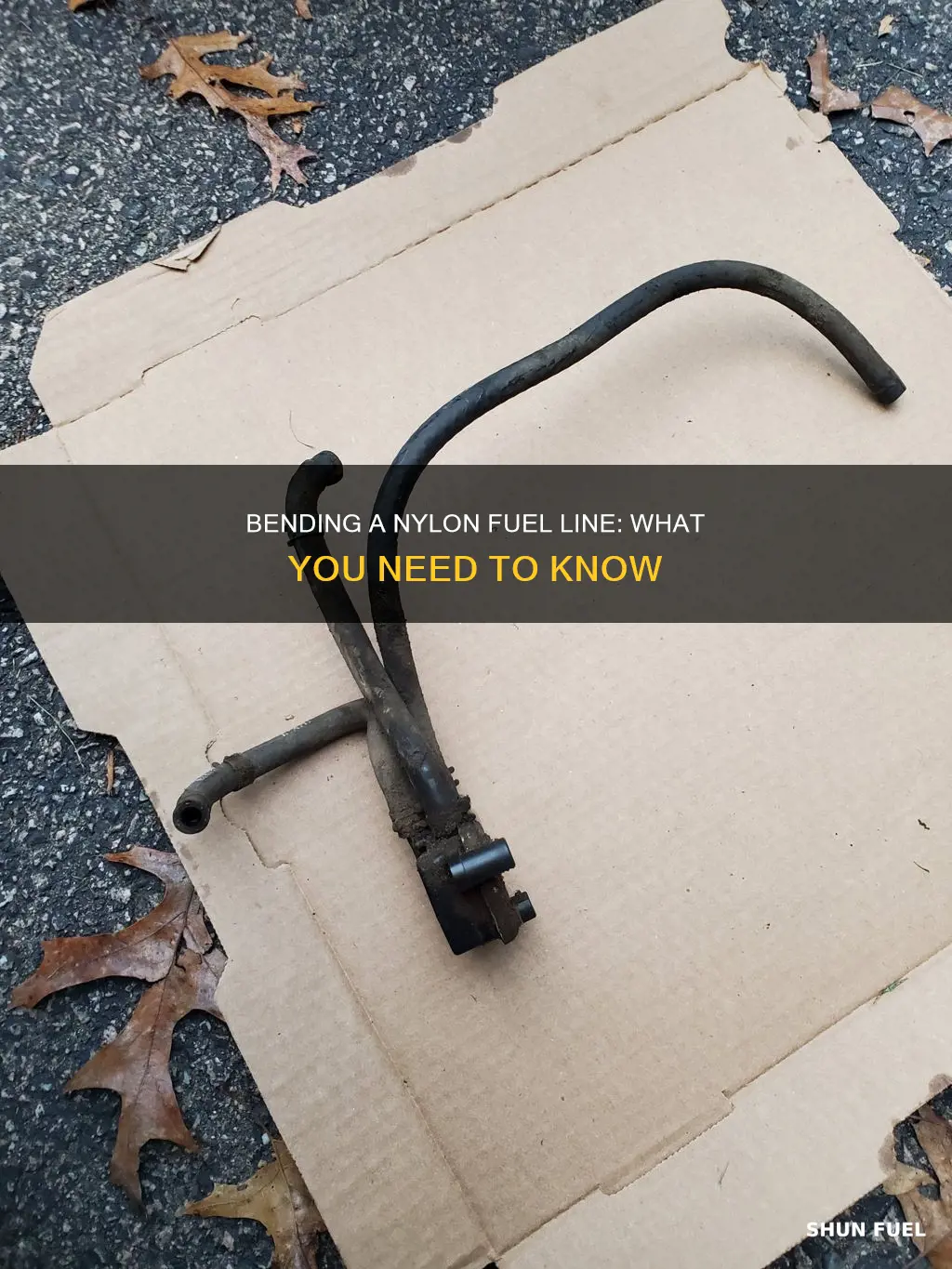
When you bend a nylon fuel line, it can lead to several potential issues. Nylon fuel lines are designed to be flexible and durable, but excessive bending or twisting can cause damage to the line's internal structure. This damage may result in a loss of fuel pressure, reduced flow rate, or even a complete break in the line. Additionally, bending can lead to the formation of kinks or bends that can restrict fuel flow, potentially causing engine performance issues or even stalling. Understanding the proper handling and installation of fuel lines is crucial to prevent these problems and ensure optimal engine performance.
Characteristics | Values |
---|---|
Flexibility | Nylon fuel lines are highly flexible, allowing them to bend and twist without kinking or cracking. |
Temperature Resistance | They can withstand a wide range of temperatures, from extreme cold to high heat, making them suitable for various automotive applications. |
Durability | Nylon is a robust material that is resistant to abrasion, chemicals, and UV radiation, ensuring long-lasting performance. |
Corrosion Resistance | These lines are immune to corrosion, which helps prevent fuel degradation and maintains the quality of the fuel. |
Lightweight | Compared to other materials, nylon fuel lines are lightweight, contributing to improved fuel efficiency and reduced vehicle weight. |
Cost-Effective | Nylon fuel lines are often more affordable than other types of fuel lines, making them a popular choice for both original equipment and aftermarket applications. |
Compatibility | They are compatible with a wide range of fuels, including gasoline, diesel, and ethanol, making them versatile for different vehicle types. |
Ease of Installation | Due to their flexibility and lightweight nature, nylon fuel lines are easy to install, saving time and effort during vehicle maintenance. |
Kinking Resistance | The material's flexibility also ensures that the lines do not kink easily, reducing the risk of fuel restriction or blockage. |
Visual Inspection | Bending a nylon fuel line may not always be noticeable, as the material can retain its shape and appearance even after repeated bending. |
What You'll Learn
- Flexibility: Nylon fuel lines bend easily, allowing for better maneuverability and reduced risk of damage during installation or repairs
- Durability: These lines are resistant to wear and tear, ensuring long-lasting performance even when bent repeatedly
- Cracking: Frequent bending can lead to micro-cracks, compromising the line's integrity and potentially causing fuel leaks
- Kink Resistance: Nylon's flexibility prevents kinking, a common issue with metal lines, which can block fuel flow
- Temperature Tolerance: Bending doesn't affect nylon's ability to withstand temperature changes, maintaining fuel line functionality in various climates
Flexibility: Nylon fuel lines bend easily, allowing for better maneuverability and reduced risk of damage during installation or repairs
Nylon fuel lines are renowned for their exceptional flexibility, a feature that significantly enhances their usability in automotive applications. This flexibility is a direct result of the material's inherent properties, making it an ideal choice for fuel line installations. When you bend a nylon fuel line, you're essentially taking advantage of its pliability, which allows it to conform to various shapes and angles without permanent deformation. This characteristic is particularly useful during the installation process, where fuel lines often need to navigate through tight spaces and complex routes within a vehicle's engine bay.
The ease of bending nylon fuel lines is a game-changer for mechanics and DIY enthusiasts alike. It simplifies the installation process, making it less time-consuming and physically demanding. For instance, when replacing a damaged fuel line, the flexibility of nylon enables it to be bent around obstacles, such as engine components or frame rails, with minimal effort. This reduced risk of damage during installation is a direct benefit of the material's flexibility, ensuring that the fuel lines can be maneuvered safely and efficiently without causing harm to the vehicle's internal structures.
Furthermore, the bendability of nylon fuel lines contributes to their overall durability. By allowing for easy bending, these lines can adapt to the natural movement and expansion of the vehicle's components during operation. This adaptability reduces the likelihood of cracks or fractures forming in the fuel line due to repeated bending or stress. As a result, the fuel lines can maintain their integrity over an extended period, ensuring a reliable fuel supply to the engine without the risk of leaks or fuel contamination.
In addition to installation and durability, the flexibility of nylon fuel lines also plays a role in their ease of repair. When a fuel line is damaged, the ability to bend it allows for creative solutions to be implemented. For example, a damaged section can be carefully cut and reshaped to fit a new fitting or adapter, ensuring a proper seal and preventing fuel leaks. This flexibility in repair procedures not only saves time and money but also contributes to the overall longevity of the vehicle's fuel system.
In summary, the flexibility of nylon fuel lines is a critical aspect of their design, offering numerous advantages during installation, repair, and everyday use. Its ease of bending allows for better maneuverability, reduces the risk of damage, and ensures a more efficient and reliable fuel system. Understanding and appreciating this property can significantly improve the overall performance and longevity of a vehicle's fuel lines.
Understanding Fuel Lines in Kerbal Space Program (KSP)
You may want to see also
Durability: These lines are resistant to wear and tear, ensuring long-lasting performance even when bent repeatedly
Nylon fuel lines are renowned for their exceptional durability, a feature that sets them apart in the automotive industry. This durability is a result of the material's inherent resistance to wear and tear, making it an ideal choice for fuel delivery systems. When you bend a nylon fuel line, it undergoes a transformation that showcases its remarkable resilience. The line's flexibility allows it to conform to various shapes and angles without compromising its structural integrity. This flexibility is crucial, especially in high-performance vehicles where fuel lines are subjected to constant movement and vibrations.
The secret to nylon's durability lies in its molecular structure. The long-chain polymeric structure of nylon provides excellent resistance to abrasion and chemical degradation. This means that even after repeated bending, the fuel line retains its shape and functionality. Unlike other materials that may become brittle or crack under stress, nylon fuel lines maintain their flexibility and strength over time. This is particularly important in applications where fuel lines are exposed to harsh environments, such as under the hood of a racing car or in off-road vehicles.
The bending process itself is a testament to the material's adaptability. When bent, the nylon fuel line does not kink or twist, which could lead to reduced performance or even fuel leaks. Instead, it smoothly transitions around curves and bends, ensuring a consistent and reliable fuel supply. This flexibility is further enhanced by the line's ability to absorb vibrations, reducing the risk of damage from road imperfections or high-speed driving.
In addition to its flexibility, nylon's durability is also evident in its resistance to temperature fluctuations. It can withstand extreme heat and cold without losing its shape or becoming brittle. This temperature resistance is crucial for maintaining the performance of the fuel system, especially in vehicles operating in diverse climates. The material's stability under varying conditions ensures that the fuel lines remain reliable and efficient over the long term.
The long-lasting performance of nylon fuel lines is a significant advantage for vehicle owners. By investing in these durable lines, they can ensure a consistent and safe fuel supply for their engines. The ability to bend and adapt without compromising strength means that nylon fuel lines provide a reliable solution for fuel delivery, even in demanding applications. This durability is a key factor in the widespread use of nylon in the automotive industry, offering a cost-effective and high-performance alternative to traditional fuel line materials.
Nylon Fuel Line Cleaning: Effective Methods and Tools
You may want to see also
Cracking: Frequent bending can lead to micro-cracks, compromising the line's integrity and potentially causing fuel leaks
Bending a nylon fuel line, especially frequently, can have detrimental effects on its structural integrity. The primary concern is the development of micro-cracks, which may not be immediately visible but can significantly impact the line's performance. These cracks can occur due to the repetitive stress and strain caused by bending, especially when the line is subjected to sharp turns or tight radii. Over time, this can lead to a gradual weakening of the material, making it more susceptible to damage and potential failure.
The process of bending can create localized stress points, especially at the bends or kinks. As the line is bent repeatedly, the stress accumulates, leading to tiny fractures in the nylon material. These micro-cracks can start as minuscule lines on the surface but may progress to deeper, more extensive cracks if the bending continues without proper reinforcement or support. The integrity of the fuel line is crucial, as it ensures the safe and efficient transfer of fuel from the tank to the engine.
When these micro-cracks occur, they can compromise the line's ability to withstand internal pressure and the force of the fuel flow. As a result, the line may become more prone to leaks, especially at the bend or where the cracks have formed. Fuel leaks are a serious issue as they can lead to engine misfires, reduced performance, and even potential fire hazards. The presence of cracks can also attract contaminants, such as moisture, which can further deteriorate the line's condition and accelerate the corrosion process.
To prevent these issues, it is essential to handle and install nylon fuel lines with care. Avoid excessive bending, and ensure that any bends or turns are gradual and well-supported. Using protective sleeves or brackets to reinforce the line at bends can also help distribute the stress more evenly and prevent the formation of micro-cracks. Regular inspections and maintenance can identify any signs of cracking early on, allowing for timely repairs or replacements to ensure the safety and reliability of the fuel system.
In summary, frequent bending of a nylon fuel line can result in micro-cracks, which, over time, can lead to significant structural weaknesses. These cracks may not be visible but can cause fuel leaks, engine performance issues, and potential safety hazards. Proper installation techniques and regular maintenance are key to avoiding these problems and ensuring the longevity of the fuel line.
Understanding Truck Fuel Lines: A Comprehensive Guide to Different Types
You may want to see also
Kink Resistance: Nylon's flexibility prevents kinking, a common issue with metal lines, which can block fuel flow
Nylon fuel lines are an excellent choice for fuel delivery systems, especially in applications where flexibility and resistance to kinking are essential. One of the primary advantages of using nylon is its inherent flexibility, which sets it apart from traditional metal fuel lines. When you bend a nylon fuel line, you'll notice its ability to conform to the shape without any permanent deformation. This characteristic is crucial because it prevents kinking, a common problem associated with metal lines. Kinking occurs when a metal line is bent or twisted, causing it to form a sharp crease or kink, which can restrict or block the fuel flow. This issue is particularly problematic as it can lead to fuel starvation, affecting the engine's performance and potentially causing it to stall.
The flexibility of nylon allows it to absorb the stresses and strains that occur during normal vehicle operation. As the engine vibrates and the vehicle moves, the fuel lines experience various movements and angles. Nylon's ability to bend and flex without kinking ensures that the fuel flow remains uninterrupted, providing a consistent supply to the engine. This is especially important in high-performance or off-road vehicles where the fuel system is subjected to more extreme conditions.
In contrast, metal fuel lines are more rigid and less flexible. When bent, they tend to retain their shape, which can lead to kinking over time. Kinking in metal lines can be a significant concern, especially in high-pressure fuel systems. As the engine operates, the pressure inside the fuel lines can cause the metal to crimp or fold, creating a physical obstruction. This obstruction may result in reduced fuel flow, leading to engine performance issues and potential damage.
Nylon's kink-resistant nature is a direct result of its material properties. The polymer's molecular structure allows it to deform without breaking, making it highly flexible. This flexibility is further enhanced by the line's construction, often featuring a braided or spiral design, which adds to its kink-resistant capabilities. When compared to metal lines, nylon lines can withstand more bending and twisting without compromising their structural integrity.
In summary, the flexibility of nylon fuel lines is a key factor in preventing kinking, a common problem with metal lines. By avoiding kinks, nylon lines ensure a consistent fuel supply, maintaining optimal engine performance. This makes nylon an ideal choice for fuel delivery systems, especially in demanding environments where flexibility and reliability are critical.
Fixing Rusted Fuel Lines: A Step-by-Step Guide to Prevent Engine Damage
You may want to see also
Temperature Tolerance: Bending doesn't affect nylon's ability to withstand temperature changes, maintaining fuel line functionality in various climates
Bending a nylon fuel line is a common practice in automotive repairs and modifications, and understanding its impact on the material's performance is crucial for ensuring the system's reliability. When it comes to temperature tolerance, nylon fuel lines exhibit remarkable resilience. Unlike some other materials, bending nylon does not compromise its ability to withstand temperature fluctuations, making it an ideal choice for fuel lines that operate in diverse environmental conditions.
Nylon's inherent flexibility and durability contribute to its excellent temperature tolerance. This material can handle extreme temperature variations without losing its structural integrity. Whether exposed to scorching summer heat or frigid winter temperatures, nylon fuel lines remain functional, ensuring a consistent fuel supply to the engine. This property is particularly advantageous in regions with varying climates, where fuel lines must adapt to rapid temperature changes.
The bending process itself does not introduce any weaknesses or vulnerabilities in the nylon material. Nylon's molecular structure allows it to retain its strength and elasticity even when bent. This is in contrast to some other materials that may become brittle or lose their shape-memory properties when subjected to bending. As a result, nylon fuel lines can withstand repeated bending without compromising their performance.
In automotive applications, the temperature tolerance of nylon fuel lines is a significant advantage. Engines generate substantial heat, and the fuel lines must manage this heat while also withstanding cold starts and rapid temperature changes during operation. Nylon's ability to maintain functionality under these conditions ensures a reliable fuel supply, contributing to the overall efficiency and longevity of the vehicle's engine system.
In summary, bending a nylon fuel line does not impact its temperature tolerance, making it a reliable and versatile choice for fuel line applications. Its flexibility, durability, and resistance to temperature changes make nylon an excellent material for fuel lines, providing consistent performance in various climates and engine operating conditions. This property is a key factor in the widespread use of nylon in automotive fuel systems.
Duromax Fuel Line Diameter: 2003 Model Specs Revealed
You may want to see also
Frequently asked questions
Bending a nylon fuel line can lead to several issues. Firstly, it can cause a permanent kink or crease in the line, which may restrict fuel flow or even cause a complete blockage. This can result in engine performance problems, such as reduced power, stalling, or difficulty starting the engine. Additionally, bending can compromise the line's flexibility, making it more susceptible to damage over time.
Yes, bending a fuel line can potentially lead to fuel leaks. When a line is bent, it can create a crack or tear in the material, especially if the bend is sharp or forceful. This can expose the inner layers of the line, allowing fuel to leak out. Leaks can be dangerous as they may result in fuel accumulation, creating a fire hazard, or they can lead to engine misfires and reduced performance.
To minimize damage to the nylon fuel line, it's essential to handle it with care. Avoid sharp bends or excessive force when manipulating the line. Instead, use a fuel line bender or a pair of pliers to create gentle curves. Ensure that the line is not twisted or kinked, as this can also cause internal damage. Regularly inspect the line for any signs of wear or damage, especially if you've recently bent it, to ensure optimal performance and prevent potential issues.