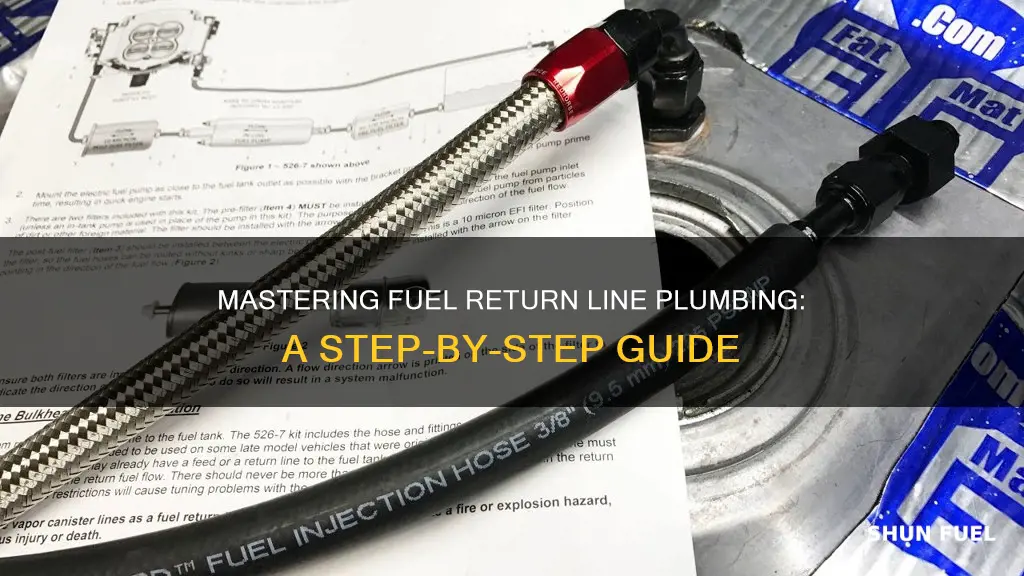
Plumbing a fuel return line is a crucial step in ensuring the efficient and safe operation of a vehicle's fuel system. This process involves connecting a secondary fuel line that returns excess fuel from the engine back to the fuel tank, preventing wastage and maintaining optimal fuel levels. By following a systematic approach, you can ensure a successful installation, ensuring the vehicle's engine receives the right amount of fuel at all times. This guide will provide a step-by-step process to help you understand the process and ensure a professional finish.
What You'll Learn
- Prepare Materials: Gather necessary tools and materials like fuel return line, fittings, and connectors
- Layout and Routing: Plan the optimal path for the line, considering accessibility and clearance
- Connect to Fuel Tank: Securely attach the line to the fuel tank using appropriate fittings
- Test for Leaks: Inspect connections and perform pressure tests to ensure no leaks
- Secure and Hide: Route the line, fasten it, and conceal it to prevent damage and maintain aesthetics
Prepare Materials: Gather necessary tools and materials like fuel return line, fittings, and connectors
When preparing to plumb a fuel return line, it's crucial to gather all the necessary tools and materials beforehand to ensure a smooth and efficient process. Here's a detailed guide on what you should collect:
Fuel Return Line: This is the primary component of your plumbing project. It's a specific type of hose or tube designed to carry fuel from the tank back to the engine. Ensure you get the correct size and length to fit your vehicle's specifications. Measure the distance between the fuel tank and the engine to determine the required length.
Fittings and Connectors: You'll need various fittings and connectors to join the fuel return line to the existing fuel system. Common fittings include elbows, tees, and unions, which allow for directional changes and connections. Look for high-quality fittings that are compatible with the fuel return line material. Additionally, get the appropriate connectors, such as quick-connect fittings or threaded adapters, to ensure a secure and leak-free connection.
Tools: Having the right tools is essential for a successful installation. Gather basic plumbing tools like wrenches, pliers, and a fuel filter removal tool. These tools will help you tighten connections, adjust fittings, and remove any existing fuel filters. It's also a good idea to have a fuel pump primer or a similar device to prime the fuel system and ensure proper fuel flow.
Safety Gear: Safety should always be a priority. Wear protective gloves and safety goggles to shield your hands and eyes from potential fuel spills or splashes. Consider wearing old clothing, as fuel can be messy, and you might need to work in tight spaces.
Additional Materials: Depending on your vehicle's setup, you might need extra materials. For instance, if your car has a complex fuel system with multiple lines, you may require additional hoses or seals to ensure a proper fit. Always refer to your vehicle's manual or consult a professional to identify any specific requirements.
By gathering these materials and tools in advance, you'll be well-prepared to tackle the plumbing of your fuel return line efficiently and effectively. Remember, proper preparation is key to a successful DIY project.
Optimizing Performance: Choosing the Right Fuel Line for Your 6HP Tohatsu 4-Stroke Engine
You may want to see also
Layout and Routing: Plan the optimal path for the line, considering accessibility and clearance
When planning the layout and routing of a fuel return line, it's crucial to prioritize accessibility and clearance to ensure a safe and efficient installation. Here's a detailed guide on how to approach this step:
- Assess the Vehicle's Structure: Begin by thoroughly examining the vehicle's architecture. Identify the areas where the fuel return line needs to be routed, considering the engine bay's layout, existing hoses, and any potential obstacles. Look for easily accessible spots where the line can be run without causing interference with other components.
- Determine the Optimal Path: Map out the desired route for the fuel return line on a diagram or directly on the vehicle. Aim for a path that is as straight and direct as possible, minimizing unnecessary bends and twists. This approach reduces the risk of kinking and ensures a smooth flow of fuel. Consider the following:
- Start at the fuel tank, identifying the lowest point to ensure gravity-assisted fuel return.
- Route the line towards the engine, keeping it as close to the ground as feasible to avoid tripping hazards.
- Avoid tight spaces and sharp corners where the line might get pinched or damaged.
- If the vehicle has a firewall or other structural elements, plan the route around these obstacles, ensuring the line remains clear and accessible.
Consider Clearance and Accessibility:
- Clearance: Ensure the line has sufficient clearance from the ground, especially in areas prone to vibration or movement. This prevents damage from road debris or suspension travel.
- Accessibility: Choose routes that allow for easy access during maintenance and repairs. Avoid areas where the line might be difficult to reach, especially if regular maintenance is required.
- Clamping and Fastening: Plan where the line will be clamped or fastened to the vehicle's frame or other components. Ensure these points are easily accessible for proper securing and adjustment.
- Use Appropriate Materials: Select fuel-compatible materials for the line and fittings to ensure longevity and performance. Consider using flexible hoses with adequate wall thickness to withstand fuel pressure and temperature variations.
- Document and Verify: Once the layout is finalized, create a detailed diagram or sketch, including all relevant measurements and connections. This documentation will be essential for the next steps and future reference. Verify the plan with a physical inspection to ensure it aligns with the vehicle's structure and meets the accessibility and clearance requirements.
Mercury Outboard Fuel Line Removal: A Step-by-Step Guide
You may want to see also
Connect to Fuel Tank: Securely attach the line to the fuel tank using appropriate fittings
When connecting the fuel return line to the fuel tank, it's crucial to ensure a secure and reliable attachment. Here's a step-by-step guide to achieve this:
Start by identifying the appropriate fittings for your specific fuel tank and line. Common fittings used for fuel lines include quick-connect couplings, compression fittings, or barbed fittings. Quick-connect couplings are convenient for a temporary setup, while compression and barbed fittings offer more permanent solutions. Choose fittings that match the diameter of your fuel return line to ensure a proper seal.
Locate the fuel tank's return port, which is typically a dedicated opening designed for the fuel return line. This port is usually positioned to allow gravity-fed fuel flow back into the tank. Carefully insert the fittings onto the fuel return line, ensuring they are aligned with the tank's port. Apply the appropriate torque to the fittings using a wrench to secure them in place. Tighten the fittings firmly, but be cautious not to overtighten, as it may damage the fuel tank or line.
Consider using sealing compounds or tape around the fittings to enhance the connection's integrity. This extra layer of protection can prevent fuel leaks and ensure a tight seal. Additionally, inspect the fittings for any signs of damage or deformation after tightening. If any issues are found, carefully remove the fittings and re-tighten them, ensuring a secure connection.
Remember, proper alignment and torque application are critical to a successful connection. Take your time to ensure the fittings are secure and well-fitted to the fuel tank. This attention to detail will contribute to the overall reliability of your fuel system.
Tygon Fuel Line: Top Sources for Purchase
You may want to see also
Test for Leaks: Inspect connections and perform pressure tests to ensure no leaks
When plumbing a fuel return line, ensuring that all connections are secure and leak-free is crucial to prevent fuel leaks and potential safety hazards. Here's a detailed guide on how to test for leaks and ensure the integrity of your fuel return line:
Visual Inspection: Begin by visually examining all connections and joints. Look for any signs of fuel leakage, such as wet spots, stains, or fuel residue around the fittings. Even a small amount of fuel can indicate a potential leak. Pay close attention to the threads of the fittings; if there are any visible damage or wear, it could compromise the seal. Check for any signs of corrosion or damage to the fuel line itself, as this can also lead to leaks over time.
Connection Tightness: Ensure that all connections are tight and secure. Loosen the fittings slightly and then retighten them by hand. You should feel a resistance when tightening, indicating a good connection. Use a wrench or pliers to ensure a firm grip, but be careful not to overtighten, as this can damage the fittings. Double-check that all connections are snug, especially at bends and elbows, where fuel lines may be more susceptible to movement.
Pressure Testing: Perform a pressure test to verify the integrity of the fuel return line. This is a critical step to identify any hidden leaks that might not be visible during a visual inspection. Use a pressure gauge and connect it to the fuel line, ensuring it is securely attached. Gradually increase the pressure and monitor for any drops or fluctuations. A stable pressure reading indicates a secure connection. If a leak is present, you will notice a rapid drop in pressure or hear hissing sounds. Remember to release the pressure slowly and safely after the test.
Bubble Test: Another effective method is the bubble test, especially useful for identifying leaks in the fuel line itself. Soak the fuel line in a container of water and observe if any bubbles appear. Bubbles indicate the presence of fuel in the water, signifying a leak. This test is particularly helpful for detecting small, internal leaks that might not be visible during a visual inspection.
Professional Assistance: If you're unsure or uncomfortable with the process, consider seeking professional help. Plumbers or automotive specialists can provide expert guidance and ensure that your fuel return line is installed correctly and safely. They have access to specialized tools and can perform comprehensive leak tests to give you peace of mind.
By following these steps, you can effectively test for leaks and ensure that your fuel return line is properly plumbed, minimizing the risk of fuel-related issues. Remember, proper installation and regular maintenance are essential for vehicle performance and safety.
Ford Ranger Flex Fuel Gas Line Disconnect: A Step-by-Step Guide
You may want to see also
Secure and Hide: Route the line, fasten it, and conceal it to prevent damage and maintain aesthetics
When plumbing a fuel return line, ensuring it is secure and well-hidden is crucial for both functionality and aesthetics. Here's a step-by-step guide to achieving this:
Routing the Line: Begin by carefully planning the path of the fuel return line. This line typically connects the fuel tank to the engine, so it should be routed in a way that avoids sharp bends and potential damage. Consider the vehicle's structure and choose a route that minimizes interference with other components. Aim for a straight path or one with gentle curves to ensure smooth fuel flow.
Using Suitable Hose and Clamps: Select a fuel-resistant hose that can withstand the pressure and temperature variations associated with fuel. Ensure the hose diameter matches the required specifications. Secure the hose using appropriate clamps at regular intervals to prevent slippage and potential leaks. Clamps should be tightened securely but carefully to avoid damaging the hose or surrounding components.
Fastening Techniques: To secure the line, utilize appropriate fasteners such as metal brackets or plastic clips, depending on the vehicle's design. Fasten the line to the frame or other sturdy structures to prevent movement and potential damage during operation. Ensure that the fasteners are tightened securely but carefully to avoid stripping the threads or causing damage to the fuel line.
Concealing for Aesthetics and Protection: Once the line is routed and fastened, conceal it to maintain a clean and professional appearance. Use heat-resistant insulation or protective sleeves to cover the line, especially in areas prone to vibration or impact. This not only enhances aesthetics but also provides an extra layer of protection against potential damage. Consider using factory-style covers or custom-made solutions to seamlessly blend the fuel line into the vehicle's interior or exterior.
Final Checks: After completing the plumbing, double-check all connections and fasteners to ensure they are tight and secure. Verify that the fuel return line is functioning correctly by testing the fuel system under various conditions. Regularly inspect the line for any signs of wear, damage, or leaks, especially in areas where it is exposed or accessible.
By following these steps, you can ensure that the fuel return line is securely installed, well-protected, and aesthetically pleasing, contributing to the overall reliability and appearance of the vehicle.
Braided Fuel Line: A Viable Substitute for Oil Lines?
You may want to see also
Frequently asked questions
A fuel return line is a crucial component in fuel systems, especially in vehicles with fuel injection. It is a pipe that returns unused fuel from the injectors back to the fuel tank or reservoir. Proper plumbing of this line ensures efficient fuel management, prevents fuel accumulation in the injectors, and maintains optimal engine performance.
The size of the fuel return line should match the capacity of the fuel system and the engine's requirements. It is typically measured in inches (e.g., 3/8", 1/2") or millimeters. Routing the line correctly involves considering the distance from the injectors to the tank, avoiding sharp bends, and ensuring it is protected from heat sources. Consult the vehicle's manual or seek professional advice for specific guidelines.
While a regular fuel line might seem like a suitable replacement, it is not recommended for a fuel return line. Return lines require specific material properties to handle the unique challenges of returning fuel, including potential contaminants. Using a regular fuel line may lead to performance issues, fuel leaks, or engine problems. It's best to use a dedicated fuel return line designed for this purpose.