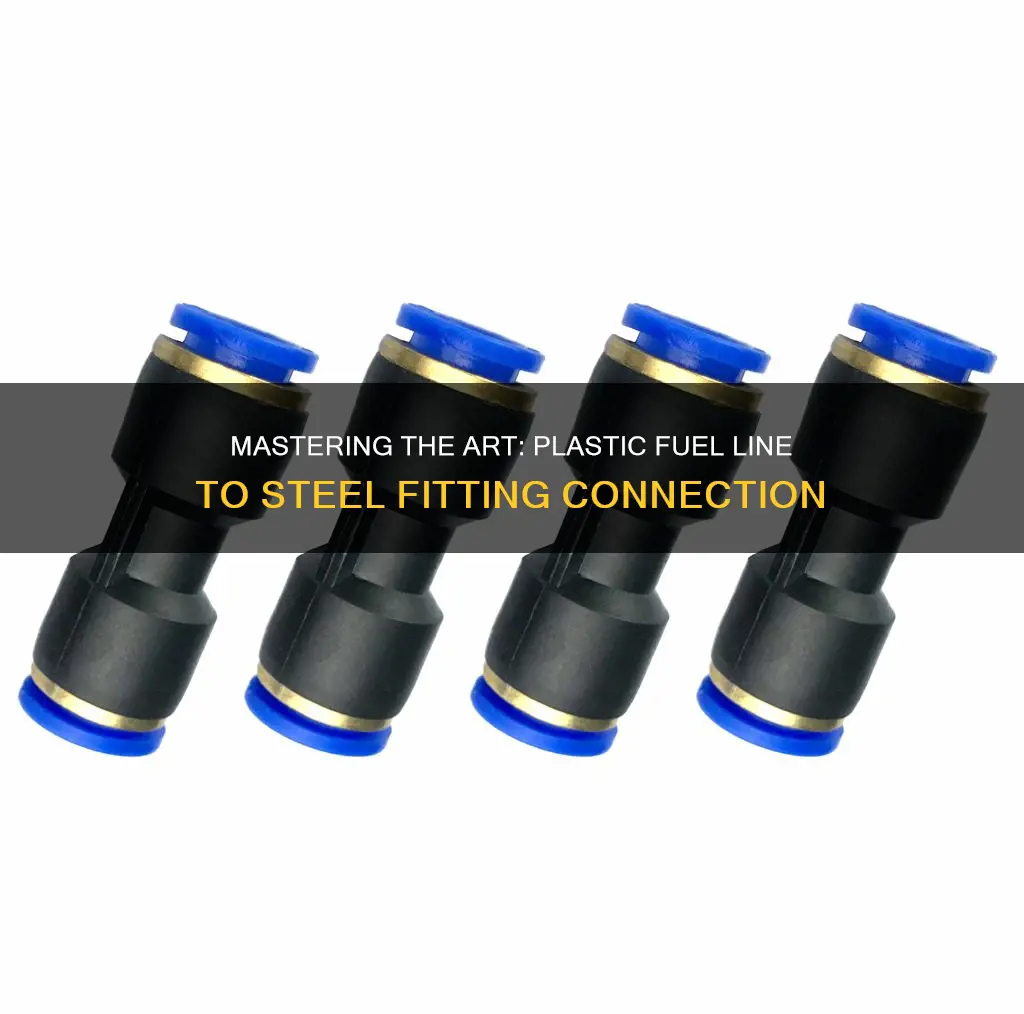
Connecting a plastic fuel line to a steel fitting requires careful consideration to ensure a secure and leak-free connection. This process involves several steps to accommodate the different materials and ensure compatibility. By following the proper techniques and using the right tools, you can effectively join these components, maintaining the integrity of your fuel system. Understanding the specific requirements and using appropriate materials will help create a reliable and durable connection.
What You'll Learn
- Prepare Materials: Ensure you have the right tools and materials, including fuel line, fittings, and connectors
- Clean Surfaces: Use a degreaser to remove dirt and contaminants from both the fuel line and fitting
- Cut and Prepare: Measure and cut the fuel line to the correct length, then deburr the ends
- Connect with Adhesive: Apply a suitable fuel-resistant adhesive to the fuel line and fitting, then connect
- Test and Secure: Check for leaks, tighten connections, and ensure a secure, leak-free bond
Prepare Materials: Ensure you have the right tools and materials, including fuel line, fittings, and connectors
Before you begin the process of connecting a plastic fuel line to a steel fitting, it's crucial to gather all the necessary tools and materials. This preparation will ensure a smooth and successful installation. Here's a comprehensive guide on what you need:
Fuel Line and Fittings: Start by acquiring the appropriate length of plastic fuel line that matches the diameter of your existing fuel line. Measure the length required to connect the old line to the new fitting. Additionally, obtain the specific steel fittings designed for this purpose. Common types include compression fittings, which use a ferrule to create a tight seal, and quick-connect fittings, which offer a convenient and secure attachment. Ensure that the fittings are compatible with both the fuel line material and the fuel type you are using.
Connectors and Adapters: Depending on your specific setup, you might need various connectors and adapters. For instance, if you're dealing with different fuel line diameters, you'll require adapters to ensure a proper fit. Quick-connect adapters can be useful if you're transitioning from a quick-connect fitting to a compression fitting or vice versa. These adapters provide a seamless transition, allowing you to use the same fitting for different fuel line sizes.
Tools: Having the right tools is essential for a successful connection. You'll need a fuel line cutter or a sharp knife to precisely cut the fuel line to the desired length. A pair of pliers or a fuel line crimping tool will be necessary for securing the fittings. Additionally, consider using a fuel line solvent or adhesive to ensure a strong bond between the fuel line and fittings, especially if you're working with plastic fuel lines.
Safety Gear: Safety should always be a priority. Wear gloves to protect your hands and ensure a clean connection. Safety goggles are essential to shield your eyes from any potential fuel splashes or debris. It's also a good practice to work in a well-ventilated area or outdoors to avoid inhaling any fuel fumes.
By gathering these materials and tools, you'll be well-prepared to tackle the task of connecting a plastic fuel line to a steel fitting. This organized approach will make the process more efficient and less prone to errors.
Fuel Return Line Repair: A Guide for Jaguar XJ6 Sovereign Owners
You may want to see also
Clean Surfaces: Use a degreaser to remove dirt and contaminants from both the fuel line and fitting
Before attempting to connect a plastic fuel line to a steel fitting, it is crucial to ensure that the surfaces are clean and free from any contaminants. This step is often overlooked but is essential for a secure and reliable connection. Start by gathering the necessary tools and materials, including a degreaser or a suitable cleaning agent, a wire brush or scrubber, and possibly a small wire brush or a similar tool for reaching tight spaces.
The first step in the cleaning process is to identify the surfaces that need attention. For this scenario, you will need to clean both the plastic fuel line and the steel fitting. Begin by examining the fuel line; look for any visible dirt, grease, or debris that might have accumulated during storage or previous use. Use the wire brush or scrubber to gently remove these contaminants, ensuring that you reach all the nooks and crannies. Pay extra attention to any bends or kinks in the fuel line, as these areas might trap dirt and grime.
Now, turn your focus to the steel fitting. Steel surfaces can often become coated with a layer of oxidation or rust, especially if they have been exposed to the elements. Use the degreaser or cleaning agent to remove any built-up contaminants. Apply the degreaser generously to the fitting, allowing it to sit for a few minutes to loosen the dirt. Then, use the wire brush to scrub the area, ensuring that you remove any residue and achieve a clean, smooth surface.
When cleaning the fuel line, be cautious not to damage the plastic material. Some degreasers or cleaning agents might be too harsh and could potentially weaken the fuel line over time. Opt for a mild degreaser or a specialized plastic cleaner if available. Rinse the fuel line thoroughly after cleaning to remove any remaining cleaning agents. For the steel fitting, ensure that all contaminants are removed to create a strong bonding surface for the fuel line.
After cleaning both components, allow them to dry completely. This step is often overlooked but is vital to ensure a proper connection. Moisture or residual cleaning agents can interfere with the bonding process. Once dry, you are ready to proceed with the connection, ensuring a secure and leak-free join. Remember, taking the time to clean the surfaces thoroughly will result in a more durable and reliable fuel line connection.
Choosing the Right Fuel Line: Size Matters!
You may want to see also
Cut and Prepare: Measure and cut the fuel line to the correct length, then deburr the ends
When connecting a plastic fuel line to a steel fitting, proper preparation is crucial to ensure a secure and leak-free connection. Here's a step-by-step guide to the 'Cut and Prepare' process:
Measuring and Cutting the Fuel Line: Begin by carefully measuring the fuel line to determine the desired length. It's essential to have a precise measurement to avoid any excess material that could lead to unnecessary connections or potential leaks. Use a sharp utility knife or a dedicated fuel line cutter to make a clean cut. Ensure that the cut is straight and smooth to facilitate a proper connection later.
Deburring the Ends: After cutting the fuel line, the ends need to be prepared to ensure a tight seal. Deburring involves removing any sharp edges or burrs that could potentially damage the fitting or cause a leak. You can use a small file or a deburring tool specifically designed for fuel lines. Carefully file the ends, moving the tool in a circular motion to create a smooth, rounded surface. This step is crucial to prevent any damage to the fitting and to ensure a reliable connection.
The preparation process is a critical phase in the installation, as it sets the foundation for a successful connection. By taking the time to measure accurately and deburr the ends, you'll ensure that the fuel line is ready for a secure attachment to the steel fitting, minimizing the risk of leaks and ensuring optimal performance.
Fixing a Flooded Fuel Line: A Step-by-Step Guide
You may want to see also
Connect with Adhesive: Apply a suitable fuel-resistant adhesive to the fuel line and fitting, then connect
When connecting a plastic fuel line to a steel fitting, using an adhesive can provide a secure and reliable bond, ensuring the system's integrity and performance. Here's a step-by-step guide on how to achieve this:
Step 1: Prepare the Materials
Start by gathering the necessary materials. You will need a high-quality fuel-resistant adhesive specifically designed for fuel line installations. Ensure you have the correct type of adhesive for the materials you are working with. Additionally, gather clean rags or cloth to wipe away any dirt or debris from the fuel line and fitting surfaces.
Step 2: Clean the Surfaces
Before applying the adhesive, it is crucial to ensure a clean and dry surface. Use the cloth to wipe away any dirt, grease, or old adhesive residue from both the plastic fuel line and the steel fitting. This step is essential to promote better adhesion. Make sure the surfaces are free from any contaminants that might interfere with the bonding process.
Step 3: Apply the Adhesive
Take a small amount of the fuel-resistant adhesive and apply it to the fuel line and the corresponding section of the steel fitting. Ensure an even and generous coating, covering the entire interface. The adhesive should be applied in a way that it forms a continuous layer without any gaps or overlaps, as this can affect the bond strength. Allow the adhesive to sit for a few moments to become tacky, which will facilitate a stronger bond.
Step 4: Connect the Components
Now, carefully connect the plastic fuel line to the steel fitting. Ensure that the line is properly aligned with the fitting, making a secure connection. Apply firm pressure to the joined area, holding it together for the recommended curing time specified by the adhesive manufacturer. This step is crucial to ensure the adhesive sets properly and creates a robust bond.
Step 5: Test and Inspect
After the adhesive has cured, test the connection by applying pressure and checking for any leaks. Inspect the joint to ensure there are no visible gaps or imperfections. If everything looks secure, your fuel line is now successfully connected to the steel fitting using an adhesive method. This technique provides a reliable and long-lasting bond, especially in fuel systems where flexibility and resistance to fuel chemicals are essential.
Small Block Engine Fuel Line Sizing: A Comprehensive Guide
You may want to see also
Test and Secure: Check for leaks, tighten connections, and ensure a secure, leak-free bond
When connecting a plastic fuel line to a steel fitting, it's crucial to follow a meticulous process to ensure a secure and leak-free bond. This process involves several key steps that, when executed properly, will guarantee a reliable and safe connection.
Firstly, you should always start by cleaning the surfaces of both the plastic fuel line and the steel fitting. Any dirt, grease, or debris can interfere with the bonding process, so a clean surface is essential. Use a mild detergent and water to clean the areas where the connection will be made. Ensure that the surfaces are completely dry before proceeding.
Next, apply a suitable primer or adhesive to the steel fitting. This step is often overlooked but is critical for creating a strong bond. The primer will help the adhesive adhere better to the steel surface, providing a more secure connection. Allow the primer to dry according to the manufacturer's instructions.
Now, it's time to connect the plastic fuel line. Ensure that the line is cut at a 45-degree angle using a sharp, clean knife or a specialized fuel line cutter. This angle allows for a better seal when the line is inserted into the fitting. Insert the fuel line into the fitting, pushing it firmly until it is fully seated. Tighten the fitting using a wrench, but be careful not to overtighten, as this can damage the fuel line.
The final step is to test for leaks. This is a critical part of the process, as even a small leak can lead to serious issues over time. Use a soapy water solution and apply it to the connection. If there are any leaks, they will be visible as bubbles. If no bubbles appear, the connection is secure. However, if there are any leaks, you may need to re-tighten the fitting or re-cut the fuel line and try again.
By following these steps, you can ensure that your plastic fuel line is securely connected to a steel fitting, providing a reliable and safe fuel supply system. It's important to take the time to do this right, as a poorly connected fuel line can lead to costly and dangerous repairs.
Bundy Fuel Line Connector: A Comprehensive Guide
You may want to see also
Frequently asked questions
When connecting plastic fuel lines to steel fittings, it's crucial to use the right tools and materials to ensure a tight and leak-free seal. Start by cleaning both the fuel line and the fitting to remove any dirt or debris. Then, use a fuel line adapter or a ferrule specifically designed for the material of your fuel line. Apply a small amount of fuel line cement or adhesive to the adapter or ferrule, and insert it onto the fuel line, ensuring it is flush with the end. Finally, use a fuel line crimping tool to create a secure crimp around the fitting, following the manufacturer's instructions for the correct size and pressure.
One common challenge is the potential for leaks due to the different expansion coefficients of plastic and steel. To prevent this, always use a high-quality fuel line cement or adhesive that is compatible with both materials. Ensure the fuel line is properly lubricated and that the fitting is clean and free of any debris. Avoid over-tightening the connection, as this can cause damage to the fuel line. Additionally, consider using a flexible fuel line that is designed to accommodate temperature changes, which can help reduce the risk of leaks.
Yes, using a fuel line crimping tool is essential for a secure connection. This tool applies the correct amount of pressure to the fitting, ensuring a tight seal. It's important to follow the manufacturer's guidelines for the specific tool and size of the fitting. Additionally, consider using a fuel line inspection mirror to visualize the connection and ensure it is free of any defects. Regularly checking and maintaining the connection is also recommended, especially in high-vibration environments, to identify and address any potential issues early on.