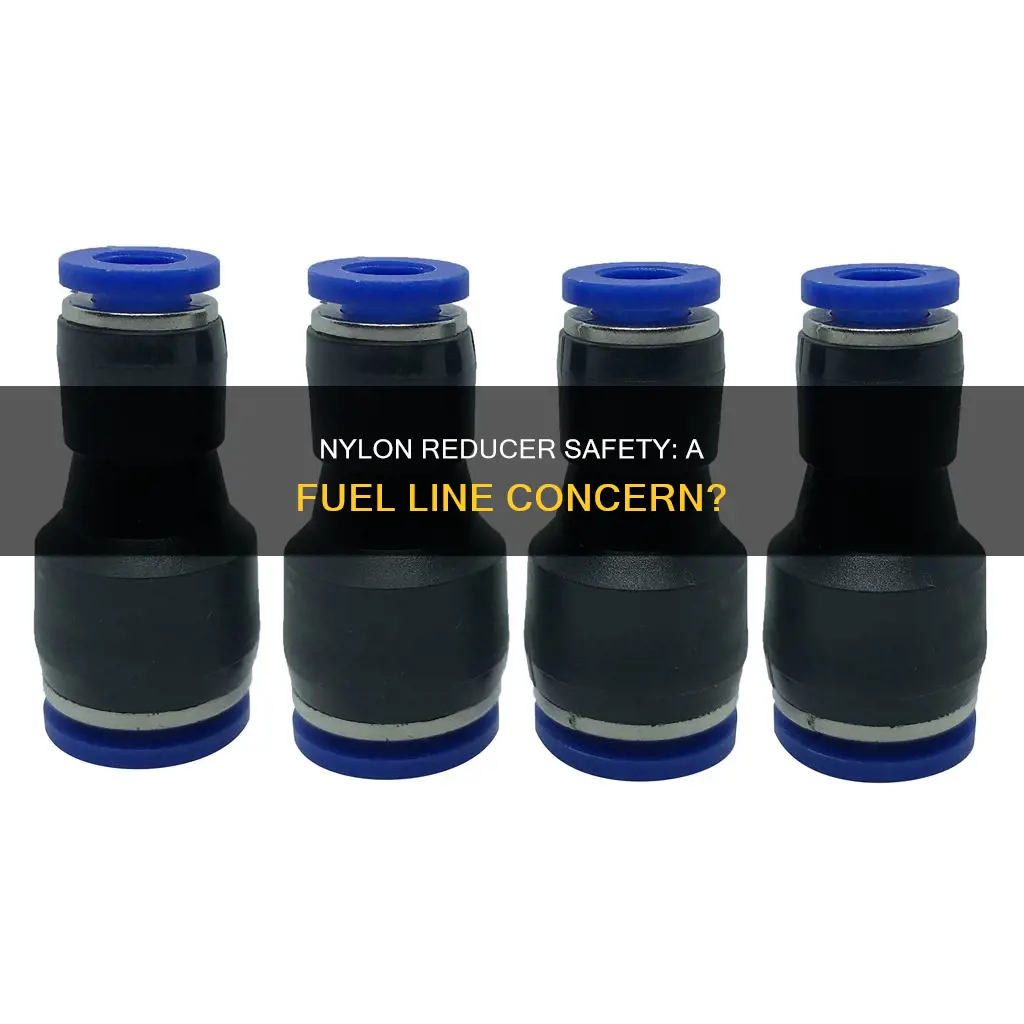
When it comes to automotive maintenance, ensuring the safety and efficiency of fuel lines is crucial. One common question that arises is whether a nylon reducer is a suitable component for fuel lines. This paragraph aims to provide an overview of this topic, addressing the safety and compatibility of nylon reducers in fuel line systems. It will explore the properties of nylon, its potential benefits, and any considerations or risks associated with its use in fuel lines, offering insights to help car owners and mechanics make informed decisions regarding fuel line maintenance and upgrades.
What You'll Learn
- Material Compatibility: Nylon reducers should be compatible with fuel types
- Temperature Tolerance: Ensure nylon reducer can withstand fuel line temperatures
- Flexibility: Nylon's flexibility is crucial for fuel line movement and durability
- Chemical Resistance: Nylon must resist fuel chemicals to prevent degradation
- Installation Guidelines: Follow manufacturer instructions for safe installation and use
Material Compatibility: Nylon reducers should be compatible with fuel types
Nylon reducers, when used in fuel lines, must be carefully considered for their compatibility with the fuel type in question. This is a critical aspect of ensuring the safety and efficiency of any fuel system. The primary concern is the potential for chemical reactions between the nylon material and the fuel, which could lead to degradation, contamination, or even the release of harmful substances.
Nylon, being a synthetic polymer, has specific chemical properties that must be understood. It is generally resistant to many common fuels, such as gasoline and diesel, due to its inert nature. However, certain fuels, especially those with higher alcohol content or those that are more corrosive, can pose challenges. Ethanol, for instance, is a common additive in gasoline and can react with nylon, leading to swelling and potential failure of the material over time.
When selecting a nylon reducer for a fuel line, it is essential to consider the fuel's composition and any additives it may contain. For instance, aviation fuels, which often contain higher levels of ethanol, should be treated with caution. In such cases, it might be necessary to opt for a nylon reducer with a higher resistance to ethanol or to consider alternative materials that are more compatible.
Additionally, the temperature and pressure conditions of the fuel system should be taken into account. Nylon reducers should be able to withstand the typical operating temperatures and pressures of the fuel line without compromising their structural integrity or chemical compatibility. This is particularly important in high-performance applications or environments with extreme temperatures.
In summary, while nylon reducers offer several advantages for fuel lines, such as lightweight and flexibility, their compatibility with specific fuel types is a critical factor. Understanding the chemical properties of the fuel and the nylon material, as well as considering the operating conditions, will help ensure the safe and efficient operation of the fuel system. Always refer to manufacturer guidelines and consult experts when in doubt to make the best choice for your application.
Optimizing Performance: Choosing the Right Fuel Lines for Your 460 Engine
You may want to see also
Temperature Tolerance: Ensure nylon reducer can withstand fuel line temperatures
When considering the use of a nylon reducer for a fuel line, one of the critical factors to evaluate is its temperature tolerance. Fuel lines operate in harsh environments, and the materials used must be able to withstand the extreme temperatures encountered during normal vehicle operation. Nylon, while a versatile and durable material, has specific temperature limitations that need to be understood to ensure the safety and reliability of the fuel system.
Nylon reducers are generally not recommended for fuel lines due to their temperature sensitivity. Nylon can become brittle and lose its flexibility when exposed to high temperatures, which can lead to cracking, splitting, or even failure of the reducer. Fuel lines often experience rapid temperature changes, especially during acceleration and deceleration, and the material must be able to handle these fluctuations without compromising its structural integrity.
The safe operating temperature range for nylon is typically between -40°F and 212°F (or -40°C and 100°C). Beyond these limits, nylon can degrade, leading to reduced performance and potential safety hazards. In automotive applications, fuel lines are exposed to much higher temperatures, often reaching up to 250°F (121°C) or more, especially in high-performance vehicles or those operating in hot climates. Therefore, it is essential to choose a material that can withstand these extreme temperatures.
To ensure temperature tolerance, it is recommended to select a nylon reducer with a higher temperature rating than the expected operating temperature of the fuel line. Some manufacturers offer nylon products with temperature ratings of up to 300°F (149°C), which can provide a safety margin in most automotive applications. Additionally, considering alternative materials such as rubber or specialized nylon compounds designed for fuel line applications can offer better temperature resistance and overall reliability.
In summary, when evaluating the safety of a nylon reducer for a fuel line, temperature tolerance is a critical consideration. Nylon's temperature sensitivity makes it unsuitable for many fuel line applications, especially those with high-temperature requirements. By understanding the temperature limitations of nylon and selecting materials with appropriate ratings, you can ensure the longevity and safety of the fuel system, preventing potential failures and maintaining optimal vehicle performance.
Tribeca Fuel Line Removal: A Step-by-Step Guide for 2006 Models
You may want to see also
Flexibility: Nylon's flexibility is crucial for fuel line movement and durability
Nylon, a versatile synthetic polymer, is renowned for its exceptional flexibility, making it an ideal choice for fuel line applications. The flexibility of nylon is a critical factor in ensuring the safe and efficient operation of fuel lines, especially in automotive and industrial settings. When considering the use of a nylon reducer for fuel lines, understanding the material's flexibility is essential to ensure compatibility and long-term performance.
In the context of fuel lines, flexibility is crucial for several reasons. Firstly, fuel lines are subject to various movements and vibrations during vehicle operation. The engine's movement, acceleration, and deceleration cause the fuel lines to flex and bend. Nylon's inherent flexibility allows it to accommodate these movements without compromising the integrity of the fuel line. This flexibility is particularly important in preventing damage to the fuel line, such as cracks or tears, which could lead to fuel leaks and potential engine issues.
The durability of fuel lines is another aspect where nylon's flexibility plays a vital role. Fuel lines are exposed to harsh environments, including temperature fluctuations, fuel pressure, and chemical exposure. Nylon's flexibility enables it to withstand these conditions without becoming brittle or fragile. It can absorb and distribute stress evenly, reducing the risk of damage and ensuring the long-term reliability of the fuel system. This is especially critical in high-performance vehicles or industrial machinery where fuel lines are subjected to more intense conditions.
Furthermore, the flexibility of nylon allows for easier installation and maintenance. Fuel lines often need to be routed through tight spaces and around various components. Nylon's pliability makes it easier to manipulate and bend, facilitating a secure and efficient installation. This flexibility also simplifies any necessary adjustments or repairs, ensuring that the fuel lines remain in optimal condition throughout their lifespan.
In summary, the flexibility of nylon is a key attribute that makes it a safe and reliable choice for fuel line applications. Its ability to accommodate movement, withstand harsh conditions, and facilitate easy installation and maintenance ensures the long-term durability and performance of fuel systems. When considering the use of a nylon reducer for fuel lines, understanding and appreciating this flexibility is essential for a successful and safe implementation.
Fuel Return Line: Essential or Overrated?
You may want to see also
Chemical Resistance: Nylon must resist fuel chemicals to prevent degradation
Nylon, a versatile polymer, is often utilized in various applications due to its flexibility, durability, and cost-effectiveness. However, when considering its use in fuel lines, a critical aspect to evaluate is its chemical resistance, particularly in the context of fuel chemicals. These chemicals can vary widely, including gasoline, diesel, kerosene, and other additives, each with unique compositions that can potentially degrade materials over time.
The primary concern with nylon in fuel lines is its susceptibility to fuel chemicals. Nylon, while generally resistant to many substances, can be compromised by the harsh conditions present in fuel. For instance, aromatic hydrocarbons in gasoline can cause swelling and softening of the nylon, leading to potential leaks and reduced performance. Similarly, aliphatic hydrocarbons in diesel can also have detrimental effects, causing the material to become brittle and prone to cracking.
To ensure the safety and longevity of a nylon reducer in a fuel line, it is essential to consider the specific chemicals present in the fuel. Different fuels have varying compositions, and some may contain additives or impurities that can accelerate degradation. For example, ethanol, a common additive in many fuels, can cause hydrolysis in nylon, leading to a loss of mechanical properties over time. Therefore, it is crucial to select a nylon grade that has been specifically formulated to withstand the particular fuel chemicals in use.
Manufacturers often provide detailed chemical resistance data for their nylon products, indicating the compatibility of the material with various substances. This information should be carefully reviewed to ensure that the chosen nylon reducer can withstand the specific fuel chemicals in the application. Additionally, regular maintenance and inspection of the fuel lines can help identify any signs of degradation or damage, allowing for timely replacement or repair.
In summary, while nylon can be a suitable material for fuel lines due to its flexibility and cost-effectiveness, its chemical resistance must be carefully evaluated. The choice of nylon grade should be based on the specific fuel chemicals present, and regular maintenance is essential to ensure the safety and efficiency of the fuel system. By considering these factors, engineers and maintenance personnel can make informed decisions regarding the use of nylon reducers in fuel lines, ensuring optimal performance and longevity.
Mastering Fuel Line Maintenance: The Ultimate Guide to Spring Lock Coupling Tools
You may want to see also
Installation Guidelines: Follow manufacturer instructions for safe installation and use
When considering the use of a nylon reducer for fuel lines, it is crucial to prioritize safety and adhere to the manufacturer's guidelines. Installation and usage instructions are designed to ensure the compatibility and integrity of the fuel system, as well as the safety of the vehicle and its occupants. Here are some detailed installation guidelines to follow:
Pre-Installation Checks: Before beginning the installation, inspect the nylon reducer and the fuel line for any signs of damage or defects. Ensure that the reducer is free from cracks, tears, or any other visible imperfections that could compromise its performance. Check the fuel line for any existing damage, ensuring it is in good condition and suitable for the application.
Manufacturer's Instructions: Always refer to the manufacturer's instructions provided with the nylon reducer and fuel line. These instructions are tailored to the specific product and will include detailed steps for installation. They may include specific torque specifications, connection methods, and any unique features or considerations for the particular model. Following these instructions is essential to ensure a proper and safe installation.
Installation Process: Start by cleaning the fuel line and the reducer's connection points to ensure a secure and leak-free fit. Use the appropriate cleaning agents recommended by the manufacturer. Then, carefully align the reducer with the fuel line, ensuring proper orientation. Secure the connection using the specified fasteners or clips, following the torque values provided. Double-check the installation to make sure all components are tightly connected and there are no visible gaps or leaks.
Post-Installation Testing: After the installation is complete, it is crucial to test the system for any leaks or malfunctions. Inspect the connections for any signs of leakage, and start the engine to check for any unusual noises or vibrations. Ensure that the fuel system operates smoothly and efficiently. If any issues are detected, immediately refer to the manufacturer's troubleshooting guide or seek professional assistance.
Regular Maintenance: Proper maintenance is essential to the long-term safety and performance of the fuel system. Regularly inspect the nylon reducer and fuel lines for any signs of wear, damage, or contamination. Clean or replace the components as recommended by the manufacturer to prevent potential issues. By following these maintenance practices, you can ensure the continued reliability of the fuel system.
Remember, the manufacturer's instructions are a vital resource for a safe and successful installation. Adhering to these guidelines will help ensure the compatibility of the nylon reducer with the fuel line and contribute to the overall safety and efficiency of your vehicle's fuel system.
WRX Fuel Line: Discover the Perfect OEM Size
You may want to see also
Frequently asked questions
Yes, nylon reducers can be used for fuel lines, but it's important to choose the right type and size to ensure a secure and leak-free connection. Nylon is a flexible and durable material that can withstand the demands of fuel lines, providing a reliable seal when properly installed.
Nylon reducers offer several benefits. They are lightweight, easy to install, and resistant to fuel-related chemicals, making them a popular choice for fuel system modifications. Additionally, nylon's flexibility allows for some movement, which can be advantageous in certain fuel line applications.
When using a nylon reducer, it's crucial to ensure a tight fit and proper sealing. Over time, fuel can degrade the nylon, so regular inspections and replacements may be necessary. It's also recommended to use a fuel-resistant adhesive or tape to reinforce the connection and provide an extra layer of protection against leaks.