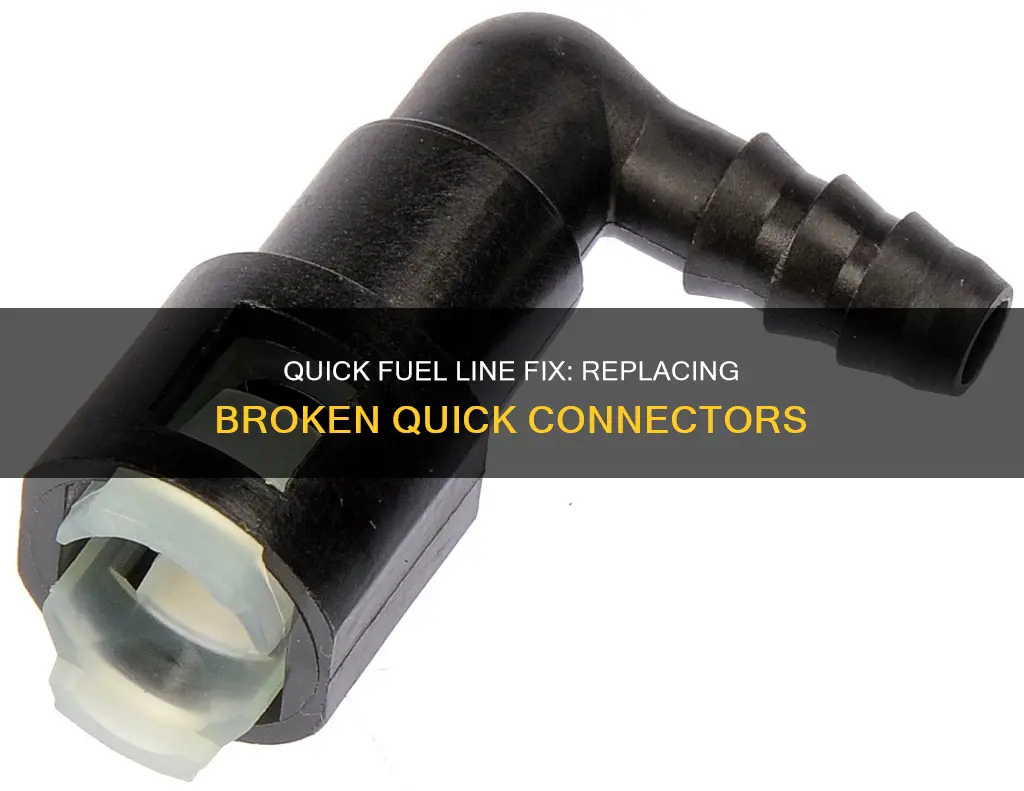
Fuel lines are prone to failure over time, and repairing them can be a complex task due to the variety of fittings and connectors used in modern fuel injection systems. In this guide, we will cover the steps to replace a broken fuel line quick connector, ensuring a safe and secure repair. It is important to note that working on fuel lines can be dangerous, and all sources of ignition should be kept away from the work area. Let's get started!
Characteristics | Values |
---|---|
Problem | A broken fuel line quick connector |
Solution | Replace the broken connector with a new one |
Tools | A short handheld tubing bender, a tubing cutter, a wood screw, a hack saw, a nylon line cutter, a flaring tool clamp, a caulking gun, a single edge razor blade or tubing cutter, a screwdriver, a wrench |
Materials | A repair kit, a replacement quick connect fitting, a length of fuel line, a compression fitting, a ferrule, a barbed fitting, a splice kit, a splice union, a rubber hose, hose clamps, fuel injection clamps, a splice barb, a quick-connect barrel connector, a new fuel line, a splice with a barb union and hose clamps, a jubilee patch, a rubber patch, plumbing epoxy, race tape, a lighter, electrical tape, bubblegum, duct tape, rubber bands, tootsie rolls, butter, a new section of cheap garden hose, a piece of rubber, a hose clamp |
What You'll Learn
Identify the type of fuel line and fittings
Identifying the type of fuel line and fittings in your car is crucial before attempting any repairs or replacements. Here's a comprehensive guide to help you identify them:
Fuel Line Types:
- Metal Lines: Metal lines, typically made of stainless steel, aluminum, or coated steel tube, are the most common type used in factory-made cars due to their durability. However, they can be challenging to fabricate.
- Rubber Fuel Hose: This type of fuel line is easy to install and is connected using barbed fittings and fuel line hose clamps. It must meet specific SAE grades, such as SAE J30R7 for carbureted engines and SAE J30R9 for fuel injection systems. Rubber hoses degrade over time, may leak fuel vapors, and are susceptible to cuts and abrasions.
- Nylon Tubing: Nylon tubing is a more affordable option for fuel line repairs and offers better durability than plain rubber hoses.
- Braided Hose: Braided hoses have a rubber core with a braided stainless steel or nylon exterior. They use AN hose ends for connections but still face issues with long-term durability and fuel vapors.
- PTFE Lined Hose: PTFE-lined hoses is the best soft hose option, featuring a PTFE liner that prevents fuel vapors from escaping and slows down degradation. It requires special fittings and is less flexible than other options.
Fuel Line Fittings:
There are various types of fittings used in fuel systems:
- Push-On Fittings: Most production cars use push-on hose fittings, which are typically 8mm in bore size. These hoses are secured with hose clips or factory swaging, where a metal collar is crimped over the hose.
- Screw-On Fittings: Competition or modified cars often use screw-on fittings, such as JIC/AN fittings, which are identified by their thread size and hose size.
- Quick-Release Fittings: Some modern cars may have quick-release fittings on the fuel rail, filter, etc.
- Adapter Fittings: Adapter, standard, or union fittings are used to connect fuel lines to fuel pumps, regulators, and filters. They can have SAE or AN (Army-Navy) specifications, with AN fittings featuring a 37-degree cone and straight thread, requiring O-ring seals.
- Port Fittings: Port fittings, also known as O-Ring Base or ORB fittings, are similar to pipe fittings but conform to AN standards. They use straight thread, a 37-degree cone, and O-rings for sealing.
- Pipe Fittings: Pipe fittings use tapered thread (also called pipe thread) and require sealing compounds or Teflon tape to prevent leakage. They are commonly used to connect fuel lines to fuel pumps, pressure regulators, and pressure gauges.
When identifying the type of fuel line and fittings, it's important to consider the vehicle's make, model, and year. Additionally, always refer to the manufacturer's recommendations and consult a professional if you're unsure about the identification or repair process.
Replacing Fuel Lines: Astro Van 2002 Edition
You may want to see also
Use a repair kit for nylon lines
If you are repairing a broken fuel line quick connector, one option is to use a repair kit for nylon lines. This is a simple process that involves measuring the line, cutting it, and installing the end fittings. While it is a straightforward process, installing the end fittings can be challenging without the proper tools.
There are a variety of nylon fuel line repair kits available on the market, such as the Dorman 800-300 Nylon Fuel Line Repair Kit, which comes with 104 pieces for a universal fit. These kits typically include the necessary tools and fittings to make the repair, such as a cutter for the nylon tube, a hose press or a handheld tool that performs the same function, and a special tool for the mini crimp-clamps.
When repairing a nylon fuel line, it is important to ensure that the line is cut cleanly, without any pinching or burrs. Warming the end of the nylon tube in hot water can help when installing the fittings by hand, but this method can be difficult and may result in kinks in the line. Using a hose press or a handheld tool that resembles a caulking gun can make the job easier and ensure a secure connection.
Additionally, when repairing a fuel line, it is crucial to use fuel line-rated hose and clamps that can withstand the pressure of the fuel system. It is also recommended to double-clamp the connections for added safety.
Replacing Fuel Injector in Ford 9700 Tractor: Step-by-Step Guide
You may want to see also
Prepare the area and cut the line
Before you start, make sure you have the necessary tools and materials. You will need a wood screw, a drain pan, wire cutters or a small hacksaw, a replacement fuel line, and a tapered fuel line connector.
Now, let's get started on preparing the area and cutting the line:
Firstly, locate the broken fuel line and place a drain pan underneath the area to catch any fuel that may leak during the repair process. It is crucial to keep the area well-ventilated and free from any sources of ignition to prevent accidental fires.
Once the area is prepared, use the wire cutters or small hacksaw to carefully cut and remove the damaged section of the fuel line. Make sure to cut the line as close to the broken area as possible, ensuring that there is enough straight line left to install the new connector securely.
After cutting the line, use a wood screw that is large enough to thread into the fuel line. Install this screw in the line to prevent further fuel leakage during the repair process.
Now, take the piece of the fuel line that you removed and use it as a reference to purchase the correct size of replacement line and fitting. It is important to get the right size to ensure a secure and leak-free connection.
With the necessary materials ready, hold the replacement line in position and mark the point where you need to cut it to match the existing line. Use a nylon line cutter or a suitable cutting tool to cut the new line to the marked length.
At this stage, you have successfully prepared the area and cut the fuel line. You can now proceed to the next steps of the repair process, which involve connecting the new line and securing it in place. Remember to work carefully and always prioritize your safety when dealing with fuel lines.
Replacing Fuel Injectors: 1991 Silverado V6 Guide
You may want to see also
Use a tapered connector to join the lines
If you're repairing a broken fuel line, you can use a tapered connector to join the lines. Tapered connectors are perfect when you don't have the option of installing two equal-diameter spigots. They can be used to reduce pipe size, directing the product into a smaller pipe and reducing or controlling the flow rate. This can be useful when dealing with fuel lines, as you can control the flow of fuel.
Tapered connectors can also help reduce wear on connector walls. If you have a small-diameter inlet pipe at the top and transition it to a larger-diameter outlet pipe below, this allows your product to flow through with minimal contact with the connector walls. This is useful when dealing with fuel, as it is a highly flammable substance.
Tapered connectors are also useful when you have mismatched pipe diameters. They can be used in applications where you need to transition between two transmission lines with different widths but the same impedance, or with different widths and different impedance. This makes them ideal for fuel lines, as you can join two fuel lines with different diameters.
When using a tapered connector, it is important to ensure that you have the correct size and type of connector for your specific application. You may also need to consider the amount of tape or compound used to seal the connection, as well as the tightness of the fitting.
Fuel Filter Replacement: Signs You Need to Know
You may want to see also
Check for leaks
Once you have replaced the broken fuel line quick connector, you will want to check for leaks. Fuel leaks can be very dangerous, so it is important to take precautions. Do not smoke while you are working, and park the vehicle outside and away from appliances with an active pilot light. If your clothes become fuel-soaked, change them immediately and wash contacted skin with mild soap and plenty of fresh water.
To check for leaks, you will need to raise the vehicle and support it on jack stands. Using a flashlight, trace the fuel lines from the tank to the engine, looking for evidence of the leak. This may include spots with a greater accumulation of dust and road grime, wet spots or streaks, or clean spots where the fuel has washed away grime. If you find evidence of dripping, follow the path of the dripping fuel to discover the source. Remember that gravity and wind pressure can affect the path of travel, so the fuel may be running along a series of members before it drips out.
There are several products available that can be added to your fuel to help locate the source of a leak. These products contain a dye that will glow under fluorescent or ultraviolet light. After adding the dye to your fuel, run the engine so that some of the treated fuel leaks out, then perform a visual inspection with a handheld light.
Some leaks may be well-hidden and defy attempts to find them visually. In these cases, you can use a device known as a leak detector, which has a probe that can be inserted into areas that are not readily visible. The device will detect the presence of compounds within both gasoline and diesel.
Air-Fuel Ratio Sensors: When and Why to Replace Them
You may want to see also
Frequently asked questions
Keep all sources of ignition away from the area to prevent accidental fires. Never use an electric tool of any kind when working on a fuel line. If one drop of fuel or vapour contacts the arc from the electric motor, it could cause a fire.
You will need a wood screw, a drain pan, wire cutters or a small hacksaw, a nylon line cutter, a tubing bender and a tubing cutter.
You will need a repair kit, which includes a gun, two opposing blocks with multiple-sized holes, and a nylon-tubing cutter. You will also need a tapered connector with three step-downs, a small amount of oil, and a new fuel line.
First, install a wood screw into the broken fuel line to prevent further draining. Then, cut the broken section of the fuel line and install the wood screw. Next, cut the replacement line to size and place the opposing ends of the fuel lines into the threaded side of the blocks, allowing 1/4 inch to protrude. After that, oil the tapered connector and place it into one side of the fuel line. Finally, squeeze the blocks together using the gun until the connector is fully seated on all three steps in both ends of the fuel line.