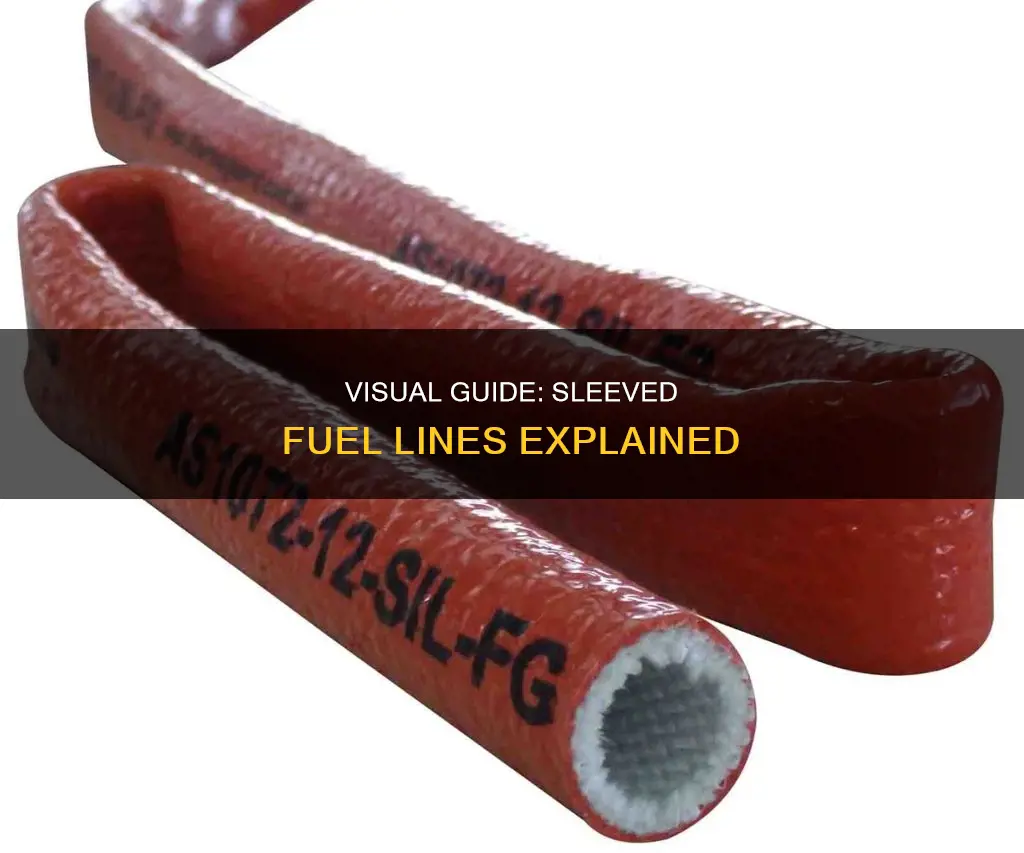
When discussing sleeved fuel lines, it's important to understand their appearance and function. Sleeved fuel lines are an essential component in the fuel delivery system of vehicles, particularly those with high-performance engines. These lines are designed to protect the fuel lines from heat, abrasion, and other potential damage. They typically consist of an inner fuel line surrounded by a protective sleeve made of materials such as rubber or plastic. The sleeve is often color-coded to indicate the type of fuel it carries, such as red for gasoline or blue for diesel. Understanding the visual characteristics of sleeved fuel lines is crucial for proper installation, maintenance, and troubleshooting in automotive applications.
What You'll Learn
- Sleeved fuel lines are typically made of rubber or plastic with a metal sleeve
- Sleeved lines have a protective covering to prevent damage from fuel
- The sleeve is often a tight fit around the fuel line
- Sleeved lines can be straight or coiled for different vehicle needs
- Visual inspection: Sleeved lines appear as a thick, flexible tube
Sleeved fuel lines are typically made of rubber or plastic with a metal sleeve
Sleeved fuel lines are an essential component of a vehicle's fuel system, designed to ensure efficient and safe fuel delivery from the tank to the engine. These fuel lines are constructed with a unique structure, combining the flexibility of rubber or plastic with the strength and durability of a metal sleeve. This innovative design allows for a robust yet adaptable fuel line that can withstand the rigors of the automotive environment.
The metal sleeve, typically made of steel or aluminum, is the key feature that sets sleeved fuel lines apart. It is carefully integrated into the rubber or plastic casing, providing structural integrity and protection against potential damage. The sleeve acts as a protective barrier, shielding the fuel line from sharp edges, vibrations, and other mechanical stresses that could compromise its performance. This design is particularly crucial in high-pressure fuel systems, where the fuel lines must handle the force of the fuel flow without leaking or rupturing.
In terms of appearance, sleeved fuel lines exhibit a distinct visual characteristic. The metal sleeve is often visible through the rubber or plastic outer layer, creating a layered effect. This layering is a result of the manufacturing process, where the metal sleeve is inserted into the fuel line casing, ensuring a secure and precise fit. The metal component may appear as a thin, flexible strip or a more rigid, cylindrical structure, depending on the specific design and application.
The color of sleeved fuel lines can vary, but it is common to see a metallic finish, such as silver or gray, on the metal sleeve. This color contrast against the rubber or plastic background makes identification and inspection easier for mechanics and vehicle owners. Additionally, the fuel lines might have markings or indicators along their length, providing important information about fuel flow direction, pressure ratings, or other specifications.
Proper installation and maintenance of sleeved fuel lines are crucial to ensure optimal performance and longevity. Mechanics should ensure that the metal sleeve is securely fastened and aligned, preventing any potential movement that could lead to fuel leakage or system failure. Regular inspections for any signs of damage, such as cracks or corrosion, are essential to maintain the integrity of the fuel system.
Rubber Hose Fuel Line Lubrication: Essential Tips for Smooth Operation
You may want to see also
Sleeved lines have a protective covering to prevent damage from fuel
Sleeved fuel lines are an essential component of a vehicle's fuel system, designed to protect the fuel lines from potential damage caused by various factors. These lines are typically made of a flexible, durable material that provides a protective barrier around the fuel-carrying tube. The primary purpose of this design is to safeguard the fuel lines from potential hazards, ensuring the vehicle's fuel system remains reliable and efficient.
The protective covering on sleeved fuel lines serves multiple purposes. Firstly, it acts as a shield against mechanical damage. Fuel lines can be susceptible to wear and tear from engine vibrations, especially in high-performance vehicles or those with modified engines. The sleeve provides a layer of insulation, reducing the risk of the fuel line chafing against other components or rubbing against sharp edges. This is particularly important in areas where the fuel lines pass through tight spaces or near moving parts.
Secondly, the protective covering helps prevent fuel contamination. Fuel lines can be exposed to various contaminants, such as dirt, debris, or even small stones, which can enter the system during fuel delivery or when the vehicle is driven off-road. The sleeve acts as a filter, trapping these particles and ensuring that only clean fuel reaches the engine. This is crucial for maintaining engine performance and longevity, as contaminated fuel can lead to engine misfires, reduced power, and potential long-term damage.
In addition, sleeved fuel lines offer protection against fuel-related chemicals. Over time, fuel lines can come into contact with engine oil, coolant, or other chemicals present in the engine bay. The protective covering acts as a barrier, preventing these substances from directly interacting with the fuel line material, which could lead to degradation or corrosion. This is especially important in older vehicles or those with less-than-ideal fuel system maintenance.
When inspecting or replacing sleeved fuel lines, it is essential to consider the specific design and material used. Some sleeves are made of rubber, while others might use more advanced materials like synthetic composites. The choice of material can impact the flexibility, durability, and overall performance of the fuel line. Proper installation and regular maintenance are also key to ensuring the effectiveness of the sleeved fuel lines in protecting the vehicle's fuel system.
Exploring Rubber Fuel Line Hose Sizes: A Comprehensive Guide
You may want to see also
The sleeve is often a tight fit around the fuel line
When considering the appearance of sleeved fuel lines, it's important to understand the purpose and design of this component. The sleeve, as the name suggests, is a protective covering or casing that surrounds the fuel line. Its primary function is to safeguard the fuel line from potential damage, such as abrasion, corrosion, or impact. This is particularly crucial in applications where the fuel line may be exposed to harsh environments or physical stress.
The sleeve is typically made from durable materials such as rubber, plastic, or metal, depending on the specific requirements and the environment in which it will be used. These materials are chosen for their ability to withstand the rigors of the fuel line's journey, ensuring the safe and efficient transport of fuel. One of the key characteristics of the sleeve is its tight fit around the fuel line. This close adherence is essential for several reasons. Firstly, it provides an effective barrier against external elements, preventing contaminants from entering the fuel system and causing potential issues. A tight fit also ensures that the sleeve remains securely in place, even when the vehicle is in motion or subjected to vibrations.
In terms of appearance, the sleeve's tight fit gives it a distinct visual characteristic. It will appear as a slender, cylindrical tube that snugly envelops the fuel line. This close proximity to the fuel line is intentional, as it allows for optimal protection and control. The sleeve's color may vary depending on the material used, but it is often designed to be inconspicuous, blending seamlessly with the surrounding components to maintain a clean and professional look under the hood.
Installation of the sleeve involves carefully sliding it over the fuel line, ensuring a precise and secure fit. This process requires attention to detail to guarantee that the sleeve is neither too tight, causing potential damage to the fuel line, nor too loose, compromising its protective function. Proper installation is crucial to the overall performance and longevity of the fuel system.
In summary, the sleeve's tight fit around the fuel line is a critical aspect of its design, providing essential protection and control. This feature ensures the sleeve's effectiveness in safeguarding the fuel line, contributing to the overall reliability and safety of the vehicle's fuel system. Understanding this tight fit is key to appreciating the functionality and benefits of sleeved fuel lines.
Creative Solutions: Exploring Alternatives to Fuel Line Clamps
You may want to see also
Sleeved lines can be straight or coiled for different vehicle needs
When considering sleeved fuel lines, it's important to understand that these lines can be tailored to fit various vehicle requirements. The design of sleeved fuel lines allows for flexibility in terms of their physical attributes, ensuring compatibility with different engine configurations and fuel systems. One key aspect is the material used for the sleeve, which can vary depending on the application. Common materials include rubber, silicone, and various types of plastic, each offering unique advantages in terms of flexibility, durability, and resistance to heat and chemicals.
The primary function of sleeved fuel lines is to provide a protective barrier around the fuel hose, ensuring it remains intact and functional over time. This is particularly crucial in high-pressure fuel systems where the hose can be susceptible to damage from engine vibrations, heat, and other environmental factors. Sleeved lines are designed to withstand these conditions, offering a robust solution for fuel delivery.
In terms of their physical appearance, sleeved fuel lines can be either straight or coiled. Straight lines are typically used in applications where the fuel source and the engine are in close proximity, allowing for a direct and efficient connection. These lines are often shorter and more rigid, making them ideal for engines with limited space. On the other hand, coiled lines are more versatile and are commonly used in vehicles with more complex fuel systems or those that require a longer path for the fuel line. The coiling allows for better flexibility, accommodating various engine positions and angles without compromising the integrity of the fuel delivery.
The choice between straight and coiled sleeved fuel lines depends on several factors, including the vehicle's engine layout, the available space, and the specific requirements of the fuel system. For instance, in high-performance vehicles or those with modified engines, coiled lines might be preferred to ensure optimal fuel flow and engine performance. Conversely, in classic cars or vehicles with traditional engine designs, straight lines may be more suitable to maintain a clean and classic look while still providing the necessary protection for the fuel hose.
In summary, sleeved fuel lines offer a customizable solution for fuel delivery systems, catering to the unique needs of different vehicles. Whether straight or coiled, these lines provide a protective barrier, ensuring the longevity and efficiency of the fuel system. Understanding the various options available allows vehicle owners and mechanics to make informed decisions when selecting the appropriate sleeved fuel lines for their specific applications.
The Color of Oxyfuel: Unveiling the Oxy-Fuel Cutting Mystery
You may want to see also
Visual inspection: Sleeved lines appear as a thick, flexible tube
When examining sleeved fuel lines, a visual inspection reveals a distinct and easily identifiable feature. These lines are designed to protect the fuel lines from potential damage and are typically made of a durable, flexible material. Visually, they appear as a thick, flexible tube, often with a slightly larger diameter compared to standard fuel lines. This thickness is a key characteristic, as it indicates the presence of the sleeve, which is a protective layer.
The flexibility of these sleeved lines is another important aspect of their visual appearance. They should be able to bend and move with the engine and fuel system without kinking or becoming rigid. This flexibility ensures that the fuel lines can accommodate the natural movement of the vehicle during operation, reducing the risk of damage.
In terms of color, sleeved fuel lines often have a distinct color, such as a bright yellow or orange, which makes them stand out against the surrounding engine components. This color coding is a practical way to identify these lines during inspections, as it helps mechanics and technicians quickly recognize and address any potential issues.
Upon closer inspection, the thickness of the sleeved lines can be felt, providing a tactile indication of their protective nature. This thickness is a result of the multiple layers of material used in their construction, including the outer sleeve and any internal protective coatings. The overall design ensures that the fuel lines remain intact and functional, even in challenging engine environments.
Identifying sleeved fuel lines is crucial for maintenance and repair purposes. Their unique appearance, with the combination of thickness, flexibility, and color, makes them easily distinguishable from regular fuel lines. This visual inspection is a valuable skill for mechanics to quickly assess the condition and integrity of the fuel system, ensuring optimal performance and safety.
Understanding Saturn Fuel Line Inner Diameter: A Comprehensive Guide
You may want to see also
Frequently asked questions
Sleeved fuel lines are an essential component in the fuel delivery system of an engine. They are designed to protect the fuel lines from potential damage caused by heat, vibration, and other engine components. The sleeves are typically made of a durable material like steel or aluminum, providing a protective layer around the fuel lines.
The primary difference is the presence of the protective sleeve. Sleeved fuel lines have a cylindrical or tubular cover that encloses the fuel line, ensuring it remains intact and secure. Regular fuel lines, on the other hand, lack this protective layer and are more susceptible to wear and tear.
These fuel lines often have a distinct look. The fuel line itself is usually a flexible hose or tube, and the sleeve is typically a rigid or semi-rigid tube that surrounds the fuel line. The sleeve may be a separate component attached to the fuel line or an integral part of the fuel line's construction. It can be made of various materials, but common choices include metal or a composite material.
Yes, there are several advantages. Sleeved fuel lines offer improved durability, reducing the risk of fuel leaks and engine performance issues. They also help prevent fuel contamination by keeping out contaminants like dust, dirt, and moisture. Additionally, the sleeves can provide better heat resistance, ensuring the fuel lines remain flexible and functional even in high-temperature environments.