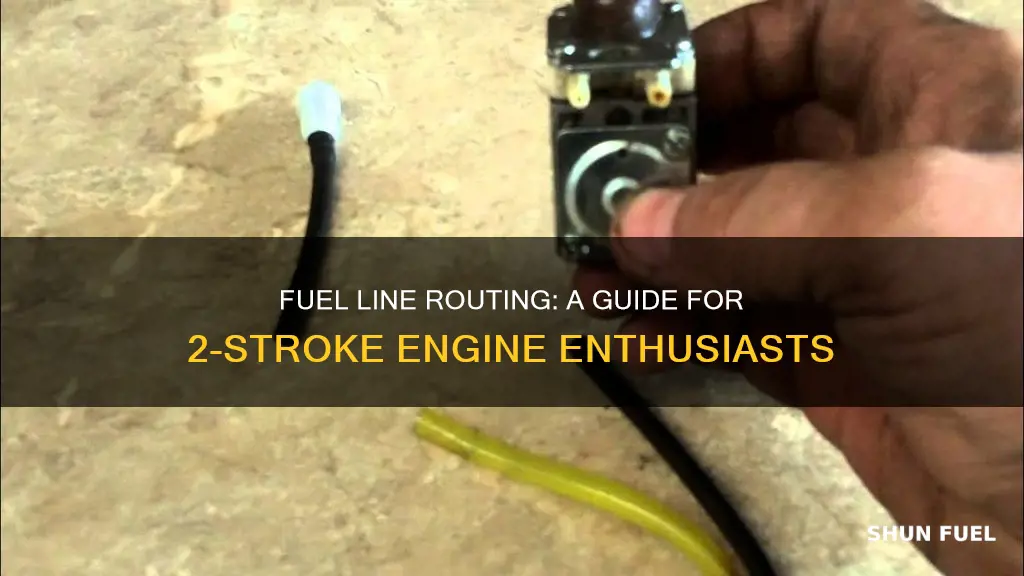
Running fuel lines on a 2-stroke engine is a crucial step in ensuring optimal performance and longevity. This process involves connecting the fuel supply to the engine's carburetor, where it mixes with air and ignites during combustion. Proper installation is essential to prevent fuel leaks and ensure efficient operation. The fuel line should be routed carefully, avoiding sharp bends and tight spaces, to maintain a steady flow of fuel to the engine. Additionally, using the right type of fuel line material and size is vital to match the engine's requirements. This guide will provide a step-by-step approach to installing fuel lines, covering everything from choosing the right components to ensuring a secure and reliable connection.
Characteristics | Values |
---|---|
Fuel Line Material | Typically made of plastic or rubber, with a flexible design to accommodate engine movement. |
Fuel Line Diameter | Varies depending on engine size and power, but commonly ranges from 3/8" to 1/2" in diameter. |
Fuel Line Length | Depends on the engine's layout and design, but usually extends from the fuel tank to the carburetor or fuel injection system. |
Fuel Line Routing | Fuel lines should be routed away from hot engine components to prevent damage and ensure proper fuel flow. |
Fuel Line Flexibility | Essential for 2-stroke engines as they require the fuel line to move with the engine's components during operation. |
Fuel Line Clamping | Securely fastened to the engine block or frame using clamps or brackets to maintain a tight connection. |
Fuel Line Filter | Often includes a fuel filter to prevent contaminants from entering the engine, ensuring clean fuel delivery. |
Fuel Line Pressure | The fuel line should be able to withstand the pressure generated by the fuel pump to deliver fuel efficiently. |
Fuel Line Maintenance | Regular inspection and cleaning are necessary to prevent clogs and ensure optimal engine performance. |
What You'll Learn
- Fuel Injection: Direct fuel injection into the engine's cylinder for optimal performance
- Fuel Pump: Choose a pump with adequate flow rate for the engine's needs
- Fuel Line Material: Select a durable material like rubber or plastic for the fuel line
- Fuel Line Routing: Route the fuel line away from heat sources and vibrations
- Fuel Line Length: Keep the fuel line length to a minimum to reduce pressure drops
Fuel Injection: Direct fuel injection into the engine's cylinder for optimal performance
Direct fuel injection, often referred to as fuel injection, is a crucial aspect of optimizing the performance of a two-stroke engine. This system involves injecting fuel directly into the engine's cylinder, ensuring a precise and efficient combustion process. By bypassing the carburetor, fuel injection offers several advantages that contribute to improved power, fuel efficiency, and reduced emissions.
The process begins with a specialized fuel injection system, which can be either electronic or mechanical. In an electronic system, a fuel injection controller precisely manages the fuel delivery based on engine speed, load, and other parameters. This controller receives input from various sensors, such as the engine's speed sensor and temperature sensor, to make real-time adjustments. The mechanical system, on the other hand, relies on a cam-driven fuel pump and injectors to deliver fuel at the right time.
When implementing fuel injection, the fuel line plays a critical role. It connects the fuel tank to the injection system, ensuring a continuous supply of fuel under pressure. The line should be made of a suitable material, such as rubber or plastic, to withstand the fuel's properties and engine operating temperatures. Proper routing and insulation of the fuel line are essential to prevent leaks and ensure a consistent fuel supply to the injectors.
Direct fuel injection offers several benefits. Firstly, it provides better fuel atomization, resulting in a more complete combustion process. This leads to increased power output and improved engine performance. Secondly, fuel injection allows for precise control over the fuel-air mixture, enabling the engine to run leaner, which can enhance fuel efficiency. Additionally, the direct injection of fuel reduces the risk of carburetor-related issues, such as carbon buildup and fuel contamination.
In summary, fuel injection, with its direct fuel delivery to the engine's cylinder, is a powerful tool for enhancing two-stroke engine performance. It offers improved control over the fuel-air mixture, increased power, and better fuel efficiency. By carefully selecting the appropriate fuel injection system and ensuring the fuel line is properly installed and maintained, enthusiasts can unlock the full potential of their two-stroke engines while enjoying a more efficient and environmentally friendly power source.
Mastering the Art of Fuel Line Removal: A Guide for 1998 Sierra 2500 Owners
You may want to see also
Fuel Pump: Choose a pump with adequate flow rate for the engine's needs
When it comes to fueling a two-stroke engine, selecting the right fuel pump is crucial for optimal performance and longevity. The primary role of the fuel pump is to deliver the correct amount of fuel to the engine at the right time, ensuring efficient combustion. Here's a detailed guide on choosing a fuel pump with an adequate flow rate for your two-stroke engine:
Understanding Flow Rate: The flow rate of a fuel pump is measured in liters per minute (L/min) or gallons per minute (GPM). It indicates the volume of fuel the pump can deliver in one minute. For a two-stroke engine, the flow rate should be carefully matched to the engine's requirements. Insufficient flow might result in poor performance, while an overly high flow rate can lead to fuel wastage and potential engine damage.
Engine Displacement and Flow Rate: The flow rate needed for your fuel pump is directly related to the engine's displacement. Displacement refers to the volume of the engine's combustion chamber. Larger engines with higher displacement require more fuel, thus demanding a pump with a higher flow rate. For instance, a 50cc two-stroke engine typically needs a fuel pump with a flow rate of around 1-2 L/min, while a 150cc engine might require 3-5 L/min or more.
Consider Engine Speed and Load: The engine's speed and load also play a significant role in determining the required flow rate. Higher engine speeds and increased load (such as during acceleration or climbing) demand more fuel. Therefore, the fuel pump should be capable of delivering the necessary amount of fuel to meet these demands.
Choosing the Right Pump: When selecting a fuel pump, consider the specific requirements of your two-stroke engine. Consult the manufacturer's specifications or technical manuals to determine the recommended flow rate. It's essential to choose a pump that provides a consistent and stable fuel supply, ensuring the engine operates efficiently across various operating conditions.
Additional Tips: Opt for a fuel pump with a built-in pressure regulator to maintain optimal fuel pressure. This feature ensures that the fuel is delivered at the correct pressure, which is vital for proper engine operation. Additionally, consider the pump's durability and reliability, especially if it's intended for frequent use or harsh environments. Regular maintenance and cleaning of the fuel pump will also contribute to its longevity and performance.
Wedeater Fuel Lines Reversed: A Recipe for Disaster?
You may want to see also
Fuel Line Material: Select a durable material like rubber or plastic for the fuel line
When it comes to choosing the right fuel line for a 2-stroke engine, material selection is crucial for durability and performance. The fuel line is responsible for delivering gasoline directly to the carburetor, and it must withstand the high pressure and temperature fluctuations that occur during engine operation.
Rubber is a popular choice for fuel lines due to its inherent flexibility and resilience. It can absorb vibrations and flex with the engine's movement, ensuring a consistent fuel supply. Natural rubber is known for its excellent resistance to gasoline, making it a reliable option for 2-stroke engines. However, it's important to note that rubber fuel lines may require more frequent inspections and replacements due to potential aging and cracking over time.
Another excellent material for fuel lines is high-density polyethylene (HDPE) plastic. HDPE is lightweight, flexible, and highly resistant to gasoline and other fuels. Its durability makes it an ideal choice for 2-stroke engines, as it can handle the corrosive effects of gasoline without degradation. Additionally, HDPE is less prone to kinking and has a longer lifespan compared to rubber, making it a low-maintenance option.
In some cases, a hybrid approach can be beneficial. Combining rubber and plastic can create a fuel line that offers the best of both materials. For instance, a rubber inner tube surrounded by a protective plastic outer layer can provide flexibility and gasoline resistance simultaneously. This hybrid design ensures the fuel line remains durable and reliable, even in demanding conditions.
When installing the fuel line, ensure that it is properly secured and protected from any sharp edges or components that could cause damage. Regularly inspect the fuel line for any signs of wear, cracks, or leaks, and replace it if necessary to maintain optimal engine performance.
Unveiling the Fuel Line Mystery: Boeing 747's Fuel Line Size Explained
You may want to see also
Fuel Line Routing: Route the fuel line away from heat sources and vibrations
When it comes to fuel line routing on a 2-stroke engine, proper placement is crucial to ensure optimal performance and longevity. One essential aspect is routing the fuel line away from heat sources and vibrations, which can cause significant damage over time. Here's a detailed guide on how to achieve this:
Start by identifying potential heat sources in the engine bay. These could include exhaust manifolds, headers, or even the engine block itself, especially in older designs. Heat can cause fuel to evaporate, leading to potential starting issues and reduced performance. To mitigate this, route the fuel line as far away from these heat sources as possible. Consider running the line along the side of the engine or even underneath it, ensuring it doesn't come into direct contact with hot components. Insulating the fuel line with heat-resistant materials can also be beneficial, especially if the engine operates in high-temperature environments.
Vibrations are another critical factor to consider. The fuel line should be secured firmly to the engine and frame to minimize movement. Route the line away from areas prone to vibrations, such as near the exhaust system or any moving parts. Secure the line with appropriate clamps or ties, ensuring it doesn't rub against other components, as this can lead to wear and tear. Properly routing the fuel line to avoid these vibration hotspots will contribute to a smoother-running engine.
Additionally, when routing the fuel line, maintain a slight downward angle to allow any accumulated fuel to drain back into the tank. This simple measure helps prevent fuel buildup and ensures that the engine receives fresh fuel with each cycle. Keep the line as short as possible to minimize the risk of fuel degradation and potential blockages.
Remember, the goal is to create a clean, efficient fuel supply system. By routing the fuel line away from heat and vibration sources, you'll contribute to a more reliable and powerful 2-stroke engine. This practice is especially important for high-performance applications where every detail matters.
Choosing the Right Primer for Boat Fuel Tanks Below Waterline
You may want to see also
Fuel Line Length: Keep the fuel line length to a minimum to reduce pressure drops
When it comes to optimizing the fuel system of a 2-stroke engine, one crucial aspect often overlooked is the length of the fuel line. The fuel line, a vital component in delivering gasoline from the tank to the carburetor, can significantly impact engine performance and efficiency. Here's why keeping the fuel line length to a minimum is essential:
Reducing Pressure Drops: The primary concern with fuel lines is the potential for pressure drops, especially as the line length increases. As fuel flows through the line, it encounters resistance, which can lead to a decrease in pressure. This pressure drop becomes more pronounced over longer distances. When the fuel reaches the carburetor, a shorter line ensures that the pressure remains adequate, allowing for efficient atomization and mixing with air. Adequate pressure is crucial for proper combustion, ensuring the engine runs smoothly and with optimal power output.
Minimizing Air Induction: Another critical aspect is the potential for air induction issues. Longer fuel lines can inadvertently introduce more air into the system, which can lead to improper fuel-air mixture ratios. This can result in poor engine performance, including reduced power, increased fuel consumption, and even starting difficulties. By keeping the fuel line short, you minimize the risk of air induction, ensuring that the carburetor receives the precise amount of fuel required for efficient combustion.
Engine Reliability and Longevity: Over time, longer fuel lines can lead to increased wear and tear on the engine components. The constant flow of fuel through a longer line can cause erosion of internal engine parts, particularly in the carburetor and intake manifold. This erosion can result in reduced engine performance, increased maintenance requirements, and even premature engine failure. By maintaining a short fuel line, you contribute to the overall reliability and longevity of your 2-stroke engine.
Optimizing Engine Tuning: The length of the fuel line also plays a role in engine tuning. Longer lines may require adjustments to the carburetor settings to compensate for the increased distance. This can be a complex process, requiring careful calibration to ensure the engine operates at its best. By keeping the fuel line short, you simplify the tuning process, allowing for easier optimization of the engine's performance characteristics.
In summary, when working on a 2-stroke engine, it is imperative to keep the fuel line length to a minimum. This simple modification can significantly enhance engine performance, reduce pressure drops, minimize air induction issues, and contribute to the overall reliability and longevity of the engine. Remember, in the world of 2-stroke engine tuning, every small detail matters, and the fuel line length is a critical one to consider.
Road King Fuel Line Removal: A Step-by-Step Guide
You may want to see also
Frequently asked questions
Before installing the fuel line, ensure it is the correct size and material for your engine. Typically, a 2-stroke engine requires a fuel line made of rubber or a flexible material like vinyl. Clean the fuel line and remove any debris or old fuel residue. Then, attach the fuel line to the carburetor and engine block using the appropriate fittings and clamps.
The fuel-to-oil ratio is critical for a 2-stroke engine's performance and longevity. The standard ratio is usually around 15:1 or 20:1, meaning 15 or 20 parts of fuel to one part of oil. You can measure this ratio using a measuring cup or a digital scale. For each liter of oil, add the specified amount of fuel according to the engine's manual.
Routing the fuel line correctly is essential to prevent fuel flow issues. Start by referring to your engine's manual for the recommended path. Keep the fuel line as straight as possible and away from sharp bends or kinks. Avoid routing it near hot engine components to prevent damage. Ensure there are no obstructions or tight spaces that might restrict fuel flow.
A clogged or damaged fuel line can cause starting issues and poor engine performance. Signs of a problem include difficulty starting the engine, hesitation, or loss of power. If you suspect a clog, inspect the fuel line for any blockages and clear them. If the line is damaged, replace it with a new one, ensuring it is the correct size and material. Always check for and address any fuel line issues promptly to maintain optimal engine operation.