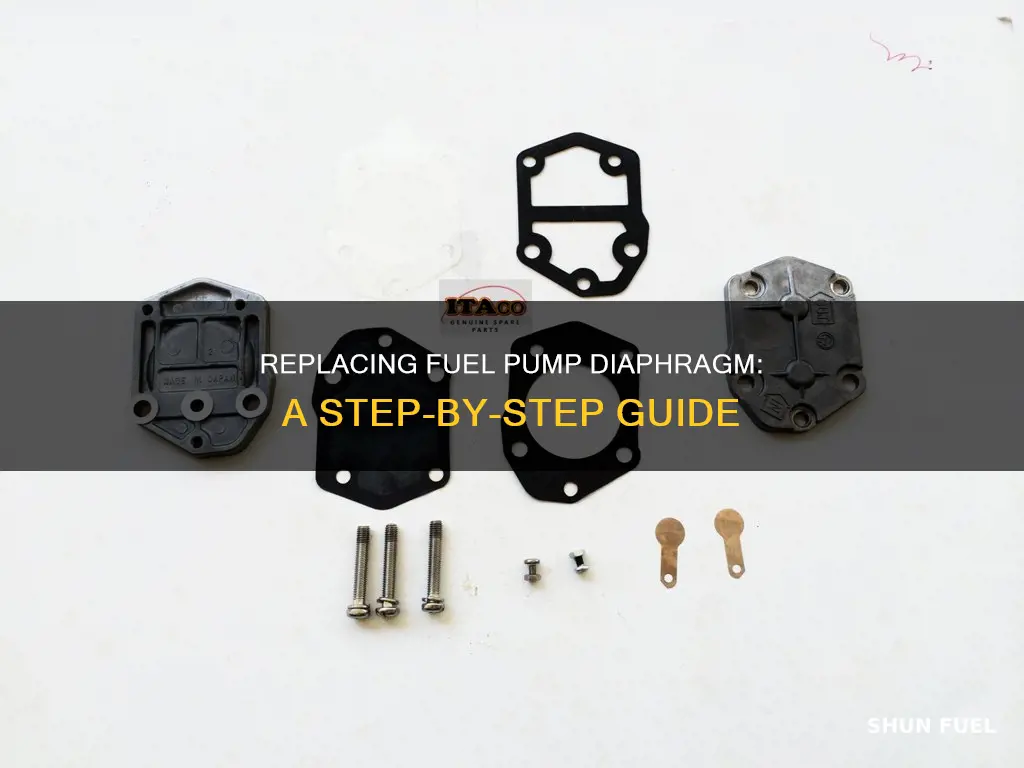
Replacing the fuel pump diaphragm can be a tricky task, but with the right tools and knowledge, it can be done successfully. The fuel pump diaphragm is responsible for regulating fuel flow and pressure in the engine, and a faulty or worn-out diaphragm can cause various issues, including reduced engine performance and fuel leaks. Before beginning the replacement process, it is crucial to source a suitable replacement diaphragm made from Viton, a type of sheet rubber that can withstand modern gasoline. It is also important to never use Teflon thread-sealing tape anywhere in the fuel system, as this can cause significant problems. When disassembling the fuel pump, care must be taken not to damage the diaphragm or other components, and it is recommended to mark the pump halves for accurate reassembly. After removing the old diaphragm, the new diaphragm can be installed, ensuring that all seals and gaskets are in good condition and properly aligned. Finally, the pump can be reassembled, tightened, and tested for proper function.
What You'll Learn
- Ensure the replacement diaphragm is made of VITON
- Don't use Teflon thread sealing tape in the fuel system
- Check for leaky check valves, a worn-out diaphragm, a broken spring or a leaky sediment bowl gasket
- Mark both halves of the pump so you can refit them in the same position
- Wash all parts with clean petrol and a fine paintbrush
Ensure the replacement diaphragm is made of VITON
When replacing your fuel pump diaphragm, it is crucial to ensure that the replacement diaphragm is made of VITON. VITON is a type of sheet rubber that can withstand modern gasoline, and it is the only material suitable for this purpose. Other materials such as Nitrile, Buna N, and Neoprene will eventually deteriorate when exposed to modern gasoline, leading to a sticky mess in your carburetor. Not only that, but the use of these unsuitable materials can also result in fuel leakage into your crankcase, posing a serious safety hazard as it may lead to a violent explosion.
VITON is specifically designed to be compatible with modern gasoline and will not suffer the same fate as other materials. It is essential to prioritize your safety and the proper functioning of your vehicle by insisting on VITON for your fuel pump diaphragm replacement. This is not an area where you want to cut corners or compromise on quality. The consequences of using inferior materials can be severe and far-reaching.
When sourcing a replacement diaphragm, be cautious of some materials marketed as fuel pump diaphragm alternatives. For example, while nitrile rubber, commonly found in work gloves, may be suggested, it is not an ideal long-term solution. Testimonies from those who have used this material reveal that it tends to fail after a year or two due to a lack of reinforcing mesh. Similarly, some materials sold on eBay from Chinese sellers have been reported to curl up and become brittle when soaked in fuel.
To ensure you are getting a genuine VITON diaphragm, it is advisable to purchase from reputable suppliers or opt for factory replacement parts. This may include sourcing from specialty suppliers or directly from the manufacturer. While the cost may be higher, it is a worthwhile investment to safeguard your vehicle and your well-being.
Replacing Fuel Lines: 1998 Chevy Silverado Step-by-Step Guide
You may want to see also
Don't use Teflon thread sealing tape in the fuel system
When replacing a fuel pump diaphragm, it is important to be aware of the potential issues that can arise when using Teflon thread sealing tape in the fuel system. While it may seem like a convenient and cost-effective option, there are several reasons why it is not recommended to use Teflon tape for sealing fuel fittings and fuel lines.
Firstly, there is a risk of the tape breaking free and clogging sensitive components downstream. Mechanics often encounter issues with fuel injectors, fuel pumps, and carburetors, which can be traced back to clogging caused by pieces of Teflon tape that have washed off the ends of the threads. This can result in costly repairs. Liquid or paste-type sealants are a better alternative as they do not pose the same risk of clogging.
Secondly, Teflon tape may degrade over time with fuel contact and break down, which can lead to leaks in the fuel system. While some people suggest that any type of PTFE thread sealant would be safe to use with fuel, others recommend avoiding Teflon tape altogether and opting for a fuel line-specific thread sealant instead. It is worth noting that if you do choose to use Teflon tape, it is important to ensure that there is no excess tape that can break off and get stuck in the fuel line.
Additionally, when choosing a thread sealant, it is crucial to consider its chemical resistance to the type of fuel (diesel or gasoline) or oil running through the line. Regular gas-resistant Teflon tape may not be sufficient and could potentially cause issues down the line. Therefore, it is always recommended to consult a professional or refer to manufacturer guidelines when selecting the appropriate sealant for your fuel system.
Finally, it is important to follow the proper installation procedures when working with fuel systems. This includes consulting a professional or having your work inspected to ensure there are no fuel leak hazards. It is also advisable to have the system pressure-tested by a qualified individual whenever alterations are made to the fuel line assembly.
Replacing Quick Disconnect Fuel Lines: A Step-by-Step Guide
You may want to see also
Check for leaky check valves, a worn-out diaphragm, a broken spring or a leaky sediment bowl gasket
To check for a leaky check valve, you can perform a pressure test. This involves pressurising the fuel system and then blocking the return line to observe if the pressure drops. If the pressure drops, this could indicate a leaky check valve or leaky injectors. To confirm it is the check valve, you can also try blocking both the feed and return lines. If the pressure holds, the issue is likely not with the injectors.
To identify a broken spring in a fuel pump, you can inspect the spring for any visible signs of damage, such as being sheared in half. If the spring is broken, it is recommended to replace the entire fuel pump, as a weak spring could indicate that the rest of the pump is also wearing out.
A leaky sediment bowl gasket can often be identified by a leaking fuel pump. If you notice fuel leaking, try cleaning the surfaces of the pump and the bowl, ensuring they are smooth. You can also try treating the gasket with soap-based bearing grease before installation. If the gasket is cork, ensure it is thick enough and not too tightly screwed in, as this can cause it to weaken and split. Alternatively, you can try using a rubber gasket instead of cork, as fuel can sometimes cause cork to swell and distort.
To identify a worn-out diaphragm, you can perform the following test: leave the hoses attached to the fuel pump and remove the screws attaching the pump to the powerhead. Reinsert the screws with nuts to clamp the pump together. With the fuel line attached, pump the primer bulb while observing the pressure/vacuum operating hole. If fuel leaks out of this hole, the diaphragm is faulty and will need to be replaced or rebuilt.
Replacing the Fuel Pump on a Kohler Engine: Step-by-Step Guide
You may want to see also
Mark both halves of the pump so you can refit them in the same position
Marking both halves of the pump is an important step in the process of replacing a fuel pump diaphragm. It ensures that you can refit the pump correctly and avoid any issues that may arise from an incorrect reassembly. Here is a detailed guide on marking and reassembling the pump:
When removing the pump's cover, which is usually held by a central bolt or screw, it is crucial to keep the two halves of the pump intact. Make a mark or a scratch on both halves so that you can put them back together in the exact same position. However, be careful not to scratch a line straight across the diaphragm edge.
As you remove all the body screws, maintain pressure to keep the halves connected. The internal spring pressure will try to push them apart, so release your grip slowly. The diaphragm might be stuck, so gently free it without using a sharp metal object, as this could cause scratches and leaks.
Once you have separated the halves, carefully remove the diaphragm. Ensure it is not stuck to the housing. If it is, gently peel it upwards. Grip the centre metal flange of the diaphragm assembly and press down while rotating the diaphragm by 90 degrees to release it. If it is difficult to turn, try pushing the pump lever away from the pump body as you press down and turn.
After cleaning and replacing the necessary parts, it is time to reassemble the pump. Position the top and bottom halves together, ensuring that the outlets are correctly aligned. Insert the screws but do not tighten them yet. Pull the pump operating arm towards the pump fully, and while holding it in this position, tighten the screws securely.
Finally, before starting the engine, turn the pump slowly on the starting handle several times to ensure it turns freely. This step is crucial to verify that the pump lever is correctly positioned, and turning it by hand will confirm this. If the pump is not correctly fitted, the engine may jam, so it is important to take your time with this step.
Replacing Fuel Line in 4218AVX: A Step-by-Step Guide
You may want to see also
Wash all parts with clean petrol and a fine paintbrush
When repairing or replacing a fuel pump diaphragm, it is essential to clean all the components thoroughly before reassembling. Here's a step-by-step guide on how to approach this task:
Begin by disassembling the fuel pump and setting up a clean workspace. Have some newspaper or an old cloth laid out to catch any spills or drips. Pour a small amount of clean petrol into a container; a glass jar or metal container is ideal. Take a fine paintbrush and dip it into the petrol. Carefully brush away any dirt, debris, or old fuel residue from each part. Pay particular attention to small crevices and openings, as these areas can harbor debris that may not be easily visible.
The fine paintbrush allows you to reach these tight spaces without damaging any of the delicate components. Work systematically through each part, ensuring that you don't miss any surfaces. The petrol will help break down and dissolve any stubborn grime, and it will also evaporate quickly, leaving the parts dry and ready for reassembly. It is important to use clean petrol for this task, as dirty fuel may introduce new contaminants to the system.
Be cautious when handling petrol, and ensure adequate ventilation in your workspace. Keep away from open flames or sparks, as petrol is highly flammable. Once you have finished cleaning, allow the parts to air-dry for a few minutes. Any remaining petrol will quickly evaporate, leaving the components clean and ready for the next step in the repair or replacement process. This thorough cleaning step is crucial to ensure the fuel pump's proper function and extend the lifespan of the diaphragm and other parts.
By taking your time and using a fine paintbrush with clean petrol, you can effectively remove any harmful debris and ensure the fuel pump operates optimally. This process is a vital step in maintaining the health of your engine and fuel system.
Replacing Fuel Line O-Rings: A Step-by-Step Guide
You may want to see also
Frequently asked questions
First, search the net for your model's fuel pump rebuild kit to make sure it is available. Remove the fuel pump from the cart's engine, disassemble the pump, and remove the diaphragms, noting their placement/order. Then, replace them with the new diaphragms, reassemble, and test it out.
One method is to bolt the pump housing, with the diaphragm, to the block, turn the crankshaft until the rocker arm is on the top of the cam, and then reinstall the pump cover. Another method is to put the hosing in a vise in a position where the diaphragm is in line with the housing rim/brim, reinstall the pump cover, and then bolt the pump to the block.
First, the replacement diaphragm you install must be made of a material called VITON, as this is the only material that will withstand modern gasoline. Second, never use Teflon thread-sealing tape anywhere in the fuel system.
First, remove the screws holding the top of the pump to the body. Do not clamp the pump in a vice to dismantle it, as the pressure could break the alloy casting. Separate the halves carefully to avoid tearing the diaphragm. Then, clean and replace the pump, and reassemble the parts.