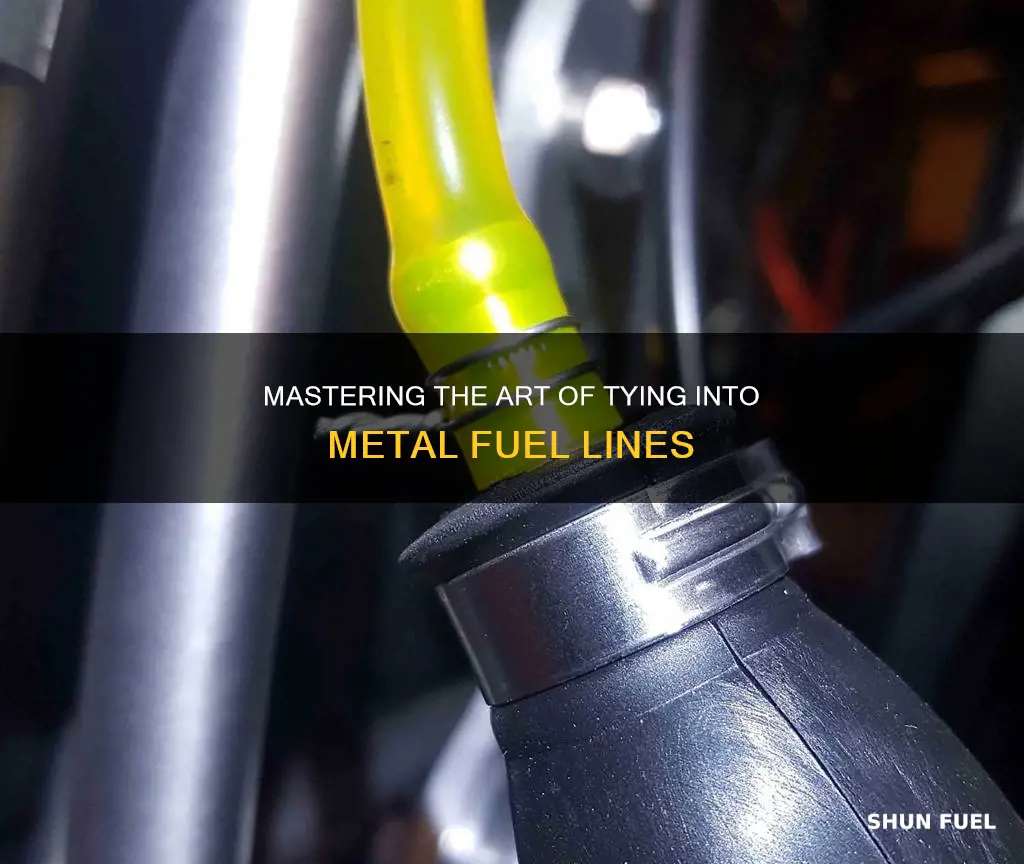
Tying into a metal fuel line requires careful preparation and adherence to safety guidelines. This process is essential when connecting a new fuel source or modifying an existing system. Before beginning, ensure you have the necessary tools and materials, including a suitable fuel line connector, a wrench, and safety equipment like gloves and goggles. It's crucial to inspect the metal fuel line for any damage or corrosion and to ensure a tight, secure connection. Start by cleaning the ends of the fuel lines and using a primer to ensure a strong bond. Then, carefully insert the connector, tightening it with a wrench, and double-check for any leaks. Always follow manufacturer instructions and safety protocols to ensure a safe and effective tie-in.
What You'll Learn
- Preparation: Clean and inspect the fuel line, ensuring it's free of debris and damage
- Tools and Materials: Gather necessary tools: pliers, fuel line connectors, and cleaning supplies
- Clamping Technique: Tighten the clamp securely, but avoid over-tightening to prevent damage
- Fuel Line Routing: Route the line away from heat sources and sharp edges for safety
- Testing: Verify the connection by checking for leaks and ensuring proper fuel flow
Preparation: Clean and inspect the fuel line, ensuring it's free of debris and damage
Before attempting to tie into a metal fuel line, it's crucial to ensure a clean and safe working environment. Start by locating the fuel line, which is typically a metal tube that carries fuel from the tank to the engine. Inspect the line for any visible signs of damage, such as punctures, tears, or corrosion. If you notice any issues, it's essential to address them before proceeding. Clean the fuel line to remove any debris or contaminants that may have accumulated over time. This can be done using a soft-bristled brush or a small air hose to blow out any loose particles. Ensure that the line is completely clear of any foreign matter, as this can lead to fuel contamination and potential engine issues.
Once the fuel line is clean, it's time to inspect it more thoroughly. Check for any signs of wear and tear, such as kinks, bends, or areas where the metal has become thin. These issues can compromise the integrity of the fuel line and lead to potential leaks. Use a flashlight to examine the line closely, especially in tight or hard-to-reach areas. Look for any signs of corrosion or oxidation, which can weaken the metal over time. If you identify any problem areas, consider replacing the affected section of the fuel line to ensure a secure connection.
Safety should always be a top priority when working with fuel lines. Before proceeding, ensure that the fuel source is turned off and that the engine is in a safe, off state. This step is crucial to prevent any accidental fuel release or engine damage. Additionally, wear appropriate personal protective equipment (PPE), such as gloves and safety goggles, to protect yourself from any potential hazards.
When cleaning and inspecting the fuel line, take note of its length and any bends or angles. This information will be useful when planning the tie-in process. Ensure that the line is straight and free-flowing, as any sharp bends or kinks can restrict fuel flow and cause engine performance issues. By taking the time to thoroughly prepare and inspect the fuel line, you'll set the foundation for a successful and safe tie-in process.
Fuel Tank Liner Removal: A Step-by-Step Guide
You may want to see also
Tools and Materials: Gather necessary tools: pliers, fuel line connectors, and cleaning supplies
To begin the process of tying into a metal fuel line, it's crucial to gather the necessary tools and materials. This ensures that you have everything readily available to complete the task efficiently and safely. Here's a detailed breakdown of the tools and supplies you'll need:
Pliers: A good pair of pliers is an essential tool for any fuel line work. You'll need pliers with a smooth jaw to avoid damaging the metal fuel line. Pliers help you grip and manipulate the fuel line, making it easier to connect and secure it. Look for pliers with a comfortable grip and a range of jaw sizes to accommodate different fuel line diameters.
Fuel Line Connectors: These connectors are designed to join fuel lines together securely. When purchasing fuel line connectors, ensure they are compatible with the type of fuel line you are working with. Common types include barbed connectors, compression fittings, and quick-connect fittings. Each type has its advantages, so choose based on your specific application and the fuel line's characteristics.
Cleaning Supplies: Before and during the installation process, keeping the work area clean is essential. Gather cleaning supplies such as a mild detergent, a soft brush, and a clean cloth. These items will help you remove any dirt, grease, or contaminants from the fuel line and the connection points, ensuring a proper seal and preventing potential leaks.
Additionally, consider having a fuel line inspection camera or borescope to visualize the interior of the fuel line and identify any potential issues or blockages. This tool can be invaluable for ensuring a smooth and successful connection. Remember to wear appropriate personal protective equipment (PPE), such as gloves and safety goggles, to protect yourself during the process.
By gathering these tools and materials, you'll be well-prepared to tackle the task of tying into a metal fuel line, ensuring a professional and safe installation.
Clogged Fuel Return Line: Engine Performance and Safety Risks
You may want to see also
Clamping Technique: Tighten the clamp securely, but avoid over-tightening to prevent damage
When working with metal fuel lines, it's crucial to ensure a secure and reliable connection to prevent any potential leaks or damage. One effective method for achieving this is by using a clamping technique that involves tightening the clamp firmly but carefully. This approach requires precision and attention to detail to avoid any adverse consequences.
The clamping process begins with selecting the appropriate clamp for the specific fuel line. Clamps come in various sizes and designs, so it's essential to choose one that fits the fuel line's diameter and material. Once the right clamp is identified, position it around the fuel line, ensuring it is centered and aligned with the line's path. This initial placement sets the foundation for a secure connection.
Now, the critical step is tightening the clamp. Use a wrench or a suitable tool to apply firm pressure to the clamp's adjusting mechanism. The goal is to create a tight seal without causing any distortion or damage to the fuel line. It's a delicate balance, as excessive force can lead to bending or even cracking of the metal line. Therefore, apply pressure gradually and evenly, ensuring a consistent grip.
To avoid over-tightening, pay close attention to the fuel line's behavior. As you tighten the clamp, observe if the line starts to bend or show any signs of strain. If so, immediately release some pressure and adjust your grip. The key is to maintain a secure hold while preserving the integrity of the fuel line. Over time, you'll develop a sense of the right amount of force required, ensuring a reliable connection.
After achieving the desired tightness, double-check the clamp's position and ensure it is firmly in place. This final inspection guarantees a secure tie-in, providing peace of mind that the fuel line is safely connected. Remember, the clamping technique is a precise art, requiring practice and a keen eye to master. With this approach, you can confidently tie into metal fuel lines, knowing your work is secure and leak-free.
Understanding Fuel Line Sizes for Optimal Pump Performance
You may want to see also
Fuel Line Routing: Route the line away from heat sources and sharp edges for safety
When routing a fuel line, it's crucial to prioritize safety by keeping the line away from potential hazards. Heat sources and sharp edges can cause damage to the fuel line, leading to leaks and potential accidents. Here's a detailed guide on how to ensure a safe fuel line routing:
Identify Heat Sources and Hazards: Begin by assessing the area where the fuel line will be installed. Locate any heat sources, such as engines, exhaust systems, or hot surfaces. Also, identify sharp edges or protruding objects that could come into contact with the fuel line. This step is essential to anticipate potential risks.
Route the Fuel Line Strategically: Plan the path of the fuel line to avoid these identified hazards. Here are some key considerations:
- Keep the line at a safe distance from heat sources. A general rule of thumb is to maintain a minimum distance of 2 inches (5 cm) between the fuel line and any hot surface.
- Route the line away from sharp edges, such as those found on metal frames, brackets, or other mechanical components. Use protective sleeves or insulation to safeguard the line if necessary.
- Consider the natural flow of the vehicle's structure. Route the line along the frame rails, behind the firewall, or in areas where it is less likely to be damaged.
Use Proper Support and Protection: To ensure the fuel line's integrity, provide adequate support and protection:
- Secure the line with ties or clips at regular intervals to maintain tension and prevent sagging.
- Use protective sleeves or insulation material to cover the line where it passes over sharp edges or around obstacles.
- In areas where the line is exposed, consider using a protective covering to shield it from potential impacts or damage.
Regular Inspection and Maintenance: Safety measures should not be limited to the initial installation. Regularly inspect the fuel line to identify any signs of wear, damage, or potential hazards. Look for cracks, brittleness, or any signs of fuel leakage. Promptly address any issues and re-route the line if necessary to maintain a safe environment.
By following these guidelines, you can ensure that the fuel line is safely routed, minimizing the risk of damage and potential fuel-related accidents. Remember, proper routing and regular maintenance are essential for the long-term reliability and safety of your fuel system.
Mastering Fuel Line Routing: Essential Tips for Optimal Performance
You may want to see also
Testing: Verify the connection by checking for leaks and ensuring proper fuel flow
Before finalizing the connection, it's crucial to test it thoroughly to ensure safety and functionality. Here's a step-by-step guide to verifying the connection:
Leak Testing:
- Prepare the Materials: Gather the necessary tools: a soapy water solution, a spray bottle, and a rag. Ensure you have the fuel line, fittings, and any additional components used in your setup.
- Clean the Connection: Thoroughly clean the areas where the fuel line and fittings meet. Remove any dirt, grease, or debris that could interfere with the test.
- Apply Soapy Water: Liberally apply the soapy water solution to both sides of the connection. Pay close attention to all seams and threads.
- Inspect for Bubbles: Carefully observe the connection. If bubbles appear around the connection, it indicates a leak. Bubbles signify that fuel is escaping, which is highly dangerous.
- Address Leaks: If leaks are detected, immediately tighten the fittings further or consider using thread seal tape or pipe compound to create a tighter seal. Repeat the leak test until no bubbles are present.
Fuel Flow Verification:
- Connect a Test Gauge: Attach a fuel flow gauge or pressure gauge to the fuel line, ensuring it's securely connected. This gauge will help you measure the fuel flow rate.
- Start the Engine (if applicable): If you're connecting to an existing fuel system, start the engine and allow it to idle. This will simulate real-world conditions.
- Monitor Fuel Flow: Observe the gauge readings. The flow rate should be consistent and within the expected range for your engine and fuel system.
- Check for Blockages: If the flow rate is significantly lower than expected, it may indicate a blockage in the line. Inspect the fuel line for any kinks, clogs, or obstructions.
- Adjust as Needed: If necessary, adjust the fuel line's position or use a fuel filter to improve flow. Ensure all connections remain secure throughout the process.
Remember, thorough testing is essential for a safe and successful fuel line connection. Always prioritize safety and consult a professional if you encounter any difficulties.
Understanding the Three Fuel Lines in an Engine: A Comprehensive Guide
You may want to see also