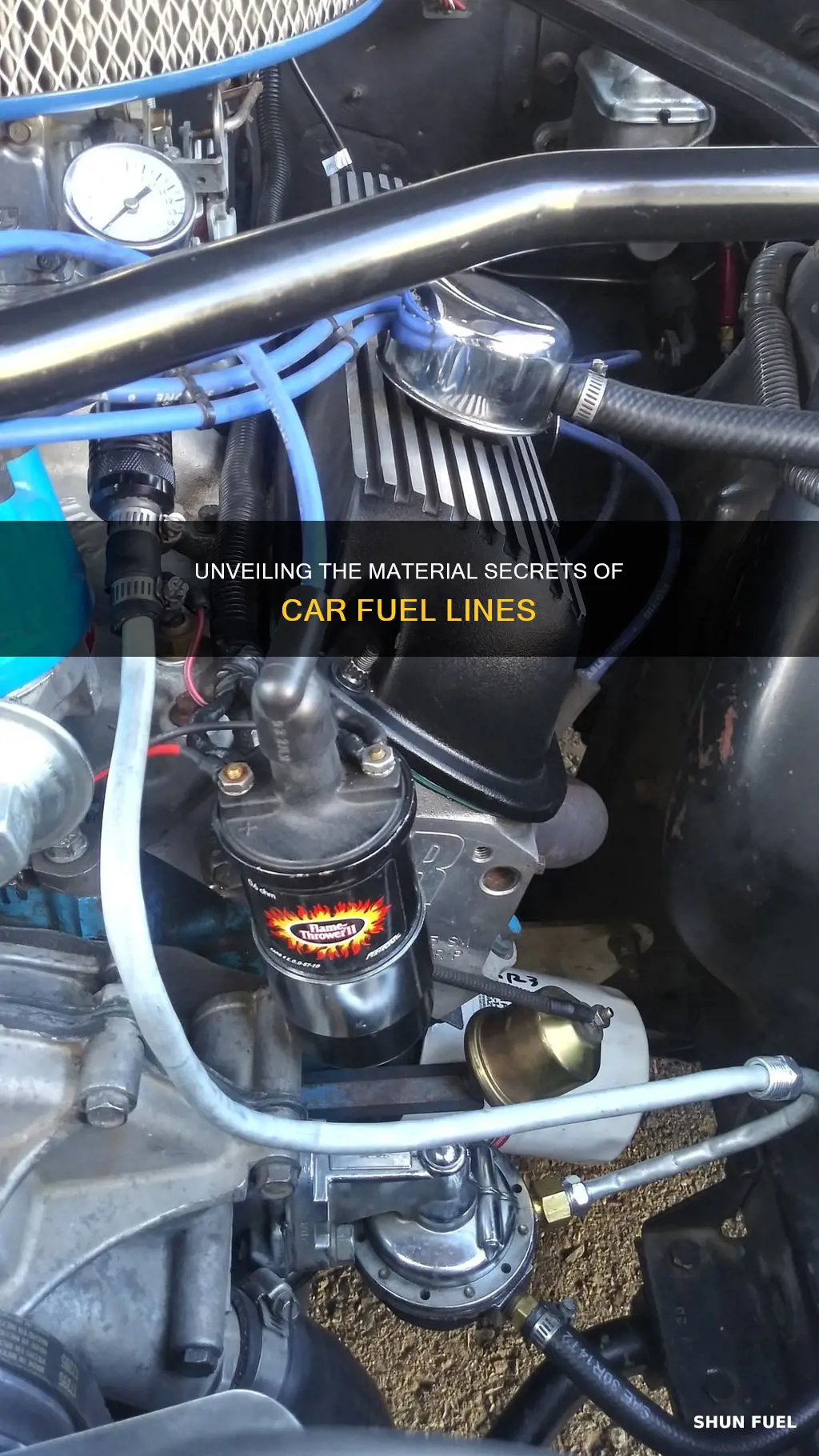
Car fuel lines are an essential component of a vehicle's fuel system, responsible for transporting fuel from the tank to the engine. These lines are typically made from a variety of materials, each chosen for its specific properties and performance characteristics. Common materials include rubber, plastic, and metal, with each material offering unique advantages in terms of flexibility, durability, and resistance to fuel degradation. The choice of material can significantly impact the overall performance and longevity of the fuel system, making it a critical aspect of vehicle engineering.
What You'll Learn
- Material Selection: Car fuel lines are typically made from materials like steel, aluminum, or plastic, each with unique properties
- Flexibility and Strength: The material must be flexible to withstand engine vibrations but also strong to resist fuel pressure
- Corrosion Resistance: Materials like stainless steel or coated plastics are chosen to prevent corrosion from fuel
- Temperature Tolerance: Lines must handle extreme temperatures, from cold starts to hot engines, without cracking or leaking
- Compliance and Standards: Fuel lines must meet industry standards and regulations for safety and performance
Material Selection: Car fuel lines are typically made from materials like steel, aluminum, or plastic, each with unique properties
Car fuel lines are an essential component of a vehicle's fuel system, responsible for transporting fuel from the tank to the engine. The choice of material for these lines is crucial, as it directly impacts the performance, safety, and longevity of the fuel system. Typically, fuel lines are crafted from a variety of materials, each selected for its unique properties and advantages.
One of the most common materials used for fuel lines is steel. Steel offers excellent strength and durability, making it a reliable choice for fuel lines. It can withstand high pressure and temperature variations, ensuring a secure and efficient fuel supply. However, steel fuel lines can be heavy and rigid, which might lead to vibrations and potential damage over time. To mitigate this, some manufacturers use flexible steel-reinforced hoses, providing a balance between strength and flexibility.
Aluminum is another popular material, often preferred for its lightweight nature. This material is highly resistant to corrosion, which is essential for fuel lines as they are exposed to various chemicals and environmental factors. Aluminum fuel lines are also known for their flexibility, making them easier to route and install. Despite these advantages, aluminum may not be as strong as steel, and its performance can be affected by extreme temperatures.
Plastic, in the form of synthetic hoses, is a lightweight and cost-effective option. It is highly flexible, allowing for easy installation and customization. Plastic fuel lines are also resistant to corrosion and can withstand high temperatures. However, they may not be as durable as metal options and can be more susceptible to damage from sharp objects or road debris. The choice between plastic and metal fuel lines often depends on the specific requirements of the vehicle and the driving conditions.
In summary, the material selection for car fuel lines is a critical aspect of vehicle design. Each material offers unique advantages, and the choice depends on factors such as strength, flexibility, corrosion resistance, and cost. Engineers and manufacturers carefully consider these properties to ensure the fuel system's reliability and performance, ultimately contributing to the overall driving experience and safety.
Outboard Motor Fuel Line: To Disconnect or Not to Disconnect?
You may want to see also
Flexibility and Strength: The material must be flexible to withstand engine vibrations but also strong to resist fuel pressure
The choice of material for car fuel lines is crucial, as it directly impacts the performance and reliability of the fuel delivery system. When it comes to flexibility and strength, the material must be able to withstand the harsh conditions of an engine's environment while also maintaining its structural integrity under varying fuel pressures.
One of the primary requirements for fuel line materials is flexibility. Engine vibrations can be intense and constant, especially during acceleration and deceleration. The fuel lines need to move and flex with the engine components without compromising their structural integrity. This flexibility is often achieved through the use of materials that can deform slightly under stress without breaking. Rubber, for instance, is a common choice due to its inherent flexibility. Natural rubber can absorb vibrations and reduce the transmission of these vibrations to the fuel system, ensuring a smoother operation.
However, flexibility alone is not sufficient. Fuel lines also need to be strong to handle the pressure generated by the fuel pump and the engine's operation. Fuel pressure can vary significantly, and the lines must be able to resist this pressure without leaking or failing. This strength is often provided by reinforcing the flexible material with additional layers or compounds. For example, a layer of steel or braided stainless steel can be incorporated within or around the rubber fuel line to enhance its strength. This reinforcement ensures that the fuel line can withstand the high pressure without kinking or collapsing, which could lead to fuel leaks or system failures.
The challenge lies in finding a balance between flexibility and strength. Materials that are too rigid may not absorb vibrations effectively, leading to increased stress on the fuel lines. On the other hand, materials that are too flexible might not provide sufficient resistance to fuel pressure. Manufacturers often use specialized compounds and construction techniques to achieve the desired balance. For instance, some fuel lines are made with a combination of rubber and a flexible plastic, ensuring both flexibility and durability.
In summary, the material used for car fuel lines must possess a unique combination of properties. It should be flexible enough to accommodate engine vibrations without compromising its structural integrity. At the same time, it needs to be strong to resist the fuel pressure generated by the engine. Achieving this balance ensures that the fuel lines remain reliable and efficient, contributing to the overall performance and longevity of the vehicle's fuel system.
Fuel Line Spray: Normal or Cause for Concern?
You may want to see also
Corrosion Resistance: Materials like stainless steel or coated plastics are chosen to prevent corrosion from fuel
The materials used in car fuel lines are carefully selected to ensure durability and longevity, especially when it comes to preventing corrosion. One of the primary reasons for this choice is the corrosive nature of fuel itself, which can lead to deterioration of the fuel lines over time. To combat this, manufacturers often opt for materials that offer excellent resistance to corrosion, ensuring the fuel lines remain intact and functional.
Stainless steel is a popular choice for this purpose. This material is known for its inherent corrosion resistance, making it ideal for fuel lines. The stainless steel used in these components is often a specific grade, such as 304 or 316, which provides even better protection against corrosion, especially in the presence of fuel. These grades contain a higher percentage of chromium, which forms a protective oxide layer on the surface, preventing further corrosion.
Coated plastics are another option for achieving corrosion resistance. These plastics are treated with a protective layer, often made of materials like zinc or a specialized polymer coating. This coating acts as a barrier, preventing the fuel from coming into direct contact with the plastic, thus reducing the likelihood of corrosion. The coating also provides additional strength and flexibility to the fuel lines, making them more durable.
In some cases, a combination of materials is used to maximize corrosion resistance. For instance, a stainless steel inner core might be surrounded by a protective plastic coating. This design ensures that the fuel comes into contact with a corrosion-resistant material while also benefiting from the flexibility and lightweight nature of plastics. This approach is particularly useful in high-pressure fuel systems where the fuel lines need to withstand varying temperatures and pressures.
The choice of materials for car fuel lines is a critical aspect of vehicle engineering, as it directly impacts the performance and reliability of the fuel system. By selecting materials with superior corrosion resistance, such as stainless steel or coated plastics, manufacturers can ensure that the fuel lines remain in optimal condition, providing efficient fuel delivery to the engine without the risk of corrosion-related failures.
Unveiling the Power of 8AN Fuel Lines: A Comprehensive Guide
You may want to see also
Temperature Tolerance: Lines must handle extreme temperatures, from cold starts to hot engines, without cracking or leaking
The fuel lines in a car are an essential component of the fuel system, responsible for transporting fuel from the tank to the engine. These lines must be designed to withstand the extreme temperature variations that occur in a vehicle's operating environment. From the harsh cold of winter mornings to the scorching heat of summer afternoons, fuel lines play a critical role in ensuring the engine receives the necessary fuel without any leaks or performance issues.
The primary challenge for fuel lines is the temperature range they need to endure. During cold weather, the fuel can become thick and difficult to flow, requiring the lines to expand and contract without any damage. This is particularly critical for the lines that connect the fuel tank to the engine, as these are often exposed to the elements. The material must be flexible enough to accommodate these temperature-induced movements without cracking or breaking.
In contrast, hot engines can cause the fuel lines to expand and potentially damage the lines if they are not made of suitable materials. The fuel lines must be able to withstand the high temperatures without softening or becoming brittle, which could lead to fuel leaks or even engine damage. This is especially important for lines that are routed close to the engine, where they are more susceptible to heat.
To address these temperature challenges, fuel lines are typically made from materials that offer a balance of flexibility and durability. One common material is rubber, which is known for its ability to withstand a wide range of temperatures without cracking. Rubber fuel lines are often reinforced with steel or braided to provide additional strength and flexibility, ensuring they can handle the extreme conditions without failing.
Another material used in fuel line construction is high-temperature plastic, such as nylon or polyether block amide (PEBA). These plastics are engineered to maintain their structural integrity over a broad temperature range, making them suitable for fuel lines. They are often used in combination with rubber in some applications, providing a lightweight and flexible solution that can handle both cold and hot temperatures effectively. The choice of material depends on various factors, including the specific engine requirements, environmental conditions, and the overall design of the fuel system.
Braided Fuel Line Protection: Sealing the Deal
You may want to see also
Compliance and Standards: Fuel lines must meet industry standards and regulations for safety and performance
The materials used in car fuel lines are carefully chosen to ensure they meet stringent industry standards and regulations, primarily for safety and performance reasons. These standards are in place to prevent potential hazards associated with fuel lines, such as leaks, blockages, or failures that could lead to dangerous situations.
One of the primary materials used in fuel lines is rubber, specifically synthetic rubber compounds. These compounds are chosen for their flexibility, durability, and resistance to heat and chemicals. The rubber is formulated to withstand the high temperatures and pressures that can occur in a vehicle's fuel system, ensuring that the fuel lines remain pliable and intact over a wide range of operating conditions. Additionally, rubber is resistant to fuel degradation, which helps prevent the fuel from breaking down the material over time.
Another common material is steel, often used for the inner core of the fuel line. Steel provides excellent strength and rigidity, which is crucial for maintaining the structural integrity of the fuel line, especially in high-pressure applications. The steel core is often surrounded by a protective layer of rubber or a composite material to ensure flexibility and prevent damage from external factors like vibrations or temperature changes.
Compliance with industry standards is essential for fuel lines. These standards, such as those set by the Society of Automotive Engineers (SAE) and the International Organization for Standardization (ISO), dictate the materials, construction, and performance requirements for fuel lines. For example, the SAE J1453 standard specifies the requirements for fuel lines, including their material composition, dimensional tolerances, and performance characteristics. Adherence to these standards ensures that fuel lines are safe, reliable, and compatible with the vehicle's fuel system.
Furthermore, fuel lines must also comply with environmental regulations to minimize the risk of fuel leaks and potential contamination. Manufacturers must ensure that the materials and construction methods used do not lead to the release of harmful substances into the environment. This includes the use of materials that are resistant to fuel leaks and have low permeability to air and moisture, which can help prevent the absorption of contaminants.
In summary, the materials used in car fuel lines are carefully selected to meet industry standards and regulations, ensuring safety, performance, and environmental compliance. The combination of rubber and steel, along with adherence to strict standards, guarantees that fuel lines are reliable and capable of withstanding the demanding conditions of a vehicle's fuel system.
Choosing the Right Fuel Line: Size Matters!
You may want to see also
Frequently asked questions
Car fuel lines are typically made from materials like steel, aluminum, or copper. Steel is the most common due to its durability and ability to withstand high pressure.
Fuel lines are crucial as they transport gasoline or diesel from the tank to the engine. They ensure a steady supply of fuel, allowing the engine to run efficiently and smoothly.
Yes, some fuel lines are constructed from plastic materials like PVC or polypropylene. These are often used in modern vehicles due to their lightweight nature and resistance to corrosion.
It is recommended to inspect fuel lines at least once a year or during routine vehicle maintenance checks. Regular inspections can help identify any cracks, leaks, or damage, ensuring the vehicle's safety and performance.