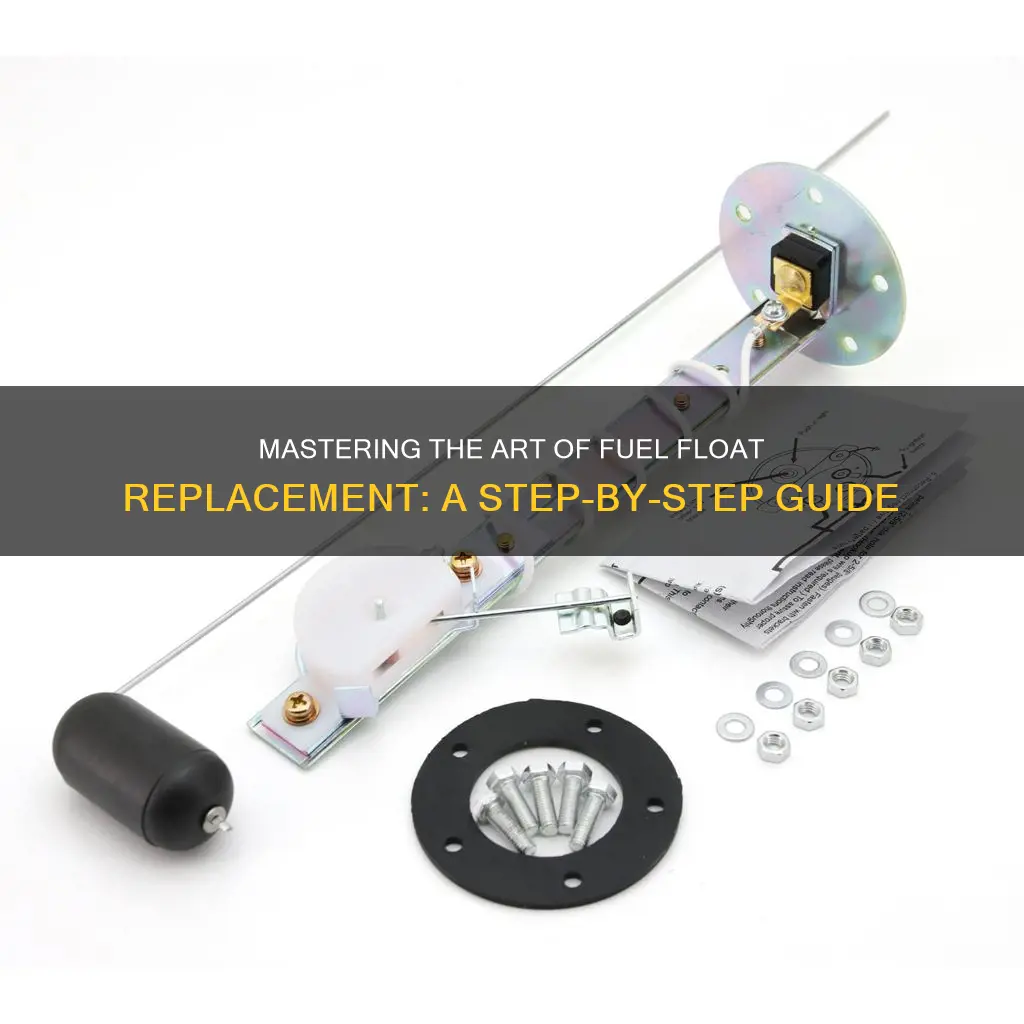
Replacing a fuel float is a crucial maintenance task for ensuring the proper functioning of your vehicle's fuel system. The fuel float, also known as a float bowl or fuel level sensor, plays a vital role in monitoring the fuel level in your tank and communicating this information to the engine's electronic control unit (ECU). Over time, the float can become worn out or damaged, leading to inaccurate fuel readings and potential engine performance issues. This guide will provide a step-by-step process to replace the fuel float, covering the necessary tools, safety precautions, and troubleshooting tips to ensure a successful repair.
What You'll Learn
- Float Inspection: Check for damage, corrosion, and proper operation
- Fuel Level Sensor: Calibrate and replace if faulty
- Hose Connections: Ensure secure and leak-free connections
- Float Arm Adjustment: Align and tighten for optimal performance
- Fuel System Cleaning: Remove debris for efficient float operation
Float Inspection: Check for damage, corrosion, and proper operation
When inspecting the fuel float, it's crucial to ensure it is in good condition and functioning correctly. Start by visually examining the float for any signs of damage or wear. Look for cracks, chips, or any visible imperfections on the surface. These issues could compromise the float's integrity and its ability to regulate fuel levels accurately. Additionally, check for any signs of corrosion, especially if the float is made of metal. Corrosion can lead to a loss of structural strength and may affect the float's performance. Inspect all surfaces, including the top, sides, and bottom, to identify any areas affected by rust or oxidation.
The float's operation is another critical aspect of the inspection. Ensure that the float moves freely within the fuel tank and responds to changes in fuel levels. It should rise and fall accordingly as the fuel is added or consumed. Test the float's sensitivity by adding a small amount of fuel to the tank and observing how the float reacts. It should adjust its position promptly to indicate the fuel level. If the float is unresponsive or slow to react, it may need adjustment or replacement.
Pay attention to the float's design and ensure it matches the specifications of your fuel tank. Different tanks may require floats with varying sizes, shapes, or mechanisms. A poorly designed or incompatible float can lead to inaccurate fuel measurements and potential engine issues. Check the float's attachment points and ensure they are secure. Over time, these connections can loosen, affecting the float's performance. Tighten any loose screws or fasteners to maintain the float's stability within the tank.
If you notice any damage, corrosion, or operational issues during the inspection, it's essential to address them promptly. Replacing a damaged or faulty float is often necessary to prevent fuel-related problems. Consider the float's condition and its impact on the overall fuel management system when making your decision. Regular float inspections are a proactive approach to maintaining a healthy fuel system and ensuring optimal engine performance.
Replacing Motorcraft PFB-101 Fuel Pump: Step-by-Step Guide
You may want to see also
Fuel Level Sensor: Calibrate and replace if faulty
The fuel level sensor, also known as the float sensor, is a critical component in monitoring the fuel level in your vehicle's tank. Over time, this sensor can become faulty, leading to inaccurate fuel level readings, which may cause issues with your vehicle's performance and fuel efficiency. Calibration and replacement of the fuel level sensor are essential to ensure accurate fuel measurements and optimal vehicle operation. Here's a step-by-step guide on how to calibrate and replace the fuel level sensor if it is faulty:
Calibration and Replacement Process:
- Fuel Level Sensor Inspection: Begin by inspecting the fuel level sensor for any visible signs of damage or wear. Check for cracks, corrosion, or any physical damage that might affect its performance. If the sensor appears faulty, proceed with the replacement process.
- Fuel Tank Access: Locate the fuel tank, which is usually positioned at the rear or bottom of the vehicle. Access the tank by removing the appropriate panels or trim pieces to gain entry. Ensure you have a safe and stable working position.
- Sensor Removal: Identify the fuel level sensor, which is typically a small float-like mechanism inside the tank. It is connected to a cable or wiring harness. Carefully disconnect the wiring harness from the sensor. You might need to release any retaining clips or screws to remove the sensor. Take note of the sensor's position and orientation for proper reinstallation.
- Replacement: Obtain a new fuel level sensor that is compatible with your vehicle's make and model. Ensure it has the correct specifications. Install the new sensor by following the reverse procedure of removal. Secure it in place and reconnect the wiring harness, ensuring all connections are tight and properly aligned.
- Calibration (if applicable): Some vehicles may require calibration of the fuel level sensor after replacement. Consult your vehicle's manual or seek professional assistance to understand the calibration process. This step ensures the sensor provides accurate readings. Calibration often involves using specialized tools and may require a professional mechanic's expertise.
Troubleshooting and Maintenance:
- Regularly check the fuel level sensor for any signs of contamination or debris that might affect its performance. Keep the fuel tank and sensor clean to ensure accurate fuel level monitoring.
- If you suspect a faulty sensor, you can temporarily disable it by disconnecting the wiring harness to prevent incorrect fuel level indications. However, this should be a temporary measure, and a proper replacement is recommended.
- Keep your vehicle's maintenance records up-to-date, including sensor replacements, to ensure optimal vehicle performance and longevity.
By following these steps, you can effectively calibrate and replace the fuel level sensor, ensuring your vehicle's fuel system operates efficiently and accurately. Remember, if you are unsure about any step, seeking professional help is always an option to ensure the job is done correctly.
Fuel Pump Replacement: Essential Tools and Components
You may want to see also
Hose Connections: Ensure secure and leak-free connections
When replacing a fuel float, ensuring secure and leak-free hose connections is crucial to prevent fuel leaks and maintain the integrity of your vehicle's fuel system. Here's a step-by-step guide to achieving this:
Prepare the Hose and Connections: Begin by inspecting the fuel hose that connects to the float. Check for any signs of damage, cracks, or wear. If the hose is old or damaged, replace it with a new one to ensure a reliable connection. Clean the hose and the corresponding fittings to remove any debris or old fuel residue. This step is essential to create a clean and secure interface for the new connection.
Use the Right Fittings: Select the appropriate hose fittings that match the diameter and type of your fuel hose. Common types include barbed fittings, compression fittings, or quick-connect fittings. Ensure that the fittings are compatible with the fuel hose material to prevent any potential leaks. Barbed fittings are often used for fuel lines due to their durability and ease of installation.
Secure the Connection: Start by inserting the hose into the fitting, ensuring it is aligned correctly. For barbed fittings, twist the hose onto the fitting until it is firmly in place. Use a hose clamp or a compression fitting to secure the connection. Tighten the clamp or compression nut hand-tight, then use a wrench to ensure a secure and tight fit. Avoid over-tightening to prevent damage to the hose.
Test for Leaks: After securing the hose connection, it's crucial to test for any leaks. Turn on the fuel supply and observe the connection area for any signs of fuel escaping. You can also use a soapy water solution and spray it around the connection to check for bubbles, indicating a potential leak. If any leaks are detected, tighten the connection further or consider replacing the fitting if it is damaged.
Final Inspection: Once you're confident that the hose connection is secure, perform a final inspection. Ensure that all fittings are tight and there are no visible signs of damage or wear. Check for any fuel residue or contamination around the connection, as this can affect the performance of the fuel system. A thorough inspection will help identify any potential issues before starting the vehicle.
By following these steps, you can ensure that the hose connections are secure, leak-free, and ready to support the new fuel float installation. Properly secured connections are vital to maintain the efficiency and safety of your vehicle's fuel system.
Replacing Fuel Tank on Craftsman Lawn Tractor: Step-by-Step Guide
You may want to see also
Float Arm Adjustment: Align and tighten for optimal performance
When replacing or adjusting the fuel float arm, it's crucial to ensure proper alignment and tightening for optimal performance. This process involves several steps to guarantee a secure and functional fuel system. Here's a detailed guide on how to achieve this:
Alignment and Tightening Process:
- Access the Float Arm: Start by locating the fuel float arm, which is typically a slender metal rod or shaft. It connects the fuel bowl to the float valve, allowing the float to control the fuel level. Carefully remove any existing float arm or access the existing one if you're replacing it.
- Prepare the Components: Gather the necessary tools, including a wrench or socket set for tightening, and ensure you have the correct replacement parts if needed. Clean the float arm and the corresponding parts to remove any dirt or debris.
- Align the Float Arm: Proper alignment is critical to the float arm's functionality. Position the float arm so that it is perpendicular to the fuel bowl's surface. Ensure it is centered and aligned with the float valve's opening. Use a straightedge or a ruler to verify the alignment.
- Tighten Securely: Once aligned, tighten the float arm securely. Apply firm pressure to the float arm using the appropriate wrench or socket. Ensure it is tightened to the manufacturer's recommended torque specifications to avoid over-tightening, which can damage the components. Tightening should be done in a clockwise direction, ensuring an even and firm hold.
- Check for Leaks: After tightening, inspect the float arm for any signs of fuel leakage. Apply a small amount of fuel to the float arm and observe if any fuel escapes. If there are leaks, recheck the alignment and tightening, ensuring all connections are secure.
- Final Adjustments: If necessary, make minor adjustments to the float arm's position. Fine-tune the alignment to ensure the float arm moves smoothly and responds to the fuel level changes. This step may require patience and a gentle touch to achieve the perfect balance.
Remember, the float arm's adjustment is a delicate process, and proper alignment is key to preventing fuel spillage and ensuring the engine's efficient operation. Always refer to the vehicle's manual or seek professional guidance for specific instructions tailored to your make and model.
Fuel Pump Replacement Kit: Step-by-Step Guide
You may want to see also
Fuel System Cleaning: Remove debris for efficient float operation
Fuel system cleaning is an essential maintenance task to ensure optimal performance and longevity of your vehicle's fuel system, especially when dealing with the fuel float mechanism. Over time, debris and contaminants can accumulate in the fuel tank and lines, leading to various issues that may impact the float's functionality. Here's a step-by-step guide on how to clean the fuel system to maintain efficient float operation:
- Prepare the Vehicle: Begin by ensuring the vehicle is parked on a level surface and the engine is cool. Locate the fuel tank, which is usually located beneath the vehicle or in the trunk, depending on the car model. It is crucial to drain the fuel tank to avoid any accidents or spills during the cleaning process. Place a suitable container under the drain valve to collect the fuel as you remove it.
- Access the Fuel Tank: Carefully inspect the fuel tank's access panel, often located on the side or rear. Remove any screws or fasteners to open the panel, providing access to the interior of the tank. Be cautious and wear protective gear, such as gloves and safety goggles, to shield yourself from any potential hazards.
- Drain and Remove Debris: Once inside the tank, locate the fuel float and take note of its position. Carefully remove the float and set it aside. Use a suction cup or a small tool to extract any visible debris, such as dirt, rust, or sediment, from the tank. Ensure you clean the entire interior surface, including the walls and bottom, to remove any built-up contaminants.
- Clean the Fuel Lines: After cleaning the tank, it's time to address the fuel lines. Start by identifying the fuel lines connected to the tank and the engine. Disconnect the lines carefully and use a fuel line cleaner or a compressed air gun to blow out any debris or residue. Inspect the lines for any signs of damage or corrosion and replace any faulty parts.
- Reassemble and Test: Once the cleaning and inspection are complete, reassemble the fuel tank, ensuring all components are securely in place. Reattach the fuel lines and reconnect the fuel source. Start the engine and monitor its performance. Efficient float operation should be restored, ensuring proper fuel level sensing and delivery.
Remember, regular maintenance and cleaning of the fuel system can prevent potential issues and ensure your vehicle's fuel system operates optimally. Always refer to your vehicle's manual for specific instructions and safety guidelines when performing any maintenance tasks.
Replacing Fuel Regulator in Arctic Cat 2002 600: Step-by-Step Guide
You may want to see also