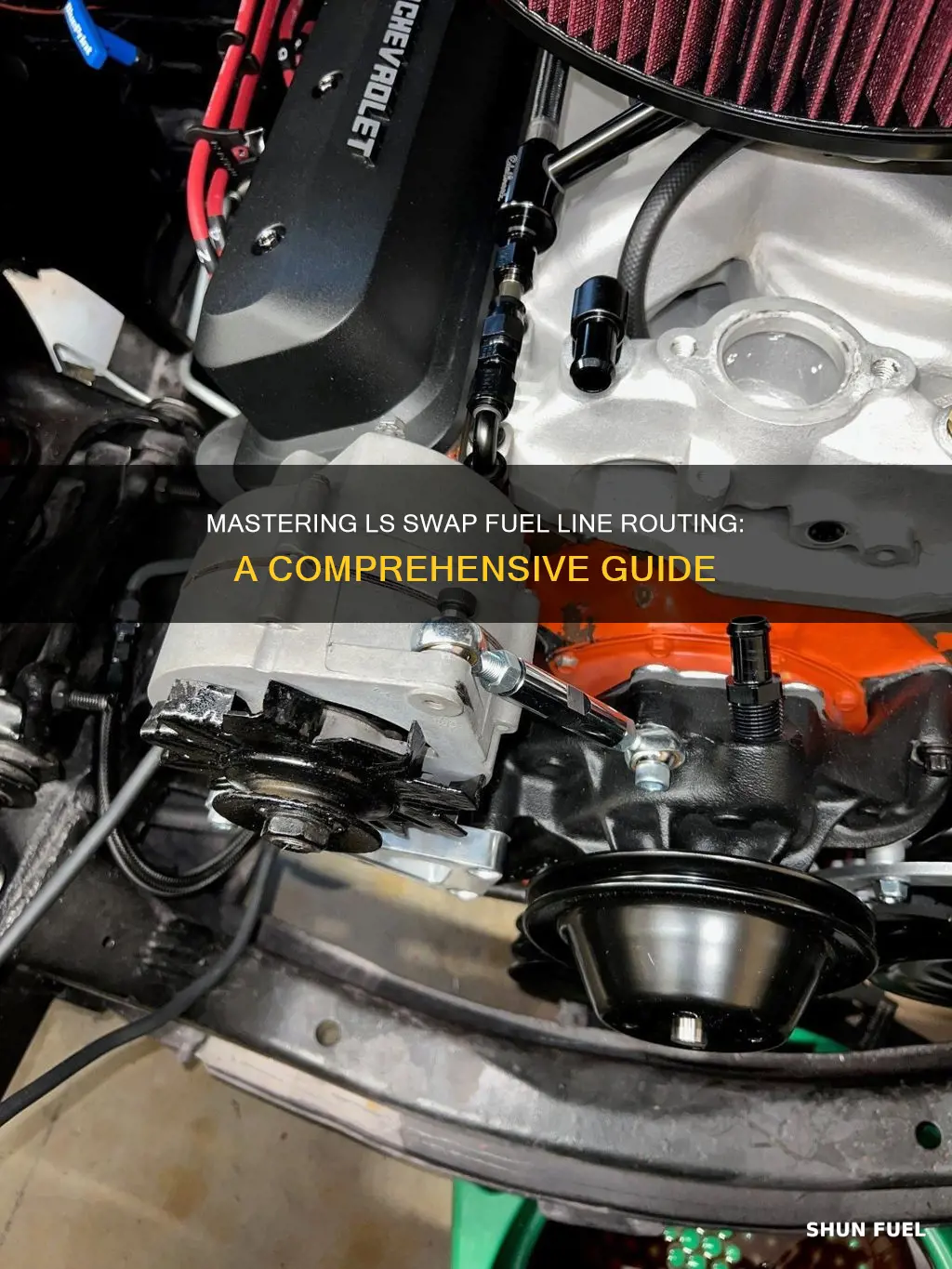
When performing an LS swap, it's crucial to properly route the fuel lines to ensure optimal performance and reliability. This guide will provide a step-by-step overview of the process, covering the necessary tools, materials, and techniques to effectively run the fuel line for your LS swap. By following these instructions, you can ensure a smooth and efficient fuel delivery system, maximizing the potential of your engine upgrade.
Characteristics | Values |
---|---|
Fuel Line Material | High-pressure fuel lines made of steel, aluminum, or braided rubber are commonly used for LS swaps. |
Line Diameter | Typically 3/8" or 1/2" ID for high-performance applications. |
Length | The length of the fuel line depends on the specific engine and vehicle setup. It's crucial to measure and cut the line accurately. |
Fittings | Use high-quality fittings like AN (Aerospace) or metric fittings for a secure and leak-free connection. |
Routing | Route the fuel line away from heat sources and under the vehicle's body to prevent damage and maintain fuel quality. |
Fuel Pump Location | Consider the placement of the fuel pump; some LS swaps may require a remote-mount fuel pump. |
Fuel Filter | Install a fuel filter to protect the engine from contaminants. |
Pressure Regulation | Use a fuel pressure regulator to maintain optimal fuel pressure for the LS engine. |
Flexibility | Choose fuel lines with sufficient flexibility to accommodate engine movement during operation. |
Safety | Ensure all connections are secure and follow safety guidelines for fuel system installations. |
What You'll Learn
- Fuel Pump Placement: Install the fuel pump close to the engine for optimal performance
- Line Routing: Route fuel lines away from heat sources and under the vehicle for protection
- Fittings and Connections: Use high-quality fittings and ensure tight connections to prevent leaks
- Fuel Filter Location: Place the fuel filter near the engine for easy access and maintenance
- Return Line Management: Route the return line to maintain proper fuel pressure and prevent cavitation
Fuel Pump Placement: Install the fuel pump close to the engine for optimal performance
When performing an LS swap, proper fuel pump placement is crucial for optimal engine performance and reliability. The fuel pump is responsible for delivering fuel from the tank to the engine, and its location can significantly impact the system's efficiency and longevity. Here's a guide on why and how to install the fuel pump close to the engine:
Proximity to the Engine: Placing the fuel pump near the engine is essential for several reasons. Firstly, it ensures a shorter fuel line route, which reduces the risk of fuel degradation and pressure loss. Longer fuel lines can lead to fuel vaporization, especially in hot engine compartments, which can negatively affect performance and fuel economy. By keeping the fuel line short, you maintain the integrity of the fuel and ensure a consistent supply to the engine.
Engine Performance and Response: A fuel pump positioned closer to the engine provides better engine response and performance. When the pump is nearby, the fuel delivery system can respond more quickly to engine demands, resulting in improved throttle response and overall power delivery. This is particularly beneficial for high-performance applications where quick and precise fuel injection is required.
Installation Considerations: When installing the fuel pump, it's important to consider the engine's layout and available space. The pump should be mounted securely and close to the engine block to ensure a straight and short fuel line run. Proper mounting angles and orientations are crucial to prevent fuel line kinks and ensure optimal flow. Additionally, ensure that the pump is easily accessible for maintenance and has adequate ventilation to prevent overheating.
Fuel Pump Type: Different fuel pump types may have specific installation requirements. For example, electric fuel pumps often have mounting brackets that need to be securely attached to the engine or firewall. Mechanical pumps might require adjustments to the timing chain or belt tension to ensure proper operation. Always refer to the manufacturer's guidelines for your specific fuel pump model.
By installing the fuel pump close to the engine, you create a more efficient and responsive fuel delivery system, which is vital for the success of an LS swap. This simple yet critical modification ensures that your engine receives the necessary fuel for optimal performance and longevity.
Isuzu Diesel Fuel Line Sizes: A Comprehensive Guide
You may want to see also
Line Routing: Route fuel lines away from heat sources and under the vehicle for protection
When performing an LS swap, proper fuel line routing is crucial for the safety and performance of your engine. One essential aspect of this process is ensuring that the fuel lines are routed away from heat sources and protected under the vehicle. Here's a detailed guide on how to achieve this:
- Identify Heat Sources: Before you begin routing, take time to identify potential heat sources in your engine bay. This includes components like the exhaust manifold, headers, engine block heater, and any other hot surfaces. These areas can cause fuel lines to degrade over time due to the high temperatures they reach. By avoiding these zones, you ensure the longevity of the fuel lines.
- Route Fuel Lines Away from Heat: When laying out the fuel lines, make a conscious effort to keep them as far as possible from direct contact with heat sources. This might involve running the lines along the sides of the engine bay or even under the vehicle, where they will be protected from the elements and potential damage. Consider the path that provides the most distance between the fuel lines and the heat-generating components.
- Use Insulation or Heat Shield: To further protect the fuel lines, consider using insulation material or heat shields. Wrap the lines with high-temperature-rated insulation or install heat shields around the areas where the lines pass close to hot surfaces. This additional layer of protection will help maintain the integrity of the fuel lines, especially in high-temperature environments.
- Route Under the Vehicle: One of the best ways to protect fuel lines is to route them under the vehicle. This placement offers several advantages. Firstly, it keeps the lines away from direct sunlight and potential road debris. Secondly, it provides a more secure environment, reducing the risk of damage from accidental bumps or impacts. Ensure that the lines are securely fastened and supported to prevent any strain or damage during vehicle operation.
- Consider Flexibility and Routing: While keeping the fuel lines away from heat sources is essential, also consider their flexibility and overall routing. Allow the lines to bend and move with the engine's natural vibrations without putting excessive strain on the connections or the lines themselves. Proper routing will also make future maintenance and inspections easier.
By following these guidelines, you can ensure that your fuel lines are well-protected during an LS swap, contributing to a reliable and long-lasting engine setup. Remember, proper routing is a critical aspect of maintaining the health and performance of your fuel system.
Vacuum Line Fuel Spill: Unraveling the Mystery
You may want to see also
Fittings and Connections: Use high-quality fittings and ensure tight connections to prevent leaks
When performing an LS swap, ensuring that the fuel lines are properly installed and connected is crucial to maintaining optimal performance and preventing leaks. The first step is to choose high-quality fittings that are compatible with your fuel lines and the engine's requirements. Look for fittings made from durable materials such as stainless steel or aluminum, as these will withstand the high pressure and temperature changes associated with fuel systems.
High-quality fittings often feature precision-machined ports and O-rings, ensuring a tight and secure seal. This is essential to prevent fuel leaks, which can lead to dangerous situations and potential engine damage. When selecting fittings, consider the size and type of your fuel lines, as well as the specific engine you are working with.
Proper connection is key to a successful LS swap. Take the time to clean and prepare the ends of the fuel lines before attaching the fittings. Use a solvent to remove any dirt or debris, ensuring a clean and smooth surface for the O-rings to seal against. Apply a small amount of fuel line sealant to the O-rings, but be careful not to overdo it, as excess sealant can cause leaks.
When connecting the fittings, ensure that they are aligned correctly and that the O-rings are properly seated. Tighten the fittings securely, but be careful not to overtighten, as this can damage the fuel lines or fittings. A good rule of thumb is to use your hand to tighten them initially, then apply a small amount of torque using a wrench, ensuring you don't exceed the recommended specifications.
Regularly inspect the fittings and connections for any signs of wear or damage. Over time, O-rings can degrade, and fittings may loosen, so it's essential to check and retighten connections as needed. By using high-quality fittings and ensuring tight, secure connections, you can minimize the risk of fuel leaks and ensure a reliable fuel system during your LS swap project.
Fixing a Rubber ATV Fuel Line: A Step-by-Step Guide
You may want to see also
Fuel Filter Location: Place the fuel filter near the engine for easy access and maintenance
When performing an LS swap, ensuring the fuel system is correctly set up is crucial for optimal engine performance and longevity. One critical aspect often overlooked is the placement of the fuel filter. Proper positioning of the fuel filter is essential for easy access and maintenance, which can save you time and potential headaches down the road.
The ideal location for the fuel filter is near the engine bay, close to the fuel pump. This placement offers several advantages. Firstly, it provides easy access for routine maintenance and filter changes. Over time, fuel filters can become clogged, leading to reduced fuel flow and potential engine issues. Regularly replacing the filter ensures clean fuel reaches the engine, promoting efficient combustion and engine health.
Secondly, having the fuel filter in close proximity to the engine allows for quick troubleshooting. If you notice any issues with fuel delivery, such as weak power or erratic engine behavior, being able to inspect and potentially replace the filter without extensive disassembly can be invaluable. This accessibility can save you from more complex and time-consuming repairs.
Additionally, placing the fuel filter near the engine bay can help prevent fuel line damage. Fuel lines can be susceptible to damage from heat, vibration, and impact. By positioning the filter close to the engine, you can ensure that any potential issues with the fuel lines are more easily identified and addressed. This proactive approach can help maintain the overall integrity of the fuel system.
In summary, when running fuel lines for an LS swap, remember that the fuel filter's location is a critical consideration. Placing it near the engine provides easy access, facilitates regular maintenance, aids in quick troubleshooting, and helps protect the fuel system from potential damage. By following this simple guideline, you'll contribute to a more reliable and efficient fuel system for your LS engine swap.
Unraveling the Mystery: Suction Fuel Line for Your Poulan Wild Thing Chainsaw
You may want to see also
Return Line Management: Route the return line to maintain proper fuel pressure and prevent cavitation
When performing an LS swap, proper return line management is crucial to ensure optimal fuel pressure and prevent issues like cavitation. Here's a detailed guide on how to route the return line effectively:
Understanding the Return Line: The return line is responsible for carrying the used fuel from the engine back to the fuel pump. This line plays a vital role in maintaining the fuel pressure within the system. When the engine is running, the fuel pump creates a vacuum, pulling fuel from the tank and sending it through the supply line. The return line then carries the used fuel back to the tank, completing the cycle.
Routing Considerations:
- Direct Path: Aim for a direct and short route for the return line. A longer return line can lead to increased pressure drop, affecting fuel pressure. Keep the line as straight as possible to minimize bends, as sharp bends can restrict flow and create pressure variations.
- Avoid Cross-Contamination: Ensure the return line does not cross paths with the supply line. Cross-contamination can lead to fuel degradation and potential engine issues. Maintain a clear separation between the two lines to prevent any mixing of fresh and used fuel.
- Use of Filters: Install fuel filters at both the inlet and outlet of the return line. This helps remove contaminants and ensures clean fuel is returned to the tank. Regularly check and replace these filters to maintain optimal performance.
- Pressure Relief: Consider adding a pressure relief valve along the return line. This valve allows excess pressure to escape, preventing a buildup that could lead to cavitation. Cavitation occurs when fuel vaporizes due to low pressure, causing air bubbles and potential engine performance issues.
Preventing Cavitation: Cavitation is a common problem in fuel systems, especially when the engine is idling or during sudden throttle changes. Here's how to manage it:
- Maintain Consistent Pressure: Ensure the return line is routed in a way that maintains a consistent pressure throughout the system. This can be achieved by using a properly sized return line and avoiding sharp bends.
- Use a Fuel Pressure Regulator: Consider installing a fuel pressure regulator to maintain a steady pressure. This device monitors and adjusts the pressure, ensuring it remains within the optimal range for your engine.
- Regular Maintenance: Regularly check the fuel system for any signs of cavitation, such as fuel vapor or air bubbles. Keep the fuel tank and lines clean to prevent contamination, which can exacerbate cavitation issues.
By carefully managing the return line route and implementing these preventative measures, you can ensure a reliable LS swap fuel system with optimal pressure and performance. Remember, proper routing and maintenance are key to a successful LS swap.
Mastering LS1 Fuel Line Removal: A Step-by-Step Guide
You may want to see also
Frequently asked questions
An LS swap refers to the process of replacing the original engine in a vehicle with a more powerful and modern General Motors LS-series engine, such as the LS3, LS7, or LS9. This swap is popular among car enthusiasts and modifiers as it offers a significant performance boost. By installing an LS engine, you gain access to a wide range of engine sizes, improved reliability, and the ability to customize and tune the engine to your specific needs.
Selecting the appropriate fuel line is crucial for a successful LS swap. The fuel line should be compatible with the engine's fuel requirements and the vehicle's system. Consider the following factors: engine displacement, fuel pump specifications, and the desired fuel pressure. For high-performance LS swaps, a fuel-injected setup might be preferable, requiring a dedicated fuel line system. It's recommended to consult the specific engine and vehicle manuals, or seek advice from experienced mechanics, to determine the best fuel line options for your particular LS swap.
Reusing the original fuel lines is generally not recommended, especially for high-performance applications. The LS engine's fuel requirements and pressure may differ significantly from the old engine, and the existing lines might not be compatible. It's best to replace the fuel lines with new, high-quality lines designed for the LS engine's specifications. This ensures optimal fuel delivery, prevents engine damage, and provides a reliable and safe setup for your modified vehicle.