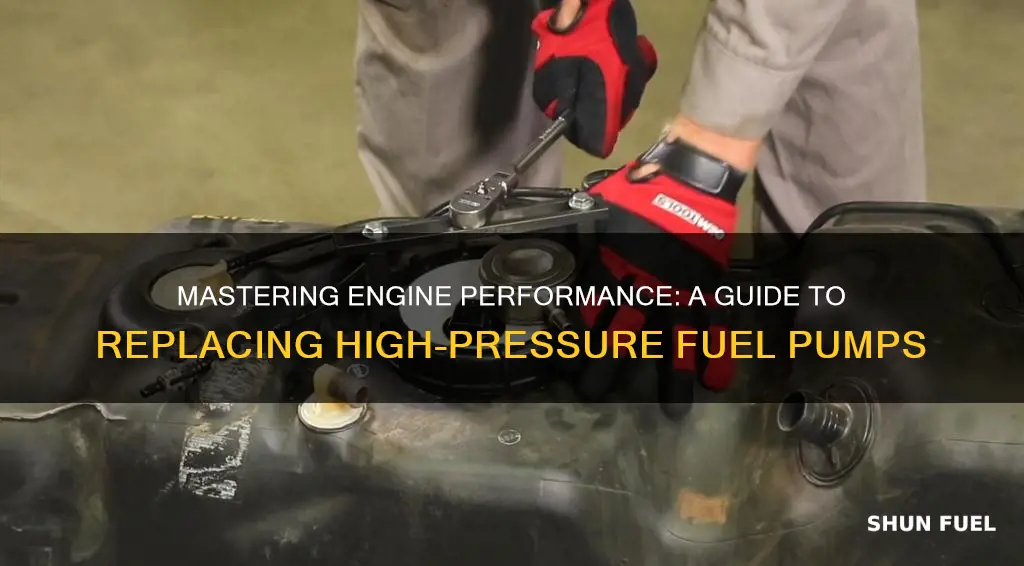
Replacing a high-pressure fuel pump is a crucial task for vehicle owners, as it ensures optimal engine performance and fuel efficiency. This process requires careful disassembly of the fuel system, including the fuel tank and lines, to access the pump. It's essential to understand the specific make and model of your vehicle to ensure you have the correct replacement parts. The replacement process involves removing the old pump, installing the new one, and reconnecting all fuel lines and components. This task demands precision and technical knowledge, so it's recommended to follow detailed step-by-step guides or consult a professional mechanic to avoid any potential issues.
What You'll Learn
- Fuel Pump Location: Identify the high-pressure fuel pump's location under the hood
- Fuel System Disconnect: Turn off the fuel supply and disconnect the fuel lines
- Pump Removal: Carefully remove the old pump, often requiring specialized tools
- New Pump Installation: Insert the new pump, ensuring proper alignment and secure it
- Fuel System Restoration: Reattach fuel lines and restore power to complete the replacement
Fuel Pump Location: Identify the high-pressure fuel pump's location under the hood
The high-pressure fuel pump is a critical component of your vehicle's fuel system, responsible for delivering fuel at the required pressure to the engine. Identifying its location under the hood is the first step in replacing it. Here's a detailed guide on how to locate this pump:
Step 1: Access the Engine Compartment
Start by opening your car's hood. Ensure you are in a well-ventilated area and follow the manufacturer's guidelines for hood release mechanisms. A well-lit area will also make it easier to inspect the engine compartment.
Step 2: Locate the Fuel Rail or Injector Assembly
The high-pressure fuel pump is typically located near the fuel rail or the injector assembly. The fuel rail is a metal bracket that holds the high-pressure fuel injectors in place. It is usually positioned close to the front of the engine, often along the top or side of the engine block. The injector assembly, on the other hand, is a cluster of fuel injectors that spray fuel directly into the engine's cylinders.
Step 3: Identify the Pump
The pump itself is often a small, rectangular or cylindrical component. It is usually connected to the fuel rail or injector assembly via a series of hoses and lines. Carefully inspect the area around the fuel rail and injector assembly to find the pump. It may be mounted horizontally or vertically, depending on your vehicle's design.
Step 4: Check for Additional Components
In some vehicles, there might be additional components, such as a fuel filter or a fuel pressure regulator, located nearby. These components are often part of the fuel delivery system and should be identified and inspected during the replacement process.
Step 5: Consult the Vehicle's Manual
If you're unsure about the exact location, consult your vehicle's owner's manual. The manual will provide detailed diagrams and instructions specific to your car's make and model, ensuring you locate the high-pressure fuel pump accurately.
Replacing the Fuel Pump on Your Kawasaki 250F
You may want to see also
Fuel System Disconnect: Turn off the fuel supply and disconnect the fuel lines
To begin the process of replacing a high-pressure fuel pump, it is crucial to ensure that the fuel supply is safely disconnected. This step is essential to prevent any accidental fuel release and potential hazards. Here's a detailed guide on how to perform this task:
Step 1: Turn Off the Fuel Supply:
Locate the fuel shut-off valve, typically found under the hood or near the fuel tank. This valve controls the flow of fuel to the engine. Turn the valve clockwise to shut off the fuel supply. Ensure that the engine is also turned off to avoid any unnecessary complications.
Step 2: Identify and Disconnect Fuel Lines:
Locate the high-pressure fuel lines that connect to the fuel pump and the engine. These lines are usually made of sturdy materials and may require some effort to disconnect. Use a fuel line disconnect tool or a pair of adjustable pliers to carefully release the fittings. Be cautious not to damage the fuel lines during this process. Once disconnected, set the lines aside in a well-ventilated area to prevent fuel vapor buildup.
When disconnecting the fuel lines, it's important to note the positions of the lines to ensure proper reattachment during the replacement process. Some vehicles may have fuel pressure regulators or additional components connected to these lines, so be mindful of any associated parts.
Safety Precaution: Always wear protective gear, such as gloves and safety goggles, when working with fuel lines to avoid any potential splashes or spills.
By following these steps, you effectively disconnect the fuel supply and remove the high-pressure fuel lines, creating a safe environment for the upcoming fuel pump replacement. Remember to exercise caution and take your time during this process to ensure a successful repair.
Replacing Fuel Injectors in Your Dodge Caravan: Step-by-Step Guide
You may want to see also
Pump Removal: Carefully remove the old pump, often requiring specialized tools
When replacing a high-pressure fuel pump, the removal process demands precision and the right tools to ensure a successful repair. Here's a step-by-step guide to safely and effectively take out the old pump:
Access the Pump: Begin by locating the high-pressure fuel pump, which is typically positioned near the engine's fuel rail. This pump is responsible for delivering fuel at high pressure to the injectors. Carefully inspect the pump's connections and ensure you understand the layout of the fuel system to avoid any accidental disconnections.
Prepare the Necessary Tools: Removing the pump often requires specialized tools due to its intricate design and secure mounting. You'll likely need a pump removal kit or a set of specialized tools that include a pump puller, which is a crucial component for safely extracting the pump. These tools are designed to grip the pump's housing without damaging it, ensuring a clean and efficient removal process.
Release Fuel Pressure: Before attempting to remove the pump, it is essential to release the fuel pressure to avoid any potential hazards. Locate the fuel pressure regulator or gauge and disconnect it from the fuel rail. This step ensures that the fuel system is depressurized, making the removal process safer and preventing any fuel spills or splashes.
Careful Disassembly: With the fuel pressure released, you can now carefully begin the disassembly process. Start by disconnecting any electrical connections to the pump. Use the appropriate socket or tool to loosen the bolts securing the pump's housing. Be gentle yet firm to avoid stripping the threads. Once the bolts are removed, carefully lift the pump out of its mounting position, ensuring you don't damage any surrounding components.
Specialized Pump Puller: In many cases, the pump's housing is designed to be pulled out rather than lifted directly. This is where the pump puller comes into play. Insert the puller into the pump's housing, aligning it with the pump's internal structure. Apply firm pressure while pulling to extract the pump. This tool is crucial to ensure a clean removal without damaging the pump's delicate components.
Final Steps: After successfully removing the old pump, you can now proceed with installing the new one, following a similar process in reverse. Remember, the key to a successful pump replacement is patience and the use of the right tools to avoid any complications.
Replacing the Fuel Filter: A Step-by-Step Guide for 2006 Ford Taurus Owners
You may want to see also
New Pump Installation: Insert the new pump, ensuring proper alignment and secure it
When replacing a high-pressure fuel pump, the installation process requires careful attention to detail to ensure optimal performance and prevent potential issues. Here's a step-by-step guide for inserting the new pump and securing it in place:
Preparation: Before you begin, ensure you have the necessary tools and components ready. This includes the new high-pressure fuel pump, a set of wrenches or sockets, and possibly a torque wrench for precise tightening. It is crucial to inspect the old pump and any associated components for any signs of damage or wear. Clean the engine bay and the pump mounting area to ensure a smooth installation.
Inserting the New Pump: Locate the mounting points and align the new pump accordingly. Carefully slide the pump into position, ensuring it fits snugly against the engine block or frame. Pay close attention to the orientation and make sure it is correctly positioned relative to the fuel rail or injection system. The pump should be securely attached to the engine, often using a combination of bolts and gaskets.
Alignment and Tightening: Proper alignment is critical to prevent leaks and ensure efficient operation. Check that the pump's inlet and outlet ports are aligned with the fuel lines and rails. Tighten the mounting bolts by hand first to ensure even pressure distribution. Then, using the appropriate tools, apply the recommended torque to secure the bolts. Over-tightening can damage the pump, so be cautious and refer to the manufacturer's specifications for torque values.
Final Adjustments: After tightening the bolts, inspect the pump for any signs of wobble or misalignment. Ensure that all connections are secure and that there is no excessive play in the pump's mounting. You may need to make minor adjustments to the pump's position to optimize its performance. Once satisfied with the alignment, start the engine and check for any unusual noises or vibrations.
Remember, each vehicle model may have specific requirements, so always refer to the vehicle's manual or consult a professional for any model-specific instructions. Proper installation and alignment are key to ensuring the longevity and efficiency of the high-pressure fuel pump system.
Nuclear Energy: Unsuitable Fossil Fuel Alternative
You may want to see also
Fuel System Restoration: Reattach fuel lines and restore power to complete the replacement
Once you've completed the replacement of the high-pressure fuel pump, the next crucial step is to restore the fuel system's functionality by reattaching the fuel lines and re-establishing power. This process ensures that the fuel pump operates efficiently and that the engine receives the required fuel for optimal performance. Here's a step-by-step guide to help you through this phase:
Prepare the Work Area: Before beginning, ensure you have a clean and well-lit workspace. Lay out all the necessary tools and components, including the new fuel pump, fuel lines, and any additional hardware required. This preparation will make the reattachment process smoother and more efficient.
Reattach Fuel Lines: Start by carefully reconnecting the fuel lines to the new pump. Ensure that each line is correctly aligned with its respective port on the pump. Tighten the connections securely, but be mindful not to overtighten, as this can damage the lines. Check for any leaks by gently pressing the connections and observing for any fuel seepage. If you notice any leaks, tighten the connections further or replace the affected lines.
Secure Fuel Lines: After reattaching the lines, secure them in place using the appropriate clamps or ties. This step is essential to prevent the lines from coming loose during engine operation. Ensure that the lines are routed correctly and do not interfere with other engine components. Proper routing and securing will contribute to a smooth and safe fuel supply.
Restore Power to the Fuel Pump: With the fuel lines reattached, it's time to restore power to the fuel pump. Connect the electrical wiring to the pump's terminals, ensuring a secure and proper connection. Double-check the wiring to guarantee that it matches the original setup. Once powered, the fuel pump should activate, and you can observe the fuel flow through the lines.
Final Checks: Before starting the engine, perform a few final checks. Inspect all connections for tightness and leaks. Ensure that there is no fuel spillage around the engine bay. Start the engine and monitor its performance, checking for any unusual noises or vibrations. If everything is functioning correctly, you've successfully restored the fuel system, and the engine should now operate efficiently.
Remember, proper reattachment and restoration of the fuel system are vital to ensure the engine's reliability and performance. Take your time during this process, and if you encounter any specific issues, consult the vehicle's manual or seek professional advice for further guidance.
Replacing Fuel Lines: Echo PB-250 Step-by-Step Guide
You may want to see also
Frequently asked questions
Common indicators include a decrease in engine power, rough idling, engine stalling, or a warning light on the dashboard. If you notice any of these symptoms, especially when accompanied by fuel-related issues, it's best to have the pump inspected.
A professional mechanic can perform diagnostic tests to identify the issue. They might use a scan tool to check for error codes related to the fuel system or perform pressure tests to confirm if the pump is failing. Sometimes, other components like the fuel filter or injectors may mimic pump issues.
Replacing a high-pressure fuel pump can be complex and requires specialized tools and knowledge. It's generally recommended to have this task performed by an experienced mechanic to ensure proper installation and avoid potential hazards. DIY kits are available, but they may not be suitable for all vehicle models.
The required tools vary depending on the vehicle make and model. Generally, you'll need a fuel pump removal and installation kit, which includes specialized tools for disconnecting the old pump and connecting the new one. You might also need a fuel pressure gauge, wrenches, and possibly a new fuel line.
Yes, safety is crucial. Make sure the engine is cool before starting the replacement to avoid burns. Disconnect the battery to prevent electrical shocks. When handling fuel-related components, ensure proper ventilation to avoid inhaling fuel vapor. Always follow the manufacturer's guidelines and consider consulting a professional for complex procedures.