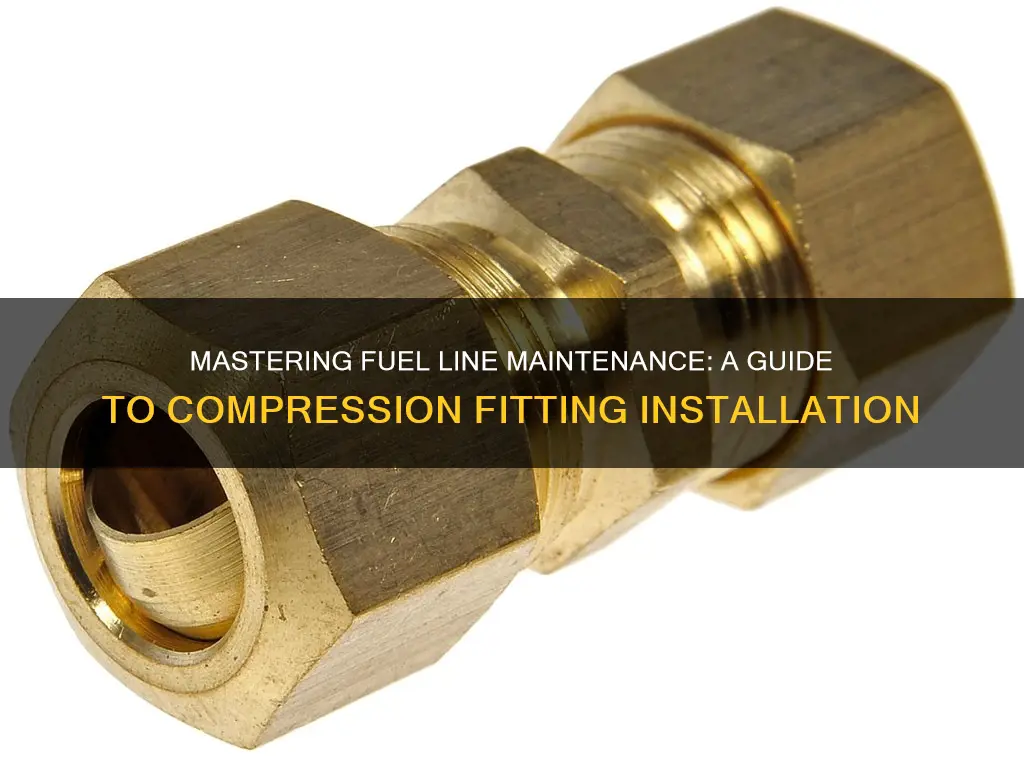
Installing a compression fitting on a fuel line is a crucial step in ensuring the safe and efficient operation of your vehicle's fuel system. This process involves securely attaching a fitting to the fuel line to allow for the proper routing and connection of fuel components. By following a few simple steps, you can ensure a tight and reliable seal, preventing fuel leaks and potential engine issues. This guide will provide a step-by-step process to help you master the art of installing compression fittings on fuel lines, ensuring your vehicle's fuel system is in top condition.
What You'll Learn
- Prepare the Tools: Gather necessary tools like fuel line cutter, compression fitting, and pipe dope
- Clean the Line: Ensure the fuel line is clean and free of debris for a secure connection
- Cut the Line: Use a fuel line cutter to make a precise cut, leaving enough length for the fitting
- Prepare the Fitting: Inspect the compression fitting for damage and ensure it fits the fuel line size
- Install the Fitting: Slide the fitting onto the fuel line, apply pipe dope, and tighten securely
Prepare the Tools: Gather necessary tools like fuel line cutter, compression fitting, and pipe dope
Before you begin the installation process, it's crucial to gather the right tools to ensure a successful and secure connection. Here's a step-by-step guide on preparing the necessary tools:
Fuel Line Cutter: Start by acquiring a fuel line cutter, a specialized tool designed to cut fuel lines with precision. This tool will allow you to make clean and accurate cuts, ensuring a proper fit for the compression fitting. Look for a cutter that can handle the specific diameter of your fuel line to ensure a tight seal.
Compression Fitting: The compression fitting is the core component of your repair. It is designed to create a secure and leak-free connection between the fuel line and the engine or other components. Choose a fitting that matches the diameter of your fuel line and is compatible with the material used. Ensure you select the correct size to accommodate the fuel line effectively.
Pipe Dope (Fuel Line Dope): Pipe dope, also known as fuel line dope, is a lubricating compound specifically formulated for fuel line installations. It plays a vital role in ensuring a tight seal and preventing leaks. Apply a small amount of pipe dope to the inside of the compression fitting and the fuel line, ensuring an even coating. This step is essential as it facilitates the easy insertion of the fuel line into the fitting and promotes a secure connection.
Additionally, consider having a pair of pliers or a fuel line crimper to assist with the installation process. These tools will help you secure the fitting and ensure a tight connection. By gathering these tools beforehand, you'll be well-prepared to tackle the installation, ensuring a professional and reliable fuel line connection.
Aluminum Tubing for Fuel Lines: A Comprehensive Guide
You may want to see also
Clean the Line: Ensure the fuel line is clean and free of debris for a secure connection
To ensure a secure and reliable connection when installing a compression fitting on a fuel line, it is crucial to start with a clean and debris-free fuel line. This step is often overlooked but is essential for the longevity and safety of your fuel system. Here's a detailed guide on how to achieve this:
Step 1: Identify the Fuel Line: Begin by locating the fuel line that you intend to work on. It is typically a rubber or plastic hose that carries fuel from the tank to the engine. Ensure you have access to the entire length of the fuel line, as you'll need to clean it thoroughly.
Step 2: Remove Obstructions: Before cleaning, identify and remove any obstructions or attachments along the fuel line. This includes any screws, clips, or brackets that might have been used to secure the line in place. Carefully detach these fasteners and set them aside, ensuring they are not lost.
Step 3: Clean the Exterior: Start by cleaning the exterior of the fuel line. Use a mild detergent or soap mixed with water to create a soapy solution. Gently scrub the fuel line with a soft-bristled brush or a clean cloth, ensuring you remove any dirt, grime, or old fuel residue. Rinse the line thoroughly with clean water to eliminate any soap residue.
Step 4: Inspect for Debris: After cleaning, inspect the fuel line closely. Look for any signs of debris, such as dirt, rust, or old fuel deposits, that might have accumulated inside the line. If you notice any debris, use a small brush or a compressed air bulb to gently remove it. Ensure that the entire interior of the fuel line is clean and free of any foreign matter.
Step 5: Dry the Line: Once you've completed the cleaning process, allow the fuel line to air dry completely. You can speed up the drying process by using a hairdryer on a low setting, ensuring it doesn't get too close to the line to avoid heat damage. A dry fuel line is essential to prevent any moisture-related issues during the installation process.
By following these steps, you'll ensure that the fuel line is clean and ready for the compression fitting installation. This process guarantees a secure connection and helps prevent potential issues like fuel leaks or reduced performance due to contaminants. Remember, taking the time to clean the fuel line is a critical aspect of successful fuel system maintenance.
Fuel Evap Line Removal: LS1 Engine Guide
You may want to see also
Cut the Line: Use a fuel line cutter to make a precise cut, leaving enough length for the fitting
When it comes to installing a compression fitting on a fuel line, precision is key. You'll need to ensure that the cut is clean and accurate to avoid any potential leaks or damage to the fuel line. One of the most effective tools for this task is a fuel line cutter, which allows you to make a precise cut without the risk of damaging the fuel line.
To begin, locate the section of the fuel line where you want to install the compression fitting. It's important to choose a spot that is easily accessible and allows for a secure connection. Once you've identified the location, use the fuel line cutter to make a clean, straight cut. The cutter should be designed specifically for fuel lines, ensuring a precise and clean cut. Take your time and apply steady pressure to the cutter to avoid any uneven cuts.
The goal is to leave enough length of the fuel line exposed so that the compression fitting can be securely attached. A good rule of thumb is to leave about 1-2 inches of the fuel line on either side of the fitting. This extra length will provide a buffer and make the installation process easier. Remember, a precise cut will make the entire installation process smoother and reduce the chances of any fuel line damage.
After making the cut, inspect the exposed fuel line to ensure it is free of any debris or contaminants. If necessary, use a cloth or paper towel to wipe away any dirt or grime. This step is crucial to ensure a tight and secure connection with the compression fitting.
By using a fuel line cutter, you can achieve a precise cut, ensuring that the installation process is efficient and effective. This method minimizes the risk of errors and potential fuel leaks, making it an essential technique for any DIY mechanic or automotive enthusiast. Always prioritize precision when working with fuel lines to ensure the safety and reliability of your vehicle's fuel system.
Craftsman Push Mower Fuel Line Sizes: A Comprehensive Guide
You may want to see also
Prepare the Fitting: Inspect the compression fitting for damage and ensure it fits the fuel line size
When preparing to install a compression fitting on a fuel line, it's crucial to inspect the fitting carefully for any signs of damage or wear. Compression fittings are designed to securely seal fuel lines, and any defects or imperfections can compromise the integrity of the connection. Start by examining the fitting for any visible cracks, chips, or deformities. These issues could indicate that the fitting has been damaged during storage or transportation, and using it could lead to fuel leaks or other problems. Check the threads of the fitting as well; ensure they are smooth and free of any damage that might prevent a tight seal. If you notice any defects, it's best to replace the fitting with a new one to ensure a safe and reliable installation.
Additionally, verify that the compression fitting is the correct size for the fuel line. Fuel lines come in various diameters, and using the wrong size fitting can result in an improper seal, leading to potential fuel leaks and engine performance issues. Measure the inside diameter of the fuel line and compare it to the specifications provided by the manufacturer of the fitting. Most compression fittings have a specific range of fuel line sizes they are designed to fit, so ensure that your fitting falls within this range. If you're unsure, consult the fitting's packaging or the manufacturer's website for detailed size information.
Before proceeding with the installation, it's a good practice to lubricate the fitting and the fuel line. A small amount of thread seal tape or pipe compound can be applied to the threads of the fitting and the fuel line to ensure a smooth and secure connection. This step helps to prevent the fitting from becoming stuck during installation and also provides an additional layer of protection against fuel leaks. Take your time with this process, ensuring that the lubricant is applied evenly and not in excess.
Once you've confirmed that the fitting is in good condition and the correct size, it's time to move on to the next step of the installation process, which typically involves inserting the fitting onto the fuel line and tightening it securely. Always follow the manufacturer's instructions for the specific compression fitting you are using, as different fittings may have unique installation requirements.
Mastering the Art of High-Pressure Fuel Line Connections: A Comprehensive Guide
You may want to see also
Install the Fitting: Slide the fitting onto the fuel line, apply pipe dope, and tighten securely
To install a compression fitting on a fuel line, you'll need to follow a few steps to ensure a secure and leak-free connection. First, gather the necessary tools and materials: a compression fitting, pipe dope (also known as thread seal tape or compound), and a wrench or pliers. It's important to use the correct size and type of fitting for your fuel line to ensure compatibility and a proper fit.
Now, let's get started with the installation process. Begin by sliding the compression fitting onto the fuel line. Ensure that the fitting is aligned correctly and that the fuel line is inserted into the fitting's grooves or channels. Take note of the direction of the fuel flow to ensure proper orientation. Once the fitting is in place, it's time to apply the pipe dope. A small amount of pipe dope should be applied to the threads of the fitting and the fuel line. Be careful not to use too much, as excess pipe dope can lead to leaks.
The next step is to tighten the fitting securely. Use your wrench or pliers to apply firm pressure and tighten the fitting hand-tight. You should feel the fitting make contact with the fuel line and hear a distinct click or feel a resistance when it's properly tightened. However, be careful not to over-tighten, as this can damage the fuel line or threads. A gentle, firm pressure is usually sufficient.
After tightening the fitting, check for any leaks by gently pressing around the fitting and looking for any signs of fuel escaping. If there are no leaks, you can proceed to the final step. To ensure a secure connection, it's a good idea to make one final adjustment by tightening the fitting slightly more. This additional tightening will help ensure that the fitting is sealed tightly and will prevent any potential leaks over time.
Remember, when working with fuel lines, it's crucial to prioritize safety and take your time with each step. Properly installed compression fittings will ensure a reliable and safe fuel system for your vehicle.
Mastering Fuel Line Removal: A Guide for 1997 Ford F150 Owners
You may want to see also
Frequently asked questions
A compression fitting is a type of connector used to join two fuel lines or a fuel line to another component, such as a fuel pump or filter. It works by compressing the fuel line material (usually rubber or plastic) into the fitting, creating a secure and leak-tight seal. This method is commonly used for fuel systems as it provides a reliable and durable connection.
Before installing a compression fitting, ensure the fuel line is clean and free of any debris or contaminants. Use a suitable solvent to remove any old sealant or adhesive. Measure and cut the fuel line to the appropriate length, ensuring it fits snugly inside the fitting. Prepare the fitting by removing any protective caps and cleaning the internal threads.
You will need a fuel line cutter, a deburring tool, a solvent, and a compression fitting of the correct size and thread type. Start by inserting the fuel line into the fitting, ensuring it is aligned properly. Use the deburring tool to remove any sharp edges from the fuel line and fitting. Apply a thin layer of fuel line sealant inside the fitting. Tighten the fitting onto the fuel line using a wrench, being careful not to overtighten. Test the connection for leaks and ensure it is secure.