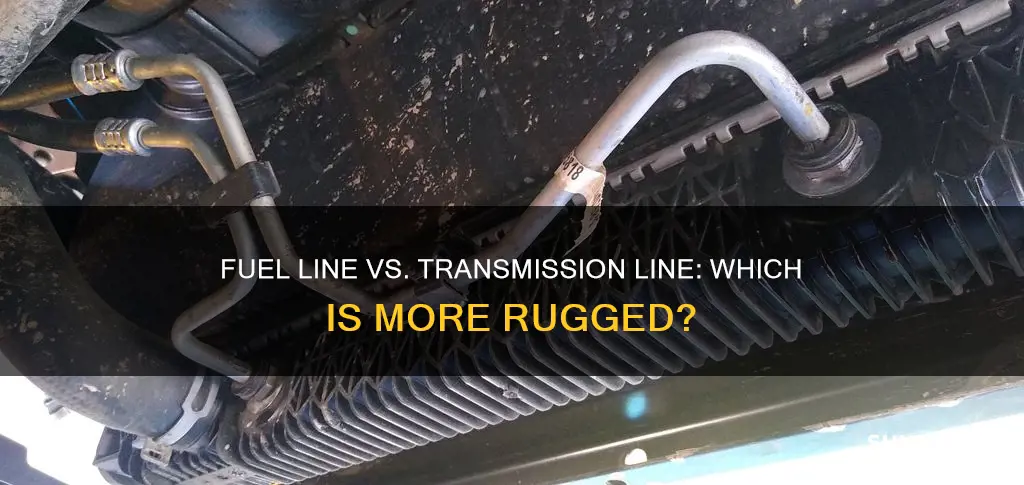
When it comes to the durability and longevity of a vehicle's components, the fuel line and transmission line are often compared. While both play crucial roles in the engine's performance, the question arises: which one is tougher? This comparison delves into the characteristics and challenges of these essential vehicle parts, examining their respective strengths and weaknesses to determine which one emerges as the more resilient in various driving conditions.
Characteristics | Values |
---|---|
Material | Fuel lines are typically made of rubber or plastic, while transmission lines are made of metal (usually steel or aluminum). |
Thickness | Transmission lines are generally thicker and more robust due to the high-pressure nature of the fluid they carry. |
Flexibility | Fuel lines are more flexible and can bend easily, whereas transmission lines are stiffer and less flexible. |
Durability | Transmission lines are designed to withstand high temperatures and pressures, making them more durable in harsh conditions. |
Resistance | Transmission lines offer better resistance to corrosion and wear due to their metal construction. |
Cost | Fuel lines are usually cheaper than transmission lines due to their simpler design and lower material costs. |
Maintenance | Transmission lines may require more frequent maintenance and inspections due to their critical role in the drivetrain. |
Compatibility | The choice between fuel and transmission lines depends on the specific vehicle and its requirements. |
What You'll Learn
- Material Comparison: Steel vs Aluminum in Fuel and Transmission Lines
- Flexibility: Which Line is More Flexible for Vibration Resistance
- Pressure Tolerance: Can Transmission Lines Handle Higher Pressures
- Corrosion Resistance: Impact of Fuel vs Transmission Line Materials
- Durability in Extreme Conditions: Cold vs Hot Environments
Material Comparison: Steel vs Aluminum in Fuel and Transmission Lines
The choice of material for fuel and transmission lines is a critical consideration in vehicle engineering, impacting performance, durability, and safety. When comparing steel and aluminum, two prominent materials in this context, it's essential to understand their unique characteristics and how they fare in these specific applications.
Steel:
Steel has been a traditional and widely used material for fuel and transmission lines due to its inherent strength and durability. It offers excellent resistance to pressure and corrosion, making it ideal for withstanding the demanding conditions within a vehicle's fuel and transmission systems. The high tensile strength of steel ensures that these lines can handle the forces exerted by the engine and transmission without compromising structural integrity. Additionally, steel's inherent rigidity provides a stable path for fuel and transmission fluids, reducing the likelihood of leaks or contamination.
Aluminum:
Aluminum, on the other hand, presents a lighter and more corrosion-resistant alternative. Its lower density compared to steel makes it an attractive option for weight-sensitive applications, such as high-performance vehicles or aircraft. Aluminum's natural corrosion resistance is particularly beneficial in fuel lines, as it helps prevent rust and degradation over time. This material's ability to maintain fluidity at lower temperatures is advantageous for fuel lines, ensuring a consistent flow even in cold climates.
Comparison and Considerations:
The choice between steel and aluminum depends on the specific requirements of the vehicle and its intended use. Steel's superior strength and durability make it a reliable option for heavy-duty applications, where structural integrity is paramount. It is commonly used in high-pressure fuel lines and transmission systems that demand robust materials. However, aluminum's lightweight nature and corrosion resistance offer advantages in certain scenarios. For instance, in racing or aviation, where weight reduction is critical, aluminum fuel lines can provide improved performance and handling.
In summary, both materials have their merits and are chosen based on the specific needs of the vehicle. Steel's strength and durability make it a go-to material for traditional fuel and transmission lines, ensuring long-lasting performance. Meanwhile, aluminum's lightweight and corrosion-resistant properties make it an attractive choice for modern vehicles, especially in applications where weight reduction is essential without compromising on corrosion resistance.
Optimal Fuel Line Size for 5-Horse Tecumseh Engine
You may want to see also
Flexibility: Which Line is More Flexible for Vibration Resistance?
The debate over which automotive component is more flexible and thus better suited for withstanding vibrations—the fuel line or the transmission line—is an interesting one, especially for those who want to optimize their vehicle's performance and longevity. Both components play crucial roles in the vehicle's operation, and their flexibility can significantly impact their ability to handle the rigors of the road.
The fuel line is responsible for transporting gasoline from the fuel tank to the engine, ensuring a steady supply of fuel for combustion. It is typically made of flexible materials like rubber or a composite material to accommodate the engine's movement and the vehicle's vibrations. The flexibility of the fuel line is essential to prevent kinks and ensure a consistent fuel flow, which can be particularly important during high-performance driving or when navigating rough terrain.
On the other hand, the transmission line, also known as the transmission fluid line, carries transmission fluid between the transmission and the engine. This line is crucial for the proper functioning of the transmission, as it ensures the fluid is at the right temperature and pressure to lubricate and cool the transmission components. Transmission lines are often made of more rigid materials to withstand the high-pressure environment and the intense forces within the transmission.
When comparing the flexibility of these two lines, it is generally true that the fuel line is designed to be more pliable. This is because the fuel line's primary function is to maintain a flexible connection, allowing it to move with the engine and the vehicle's structure. The transmission line, while also flexible, is typically more rigid to handle the higher pressures and forces within the transmission system.
However, the flexibility of a line is just one aspect to consider. The material composition, diameter, and overall design of the line also play significant roles in vibration resistance. For instance, a fuel line made of a high-quality, flexible rubber compound might offer superior flexibility and vibration dampening compared to a transmission line made of a less flexible material. Additionally, the diameter of the lines can affect their flexibility; thinner lines might be more flexible but could also be more susceptible to damage from sharp edges or vibrations.
In conclusion, while the fuel line is generally more flexible, the choice between the two lines depends on the specific application and the vehicle's design. Understanding the unique requirements of each component is essential for making an informed decision when it comes to choosing the right materials and designs for optimal performance and longevity.
Troubleshooting Tips: Fixing Your Tohatsu 6HP Fuel Line Issues
You may want to see also
Pressure Tolerance: Can Transmission Lines Handle Higher Pressures?
Transmission lines, an essential component in electrical systems, are designed to transmit power efficiently over various distances. One critical aspect of their performance is pressure tolerance, which directly impacts their ability to handle higher pressures without compromising functionality. This feature is particularly crucial in applications where power transmission lines are exposed to varying environmental conditions and loads.
The pressure tolerance of transmission lines is primarily determined by the materials used in their construction. These lines are typically made of conductive materials such as aluminum or copper, which are chosen for their excellent electrical conductivity and durability. The insulation surrounding the conductor is another critical factor, as it must withstand the pressure and environmental factors without degrading. Insulation materials like polyethylene or cross-linked polyethylene (XLPE) are commonly used for their excellent pressure resistance and ability to maintain electrical integrity.
In high-pressure environments, transmission lines must be designed to handle the increased stress without failing. This involves careful selection of materials and construction techniques. For instance, the insulation layer may be thicker to provide better protection against pressure-induced damage. Additionally, the conductor's cross-sectional area might be larger to accommodate the higher current flow without excessive heating, which could lead to pressure buildup.
The pressure tolerance of transmission lines is also influenced by the system's design and installation. Proper grounding techniques and the use of surge protection devices can help manage pressure spikes caused by lightning strikes or other transient events. Regular maintenance and inspections are essential to identify and rectify any issues that may compromise the line's pressure tolerance, ensuring the system's reliability and safety.
In summary, transmission lines' pressure tolerance is a critical consideration in their design and application. By selecting appropriate materials, employing effective construction methods, and implementing protective measures, engineers can ensure that these lines can handle higher pressures, thereby maintaining the efficiency and reliability of power transmission systems. Understanding and addressing pressure tolerance is vital for the long-term performance and safety of electrical infrastructure.
Mastering Quick Connect Fuel Lines: A Comprehensive Guide
You may want to see also
Corrosion Resistance: Impact of Fuel vs Transmission Line Materials
The durability and longevity of fuel and transmission lines in vehicles are significantly influenced by the materials used in their construction, particularly in terms of corrosion resistance. Corrosion, a natural process where materials degrade due to chemical reactions with their environment, can lead to various issues, including reduced performance, increased maintenance needs, and even system failures. When comparing fuel lines and transmission lines, understanding the corrosion resistance of their respective materials is crucial for ensuring optimal vehicle performance and reliability.
Fuel lines, typically made from materials like rubber, vinyl, or synthetic compounds, are exposed to a variety of corrosive elements. These include fuel itself, which can contain impurities and volatile compounds, as well as environmental factors such as heat, sunlight, and moisture. Rubber, for instance, is susceptible to degradation when exposed to fuel, leading to cracking, brittleness, and eventual failure. Over time, this can result in fuel leaks, reduced engine performance, and potential safety hazards.
In contrast, transmission lines, often constructed from materials like steel or aluminum, may offer better inherent corrosion resistance. Steel, for example, forms a protective oxide layer on its surface when exposed to air, which helps prevent further corrosion. However, the presence of transmission fluid, which can be corrosive, and the high-stress environment within the transmission system, can still lead to material degradation over time. Aluminum, while lighter and more resistant to corrosion than steel, may not be as durable in certain transmission line applications due to its lower strength.
The choice of materials for fuel and transmission lines is a critical consideration in vehicle design. Engineers must balance the need for corrosion resistance with other factors such as flexibility, cost, and compatibility with the vehicle's operating environment. For fuel lines, materials like synthetic rubber compounds or fluoropolymers are often preferred for their superior resistance to fuel degradation. In transmission lines, the use of stainless steel or specialized coatings can enhance corrosion resistance, ensuring the lines can withstand the harsh conditions within the transmission system.
In summary, the materials used in fuel and transmission lines play a pivotal role in their corrosion resistance and, consequently, their overall durability. While fuel lines often rely on specialized rubber compounds or fluoropolymers to resist fuel-related corrosion, transmission lines may benefit from materials like stainless steel or aluminum, which offer inherent corrosion protection. Understanding these material properties is essential for vehicle manufacturers and enthusiasts to ensure the longevity and reliability of their vehicles' critical fluid transfer systems.
Mastering Chainsaw Maintenance: The Ultimate Guide to Using a Fuel Line Tool
You may want to see also
Durability in Extreme Conditions: Cold vs Hot Environments
The debate of which is tougher, the fuel line or the transmission line, often sparks curiosity, especially when considering the extreme conditions they endure. Both play critical roles in vehicle performance, but their durability in cold and hot environments varies significantly.
In cold climates, the fuel line takes center stage. Fuel lines are typically made of materials like rubber or plastic, which can become brittle and crack when exposed to freezing temperatures. This is a critical issue as it can lead to fuel leaks, engine misfires, and even complete engine failure. The fuel line's primary function is to transport fuel from the tank to the engine, and in extreme cold, this task becomes more challenging. The material's reduced flexibility and increased brittleness make it more susceptible to damage from temperature fluctuations.
On the other hand, transmission lines, often made of metal or reinforced rubber, are designed to withstand a wide range of temperatures. These lines are crucial for transmitting power from the engine to the wheels, and their durability is essential for maintaining vehicle performance. In cold conditions, transmission lines may experience some stiffness, but their robust construction and ability to handle temperature changes make them more resilient.
When it comes to hot environments, the transmission line takes the lead in terms of durability. High temperatures can cause fuel lines to expand and become more susceptible to damage, especially if they are not made of heat-resistant materials. Transmission lines, however, are engineered to handle the heat. They are often made of materials that can withstand extreme temperatures without compromising their structural integrity. This is vital for maintaining the vehicle's performance and preventing damage to the transmission system.
In summary, while both fuel and transmission lines are essential components, their toughness in extreme conditions differs. Fuel lines are more vulnerable in cold environments due to their material properties, while transmission lines excel in hot conditions, thanks to their heat-resistant construction. Understanding these differences is crucial for vehicle owners and mechanics to ensure optimal performance and longevity in various climates.
Fuel Return Line Size for 1998 Honda Civic
You may want to see also
Frequently asked questions
A fuel line is a type of hose used to transport fuel from the tank to the engine, while a transmission line is a component in a vehicle's transmission system that carries fluid to and from the transmission.
Both the fuel line and the transmission line are essential for the vehicle's operation. However, the transmission line is generally considered more critical as it directly impacts the vehicle's ability to shift gears and maintain proper fluid flow, which is crucial for smooth and efficient transmission operation.
Signs of a failing fuel line may include fuel leaks, reduced engine performance, or engine stalling. For the transmission line, look out for transmission slippage, harsh or delayed gear changes, and unusual noises from the transmission. Regular maintenance and inspections can help identify issues early on.