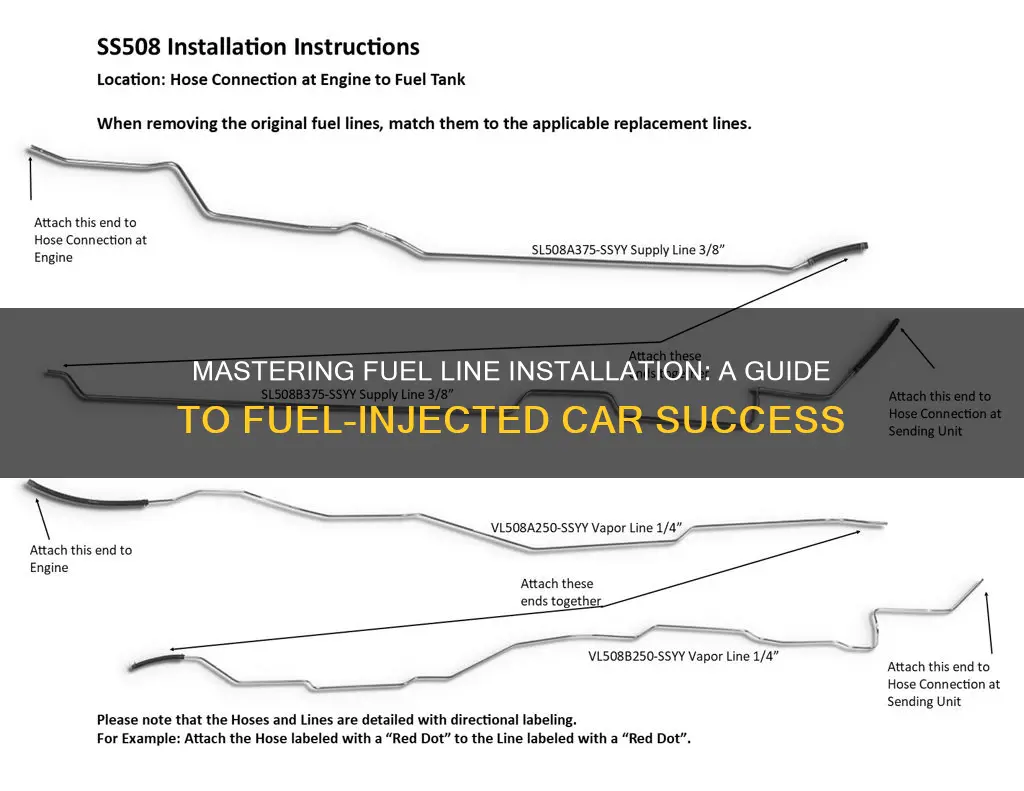
Hooking up fuel lines in a fuel-injected car can seem daunting, but with the right tools and a systematic approach, it's a manageable task. This guide will walk you through the process, ensuring you understand the importance of proper connections and the potential risks of incorrect assembly. We'll cover the necessary tools, safety precautions, and step-by-step instructions to help you successfully connect the fuel lines, ensuring your vehicle runs smoothly and efficiently.
What You'll Learn
- Preparation: Gather tools, ensure fuel tank empty, and locate fuel lines
- Fuel Line Inspection: Check for damage, ensure correct size, and verify compatibility
- Clamps and Fittings: Use proper clamps, tighten securely, and avoid cross-threading
- Routing and Support: Route lines away from heat sources and secure with ties
- Testing and Safety: Verify fuel flow, check for leaks, and ensure proper grounding
Preparation: Gather tools, ensure fuel tank empty, and locate fuel lines
Before you begin the process of connecting fuel lines to your fuel-injected car, it's crucial to prepare and gather the necessary tools to ensure a smooth and safe installation. Here's a step-by-step guide to the preparation phase:
Gather the Tools: Start by assembling all the required tools and equipment. You will need a fuel pump primer bulb, which is essential for priming the fuel lines and ensuring a steady fuel flow. Additionally, get a fuel filter and a set of fuel line connectors that match your car's specifications. It's also advisable to have a fuel pressure gauge to monitor the system's performance. Other useful tools include a wrench or socket set for tightening connections and a clean rag or cloth for wiping away any fuel residue.
Empty the Fuel Tank: This step is critical for your safety and the success of the project. Ensure that the fuel tank is completely empty to avoid any potential hazards. You can do this by either running the car until the fuel light comes on or using a fuel pump primer bulb to drain the tank. It's important to follow the manufacturer's guidelines for your specific vehicle to ensure you drain the tank correctly.
Locate the Fuel Lines: Familiarize yourself with the vehicle's fuel system layout. Locate the fuel tank, which is typically located beneath the car or in the trunk. Identify the fuel lines that run from the tank to the engine. These lines are usually made of rubber or plastic and are color-coded for easy identification. Note their positions and any attachments or fittings they have. Understanding the layout will make the installation process much easier and help you avoid any potential damage during the setup.
By following these preparation steps, you'll be well-equipped to begin the fuel line installation process, ensuring a successful and safe connection to your fuel-injected car's system. Remember, taking the time to prepare is essential for a smooth and efficient project.
Mastering the Art: A Step-by-Step Guide to Removing Fuel Line Connectors from Nylon Hoses
You may want to see also
Fuel Line Inspection: Check for damage, ensure correct size, and verify compatibility
When dealing with fuel lines on a fuel-injected car, a thorough inspection is crucial to ensure optimal performance and safety. Here's a step-by-step guide to inspecting and connecting fuel lines:
Damage Assessment: Begin by visually examining the fuel lines for any signs of damage. Look for cracks, cuts, or punctures along the length of the lines. Inspect the fittings and connectors as well; ensure they are intact and securely attached. Over time, fuel lines can deteriorate due to heat, vibration, or chemical exposure, so it's essential to check for any signs of wear and tear. If you notice any damage, it's best to replace the affected fuel line to prevent potential leaks or system failures.
Size Verification: Fuel lines come in various sizes, and using the correct size is critical. Measure the fuel line's inside diameter using a micrometer or caliper. Compare this measurement to the specifications provided by the vehicle manufacturer. Using a line that is too small can restrict fuel flow, while a larger line might not fit properly, leading to potential leaks. Ensure that all connections are made with the correct size to maintain optimal performance.
Compatibility Check: Compatibility is key to a successful fuel line installation. Check the fuel line's compatibility with the vehicle's fuel system, including the fuel pump, injectors, and tank. Incompatible lines might not function properly or could even cause damage to the engine's fuel system. Refer to the vehicle's manual or consult a professional to confirm the compatibility of the fuel line with your specific car model.
Secure Installation: When connecting the fuel lines, ensure a tight and secure fit. Use the appropriate tools to tighten fittings and connectors, but be careful not to overtighten, as this can damage the lines. Make sure all connections are leak-free by applying a small amount of fuel line sealant to the threads of the fittings. Properly secured connections will prevent fuel leaks and ensure a reliable fuel supply to the engine.
Remember, fuel lines are a critical component of your vehicle's fuel system, and proper inspection and installation are essential for safe and efficient operation. Always refer to the manufacturer's guidelines and, if in doubt, consult a qualified mechanic to ensure the job is done correctly.
Can Rubber Fuel Lines Withstand High Temperatures?
You may want to see also
Clamps and Fittings: Use proper clamps, tighten securely, and avoid cross-threading
When working on fuel lines of a fuel-injected car, it's crucial to use the right clamps and fittings to ensure a secure and reliable connection. The first step is to identify the appropriate clamp for your specific fuel line. Different fuel lines may require different types of clamps, such as metal, rubber, or plastic, depending on the material of the line and the application. Always refer to the vehicle's manual or the manufacturer's guidelines to determine the correct clamp type. Once you have the right clamp, ensure it is the proper size to fit the fuel line snugly. A well-fitted clamp will prevent leaks and ensure the line remains secure during operation.
Tightening the clamp is a critical step in the installation process. Use a wrench or a specialized fuel line tool to tighten the clamp securely. Over-tightening should be avoided as it can damage the fuel line or cause it to crack. The goal is to achieve a firm, yet gentle grip without applying excessive force. Check the manufacturer's recommendations for the correct torque value to ensure a proper seal. It's essential to tighten the clamp evenly to avoid creating a bulge or distortion in the fuel line.
Cross-threading, a common mistake, can lead to leaks and potential engine damage. When tightening the clamp, ensure that the threads are aligned properly and that you are turning the clamp in the correct direction. Always follow a clockwise direction when tightening to avoid cross-threading. If you encounter resistance while tightening, it may indicate that the clamp is already secure, and further tightening could damage the fuel line. Take your time and apply steady pressure to achieve the desired tightness.
In addition to clamps, various fittings, such as unions, elbows, and tees, may be required for complex fuel line routing. These fittings should also be tightened securely, following the same principles as the clamp installation. Ensure that all fittings are properly sealed and that there are no gaps or spaces that could allow fuel to leak. Regularly inspect these connections, especially in high-pressure areas, to maintain optimal performance and safety.
Remember, proper installation and maintenance of fuel lines are vital for the efficient operation of your fuel-injected vehicle. By using the correct clamps and fittings, tightening them securely, and avoiding cross-threading, you can ensure a reliable fuel supply to your engine, promoting optimal performance and longevity. Always take your time and double-check your work to guarantee a safe and successful fuel line installation.
Mastering the AC Fuel Line Disconnect: A Comprehensive Guide
You may want to see also
Routing and Support: Route lines away from heat sources and secure with ties
When working on a fuel-injected car, proper routing and support of fuel lines are crucial to ensure optimal performance and prevent potential issues. Here's a detailed guide on how to approach this task:
Routing Fuel Lines:
- Begin by referring to your vehicle's manual or a reliable online resource specific to your car model. This will provide you with detailed diagrams and recommendations for fuel line placement. The goal is to route the lines away from potential heat sources, such as the engine block, exhaust system, and transmission.
- Identify the fuel tank, fuel pump, and injectors' locations. Fuel lines should be routed from the tank, passing near the rear of the engine compartment, and then leading to the fuel pump and injectors. Keep the lines as straight and direct as possible to minimize the risk of damage or restriction.
- Avoid routing fuel lines near hot engine components. The heat can cause the fuel to degrade and potentially lead to fuel leaks or performance issues. If you must route lines close to heat sources, use protective sleeves or insulation to safeguard the lines.
Securing the Lines:
- Once the routing is complete, secure the fuel lines using appropriate ties or clips. This step is essential to prevent the lines from becoming tangled or damaged during vehicle operation.
- Use rubber or plastic ties that are designed for fuel line applications. These ties should be tight enough to hold the lines in place but not so tight that they cause any strain or damage. Secure the ties at regular intervals to ensure the lines remain taut and free-flowing.
- Avoid securing the lines too tightly, as this can restrict fuel flow and cause pressure buildup. Allow for some flexibility in the routing to accommodate engine movement and vibrations.
- Consider using metal clips or brackets if the lines are particularly long or exposed. These provide additional support and can be especially useful for lines running along the frame or near the ground.
Remember, proper routing and support are vital to maintaining the integrity of your fuel system. By following these steps, you can ensure that your fuel lines are secure, well-protected, and functioning optimally, contributing to the overall performance and reliability of your fuel-injected vehicle.
Rust Removal: Effective Methods for Fuel Line Restoration
You may want to see also
Testing and Safety: Verify fuel flow, check for leaks, and ensure proper grounding
Before you even think about connecting the fuel lines, it's crucial to understand the importance of testing and safety in this process. Fuel systems are inherently dangerous due to the volatile nature of gasoline. Any mistake during installation can lead to fuel leaks, which can cause fires or explosions. Therefore, thorough testing and safety measures are essential.
Verifying Fuel Flow:
Start by ensuring that the fuel pump is functioning correctly. You can do this by temporarily disconnecting the fuel lines and using a fuel pressure gauge to check the pressure. If the pump isn't working, you'll need to address the issue before proceeding. Once the pump is confirmed to be operational, reconnect the fuel lines and start the engine. Monitor the fuel flow by checking for any unusual noises or vibrations. The engine should start smoothly, and you should feel the characteristic 'whoosh' of fuel entering the engine. If the engine doesn't start or the fuel flow seems inconsistent, there might be an issue with the fuel lines or the pump.
Checking for Leaks:
After the engine is running, it's time to inspect for any fuel leaks. Turn off the engine and carefully examine all connections, including the fuel lines, fittings, and the fuel pump. Look for any signs of fuel seeping or dripping. You can use a soapy water solution to make this process easier. If you notice any leaks, tighten the connections or replace the affected parts. Ensure that all fuel lines are properly secured and that there are no kinks or bends that could cause a restriction.
Ensuring Proper Grounding:
Grounding is often overlooked but is critical for the safe operation of your fuel-injected engine. A proper ground ensures that any static electricity built up in the fuel system is safely discharged, preventing sparks that could ignite fuel vapor. Check the engine block and the fuel tank for grounding points. Ensure that the fuel lines are connected to these grounding points and that the connections are clean and tight. You can use a multimeter to test the continuity of the ground path. If the grounding is insufficient, you might experience engine misfires or even a no-start condition.
Remember, safety should always be your top priority when working on fuel systems. Take your time, follow the manufacturer's guidelines, and don't hesitate to seek professional help if you're unsure about any step. Proper testing and safety measures will ensure that your fuel-injected car runs smoothly and reliably.
Fuel Line Disconnect Tool: A Transmission Line Companion?
You may want to see also
Frequently asked questions
Before you begin, ensure you have the correct fuel lines and fittings for your specific car model. Inspect the lines for any damage or bends, and if necessary, straighten them carefully. It's crucial to prime the fuel system to remove air bubbles. Prime the fuel lines by attaching one end to the fuel pump and the other to a fuel pressure gauge (if you have one) or a temporary fitting. Prime the pump to create pressure and allow the fuel to flow through the lines, ensuring there are no leaks.
When connecting the fuel lines to the injectors, start with the high-pressure line, which is typically the larger diameter line. Locate the fuel injector and identify the high-pressure port, usually marked with a specific color or a small arrow. Insert the high-pressure line into the port, ensuring a snug fit. Tighten the fitting securely but be careful not to overtighten, as it may damage the injector. For the low-pressure line, it usually connects to a smaller port on the injector. Attach the line and tighten the fitting, again being mindful of the torque specifications for your car.
Yes, using the right tools is essential for a proper connection. You'll need fuel line connectors or fittings that match your car's specifications. Use a fuel line crimping tool to secure the fittings onto the lines, following the manufacturer's instructions for the correct torque settings. It's important to torque the connections properly to ensure a tight seal. Additionally, consider using fuel line tape or protective sleeves over the connections to prevent leaks and ensure a clean appearance. Always refer to your vehicle's manual for specific torque values and connection procedures.