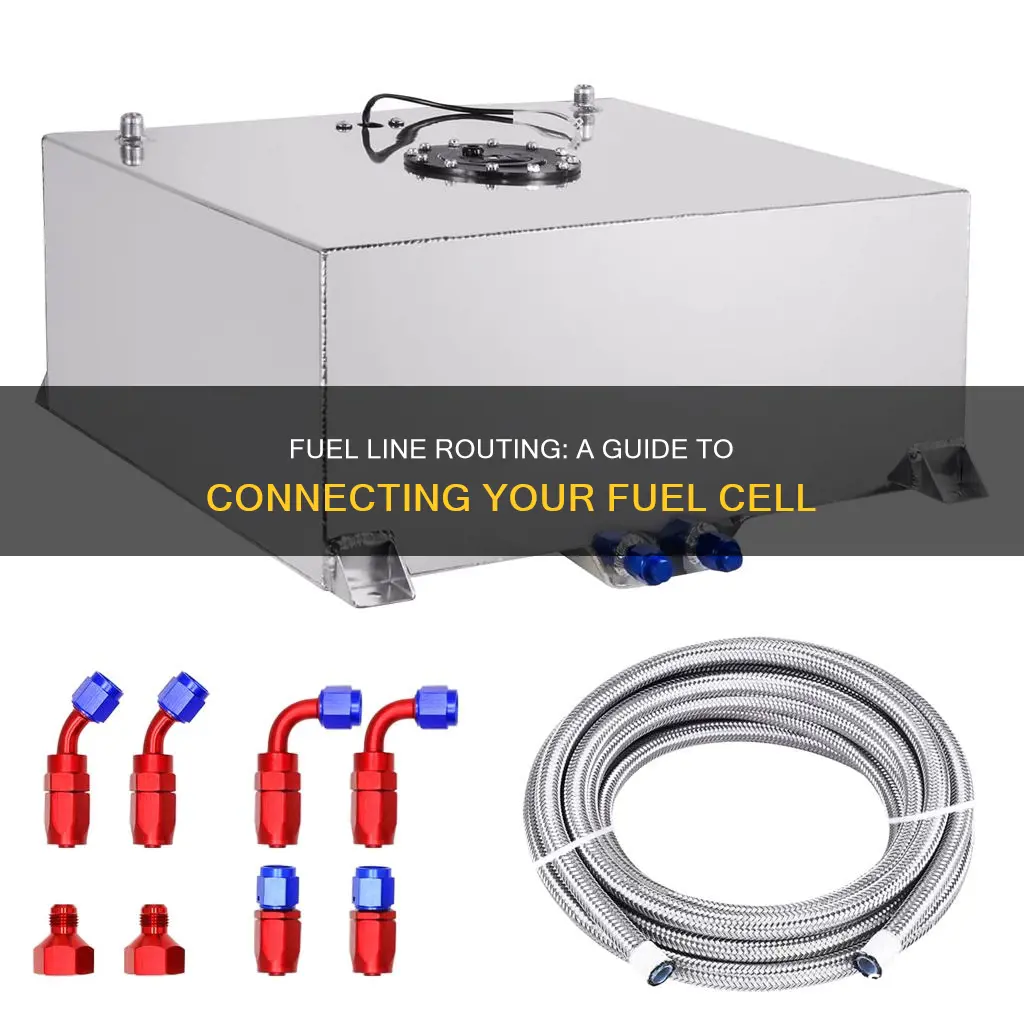
Running fuel lines from a fuel cell is a crucial step in any fuel-cell-powered project, whether it's a vehicle, a portable generator, or a stationary power system. This process involves carefully routing the fuel lines to ensure efficient and safe operation. The lines must be connected to the fuel cell, which converts chemical energy into electricity, and then to the fuel supply, typically a tank or a reservoir. Proper installation requires attention to detail, including selecting the right materials, ensuring secure connections, and considering factors like pressure, temperature, and vibration to maintain optimal performance and prevent leaks. Understanding the specific requirements of your fuel cell and fuel system is essential to ensure a successful and reliable setup.
What You'll Learn
- Location and Routing: Plan optimal paths for fuel lines, avoiding heat sources and sharp bends
- Clamping and Support: Secure fuel lines with appropriate clamps and brackets for stability
- Fuel Compatibility: Ensure fuel lines are compatible with the fuel type to prevent leaks
- Ventilation: Provide adequate ventilation to prevent fuel buildup and potential hazards
- Testing and Inspection: Regularly test and inspect fuel lines for leaks and damage
Location and Routing: Plan optimal paths for fuel lines, avoiding heat sources and sharp bends
When planning the routing of fuel lines from a fuel cell, it's crucial to consider the optimal path that ensures efficient and safe operation. The primary goal is to minimize potential hazards and maintain the integrity of the fuel system. Here's a detailed guide on how to achieve this:
Location and Placement: Begin by identifying the ideal locations for the fuel cell and the associated components. Typically, fuel cells are positioned in areas with good ventilation to prevent the accumulation of flammable gases. Place the fuel cell in a well-ventilated space, preferably with a dedicated ventilation system to expel any potential hazards. The fuel lines should be positioned to avoid direct contact with heat sources, such as engines or exhaust systems, as high temperatures can accelerate fuel evaporation and increase the risk of leaks.
Routing Strategy: Design a routing strategy that prioritizes safety and efficiency. Aim for a straight path whenever possible to reduce the risk of sharp bends, which can cause stress on the fuel lines and potentially lead to leaks. Utilize 90-degree elbows and fittings at strategic points to change the direction of the fuel lines without compromising their integrity. Ensure that the fuel lines are not routed through areas with excessive vibration or movement, as this can cause damage over time.
Avoiding Heat and Vibration: One of the critical aspects of routing is to keep the fuel lines away from heat sources. Use heat shields or insulation materials to protect the fuel lines if they must pass near hot components. Similarly, avoid routing fuel lines through areas with high vibration, such as engine compartments, as this can lead to premature wear and potential leaks. Consider the long-term effects of heat and vibration on the fuel lines and choose materials that can withstand these conditions.
Bending Radii: Maintain a minimum bending radius for the fuel lines to prevent kinking and potential damage. The specific radius required depends on the material and diameter of the fuel line, but generally, a radius of at least 25 times the diameter is recommended. This ensures that the fuel lines can flex without causing stress or compromising their structural integrity.
Regular Inspection: Implement a regular inspection schedule for the fuel lines to identify any signs of wear, damage, or potential issues. Visual inspections should be conducted periodically, and any areas with visible wear or corrosion should be addressed promptly. Additionally, consider using pressure-sensitive tape or markers to indicate potential problem areas, ensuring that any issues are caught early.
By following these guidelines, you can ensure that the fuel lines are routed optimally, avoiding heat sources and sharp bends, which is essential for the safe and efficient operation of the fuel cell system. Proper planning and attention to detail will contribute to a reliable and long-lasting fuel supply.
Understanding Fuel Lines: The Return Line's Role
You may want to see also
Clamping and Support: Secure fuel lines with appropriate clamps and brackets for stability
When running fuel lines from a fuel cell, ensuring the lines are properly clamped and supported is crucial for maintaining the system's integrity and preventing leaks. The fuel lines should be secured at regular intervals to provide stability and reduce the risk of damage during operation. Here's a detailed guide on how to achieve this:
Clamping System:
Start by selecting the right type of clamps for your fuel lines. The clamps should be designed to securely hold the lines in place without causing any damage. Metal or heavy-duty plastic clamps are commonly used for this purpose. Ensure the clamps have a good grip and are adjustable to accommodate different line sizes. Install the clamps at various points along the fuel lines, especially where the lines might experience more strain or movement. For example, you can place a clamp near the fuel cell, at regular intervals along the line, and at the point where the line connects to the engine or other components. Tighten the clamps firmly but avoid over-tightening to prevent line damage.
Brackets and Support Structures:
In addition to clamps, consider using brackets and support structures to reinforce the fuel lines. Brackets can be made from sturdy materials like aluminum or steel and should be designed to fit the specific layout of your fuel system. These brackets can be attached to the fuel cell, engine block, or any other stable part of the vehicle's frame. By securing the fuel lines to these brackets, you provide an extra layer of support, especially in areas where the lines might sag or rub against other components. Ensure that the brackets are securely fastened and can withstand the pressure and movement of the fuel lines.
Routing and Placement:
As you run the fuel lines, maintain a neat and organized route to avoid tangling or interference with other components. Keep the lines as straight as possible to minimize stress points. Avoid routing the lines through areas where they might be damaged by heat, vibration, or sharp edges. Use protective sleeves or conduits if necessary to shield the lines from potential hazards. Proper placement and routing will also make it easier to inspect and maintain the system in the future.
Regular Inspection:
After securing the fuel lines, it's essential to conduct regular inspections to ensure the clamps and brackets remain effective. Check for any signs of wear, corrosion, or damage to the clamps and replace them if necessary. Look for any leaks or signs of fuel line failure, especially at the clamp and bracket connections. Regular maintenance will help identify potential issues early on and ensure the long-term reliability of your fuel system.
By following these clamping and support techniques, you can create a robust and secure fuel line system, ensuring the safe and efficient operation of your fuel cell setup. Remember, proper installation and regular maintenance are key to avoiding costly repairs and potential safety hazards.
Fixing Fuel Leaks: The Best Tape for Your Car's Safety
You may want to see also
Fuel Compatibility: Ensure fuel lines are compatible with the fuel type to prevent leaks
When it comes to fuel lines, compatibility is key. Different fuels have varying properties, and using the wrong type of fuel line can lead to leaks, reduced performance, and potential safety hazards. Here's a detailed guide on ensuring fuel compatibility:
Understand Fuel Properties: Begin by understanding the properties of the fuel you are using. Different fuels have different densities, viscosities, and chemical compositions. For example, gasoline and diesel have distinct characteristics that require specific fuel line materials to handle them effectively. Research the fuel's specifications to determine its compatibility with various materials.
Select the Right Material: Fuel lines should be made from materials that can withstand the chemical and physical properties of the fuel. Common materials include rubber, vinyl, and synthetic compounds. For instance, natural rubber is commonly used for gasoline fuel lines due to its flexibility and resistance to gasoline dissolution. However, for diesel fuel, synthetic compounds like nitrile or neoprene are preferred as they offer better resistance to fuel dissolution and aging.
Consider Temperature and Pressure: Fuel lines must also be compatible with the temperature and pressure conditions of the fuel system. Extreme temperatures can cause fuel lines to expand or contract, leading to potential leaks. Ensure that the chosen material can handle the operating temperature range of your fuel system. Additionally, consider the pressure requirements; some fuels may require specific fuel lines with reinforced layers to withstand higher pressure.
Test and Inspect: Before installation, thoroughly test and inspect the fuel lines. Perform pressure tests to ensure they can withstand the system's operating pressure. Check for any signs of damage, cracks, or leaks. If any issues are found, replace the fuel lines with compatible alternatives. Regular inspections are crucial, especially in high-temperature environments or after any modifications to the fuel system.
Maintain and Replace: Proper maintenance is essential to ensure long-term compatibility. Regularly check for any signs of degradation, such as cracking or swelling, and replace the fuel lines if necessary. Over time, fuel lines may degrade due to fuel exposure, temperature fluctuations, or mechanical stress. By staying proactive and replacing worn-out lines, you can prevent leaks and maintain a safe and efficient fuel system.
Kawasaki Brute Force 750 Fuel Line Sizing Guide
You may want to see also
Ventilation: Provide adequate ventilation to prevent fuel buildup and potential hazards
Ventilation is a critical aspect of any fuel cell system, and it plays a vital role in ensuring the safety and efficiency of your setup. When running fuel lines from a fuel cell, proper ventilation is essential to prevent the accumulation of hazardous substances and potential dangers. Here's a detailed guide on how to achieve this:
Understanding the Risks: Before implementing any ventilation system, it's crucial to understand the potential hazards associated with fuel cells. Fuel cells produce hydrogen gas, which, when combined with oxygen, creates electricity. However, this process also generates small amounts of carbon monoxide and other byproducts. If these gases accumulate in a confined space, they can pose serious health risks, including asphyxiation and potential fire hazards. Therefore, adequate ventilation is key to mitigating these risks.
Ventilation Design: Start by assessing the space where your fuel cell system is installed. Ensure that the area has proper airflow and is well-ventilated. If the space is enclosed or has limited ventilation, consider the following:
- Exhaust Systems: Install a robust exhaust system that can efficiently remove the generated gases. This system should be designed to handle the specific byproducts of your fuel cell. For instance, carbon monoxide detectors and exhaust fans can be employed to ensure any harmful gases are promptly vented outside.
- Ventilation Fans: Place strategically positioned ventilation fans to encourage airflow. These fans should be powerful enough to create a continuous flow of air, preventing the buildup of gases. Ensure the fans are designed to handle the volume of air required for your specific setup.
- Air Intakes: Consider adding air intakes to bring in fresh outdoor air, diluting the concentration of any generated gases. This is especially important if your fuel cell is located in a confined space.
Maintenance and Regular Checks: Adequate ventilation is not a one-time task; it requires regular maintenance and checks.
- Periodically inspect the ventilation system for any blockages or damage. Clean or replace filters as recommended by the manufacturer to ensure optimal performance.
- Monitor the system's efficiency by checking for any unusual odors or gas buildup. This proactive approach can help identify potential issues before they become dangerous.
- Keep a record of maintenance activities and any issues encountered to ensure the system's longevity and safety.
By implementing a well-designed ventilation system and adhering to regular maintenance practices, you can significantly reduce the risks associated with fuel cell operations. This ensures a safer environment for both the system and its operators, allowing for efficient and reliable power generation. Remember, proper ventilation is a fundamental step towards a successful and safe fuel cell setup.
Thawing Frozen Fuel Lines: A Guide to Winter Car Care
You may want to see also
Testing and Inspection: Regularly test and inspect fuel lines for leaks and damage
When it comes to maintaining a fuel cell system, regular testing and inspection of fuel lines are crucial to ensure optimal performance and safety. Fuel lines are responsible for transporting fuel from the storage tank to the engine, and any leaks or damage can lead to significant issues. Here's a detailed guide on how to approach this task:
Start by familiarizing yourself with the fuel cell system's layout. Locate the fuel lines, which are typically made of rubber or synthetic materials, and understand their path from the fuel tank to the engine. Inspect the lines for any visible signs of wear, cracks, or damage. Look for any bulges, kinks, or areas where the material might have deteriorated over time. It's essential to identify potential weak points that could lead to leaks.
The testing process should involve both visual inspections and practical methods. Begin with a visual check, looking for any signs of fuel leakage around the connections, fittings, and bends in the lines. Even a small amount of fuel can indicate a potential issue. Pay close attention to the areas where the fuel lines connect to the fuel tank, pump, and engine. Any corrosion or damage to these connections can lead to leaks.
Next, perform a pressure test to ensure the integrity of the fuel lines. This can be done using a fuel line pressure tester, which is a specialized tool designed for this purpose. Connect the tester to the fuel line and apply the recommended pressure. Observe the gauge for any drops in pressure, which could indicate a leak. Ensure that the pressure is held steady for the specified duration as per the manufacturer's guidelines.
Additionally, consider using a dye test to detect leaks. This method involves adding a small amount of fuel dye to the fuel tank and then checking for the dye's presence in other areas, such as under the car or near the fuel lines. If the dye is found in unexpected places, it indicates a potential leak. This non-invasive test can help identify issues that might not be visible during a visual inspection.
Regular maintenance and testing are key to preventing costly repairs and ensuring the longevity of your fuel cell system. By following these steps, you can effectively inspect and test the fuel lines, catching any potential issues before they become major problems. Remember, proper maintenance will contribute to the overall reliability and efficiency of your fuel cell setup.
Backwards Fuel Lines: A Recipe for Disaster
You may want to see also
Frequently asked questions
Running fuel lines from a fuel cell to the engine requires careful planning and installation. Start by identifying the fuel cell's output port and the engine's fuel inlet. Use flexible fuel lines with the appropriate diameter to ensure a good flow rate. Route the lines through the engine bay, keeping them away from hot surfaces and sharp edges. Secure the lines with clips or ties to prevent movement and potential damage.
Securing fuel lines properly is crucial to prevent leaks and ensure safety. Use fuel line clips or ties specifically designed for fuel applications. Space the clips at regular intervals to avoid excessive tension, which can lead to cracks. Avoid routing the lines through sharp bends or kinks, as these can cause stress points and potential leaks. Regularly inspect the lines for any signs of damage or wear.
No, it's essential to use fuel lines specifically designed for the fuel cell and engine system. Regular automotive fuel lines may not withstand the unique properties of the fuel cell's output. Look for fuel lines made from materials compatible with the fuel type (e.g., ethanol-resistant for ethanol blends). Ensure the lines have the correct diameter to handle the desired fuel flow rate. Always refer to the manufacturer's guidelines for the best results.