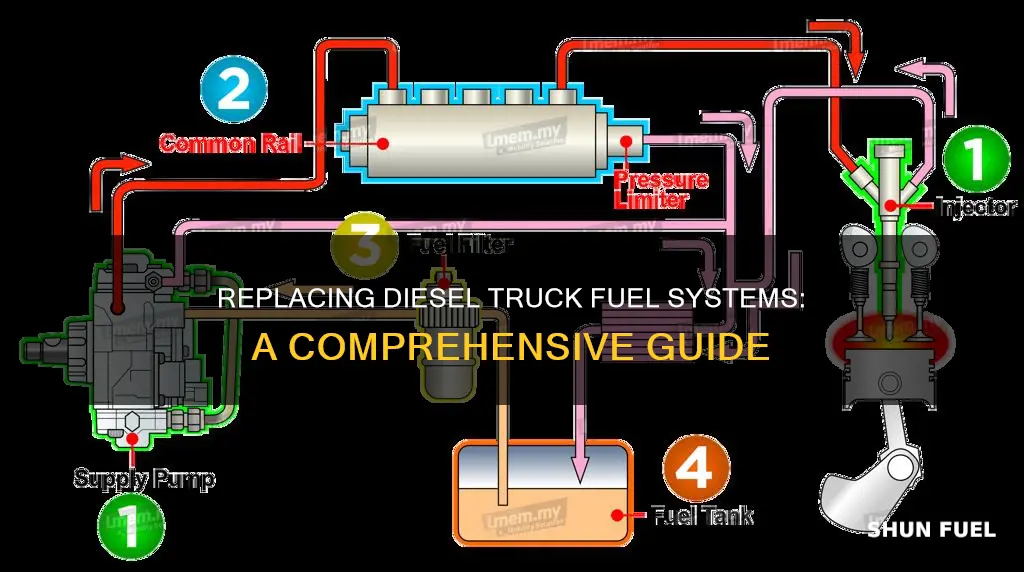
Replacing the fuel system in a diesel truck is a complex process that requires expertise and specialized tools. Diesel engines, such as Cummins, Paccar, and Volvo, have unique fuel systems that demand specific knowledge for replacement. Before attempting any replacement, it is crucial to consult the manufacturer's service manual or seek assistance from a qualified technician. The process typically involves disconnecting the battery, carefully removing the old fuel system components, thoroughly cleaning the area, installing the new fuel system according to manufacturer specifications, and reassembling the engine components. Contamination is a significant concern during installation, as it is the leading cause of premature fuel injector failures. Additionally, proper disposal of old diesel fuel and filters is essential, as it can have negative environmental consequences.
Steps to replace a diesel truck fuel system:
Characteristics | Values |
---|---|
Step 1: Prepare your service area | Ensure you have a spotless service area and the proper tools for the job. |
Step 2: Disconnect the battery | Disconnect the negative battery cable to prevent electrical issues or accidental engine starting. |
Step 3: Remove the old injectors | Remove covers, assemblies, and disconnect fuel lines. Clean and set aside components for reinstallation. |
Step 4: Clean the engine | Clean each injector cylinder and remove any fuel, water, or contaminants. Remove tip gaskets and wipe away dirt, grime, or debris near cylinders or on injector clamps. |
Step 5: Prepare new injectors | Carefully remove new injectors from packaging and lubricate them in advance of installation. |
Step 6: Install the new injectors | Delicately press new injectors into each cylinder by hand, guiding them carefully to avoid damage. |
Step 7: Secure the injectors | Use a hold-down clamp to lock the injector into the cylinder. Torque the bolt of the hold-down clamp with a specialty torque wrench to ensure proper torque and angle. |
Step 8: Reassemble the engine | Reassemble engine components, ensuring proper alignment and connection of wiring, hoses, sensors, etc. |
Step 9: Test and verify | Start the engine and monitor for fuel leaks, abnormal noises, or performance issues. Perform additional checks, such as balance and fuel pressure tests, to verify the repair. |
What You'll Learn
How to replace a diesel fuel filter
Diesel fuel is quite dirty, so it's important to keep your fuel filters clean to ensure optimal engine performance. Most diesel engines have two fuel filters: a primary and a secondary filter. The primary filter is usually located on the fuel line between the fuel tank and the engine, while the secondary filter is typically found near the engine. It is recommended to change both filters before colder weather arrives and approximately every 10,000 to 15,000 miles.
- Locate the primary fuel filter: The first fuel filter will be on the fuel line and should be underneath the vehicle. Place an oil drain pan directly underneath the filter to catch any spills.
- Remove the fuel filter housing plug: Using the proper tool, usually an Allen wrench or a hex tool, remove the fuel filter housing plug and allow the fuel to drain into the pan. Once completely drained, secure the plug.
- Remove the primary fuel filter: Use a wrench and socket to loosen the cap and remove the first fuel filter.
- Locate and remove the O-ring: Use a flathead screwdriver to separate the O-ring on the cap. Dispose of the old ring, as the new filter will come with a new one.
- Clean the housing and sealing surface: Before installing the new fuel filter, use a clean cloth to wipe the inside of the housing and the sealing surface.
- Install the new O-ring and filter: Place the new O-ring on the cap and secure it. Then, put the new filter inside the cap and secure both inside the housing. Tighten by hand, and then finish tightening with a torque wrench.
- Repeat for the secondary fuel filter: Move the oil drain pan to underneath the secondary filter and repeat steps 1 through 3.
- Properly dispose of old filters and diesel fuel: Do not dump old diesel fuel down a drain or dispose of it with your trash. Recycle the diesel fuel at a suitable recycling center in your area.
Remember to update your maintenance records after completing this task, so you know when to perform it again. Replacing your diesel fuel filters regularly is crucial for the smooth operation of your diesel-powered vehicle.
Replacing Fuel Pump in Crown Victoria: Step-by-Step Guide
You may want to see also
Disconnecting the battery
To begin, locate the battery and identify the negative terminal, which is usually marked with a "-" symbol or a black cover. You may need to remove a protective cover or plastic casing to access the terminal. Once located, proceed to disconnect the negative battery cable by loosening the clamp or bolt that secures it to the terminal. Use the appropriate tool, such as a wrench or socket, to loosen it, being careful not to damage the cable or terminal.
After the cable is disconnected, secure it away from the battery to prevent accidental contact. You can use a cable tie or zip tie to hold it in place, ensuring it doesn't touch any metal parts of the vehicle. It is important to note that modern vehicles may have multiple batteries or complex electrical systems, so ensure you refer to the vehicle's manual for specific instructions.
Additionally, it is recommended to discharge any built-up static electricity from your body before proceeding with the fuel injector replacement. You can do this by touching a metal part of the vehicle's chassis or engine block before handling any electrical components. This step is crucial to prevent any accidental electrical discharge, which could damage sensitive electronic components.
Once the battery is disconnected and you have discharged any static electricity, you can proceed with the next steps of the fuel injector replacement process, ensuring you follow the vehicle and engine manufacturer's recommendations and guidelines.
Replacing Fuel Pump in 2002 Ford Explorer: Step-by-Step Guide
You may want to see also
Removing the old injectors
Firstly, ensure the truck is stabilised in a service bay, with the keys removed from the ignition and the battery supply disconnected. This is an important safety precaution to prevent any electrical issues or accidental starting of the engine.
Next, locate the fuel injector on the engine. Carefully disconnect the electrical connector and fuel line connections. Remove any components, such as valve covers or intake manifolds, that may be obstructing access to the fuel injector.
Once you have clear access to the fuel injector, loosen and remove the retaining bolts or clamps securing it. Be sure to keep the removed components organised and clean, to facilitate easy reinstallation when the new injectors are in place.
After removing the injector, thoroughly clean the injector bore and the surrounding area to eliminate any dirt, debris, or carbon deposits.
At this point, the old injector has been successfully removed, and you can proceed to install the new injector, following the manufacturer's specifications and procedures. Ensure the injector is properly seated and aligned, and replace any necessary seals, O-rings, or gaskets.
It is important to carefully follow all truck and engine OEM recommendations during this process, as each manufacturer's engine design and fuel injector system is unique. Additionally, in cases where an injector has failed prematurely, it is advisable to identify the root cause of the failure to prevent recurrence with the new injectors.
Replacing the Fuel Pump in Your 2003 Malibu: Step-by-Step Guide
You may want to see also
Cleaning the engine and injector cylinders
Step 1: Prepare your service area
Having a spotless service area is essential when replacing fuel injectors. Contamination is the leading cause of premature fuel injector failures, so ensure your workspace is clean before you begin.
Step 2: Remove the old injectors
Once your truck is stabilized in a service bay, with the keys removed from the ignition and the battery supply disconnected, you can start to remove the old fuel injectors. Remember to carefully follow the manufacturer's recommendations, as each engine design is unique.
Step 3: Clean the engine and injector cylinders
This step is crucial. Each injector cylinder must be cleaned and purged, removing any fuel, water, or other contaminants. Remove the tip gaskets, which sit within the cylinder, and wipe away any dirt, grime, or debris near the cylinders or on the injector clamps. Install clean, fresh replacements for the old gaskets.
Step 4: Prepare the new injectors
Before installing the new injectors, carefully remove them from their packaging and lubricate them.
Step 5: Install the new injectors
Delicately press each new injector into its cylinder by hand, guiding it carefully to avoid any damage to the injector tip. Injector nozzle tips are microscopically small, so it doesn't take much to impact their functionality.
Step 6: Secure the injectors
The injectors should fit firmly into the cylinder with minimal effort. Do not use a hammer or any blunt instrument. After positioning, use a hold-down clamp to lock the injector in place, and torque the bolt with a specialty torque wrench to ensure proper torque and torque angle.
Step 7: Final steps
Once all new injectors are installed, reconnect the fuel lines and reposition assemblies, covers, and other components. Finally, add the specialized TRIM codes that come with the new injectors into the engine's electronic control module (ECM).
The Evolution of Fuel Injection: Replacing Carburetors
You may want to see also
Installing the new injectors
Now that the old injectors have been removed and the engine and new injectors have been cleaned, it's time to install the new injectors.
Experts say new injectors should be delicately pressed into each cylinder by hand. When moving the injector into place, ensure that the injector tip doesn't encounter anything that could cause damage. Injector nozzle tips are microscopically small, with diameters of typically 200 microns or fewer, so it doesn't take much contact or contamination to impact their functionality.
Pure Power Technologies' Prototype Engineer, Nelson Dowdey, recommends that new injectors should not be unboxed until they are ready to be installed. Each component should be carefully removed from its packaging and lubricated in advance of installation.
Once the new injectors are in place, they should fit firmly into the cylinder with minimal effort. Technicians should never use a hammer or blunt instrument to drive an injector in place. After an injector is positioned, a hold-down clamp should be used to lock the injector into the cylinder. Dowdey suggests using a specialty torque wrench to torque the bolt of the hold-down clamp to ensure proper torque and torque angle.
It is important to follow the manufacturer's recommendations during injector installation, as different engines and injector systems may require additional steps or components to be replaced. For example, O-rings are replaced during the remanufacturing process and can become damaged during installation, so these should be properly installed and aligned to prevent poor injector performance.
Once all the new injectors have been installed, the technician can then reconnect fuel lines and reposition assemblies, covers, and other related components.
Replacing Fuel Filter in 2003 Suburban: Step-by-Step Guide
You may want to see also