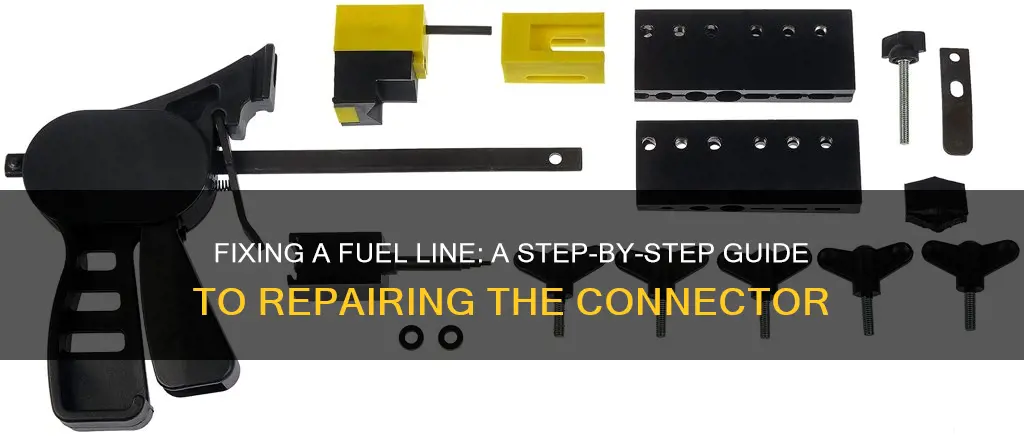
Repairing a broken fuel line connector can seem daunting, but with the right tools and a bit of know-how, it's a task you can tackle yourself. This guide will walk you through the process step-by-step, ensuring you understand the importance of proper diagnosis and the necessary safety precautions before beginning any repair work. You'll learn how to identify the issue, gather the required tools and materials, and then carefully disassemble and reassemble the connector to ensure a secure and reliable connection. By following these instructions, you'll be able to get your vehicle back on the road safely and efficiently.
What You'll Learn
- Locate the Fuel Line: Identify the damaged connector by following the fuel line from the tank to the engine
- Prepare Tools and Materials: Gather necessary tools like a fuel line repair kit, wrench, and cleaning supplies
- Remove the Connector: Carefully disconnect the damaged connector, ensuring no fuel spills
- Clean and Inspect: Thoroughly clean the connector and surrounding area, then inspect for any further damage
- Install New Connector: Attach a new connector, ensuring proper alignment and secure it with the recommended torque
Locate the Fuel Line: Identify the damaged connector by following the fuel line from the tank to the engine
To begin the repair process of a broken fuel line connector, you must first locate the fuel line and identify the damaged connector. This is a crucial step as it allows you to understand the extent of the damage and the specific area that requires attention. Start by accessing the fuel tank, which is typically located beneath the vehicle's body or in the trunk, depending on the car model. Locate the fuel line, which is a flexible tube that runs from the tank to the engine, supplying fuel to the vehicle's engine. It is important to handle the fuel line with care as it can be fragile.
Once you have located the fuel line, carefully trace it along its path towards the engine. The fuel line will likely be secured in place by rubber or plastic hoses and clips. As you follow the line, keep an eye out for any signs of damage, such as cracks, punctures, or dislodged connections. The connector, often a small fitting or coupling, is where the fuel line connects to the engine's fuel injection system or the carburetor, depending on the vehicle's setup.
Identify the specific connector by its unique shape and size, as different vehicles may have varying connector designs. The connector should securely attach the fuel line to the engine's fuel system. If the connector is damaged, you may notice leaks or spills around the connection point, indicating a potential issue. In some cases, the fuel line might have a visible break or separation from the connector, making it easier to pinpoint the problem area.
It is essential to inspect the entire length of the fuel line to ensure you don't miss any potential damage. This thorough examination will help you understand the full extent of the repair needed. Once you have identified the damaged connector, you can proceed with the appropriate repair or replacement steps, ensuring your vehicle's fuel system is safely and effectively operational again.
Fuel Line Orientation: Understanding the 'On' Position
You may want to see also
Prepare Tools and Materials: Gather necessary tools like a fuel line repair kit, wrench, and cleaning supplies
To effectively repair a broken fuel line connector, it's crucial to start by gathering the necessary tools and materials. Here's a step-by-step guide on what you should prepare:
Fuel Line Repair Kit: This is the cornerstone of your repair process. A fuel line repair kit typically includes all the components needed to fix a damaged fuel line, including specialized connectors, hoses, and sealing compounds. Look for a kit that is compatible with your vehicle's fuel line specifications.
Wrenches and Pliers: You'll need a set of wrenches and pliers to tighten or loosen connections. Ensure you have various sizes to accommodate different fuel line fittings. A adjustable wrench is versatile and can be particularly useful for gripping tight or irregular-shaped connectors.
Cleaning Supplies: Cleaning is an essential part of the repair process. Gather cleaning supplies such as a fuel line cleaner, a degreaser, and a brush or wire brush to remove any debris or contaminants from the fuel line and connectors. This step ensures a proper seal and prevents further issues.
New Gaskets or Seals (if applicable): If your repair kit includes new gaskets or seals, make sure you have a supply of these. Gaskets are crucial for creating a tight seal between fuel line connectors and preventing fuel leaks. Check the kit's contents to ensure you have the correct size and type for your fuel line.
Safety Gear: While not strictly a tool, safety gear is essential. Wear gloves to protect your hands during the repair process, and consider safety goggles to shield your eyes from any potential fuel splashes.
Having these tools and materials ready will ensure that you can efficiently and effectively repair the broken fuel line connector, minimizing the risk of further damage and ensuring your vehicle's fuel system operates safely and reliably.
Motorcycle Fuel Line Sizes: A Comprehensive Guide to Diameter
You may want to see also
Remove the Connector: Carefully disconnect the damaged connector, ensuring no fuel spills
When dealing with a broken fuel line connector, the first step is to ensure your safety and that of your surroundings. Before you begin any repair, make sure the engine is cool to prevent any accidents. Locate the fuel line connector, which is typically a small, cylindrical component that connects the fuel line to the engine. It is usually positioned near the engine bay, close to the fuel pump or the fuel injectors.
Carefully inspect the connector to identify the extent of the damage. If the connector is cracked, leaking fuel, or showing visible signs of corrosion, it needs to be replaced. Take note of the position of the connector relative to other components to ensure proper alignment during reattachment.
Now, proceed with disconnecting the damaged connector. Start by locating the fuel line that is connected to the connector. Use a fuel line disconnect tool or a pair of pliers to carefully grip and pull the fuel line away from the connector. Be gentle to avoid damaging the fuel line itself. Once the fuel line is disconnected, you should see the connector come loose.
As you remove the connector, be cautious of any remaining fuel in the line. Fuel can be hazardous, so take extra care to prevent spills. Hold the connector at an angle to allow any remaining fuel to drain back into the fuel tank. If you notice any fuel leaking, stop the process immediately and address the issue to prevent further damage or hazards.
Once the connector is disconnected, you can now proceed with the repair or replacement process. Ensure that you have the necessary replacement parts and tools ready before starting the repair to avoid any unnecessary delays. Remember to follow the manufacturer's instructions for the specific model of your vehicle to ensure a proper and safe repair.
Unraveling the Mystery: Lines Attached to the Fuel Pump
You may want to see also
Clean and Inspect: Thoroughly clean the connector and surrounding area, then inspect for any further damage
When dealing with a broken fuel line connector, the first step is to ensure a thorough cleaning and inspection process to identify any potential issues and ensure a proper repair. Start by gathering the necessary tools and materials, including a fuel line cleaner, a soft-bristled brush, a clean rag, and a magnifying glass or small flashlight for detailed inspection.
Begin by disconnecting the fuel line from the engine and placing it in a suitable container to catch any fuel that may spill. This step is crucial to prevent any fuel from contaminating the surrounding area and causing further damage. Once the fuel line is disconnected, use the fuel line cleaner to thoroughly clean the connector and the surrounding area. Apply the cleaner directly to the connector and use the brush to gently scrub away any debris, corrosion, or fuel residue. Ensure that you clean every inch of the connector, including the threads and any small openings.
After cleaning, rinse the connector and the area with a clean water supply to remove any remaining cleaner. Use a rag to wipe away the water and ensure that the connector is completely dry. Pay close attention to the threads and small openings, as these areas can accumulate dirt and debris over time.
With the connector and the surrounding area now clean, it's time for inspection. Use the magnifying glass or flashlight to carefully examine the connector for any signs of damage. Look for cracks, corrosion, or any other abnormalities that may have been caused by the break. Inspect the threads and ensure they are not stripped or damaged. Also, check for any small holes or openings that may have been created during the break, as these could be sources of further issues.
If you notice any additional damage during the inspection, it's important to address it before proceeding with the repair. Take notes of any issues and consider consulting a professional mechanic for guidance on how to proceed. Thorough cleaning and inspection are essential to ensure that the repair is effective and long-lasting.
Unclogging the Fuel Line: A Step-by-Step Guide to Removing Seized Lines
You may want to see also
Install New Connector: Attach a new connector, ensuring proper alignment and secure it with the recommended torque
When dealing with a broken fuel line connector, replacing it is often the most effective solution. Here's a step-by-step guide to help you install a new connector:
Step 1: Prepare the Necessary Tools and Materials
Before you begin, ensure you have the right tools and parts. You'll need a new fuel line connector that matches your vehicle's specifications, along with a fuel line (if the old one is also being replaced). Additionally, have a torque wrench ready to apply the correct amount of force during installation.
Step 2: Locate the Fuel Line Connector
Identify the fuel line connector that needs to be replaced. This connector is typically located near the fuel tank or along the fuel lines, where they connect to the engine. Carefully inspect the old connector to understand its design and any unique features.
Step 3: Remove the Old Connector
Carefully detach the old fuel line connector from the fuel line. Take note of how it is secured and any clips or fasteners that hold it in place. Gently pull the connector away from the fuel line, being mindful of any potential damage to the fuel line itself.
Step 4: Attach the New Connector
Now, carefully align the new fuel line connector with the fuel line. Ensure that it is positioned correctly, matching the old connector's orientation. Use your fingers or a small tool to gently push the connector onto the fuel line until it is fully seated.
Step 5: Secure with Recommended Torque
This step is crucial to ensure a proper connection. Using the torque wrench, apply the manufacturer's recommended torque value to the connector's mounting fasteners or clips. This step ensures that the connector is securely attached and will not loosen over time. Make sure to follow the torque specifications provided by the vehicle's manual or the connector's manufacturer.
Step 6: Test and Inspect
After securing the new connector, start the engine and check for any leaks. Ensure that the fuel line is functioning correctly and that there are no signs of fuel leakage around the new connector. If everything is in order, you've successfully repaired the broken fuel line connector.
Unveiling the Mystery: The Essential Metal Tool for Fuel Line Disconnects
You may want to see also
Frequently asked questions
Repairing a damaged fuel line connector can be a straightforward process. First, ensure you have the necessary tools, including a fuel line repair kit, which typically includes a new connector and sealing compound. Start by disconnecting the fuel line from the engine and the fuel tank. Carefully cut away any damaged sections of the fuel line and prepare the ends for the new connector. Slide the new connector over the fuel line, ensuring it fits snugly, and use the sealing compound to create a secure, leak-free connection. Finally, reattach the fuel line to the engine and fuel tank, and test the system to ensure there are no leaks.
In some cases, you might be able to repair a fuel line connector without a full replacement. If the connector is only slightly damaged, you can try cleaning it with a solvent to remove any debris or corrosion. Ensure the connector is dry before reassembling. You can also use a fuel line repair kit to seal small punctures or tears in the connector. However, if the damage is extensive or the connector is severely corroded, it's best to replace it to ensure a reliable connection.
Fuel line connectors can break due to several factors. Age and prolonged exposure to fuel can cause corrosion and deterioration. Physical damage, such as being run over by a vehicle or impacted by debris, can also lead to cracks or breaks. Additionally, improper installation or poor-quality connectors can result in premature failure. Regular maintenance and inspections can help identify potential issues before they cause significant problems.