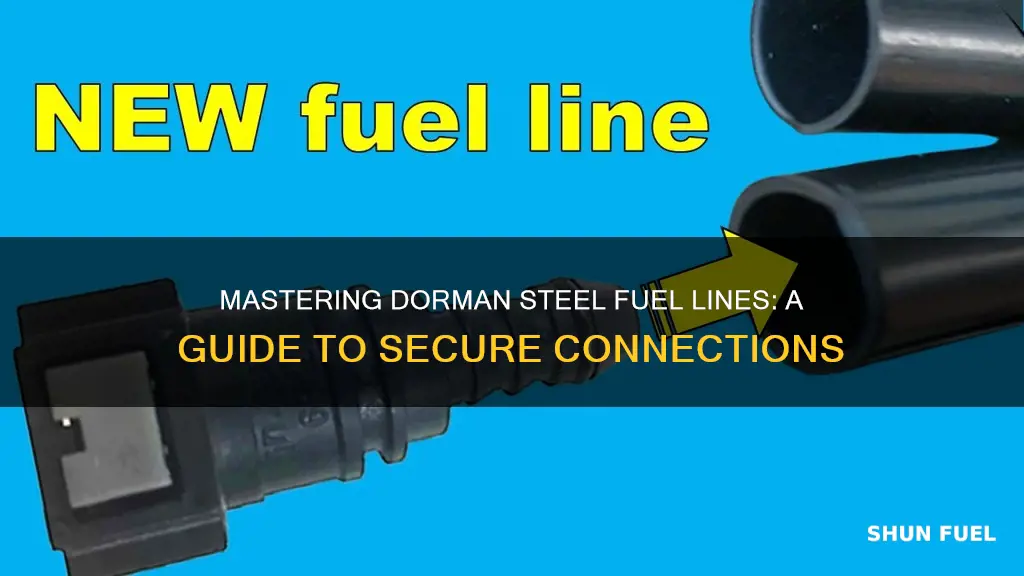
Dorman steel fuel line connectors are essential components for maintaining the integrity of your vehicle's fuel system. These connectors are designed to securely join fuel lines, ensuring a reliable and leak-free connection. By using Dorman steel fuel line connectors, you can effectively prevent fuel leaks, maintain optimal fuel pressure, and enhance the overall performance and safety of your vehicle's engine. This guide will provide a step-by-step overview of how to properly install and use these connectors, ensuring a professional and durable fuel line connection.
Characteristics | Values |
---|---|
Material | Steel |
Compatibility | Dorman fuel lines |
Installation | Easy and straightforward |
Durability | Long-lasting and resistant to corrosion |
Flexibility | Allows for some movement and flexibility |
Temperature Resistance | Suitable for a wide range of temperatures |
Leak-Proof | Ensures a secure connection to prevent fuel leaks |
Cost-Effective | Affordable compared to other fuel line connectors |
Availability | Widely available in automotive stores |
Maintenance | Low maintenance required |
What You'll Learn
- Preparation: Clean and inspect fuel lines, ensuring no damage or debris
- Assembly: Follow manufacturer's instructions for connector placement and tightening
- Fitting: Use the right size and type of connector for your fuel line
- Testing: Check for leaks and ensure proper connection after installation
- Maintenance: Regularly inspect and replace connectors to prevent fuel leaks
Preparation: Clean and inspect fuel lines, ensuring no damage or debris
Before attempting to connect any fuel lines, it's crucial to ensure a clean and safe working environment. Start by thoroughly cleaning the fuel lines to remove any dirt, rust, or debris that may have accumulated over time. This step is essential to prevent contamination and ensure the longevity of your fuel system. Use a suitable cleaning agent, such as a fuel line cleaner, and apply it generously along the length of the lines. Allow the cleaner to work its magic, following the manufacturer's instructions for the best results.
Once the cleaning process is complete, give the lines a thorough rinse to eliminate any remaining cleaner and loose particles. Ensure that you rinse the lines thoroughly to avoid any residue that could attract contaminants. After rinsing, inspect the fuel lines for any signs of damage, cracks, or leaks. Look for any visible corrosion or deterioration, especially at the connections and bends. If any damage is found, it's crucial to replace the affected line to prevent potential fuel leaks and ensure the safety of your vehicle.
Pay close attention to the connectors and fittings. Check for any signs of corrosion or damage that could affect the seal. Ensure that all connectors are in good condition and securely tightened. If any connectors are damaged or worn out, replace them with new ones that are compatible with your fuel line material. This step is vital to guarantee a proper seal and prevent fuel leakage.
Additionally, inspect the surrounding area for any potential sources of contamination or interference. Look for any sharp objects, debris, or foreign matter that could come into contact with the fuel lines during the installation process. Clearing the area ensures a smooth and safe installation, reducing the risk of damage to the lines.
By taking the time to clean and inspect the fuel lines, you are setting a strong foundation for a successful installation. This preparation process ensures that the fuel lines are in optimal condition, ready to be connected securely and efficiently using the appropriate connectors, such as Dorman Steel Fuel Line Connectors.
Honda Foreman 450 Fuel Line: Size and Compatibility Guide
You may want to see also
Assembly: Follow manufacturer's instructions for connector placement and tightening
When working with Dorman steel fuel line connectors, it's crucial to follow the manufacturer's instructions for a successful and secure assembly. These connectors are designed to ensure a tight and reliable connection for fuel lines, so adhering to the provided guidelines is essential. The first step is to locate the appropriate connector for your specific fuel line application. Dorman offers a range of connectors, so identify the one that matches your fuel line diameter and connection type.
Once you have the correct connector, carefully inspect it for any damage or defects. Ensure that the threads are intact and free of any debris or contaminants. Clean the connector and the fuel line ends if necessary, using a suitable solvent to remove any dirt or old sealant. This step is vital to ensure a proper seal and prevent leaks.
Now, proceed with the assembly process. Start by inserting the fuel line into the connector, ensuring it is aligned correctly. Follow the manufacturer's instructions regarding the insertion depth to guarantee a secure fit. Tighten the connector by hand first, then use a wrench or the appropriate tool provided by Dorman to apply the recommended torque. Over-tightening can damage the fuel line, so be cautious and use the correct torque value as a guide.
After tightening, inspect the connection for any signs of leakage. If everything appears secure, test the system by starting the engine and monitoring for any fuel-related issues. If the engine runs smoothly, your assembly is successful. However, if any problems arise, double-check your work and refer to the manufacturer's troubleshooting guide for further assistance.
Remember, each Dorman connector may have unique specifications, so always refer to the provided instructions for the most accurate and safe assembly process. Following these steps will help ensure a reliable fuel system and contribute to the overall performance and longevity of your vehicle.
Mastering the Art of GM Fuel Line Connector Removal: A Step-by-Step Guide
You may want to see also
Fitting: Use the right size and type of connector for your fuel line
When working with fuel lines, ensuring a proper fit is crucial for maintaining the integrity of your fuel system and the overall performance of your vehicle. The right size and type of connector are essential components in this process. Here's a step-by-step guide to help you with the fitting process:
Identify the Connector Type: Different fuel lines may require specific connector types, such as the Dorman steel fuel line connectors. These connectors are designed to securely attach to the fuel lines and provide a reliable seal. Check the specifications of your fuel line and the vehicle's manual to determine the correct connector type. For instance, if your fuel line is made of steel, you'll need steel connectors that are compatible with the material.
Measure and Cut: Accurate measurements are vital. Measure the length of the fuel line you need to connect, ensuring you account for any bends or turns. Then, cut the fuel line to the appropriate length using a sharp, clean blade. This precision ensures a snug fit when inserting the connector.
Prepare the Connector: Before attaching, inspect the connector. Ensure it is free from any damage or debris. If necessary, clean the connector's threads and interior to remove any old fuel line material or contaminants. This step is crucial for a tight seal.
Assembly: Now, it's time to assemble the connector. Start by inserting the fuel line into the connector, ensuring it is aligned correctly. Use a suitable lubricant on the connector threads to facilitate a smooth connection. Tighten the connector securely by hand, and then use a wrench to ensure it is tightened to the recommended torque specifications. Over-tightening can damage the fuel line, so be cautious.
Test for Leaks: After fitting the connector, it's essential to check for any leaks. Turn on the fuel supply and inspect the connection for any signs of fuel escaping. If you notice any leaks, carefully tighten the connector further or re-lubricate the threads and re-insert the fuel line. Ensure the connector is tight enough to prevent any fuel loss.
Remember, using the correct size and type of connector is fundamental to the success of your fuel line installation or repair. Always refer to the manufacturer's guidelines and vehicle specifications for the best results.
Fuel Line Injection: Unlocking Engine Power with Liquid Magic
You may want to see also
Testing: Check for leaks and ensure proper connection after installation
After installing the Dorman steel fuel line connectors, it's crucial to perform a thorough testing procedure to ensure the system's integrity and prevent potential fuel leaks. Here's a step-by-step guide to checking for leaks and verifying the proper connection:
Step 1: Visual Inspection
Start by visually inspecting the entire fuel line system. Look for any visible signs of damage, such as cracks, bends, or kinks in the lines. Ensure that all connectors are securely attached and aligned. Check for any debris or contaminants around the connection points, as these could interfere with the sealing process.
Step 2: Pressure Testing
The most critical step is to perform a pressure test to identify any potential leaks. You can use a fuel line pressure tester or a simple pump and gauge set. Here's how:
- Attach the pressure gauge to the fuel line, ensuring it is connected to the connector you just installed.
- Gradually increase the pressure in the fuel line using the pump or tester. Start with a low pressure and gradually build up.
- Observe the gauge for any drops in pressure, which could indicate a leak. Pay attention to the connector area, as this is where the leak is most likely to occur.
- If a leak is detected, immediately release the pressure and inspect the connection. Clean the area and re-tighten the connector, ensuring it is secure.
Step 3: Bubble Testing (Optional)
For added assurance, you can perform a bubble test using a soapy water solution. This method helps identify even the smallest leaks.
- Mix a small amount of dish soap with water and apply it to the fuel line, focusing on the connector.
- Watch for bubbles forming on the surface, which would indicate a leak. Even a small bubble can signify a potential issue.
- If bubbles are present, carefully inspect the connection and address any leaks as per the pressure test instructions.
Step 4: Functionality Check
After ensuring no leaks, it's essential to check the functionality of the fuel line. Start the engine and monitor its performance. Listen for any unusual noises and observe the engine's behavior. A properly installed connector should allow the fuel to flow smoothly without any issues.
Step 5: Final Inspection
Finally, inspect the entire fuel line system one last time. Check for any signs of fuel accumulation or residue around the connectors. Ensure that all components are clean and free from contaminants. This final inspection ensures that the installation process was successful and that the system is ready for use.
Remember, proper testing is vital to guarantee the safety and efficiency of your fuel system. Always follow the manufacturer's guidelines and recommendations for your specific vehicle and fuel line connectors.
Step-by-Step Guide: Removing Fuel Lines from Ford Explorer Fuel Pump
You may want to see also
Maintenance: Regularly inspect and replace connectors to prevent fuel leaks
Regular maintenance of fuel lines is crucial to ensure the safe and efficient operation of your vehicle. One critical aspect of this maintenance is the inspection and replacement of fuel line connectors, particularly those made from Dormant Steel. These connectors are designed to withstand the corrosive effects of fuel and the pressure it exerts, but they can still deteriorate over time. Neglecting their maintenance can lead to fuel leaks, which pose a significant risk of fire and engine damage.
The inspection process should be thorough and regular. Start by visually checking the connectors for any signs of damage, such as cracks, brittleness, or corrosion. Dormant Steel connectors, in particular, may show signs of wear at the connection points, where the fuel line and the connector meet. Look for any signs of fuel seepage or contamination around these areas. If you notice any issues, it's essential to address them immediately.
When inspecting, also pay attention to the overall condition of the fuel lines. Cracks, kinks, or any other form of damage can compromise the integrity of the line and the connector. Ensure that the fuel lines are securely attached to the connectors and that there is no excessive movement or play in the connections. Any loose or damaged fuel lines should be replaced to prevent potential leaks.
To prevent fuel leaks, it is recommended to replace the connectors and fuel lines at regular intervals, especially if your vehicle is older or has a history of fuel line issues. Over time, the connectors can become less effective due to the constant exposure to fuel and engine heat. Regular replacement ensures that the fuel system remains reliable and safe. It is also a good practice to use high-quality replacement parts that meet or exceed the original specifications to ensure optimal performance.
In addition to visual inspections, it's beneficial to develop a routine maintenance schedule. This schedule should include regular checks for any unusual noises or smells coming from the fuel system, as these can be early indicators of potential issues. By staying proactive and addressing any problems promptly, you can significantly reduce the risk of fuel leaks and maintain the overall health of your vehicle's engine.
Mastering Fuel Return Line Removal: A Comprehensive Guide
You may want to see also
Frequently asked questions
Dorman Steel Fuel Line Connectors are designed to securely join fuel lines, ensuring a tight and leak-free connection. They are made from durable steel, making them suitable for fuel systems that require reliable and long-lasting performance.
Installation is straightforward. First, ensure the fuel lines are clean and free of debris. Then, insert the male connector into the female connector, aligning the threads. Tighten the connector securely using a wrench, being careful not to overtighten to avoid damage.
Yes, Dorman Steel Fuel Line Connectors are generally compatible with various fuel types, including gasoline, diesel, and ethanol blends. However, always check the specific application and fuel system requirements to ensure compatibility.
Yes, the connectors are reusable. Simply remove them by unscrewing them from the fuel line, clean any debris or fuel residue, and store them for future use. Ensure the threads remain intact and undamaged during the removal process.
You will typically need a standard socket or wrench that matches the connector's thread size. It's recommended to use a tool with a comfortable grip to ensure a secure and controlled tightening process.