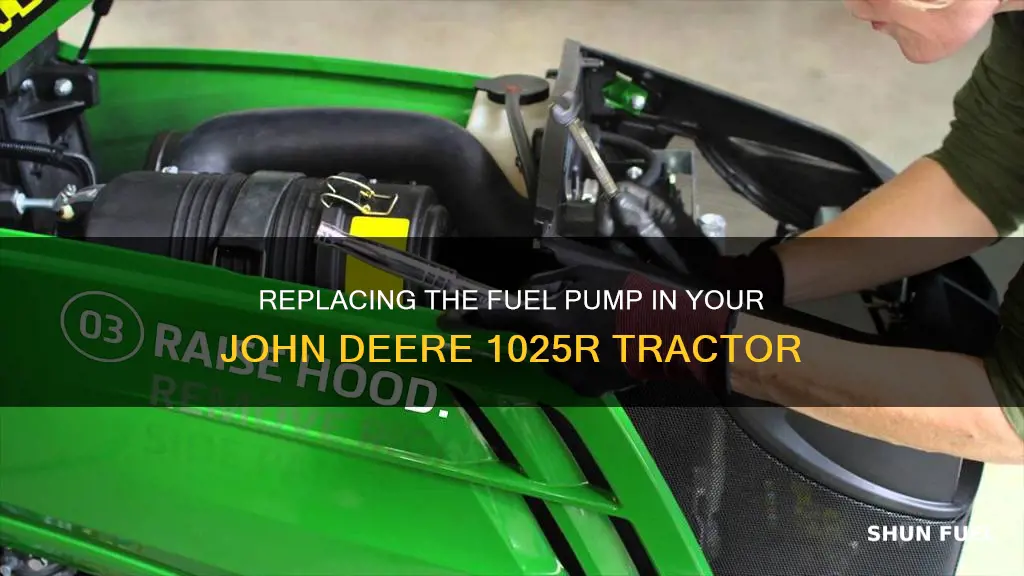
Replacing the fuel pump on a John Deere 1025R tractor is a straightforward process that can be completed in a few steps. First, park the machine and allow the engine to cool. Next, close the fuel shutoff valve at the fuel filter and water separator, clamping or pinching the inlet hose to prevent draining. Disconnect the inlet and outlet hose clamps and the wiring harness, then remove the fuel pump mounting cap screws. To install the new fuel pump, simply reverse the removal process. Finally, turn on the fuel shutoff valve and turn the key switch to the on position for 20-30 seconds to bleed air from the system.
Characteristics | Values |
---|---|
Vehicle Type | Sub Compact Utility Tractors (SCUT) |
Vehicle Make | John Deere |
Vehicle Model | 1025R |
Fuel Pump Type | 12V |
Fuel Pump Part Number | AM876266 AM876207 |
Fuel Pump Replacement Cost | $19.50 |
Fuel Pump Installation Steps | 1. Park machine safely. 2. Allow engine to cool. 3. Close fuel shutoff valve at the fuel filter and water separator. 4. Clamp or pinch inlet hose end to prevent draining from tank due to gravity. 5. Remove inlet and outlet hose clamps at fuel transfer pump and disconnect hoses. 6. Disconnect wiring harness at connector. 7. Remove two fuel pump mounting cap screws. 8. Install pump in the reverse order of removal. 9. Turn on fuel shutoff valve and turn key switch to ON position for 20 or 30 seconds to bleed air from the system. |
What You'll Learn
Park machine and allow engine to cool
Before you begin to replace the fuel pump on your John Deere 1025R, it is important to find a safe place to park your machine and allow the engine to cool. This is a crucial step to ensure your safety and the integrity of the machine during the fuel pump replacement process. Here are some detailed instructions to guide you through this step effectively:
Step 1: Park the Machine Safely
Park your John Deere 1025R in a flat and open area, away from any obstacles or hazards. Ensure that the surface is level and stable to prevent any accidental movement of the machine during the repair work. Engage the parking brake to keep the tractor securely in place and prevent any unintended rolling.
Step 2: Allow the Engine to Cool Down
Before proceeding with any maintenance or repair work, it is essential to allow the engine to cool down completely. Give the engine sufficient time to cool, especially if it has been running for an extended period. This step is crucial for your safety and to prevent the risk of burns or damage to any components from the high temperatures generated during operation.
Step 3: Understand the Importance of Cooling
The engine of your John Deere 1025R generates a significant amount of heat while running, and it is crucial to let it cool down before performing any maintenance or repairs. Working on a hot engine can be dangerous and may lead to burns or other injuries. Additionally, certain components and fluids can be under pressure when the engine is hot, and working on them without allowing them to cool can result in spills or leaks that may cause damage to the machine or the environment.
Step 4: Be Patient During the Cooling Process
Depending on the ambient temperature and the duration of machine operation, the cooling-down process can take some time. Be patient and allow the engine to cool naturally. Do not attempt to accelerate the cooling process by using water or other cooling agents, as this can damage the engine or its components. Once the engine has cooled down, you can proceed to the next steps of replacing the fuel pump, as outlined in the service manual or other instructions.
Step 5: Prioritize Safety
While waiting for the engine to cool, use this time to gather the necessary tools and equipment for the fuel pump replacement. Ensure that you have a suitable workspace with adequate lighting and a flat surface to place tools and parts. Put on appropriate personal protective equipment (PPE), such as gloves and eye protection, to safeguard yourself during the repair work.
How Often Should You Replace Your Diesel Fuel Filter?
You may want to see also
Disconnect hoses and wiring
To disconnect the hoses and wiring of your John Deere 1025R, follow these steps:
First, park your machine on level ground and allow the engine to cool. This is important for safety and to ensure that the engine and its components are not hot when you begin working. Once the engine is cool, locate the fuel shutoff valve at the fuel filter and water separator. Close this valve to prevent any fuel leakage during the process.
Now, you'll need to prevent the fuel from draining from the tank due to gravity. To do this, clamp or pinch the inlet hose end. After securing the inlet hose, locate the inlet and outlet hose clamps at the fuel transfer pump. Remove these clamps and carefully disconnect the hoses from the pump.
With the hoses disconnected, you can now focus on the wiring. Locate the wiring harness connector and carefully disconnect it. At this point, the hoses and wiring to the fuel pump should be completely detached from the rest of the system.
The next step is to remove the fuel pump itself, but before doing so, make sure you have a suitable replacement pump on hand to install. Removing the pump without an immediate replacement could lead to fuel leakage and potential safety hazards.
If you have a replacement pump ready, proceed to remove the fuel pump mounting cap screws. There should be two screws securing the pump in place. Once these are removed, you can carefully lift and remove the pump from its mounting location.
Now that the old pump has been removed, you can install the new pump by following the previous steps in reverse. Start by securing the new pump with the mounting cap screws, then reconnect the wiring harness and the inlet and outlet hoses, ensuring all connections are secure and properly clamped.
Finally, turn on the fuel shutoff valve and turn the key switch to the "ON" position for 20-30 seconds to bleed air from the system. This will help ensure that there are no air bubbles in the fuel lines, which could cause issues with fuel flow and engine performance.
By following these steps, you should be able to successfully disconnect and replace the fuel pump hoses and wiring on your John Deere 1025R.
Replacing Ford Falcon Fuel Injectors: A Step-by-Step Guide
You may want to see also
Remove fuel pump mounting cap screws
To remove the fuel pump mounting cap screws, you will need to first park your machine safely and allow the engine to cool. Once the engine is cool, close the fuel shutoff valve at the fuel filter and water separator. Clamp or pinch the inlet hose end to prevent draining from the tank due to gravity.
Now, you can remove the inlet and outlet hose clamps at the fuel transfer pump and disconnect the hoses. Disconnect the wiring harness at the connector.
Finally, you can remove the two fuel pump mounting cap screws. Be sure to keep them in a safe place so that you can reinstall the pump if needed.
Tractor Fuel Injector Replacement: A Step-by-Step Guide
You may want to see also
Check for air in the system
To check for air in the system, you can perform the following steps:
Firstly, locate the fuel filter and the fuel hose connected to it. Place a bucket underneath the fuel hose to catch any spilling fuel. Then, turn the key in the ignition to the first position. This will activate the fuel pump, which will start to draw out the fuel from the tank. Ensure you have a firm grip on the hose and be prepared for fuel to begin flowing once the pump is activated.
By performing this action, you are manually engaging the fuel pump to draw out any air that may be trapped in the system. This process will also help to prime the fuel system, ensuring that fuel is being delivered efficiently to the engine.
If you notice that the fuel appears aerated or bubbly, this is an indication that there is air in the system. At this point, you can either continue to run the fuel pump for a short period to see if the air is removed or proceed to bleed the fuel system.
To bleed the fuel system, you will need to locate the bleed screw or valve, which is usually found on the fuel filter housing or on the fuel injectors. Loosen this screw slightly with an appropriate tool, being careful not to remove it completely, as fuel will spray out. You should also have a container ready to catch any spilling fuel. Once the screw is loosened, manually turn the ignition over several times without starting the engine. This action will help to force out any air trapped in the fuel lines and injectors. Retighten the screw when finished.
After completing these steps, attempt to start the engine. If the engine starts and runs smoothly, you have successfully removed the air from the system. If the engine still exhibits issues, there may be other underlying problems that require further diagnosis and repair.
Replacing the Fuel Pump in Your 2004 VW Jetta Wagon
You may want to see also
Reinstall in reverse order
To reinstall the fuel transfer pump in your John Deere 1025R, you will need to reverse the removal steps.
First, turn the key switch to the 'ON' position and leave it for 20 to 30 seconds to bleed air from the system. Next, tighten the two fuel pump mounting cap screws. Reconnect the wiring harness at the connector. Reattach the inlet and outlet hoses to the fuel transfer pump, and secure them with the hose clamps. Ensure the hoses are correctly attached to prevent leaks. Finally, open the fuel shutoff valve, and your tractor should be ready to operate again.
Replacing GM Fuel Sending Unit: Step-by-Step Guide
You may want to see also
Frequently asked questions
If your tractor is not getting fuel, you may need to replace the fuel pump. Check for broken wires or anything odd. If you don't see anything wrong, the fuel pump may not be getting power.
First, park the machine and allow the engine to cool. Close the fuel shutoff valve at the fuel filter and water separator. Clamp or pinch the inlet hose end to prevent draining from the tank due to gravity. Disconnect the inlet and outlet hose clamps and wiring harness at the connector. Remove the two fuel pump mounting cap screws and install the new pump in the reverse order.
Check that fuel can get out of the tank to the filter, the filter is the correct way up, and that you've bled the air out of the system before starting the engine. The engine may be sucking air somewhere, so check the O-ring and run the priming pump until the bowl is full of fuel.