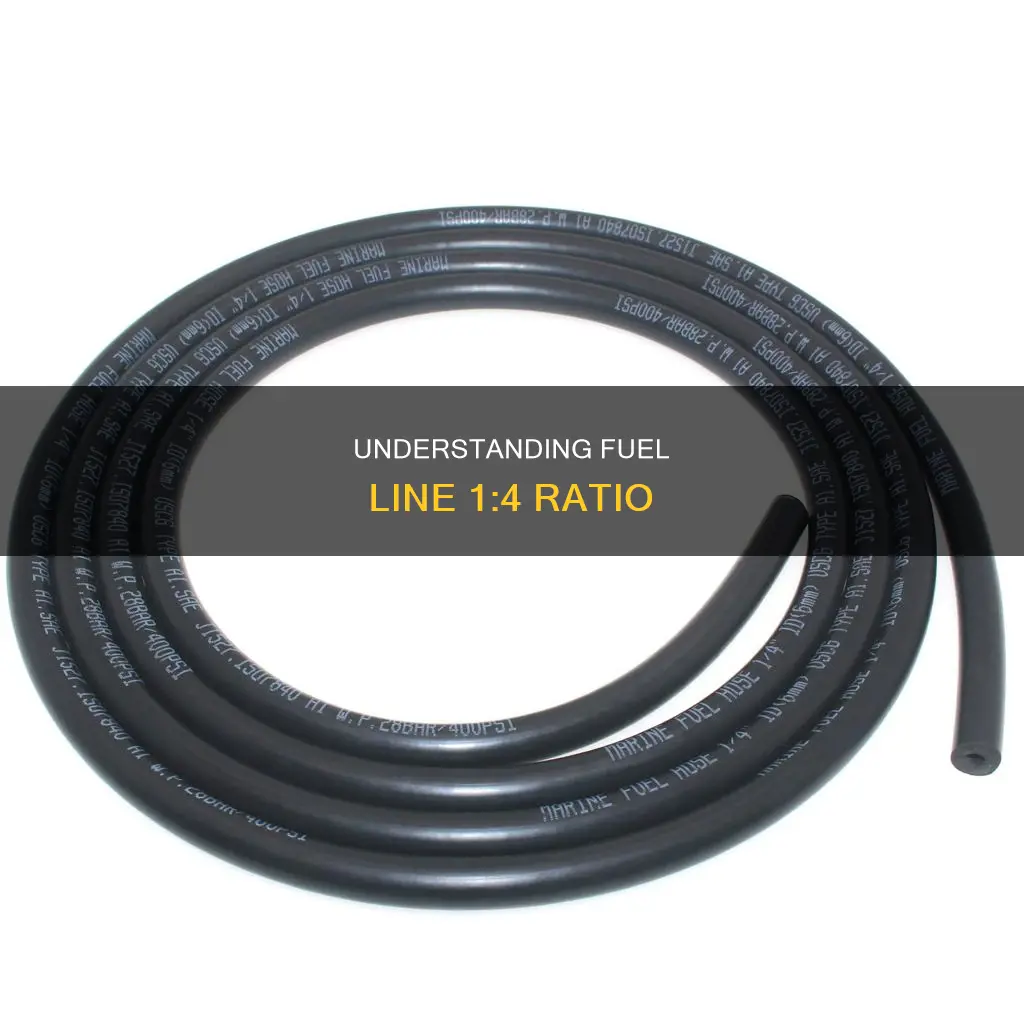
The fuel line 1-4 system is a critical component in the operation of many vehicles and machinery. It is responsible for transporting fuel from the tank to the engine, ensuring a steady supply of energy for optimal performance. Understanding the intricacies of this system is essential for maintenance and troubleshooting, as it can directly impact the efficiency and reliability of the machine. This paragraph aims to provide an overview of the fuel line 1-4, its function, and its significance in various applications.
What You'll Learn
- Fuel Line Material: Different materials like rubber or plastic for fuel lines 1-4
- Fuel Line Routing: Proper placement and routing of fuel lines 1-4 in engines
- Fuel Line Diameter: Sizes of fuel lines 1-4 for optimal fuel flow
- Fuel Line Pressure: Pressure requirements for fuel lines 1-4 in automotive systems
- Fuel Line Compatibility: Compatibility of fuel lines 1-4 with engine types
Fuel Line Material: Different materials like rubber or plastic for fuel lines 1-4
When it comes to fuel lines, the choice of material is crucial for ensuring optimal performance and safety. Different types of fuel lines, such as lines 1 and 4, require specific materials to handle the unique challenges they face. Rubber and plastic are two commonly used materials for these lines, each offering distinct advantages.
Rubber fuel lines are known for their flexibility and durability. This material is ideal for applications where the line needs to withstand constant movement and vibration. Rubber is highly resistant to fuel degradation, ensuring that the fuel remains stable and does not break down over time. It is also resistant to temperature changes, making it suitable for both hot and cold environments. The flexibility of rubber allows it to conform to the vehicle's contours, providing a secure and reliable connection. Additionally, rubber fuel lines are often used in high-pressure applications due to their ability to handle increased stress without compromising performance.
On the other hand, plastic fuel lines offer a lightweight and cost-effective solution. Plastic is known for its excellent resistance to corrosion and chemicals, making it a safe choice for fuel transportation. It is also highly flexible, allowing for easy installation and routing within the vehicle. Plastic lines are often used in situations where weight reduction is essential, as they are lighter than rubber alternatives. However, it's important to note that plastic may not be as durable as rubber in extreme conditions, so it is generally recommended for less demanding applications.
The choice between rubber and plastic for fuel lines 1 and 4 depends on various factors, including the vehicle's specifications, operating conditions, and personal preferences. Rubber provides superior durability and temperature resistance, making it ideal for high-performance vehicles or extreme weather conditions. Plastic, with its lightweight and corrosion-resistant properties, is a practical choice for everyday vehicles or applications where weight is a critical factor.
In summary, when selecting the material for fuel lines 1 and 4, it is essential to consider the specific requirements of the vehicle and the environment it operates in. Rubber and plastic each bring unique advantages, and choosing the right material will ensure the fuel system's longevity and optimal performance. Understanding the characteristics of these materials allows for informed decisions, ensuring a reliable and safe fuel supply.
Understanding Audi's Torque Fuel Line and Fuel Pump System
You may want to see also
Fuel Line Routing: Proper placement and routing of fuel lines 1-4 in engines
The proper routing of fuel lines is crucial for maintaining optimal engine performance and longevity. When it comes to fuel lines 1-4, their placement and routing can significantly impact fuel delivery and overall engine efficiency. Here's an overview of the key considerations for fuel line routing:
Placement and Positioning: Fuel lines should be strategically placed to ensure a direct and unobstructed path from the fuel tank to the engine. Each fuel line (1-4) is typically responsible for supplying fuel to specific cylinders or banks of cylinders. Line 1, for instance, might supply fuel to cylinders 1 and 2, while line 2 serves cylinders 3 and 4, and so on. Proper placement ensures that fuel reaches the intended cylinders at the right pressure and volume. The lines should be positioned close to the engine block to minimize the length of the fuel lines, reducing the risk of fuel degradation and ensuring a faster response time during engine operation.
Routing Considerations: Routing fuel lines requires careful planning to avoid potential issues. The lines should be routed away from high-temperature areas, such as exhaust manifolds and headers, to prevent fuel degradation and potential damage. Additionally, fuel lines should be kept as straight as possible to minimize the risk of kinking, which can restrict fuel flow. It is essential to use appropriate fuel line materials that can withstand engine operating temperatures and pressures. Flexible fuel lines with a suitable inner diameter are often used to accommodate engine movement without restricting flow.
Clamping and Support: Proper clamping is vital to secure the fuel lines in place and prevent any movement that could lead to fuel leaks or damage. Clamps should be tightened securely, ensuring a tight seal without causing damage to the fuel lines or surrounding components. Additionally, consider using fuel line supports or brackets to maintain the lines' shape and prevent excessive bending, which can lead to fuel line failure over time.
Maintenance and Inspection: Regular maintenance and inspection of fuel lines are essential. Over time, fuel lines can develop cracks, leaks, or become brittle due to fuel contamination or engine chemicals. Inspecting the lines for any signs of damage, corrosion, or deterioration is crucial. Replacing worn-out fuel lines with new ones of the same specifications can help ensure optimal engine performance and reliability.
In summary, proper fuel line routing involves careful placement, strategic positioning, and consideration of routing paths to avoid potential issues. By following these guidelines, mechanics can ensure that fuel lines 1-4 deliver fuel efficiently to the engine's cylinders, contributing to improved performance and engine longevity. Regular maintenance and inspection play a vital role in identifying and addressing any potential fuel line-related problems.
The Ultimate Guide to Choosing Lubricant for Fuel Line Installation
You may want to see also
Fuel Line Diameter: Sizes of fuel lines 1-4 for optimal fuel flow
When it comes to fuel lines, understanding the diameter is crucial for ensuring optimal fuel flow in your vehicle. The size of the fuel line, often referred to as the "fuel line diameter," directly impacts the efficiency and performance of your engine. This is especially important when considering different fuel line sizes, such as 1, 2, 3, or 4, as each size has its own set of advantages and applications.
Fuel line diameters are typically measured in inches or millimeters, and the size can vary depending on the make and model of your vehicle, as well as the specific engine requirements. For instance, a fuel line size of 1, also known as a 1-inch fuel line, is commonly used in high-performance vehicles or those with larger engines. This size offers a larger cross-sectional area, allowing for increased fuel flow and improved performance. It is ideal for applications where a substantial amount of fuel needs to be delivered quickly to the engine, such as in racing or high-power applications.
On the other hand, a 2-inch fuel line is often used in smaller vehicles or those with lower engine capacities. This size provides a good balance between fuel flow and flexibility. It is suitable for everyday driving and ensures that the engine receives an adequate supply of fuel without compromising on the overall performance. Similarly, a 3-inch fuel line is even larger and is typically used in specialized applications or custom builds, where maximizing fuel delivery is essential.
The largest size, a 4-inch fuel line, is reserved for extreme performance and high-output engines. This size offers the maximum possible fuel flow, making it ideal for racing or vehicles with oversized engines. However, it is important to note that larger fuel lines may require additional support and modifications to the vehicle's structure to accommodate the increased diameter.
In summary, the fuel line diameter is a critical factor in optimizing fuel flow. Each size, from 1 to 4, serves a specific purpose and should be chosen based on the vehicle's requirements. Understanding these sizes and their applications will help ensure that your vehicle's fuel system operates efficiently, delivering the necessary power and performance. Remember, when dealing with fuel lines, it's essential to consult the manufacturer's guidelines and consider the specific needs of your engine to make the right choice.
Mastering the Fuel Line Mystery: Supply vs. Return
You may want to see also
Fuel Line Pressure: Pressure requirements for fuel lines 1-4 in automotive systems
The fuel lines in an automotive system are crucial components that ensure the efficient delivery of fuel from the tank to the engine. Each fuel line has a specific role and pressure requirements to maintain optimal performance. When it comes to fuel line 1 and 4, understanding their pressure needs is essential for maintaining the overall health of the vehicle's fuel system.
Fuel line 1, often referred to as the primary fuel line, is responsible for supplying fuel from the tank to the engine's fuel injectors or carburetor. It operates under a specific pressure range to ensure a steady and consistent fuel flow. The pressure requirements for fuel line 1 typically range from 20 to 40 psi (pounds per square inch). This pressure range is critical as it ensures that the fuel is delivered at the right rate and volume to the engine, allowing for efficient combustion. Insufficient pressure might result in poor engine performance, while excessive pressure could lead to fuel spray issues and potential engine damage.
Fuel line 4, on the other hand, is usually associated with the return line, which carries the unused fuel back to the tank. This line's primary function is to maintain a slight vacuum to ensure proper fuel flow and prevent air from entering the system. The pressure requirements for fuel line 4 are generally lower, often ranging from 0 to 5 psi. This lower pressure ensures that the fuel returns to the tank without causing excessive pressure buildup, which could lead to fuel system issues.
Maintaining the correct pressure in these fuel lines is crucial for several reasons. Firstly, it ensures that the engine receives the right amount of fuel for optimal performance. Secondly, it helps prevent issues like fuel pump overheating, which can occur if the pressure is too high. Additionally, proper pressure management reduces the risk of fuel leaks and ensures the longevity of the fuel system components.
In automotive systems, fuel line pressure is often regulated by various components such as fuel pumps, pressure regulators, and fuel injectors. These components work together to ensure that the fuel lines operate within the specified pressure ranges. Regular maintenance and inspections of these components are essential to guarantee that the fuel system functions efficiently and reliably.
Understanding the pressure requirements for fuel lines 1 and 4 is a vital aspect of automotive maintenance. It allows mechanics and enthusiasts to identify potential issues and make necessary adjustments to ensure the vehicle's fuel system operates at its best. By adhering to the recommended pressure ranges, vehicle owners can optimize engine performance and extend the lifespan of their fuel system components.
Fuel Return Line Exit: Unveiling the Passenger Side Mystery
You may want to see also
Fuel Line Compatibility: Compatibility of fuel lines 1-4 with engine types
The compatibility of fuel lines with engine types is a critical aspect of vehicle maintenance, ensuring optimal performance and safety. When it comes to fuel lines, specifically those labeled as "1-4," understanding their compatibility with various engine types is essential for any vehicle owner or mechanic. These fuel lines are designed to deliver fuel from the tank to the engine, and their proper fitment is crucial to prevent leaks, engine misfires, and potential hazards.
Engine manufacturers often specify the exact dimensions and types of fuel lines required for their engines. For instance, a fuel line labeled "1-4" might refer to a specific set of lines that are compatible with a particular engine series. These lines are typically designed to withstand the pressure and temperature changes that occur during engine operation. For example, a high-performance engine may require fuel lines with a higher pressure rating to handle the increased fuel flow, while a standard engine might use lines with a lower pressure rating.
Compatibility is not just about physical dimensions but also about the material used. Different engine types may require fuel lines made from specific materials to ensure longevity and performance. For instance, some engines might use fuel lines with a flexible, yet durable, construction to accommodate engine vibrations, while others may need rigid lines to maintain a precise fuel path. The material choice also impacts the fuel line's resistance to corrosion and the effects of fuel type, such as ethanol-blended fuels.
When considering fuel line compatibility, it's important to consult the vehicle's manual or the engine manufacturer's guidelines. These resources provide detailed information on the recommended fuel lines for a specific engine type. Additionally, understanding the engine's fuel system layout is crucial. Some engines may have unique fuel line routing, requiring specific lengths and configurations to ensure proper fuel delivery.
In summary, fuel line compatibility, especially for lines labeled "1-4," is a critical factor in maintaining engine performance and safety. It involves matching the physical dimensions, material properties, and engine-specific requirements to ensure a proper fit. By understanding these compatibility aspects, vehicle owners and mechanics can make informed decisions when selecting and installing fuel lines, contributing to a reliable and efficient vehicle operation.
Unraveling the Mystery: Why Fuel Lines Bubble
You may want to see also
Frequently asked questions
The fuel line 1 4 is a component in a vehicle's fuel system, responsible for delivering fuel from the tank to the engine. It is a crucial part of the fuel injection system, ensuring a steady and controlled supply of fuel for optimal engine performance.
A leaking fuel line can be identified by several signs. These include fuel odors around the vehicle, stains or puddles of fuel under the car, engine misfires or poor performance, and a noticeable decrease in fuel efficiency. If you suspect a leak, it is best to consult a professional mechanic for a thorough inspection.
While some fuel line replacements can be DIY projects, it is generally recommended to have professional assistance, especially for complex vehicles. Fuel lines often require specialized tools and knowledge to remove and install correctly. Improper installation can lead to further issues, so it's best to rely on experienced mechanics to ensure a safe and proper fix.
Fuel line 1 4 failure can be caused by several factors, including age, corrosion, physical damage, and contamination. Over time, fuel lines can deteriorate due to exposure to fuel chemicals, heat, and vibration. Physical damage from accidents or road debris can also lead to leaks. Regular maintenance and inspections can help identify and prevent such failures.