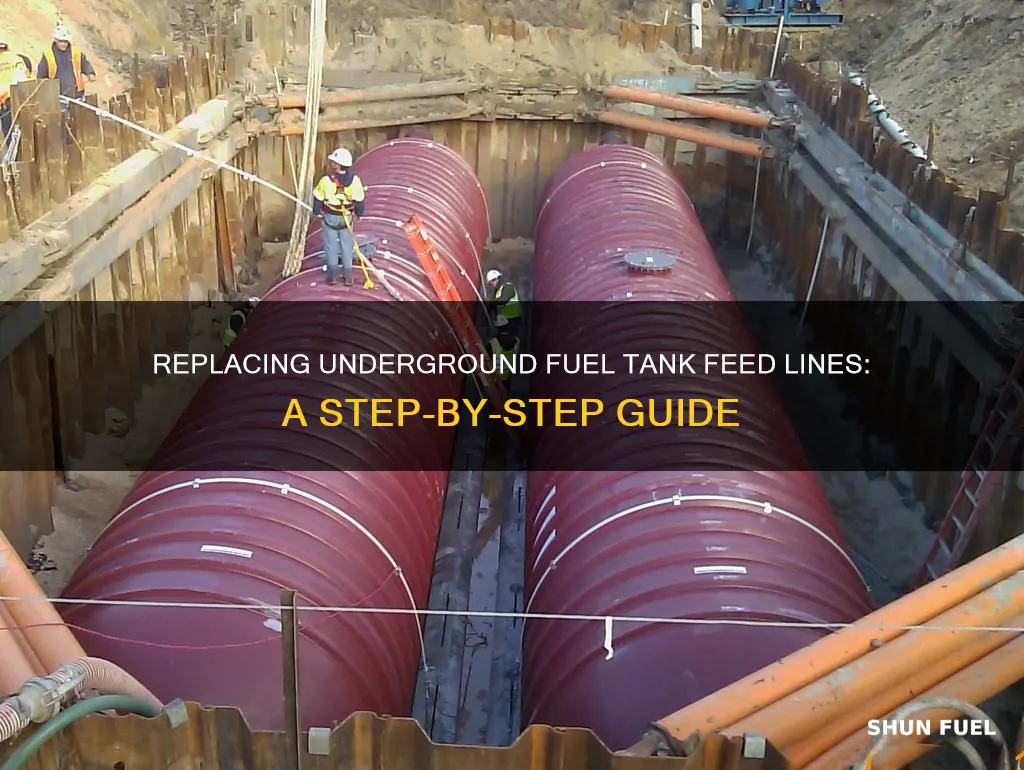
Replacing the feed line in an underground fuel tank is a complex task that requires careful consideration of the specific fuel tank setup and available replacement parts. It is important to assess the condition of the entire fuel line and, if possible, replace it entirely to avoid future issues. When repairing a fuel line, it is crucial to use high-quality materials and connectors to ensure a secure and leak-proof connection. Steel or copper alloy lines are recommended, with flared ends and appropriate fittings, such as compression fittings, to securely join the lines. Rubber fuel hoses can be used but should be inspected regularly as they may deteriorate over time.
What You'll Learn
- Splicing in a new line: use compression fittings or flare the line with new fittings and unions
- Steel vs rubber: steel is the OEM material but rubber fuel hose is easier to install and replace
- Rubber hose connections: flare the hard line first and then slip the hose over it, securing it with hose clamps
- Fuel line materials: stainless steel rubber fuel lines may not last as long as steel but are easier to install and replace
- Fuel line diameter: using a line with a smaller diameter could starve the engine of fuel during high demand
Splicing in a new line: use compression fittings or flare the line with new fittings and unions
Splicing in a new line is a complex process and it is important to be cautious when attempting this. It is recommended that you use nylon for a replacement line. If you are using compression fittings, you will need to ensure the mating steel line is rust-free to ensure a long-lasting, leak-free connection. It is also important to keep a fire extinguisher nearby.
If you are flaring the line, you will need to use a flaring tool. This can be a difficult process, especially if you are working in a confined space. It is also important to ensure that the line is cut straight and that the flare is even. If you are using a budget flaring tool, it may take some practice to get it right.
When using compression fittings, it is important to ensure that the line is cut squarely. Compression fittings can also be useful if the line is cut at an angle, as they will still seal.
If you are using braided lines, it is important to consider the outer diameter and ensure that it is not too large, which may make routing more difficult. Traditional braided lines are made of rubber hose, which will eventually break down. It is also important to ensure that the fittings are compatible with ethanol-blended fuels. PTFE (Teflon) lined braided hoses are smaller in diameter and can handle ethanol, but the fittings will be more expensive.
When deciding between hard lines and braided lines, it is generally recommended to use as much hard line as possible, especially for street cars. Stainless steel or nickel-copper alloy are good options for hard lines. If you are using stainless steel, it is important to note that it is more difficult to bend and flare.
If you are adapting AN lines to existing hard lines, you will need a flare nut and a 37-degree flare tool. It is recommended to keep flexible fuel lines under 15 inches in length.
When working with fuel lines, it is important to take the necessary safety precautions and ensure that you have the proper tools and knowledge to complete the task safely and effectively.
Replacing Fuel Lines: Chrysler PT Cruiser Guide
You may want to see also
Steel vs rubber: steel is the OEM material but rubber fuel hose is easier to install and replace
When it comes to choosing the material for your fuel line, there are a few options available, each with its own advantages and disadvantages. Here is a detailed comparison between steel and rubber fuel hoses to help you decide which one is more suitable for your needs:
Steel Fuel Lines:
Steel, including stainless steel and coated steel, is the original equipment manufacturer (OEM) material for fuel lines in most cars. It has excellent durability and holds up better than any soft material. However, one of the main drawbacks of steel fuel lines is the difficulty in fabrication and installation. Bending steel lines to fit specific routes can be challenging and may require specialised tools. Steel lines are also more expensive compared to rubber hoses. Nonetheless, if you prioritise longevity and are willing to invest in professional installation or have the necessary equipment and skills, steel fuel lines remain a reliable option.
Rubber Fuel Hose:
Rubber fuel hoses, on the other hand, offer greater flexibility and ease of installation. They are typically connected using standard barbed fittings and fuel line hose clamps. When it comes to compatibility, it is crucial to ensure that the rubber hose is rated for fuel, meeting either SAE J30R7 for carbureted engines or SAE J30R9 for fuel injection systems. While rubber hoses are more susceptible to degradation, cuts, and abrasions, they are a more budget-friendly option for fuel line repairs. Additionally, rubber hoses can be easier to manoeuvre and shape to fit the required path. Keep in mind that rubber hoses should not be used for extended lengths in the fuel system due to their limitations. Regular inspections and replacements are necessary to maintain the integrity of rubber fuel hoses.
Replacing the Fuel Pump in a '97 Mazda MPV
You may want to see also
Rubber hose connections: flare the hard line first and then slip the hose over it, securing it with hose clamps
To connect a rubber hose to a hard line, you must first flare the hard line. Flaring is the process of creating a cone shape at the end of a fuel line so it can securely attach to a fitting or hose. This is an essential step in automotive applications where fuel lines have to hold pressure and not leak.
To flare the hard line, you will need a tube cutter, a deburring tool, and a flaring tool. First, use the tube cutter to cut the hard line to the desired length, ensuring the cut is straight and clean. Next, use the deburring tool to smooth out the inside and outside edges of the tube; this will prevent the tube from cracking when it is flared. Then, insert the tube into the flaring tool, tightening the clamp to hold it in place. Now, attach the yoke and screw down the flaring cone into the tube. It is important to gradually apply pressure to form the flare and avoid overtightening, as this can damage the tube and distort the flare. Once complete, inspect the flare for any cracks or deformities, ensuring it is smooth and symmetrical.
Now that the hard line is flared, you can attach the rubber hose. Slide the rubber hose over the flared end of the tube, ensuring a tight fit inside the hose. Use a high-quality clamp, such as a fuel injection hose clamp, to secure the hose in place. This will create a secure connection and prevent leaks.
Firestone's Fuel Line Innovations: Replacement Revolutionized
You may want to see also
Fuel line materials: stainless steel rubber fuel lines may not last as long as steel but are easier to install and replace
When it comes to fuel line materials, you have a few options to choose from, each with its own advantages and drawbacks.
Rubber Fuel Lines
Rubber fuel lines are flexible and easy to install, making them a popular choice for many vehicle owners. They can be cut to the desired length and are typically connected using barbed fittings and fuel line hose clamps. However, rubber lines have a few downsides. They start degrading as soon as they come into contact with fuel and are susceptible to cuts and nicks, leading to fuel leaks. Additionally, rubber lines can rot when exposed to extreme heat and will need to be replaced more frequently than other materials.
Nylon Fuel Lines
Nylon fuel lines offer improved corrosion resistance compared to rubber, resulting in a longer lifespan. They are also lightweight and flexible, making them easy to work with. However, nylon is sensitive to tears and abrasions, so careful installation is crucial to ensure the lines don't rub against other parts. Like rubber, nylon fuel lines have poor heat resistance and can dry and crack when exposed to high temperatures.
Stainless Steel Fuel Lines
Stainless steel fuel lines, often braided, are the most durable and corrosion-resistant option. They can withstand abrasion and high-pressure liquid fuel without tearing or leaking. While stainless steel lines are not as flexible as nylon or rubber, the braided design improves their flexibility. Stainless steel also has a much higher heat resistance, making it a superior choice for fuel lines that need to withstand extreme temperatures.
While stainless steel fuel lines may be more challenging to fabricate and bend, their durability and resistance to fuel vapors make them a popular choice for those seeking a long-lasting solution.
Replacing Fuel Pump Sensors: A Step-by-Step Guide for Beginners
You may want to see also
Fuel line diameter: using a line with a smaller diameter could starve the engine of fuel during high demand
When replacing the feed line in an underground fuel tank, it is important to consider the fuel line diameter to ensure optimal engine performance. Using a fuel line with a smaller diameter can result in insufficient fuel delivery to the engine, especially during periods of high demand. This is because a reduction in fuel line diameter increases fuel restriction, hindering the flow of fuel to the engine.
The fuel line diameter should be selected based on the engine's total fuel flow requirements at rated speeds and horsepower output. For example, a 250-450 horsepower six-cylinder diesel engine typically has a total fuel flow of about 1 gallon per minute (GPM). To meet this demand, a fuel line with a larger diameter, such as 5/8 inch, is recommended to minimise fuel restriction.
In contrast, using a smaller diameter fuel line, such as 3/8 inch, can result in a significant pressure drop and hinder fuel flow. For instance, a 10-foot section of 3/8-inch fuel line with a couple of 90-degree bends can cause a pressure drop of up to 3 inches of mercury (Hg), which is comparable to the pressure drop across a properly sized fuel filter system. This increased fuel restriction can lead to insufficient fuel delivery to the engine, resulting in reduced performance or even engine stalling during high-demand periods.
Therefore, it is crucial to select a fuel line diameter that is appropriate for your engine's fuel flow requirements. Using a fuel line with a larger diameter can help minimise fuel restriction and ensure an adequate fuel supply during both normal and high-demand operating conditions. Additionally, the length of the fuel line and the number of bends or fittings should be considered, as these factors can also impact fuel restriction and flow.
Craftsman Model 358797290: Replacing Fuel Lines Like a Pro
You may want to see also