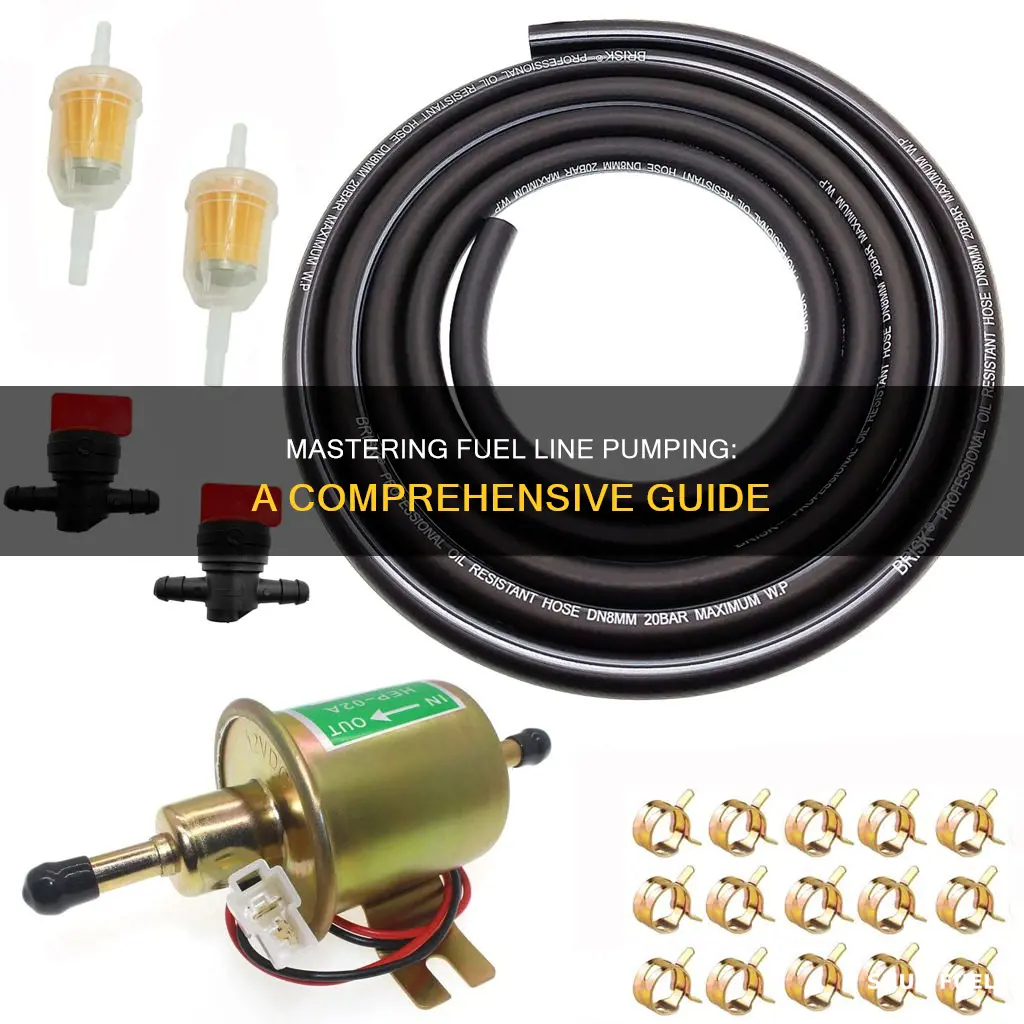
Understanding how to pump fuel lines is essential for anyone working on vehicles or machinery that relies on fuel systems. This guide will provide a step-by-step process for safely and effectively pumping fuel lines, ensuring optimal performance and longevity of the fuel system. From preparing the necessary tools and safety equipment to identifying the correct fuel type and applying proper pumping techniques, this comprehensive overview will empower you to handle fuel line pumping with confidence and precision.
What You'll Learn
- Fuel Line Inspection: Check for damage, leaks, and proper connections
- Pressure Testing: Ensure fuel pump delivers adequate pressure
- Filter Replacement: Clean or replace filters to prevent contamination
- Pump Maintenance: Regularly clean and lubricate pump components
- Safety Procedures: Follow guidelines for handling fuel and using tools
Fuel Line Inspection: Check for damage, leaks, and proper connections
Fuel lines are critical components of your vehicle's fuel system, and regular inspections are essential to ensure optimal performance and prevent potential issues. Here's a step-by-step guide on how to inspect your fuel lines for damage, leaks, and proper connections:
- Visual Inspection: Start by visually examining the fuel lines for any visible signs of damage. Look for cracks, punctures, or any unusual wear and tear. Check the lines for any bends or kinks that might have occurred due to vehicle movement or previous repairs. Pay close attention to the areas where the lines connect to the fuel tank, pump, and injectors. Even small tears or cuts can lead to fuel leaks, so any damage should be addressed immediately.
- Leaks Detection: Fuel line inspections also involve checking for leaks. Start the engine and listen for any hissing or bubbling sounds, which could indicate a fuel leak. You can also use a fuel line inspection kit, which typically includes a spray bottle filled with a dye or a special liquid that will show up as a stain if there's a leak. Spray the dye around the fuel lines and observe if any color appears on the ground or nearby surfaces, indicating a potential leak.
- Connection Integrity: Proper connections are vital to prevent fuel leaks and ensure efficient fuel delivery. Inspect all fuel line connections for tightness and security. Ensure that all fittings and clamps are securely in place and haven't become loose over time. Tighten any loose connections carefully, but be cautious not to overtighten, as this can also cause damage. If you encounter any damaged or corroded connections, replace them with new parts to maintain a reliable fuel supply.
- Route and Support: Examine the fuel lines' routing for any obstructions or damage. Ensure they are not pinched, crushed, or rubbing against any sharp edges or moving parts. The lines should be securely supported and not hanging loosely, as this can lead to damage over time. Consider the vehicle's manual or consult a professional to understand the optimal routing and support methods for your specific make and model.
- Regular Maintenance: Fuel line inspections should be part of your regular vehicle maintenance routine. It's recommended to inspect the fuel lines at least once a year or whenever you notice any changes in engine performance or fuel efficiency. Regular checks can help identify issues early on, allowing for prompt repairs or replacements, thus ensuring your vehicle's fuel system operates efficiently and safely.
Marine Fuel Line Length: Optimal Sizing for Efficiency
You may want to see also
Pressure Testing: Ensure fuel pump delivers adequate pressure
Pressure testing is a critical step in ensuring that your fuel pump system is functioning correctly and delivering the required pressure to your engine. This process involves measuring the pressure at various points in the fuel line to verify that it meets the specifications for your vehicle. Here's a step-by-step guide on how to perform this test:
Preparation: Before you begin, ensure you have the necessary tools and equipment, including a fuel pressure gauge, a fuel pump, and a fuel line. Familiarize yourself with the vehicle's fuel system diagram to locate the correct pressure points. It is recommended to work on the vehicle in a well-ventilated area and wear protective gear to handle fuel safely.
Step 1: Locate the Fuel Pump and Lines: Start by identifying the fuel pump, which is typically located near the engine. Follow the fuel lines from the pump to the engine, noting their positions and any connections or filters along the way.
Step 2: Disconnect and Isolate: Carefully disconnect the fuel lines at the pump and the engine. Ensure you have a clear understanding of the fuel flow direction to reconnect the lines correctly later. Isolate the fuel lines by placing a temporary block or using a clamp to prevent fuel from flowing back into the system.
Step 3: Set Up the Gauge: Attach the fuel pressure gauge to the fuel line at the pump's output. Ensure a secure connection to get accurate readings. Turn on the fuel pump to prime the system and allow it to run for a few seconds to ensure it's operational.
Step 4: Measure Pressure: With the pump running, take the pressure reading. The ideal pressure can vary depending on the vehicle's make and model, so consult the vehicle's manual for the specified range. Record the pressure value. If the pressure is below the recommended range, you may need to adjust the pump's settings or check for any blockages in the lines.
Step 5: Reconnect and Test Engine Operation: Carefully reconnect the fuel lines to the engine and pump. Start the engine and allow it to idle. Monitor the fuel pressure gauge while the engine is running. If the pressure remains adequate, you've successfully passed the pressure test. If the pressure drops or fluctuates, further investigation is required.
Troubleshooting: If the pressure test reveals issues, check for any clogs or restrictions in the fuel lines. Inspect the pump for any signs of damage or wear. Ensure that the fuel filter is clean and functional. Adjusting the pump's settings or replacing components may be necessary to achieve the required pressure.
Remember, proper pressure in the fuel system is essential for optimal engine performance and longevity. This testing process ensures that your fuel pump is delivering the necessary pressure to power your vehicle efficiently.
Understanding Fuel Line Drainage: A Comprehensive Guide
You may want to see also
Filter Replacement: Clean or replace filters to prevent contamination
When it comes to maintaining your fuel system, one of the most critical tasks is ensuring that the filters are clean and free of contaminants. Over time, these filters can become clogged with dirt, debris, and other impurities, which can lead to a variety of issues. Here's a step-by-step guide on how to properly clean or replace filters to keep your fuel lines in optimal condition.
Identifying the Filters: Before you begin, it's essential to know where the filters are located. Fuel lines typically have filters in strategic positions to catch contaminants before they reach the engine. These filters can be found near the fuel tank, in the fuel pump module, or even within the engine bay. Consult your vehicle's manual or online resources to locate the specific filters relevant to your make and model.
Cleaning the Filters: In some cases, you might be able to clean the filters instead of replacing them. This process involves removing the filters and using a suitable cleaning agent to eliminate any built-up contaminants. Start by disconnecting the fuel lines from the filters and placing them in a clean container filled with the recommended cleaning solution. Allow the filters to soak for the specified duration, then rinse and dry them thoroughly. After cleaning, reinstall the filters, ensuring they are securely in place.
Replacing the Filters: If the filters are heavily contaminated or show signs of wear, replacement is necessary. Start by draining any remaining fuel from the system to avoid spills. Locate the old filters and carefully remove them, being mindful of any fuel residue. Take the filters to a professional or a well-equipped workshop for proper disposal. Then, install the new filters, ensuring they are the correct size and type for your vehicle. Tighten the mounting screws securely but avoid over-tightening.
Regular Maintenance: Preventive maintenance is key to avoiding fuel system issues. Establish a regular filter replacement schedule based on your vehicle's manufacturer recommendations or mileage. By doing so, you can ensure that contaminants are consistently caught, preventing them from reaching the engine and causing potential damage.
Remember, proper fuel system maintenance is crucial for optimal engine performance and longevity. By regularly cleaning or replacing filters, you can keep your fuel lines free from contamination, ensuring a smooth and efficient driving experience.
2007 Honda Accent Fuel Line Location: Under the Hood
You may want to see also
Pump Maintenance: Regularly clean and lubricate pump components
Pump maintenance is a critical aspect of ensuring the longevity and efficient operation of fuel pumps. Regular cleaning and lubrication of pump components are essential practices that can prevent issues and maintain optimal performance. Here's a detailed guide on how to approach this maintenance task:
Cleaning the Pump Components: Start by disassembling the pump to access its various parts. This process may vary depending on the pump model, but generally, you'll need to remove any accessible components that can be cleaned separately. Use a suitable cleaning agent or solvent recommended for the specific pump type. Common cleaning methods include using a degreaser to remove built-up fuel residue and contaminants. Pay close attention to the pump's internal passages, filters, and nozzles, as these areas are prone to accumulating debris and fuel-related contaminants. Thoroughly clean these parts to ensure the pump's overall health.
After cleaning, it's crucial to inspect the components for any signs of wear and tear. Look for cracks, corrosion, or any damage that might have occurred during the cleaning process. Replace any worn-out parts to maintain the pump's integrity. Rinse the cleaned components with clean water to remove any residual cleaning agents and ensure they are free from debris.
Lubrication Techniques: Lubrication plays a vital role in reducing friction and wear between moving parts. Apply a suitable lubricant to the pump's internal mechanisms, focusing on the pump rod, piston, and any rotating parts. Common lubricants used for fuel pumps include silicone-based or synthetic lubricants. Ensure an even coating to prevent dry spots, which can lead to increased friction and potential damage.
When lubricating, consider the pump's operating temperature and the type of fuel it handles. Different fuels and environmental conditions may require specific lubricants. For instance, ethanol-blended fuels might necessitate a different lubrication approach. Always refer to the pump manufacturer's guidelines for the most appropriate lubrication methods and products.
Reassembly and Testing: Once cleaning and lubrication are complete, carefully reassemble the pump components, ensuring they are aligned correctly. Reattach the pump to the fuel line and secure all connections. Start the pump and check for any leaks or unusual noises. Test the pump's performance by running it under various load conditions to ensure it operates smoothly and efficiently.
Regular maintenance, including cleaning and lubrication, will help identify potential issues early on, preventing costly repairs or replacements. It is a simple yet effective practice that contributes to the overall reliability of fuel pump systems.
Stainless Fuel Line Install: 95 Integra Guide
You may want to see also
Safety Procedures: Follow guidelines for handling fuel and using tools
When working with fuel lines, it is crucial to prioritize safety to prevent accidents and ensure the well-being of both yourself and those around you. Here are some essential safety procedures to follow:
Personal Protective Equipment (PPE): Always wear appropriate PPE when handling fuel. This includes safety goggles to protect your eyes from potential splashes or spills, and gloves to safeguard your hands. Opt for heat-resistant gloves if you anticipate working with hot fuel lines or near heat sources. Additionally, consider wearing a respirator mask to avoid inhaling fumes, especially in enclosed spaces.
Fuel Handling: Exercise extreme caution when handling fuel. Always use approved containers and ensure they are tightly sealed to prevent leaks. Avoid using damaged or cracked containers, as they may not be able to withstand the pressure. When transferring fuel, do so slowly and carefully, minimizing any potential for spillage. Keep fuel containers away from open flames or heat sources to prevent ignition. It is advisable to work in a well-ventilated area to reduce the risk of inhaling fumes.
Tool Safety: Familiarize yourself with the proper use of tools related to fuel line work. This includes fuel pumps, hoses, and any specialized equipment. Ensure that tools are in good working condition and free from defects. Before using any tool, inspect it for any signs of damage or wear. Always follow the manufacturer's guidelines for tool operation and maintenance. Keep tools organized and stored safely to prevent accidents or injuries.
Ventilation and Ventilation: Adequate ventilation is crucial when working with fuel. Ensure that the work area has proper ventilation to disperse fumes and prevent the buildup of hazardous gases. If working in a confined space, use a fume hood or ventilation system to maintain a safe air quality. Regularly monitor the area for any signs of fuel leaks or gas accumulation, and take appropriate action if detected.
Emergency Preparedness: Be prepared for emergencies by having a well-stocked first-aid kit and knowing the location of fire extinguishers or other emergency equipment. In the event of a fuel spill or leak, follow established procedures for containment and cleanup. Keep a fire extinguisher nearby, specifically rated for fuel or flammable liquid fires. Ensure that all personnel are trained in emergency response protocols.
Remember, safety should always be the top priority when working with fuel lines. By following these guidelines and staying vigilant, you can minimize risks and create a safer work environment.
Perfect Fuel Line Size for Harley-Davidson Crossover: Expert Guide
You may want to see also
Frequently asked questions
Pumping a fuel line is a process used to transfer fuel from a storage tank to an engine. It ensures a steady supply of fuel for combustion, allowing the engine to run efficiently and smoothly.
If you notice any of the following signs, it might be time to pump your fuel line: engine stalling or hesitation during acceleration, reduced fuel efficiency, or a strong fuel odor in the cabin. Regular maintenance checks can also help identify potential issues.
You will typically need a fuel pump, a fuel filter, a fuel pressure gauge, and a suitable container to collect the old fuel. It's also essential to have the necessary safety gear, such as gloves and eye protection, to handle the fuel and any potential spills.
While it is possible to pump a fuel line yourself, especially for routine maintenance, it is recommended to have some experience or seek professional assistance. Fuel lines can be complex, and improper handling may lead to fuel leaks or engine damage.
Absolutely! Always ensure the engine is turned off and the vehicle is in a secure location before starting the pumping process. Wear protective gear, work in a well-ventilated area, and be cautious of potential fuel spills. It's also a good idea to have a spill kit nearby in case of any accidents.