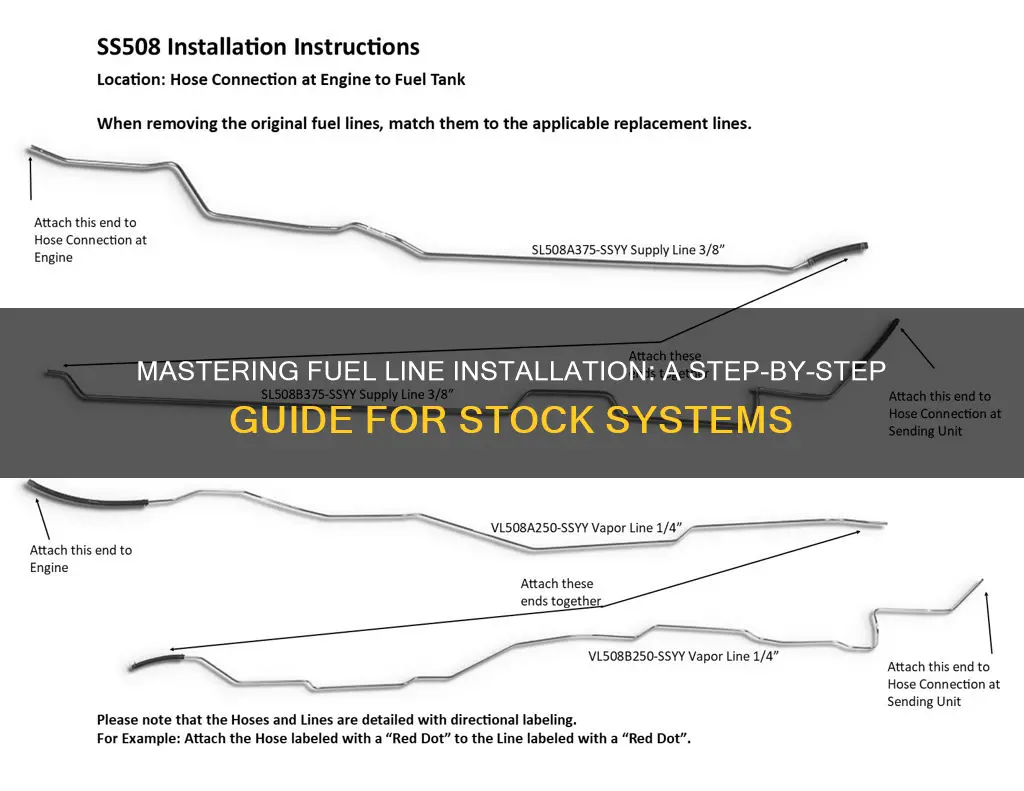
Installing a line on stock fuel lines can seem daunting, but with the right tools and a bit of patience, it's a manageable task. This guide will walk you through the process step-by-step, ensuring you have all the necessary information to complete the job safely and effectively. From preparing the materials to connecting the new line, you'll learn how to make the necessary modifications to your vehicle's fuel system.
What You'll Learn
- Prepare Tools: Gather necessary tools like fuel line cutters, crimping pliers, and a fuel line cleaner
- Inspect Stock Lines: Check for damage, leaks, and proper connections before replacing
- Cut and Measure: Accurately cut new fuel lines to length, ensuring a precise fit
- Crimp Connections: Securely crimp fittings onto the new lines, following manufacturer instructions
- Test and Clean: Verify no leaks, then clean the system to prevent contamination
Prepare Tools: Gather necessary tools like fuel line cutters, crimping pliers, and a fuel line cleaner
Before you begin the process of replacing or modifying stock fuel lines, it's crucial to ensure you have the right tools to make the job efficient and successful. Here's a breakdown of the essential tools you'll need:
Fuel Line Cutters: These specialized cutting tools are designed to precisely trim fuel lines without causing damage or leaving jagged edges. Look for cutters that can handle the thickness of your stock fuel lines. Having multiple sizes can be beneficial for different line diameters.
Crimping Pliers: Crimping pliers are essential for creating secure and leak-free connections. They allow you to crimp fuel line fittings onto the fuel lines, ensuring a tight seal. Choose a set with various sizes to accommodate different fitting types.
Fuel Line Cleaner: Cleaning the fuel lines is a critical step often overlooked. Over time, fuel lines can accumulate dirt, debris, and varnish, which can lead to reduced performance and potential blockages. A fuel line cleaner will help remove these contaminants, ensuring a clean and smooth installation process.
Additionally, consider having a fuel line inspection camera or borescope to visualize the interior of the fuel lines, especially if you're dealing with hidden or hard-to-reach areas. This tool can help identify any existing damage or issues before you start the installation. Remember, having the right tools not only makes the job easier but also ensures a professional-quality finish.
Unveiling the Mystery: Do Sisters Have a Reserve Fuel Line?
You may want to see also
Inspect Stock Lines: Check for damage, leaks, and proper connections before replacing
Before you begin any work on replacing fuel lines, it's crucial to thoroughly inspect the stock lines to ensure you understand the condition they are in. This initial step is often overlooked but is essential to avoid unnecessary replacements and potential safety hazards. Here's a detailed guide on how to inspect the stock fuel lines:
- Visual Inspection: Start by visually examining the fuel lines for any signs of damage. Look for cracks, punctures, or any visible tears in the line's outer covering. Check for any discolored areas, which could indicate internal damage or contamination. Inspect the connections at both ends of the line for any signs of wear or damage. Ensure that the lines are not kinked or twisted, as this can lead to reduced performance and potential leaks.
- Leaks and Spills: The next step is to check for leaks. This is a critical aspect of the inspection process. Turn on the fuel pump and listen carefully for any hissing or bubbling sounds, which could indicate a leak. You can also use a soapy water solution to create a foam and carefully inspect the lines for any bubbles forming, which would signify a leak. Check the ground around the fuel tank and lines for any signs of fuel spills or stains, as this could indicate a problem.
- Proper Connections: Ensure that all connections are secure and tight. Loosen the fuel pump's electrical connector and gently wiggle the fuel line to check for any loose connections. Tighten any loose fittings and ensure that the lines are not pinched or crushed against the tank or other components. Proper connections are vital to maintain the integrity of the fuel system.
- Documentation and Notes: As you inspect, take detailed notes on the condition of the lines, including any issues found. Document the location of any damage or leaks for reference during the replacement process. This step ensures that you have a clear understanding of the work required and helps in creating a comprehensive plan for the replacement.
By following these inspection steps, you can identify potential issues with the stock fuel lines, ensuring that any replacements are necessary and targeted. This approach also helps in maintaining the overall health and efficiency of the fuel system, promoting better performance and longevity.
Aluminum Fuel Lines: Pros and Cons for Your Engine
You may want to see also
Cut and Measure: Accurately cut new fuel lines to length, ensuring a precise fit
To ensure a successful installation of new fuel lines, the cutting and measurement process is crucial. Here's a step-by-step guide to achieving accurate lengths:
Step 1: Gather the Necessary Tools and Materials
Before you begin, ensure you have the required tools and materials. You'll need a fuel line cutter, preferably a specialized fuel line cutting tool designed for precision. This tool will allow you to make clean, straight cuts. Additionally, have the new fuel lines ready, ensuring they are the correct length for your specific application.
Step 2: Inspect the Existing Fuel Lines
Carefully examine the stock fuel lines to understand their routing and positioning. Identify any bends, kinks, or areas where the lines are worn or damaged. This inspection will help you determine the optimal path for the new lines and ensure they follow a similar route. Take note of any attachments or fittings that need to be retained or replaced.
Step 3: Measure and Mark the New Fuel Lines
Using the existing fuel lines as a guide, measure and mark the new lines at the required lengths. Start from the fuel source and measure along the path you've identified. Mark the points where the lines need to be cut, ensuring you account for any bends or changes in direction. Double-check your measurements to avoid errors.
Step 4: Cut the Fuel Lines with Precision
Using the fuel line cutter, carefully cut along the marked lines. Apply gentle pressure to ensure a clean cut. Avoid forcing the cutter, as it may cause damage to the surrounding material. Take your time to achieve a precise cut, especially if the lines have a specific diameter or thickness.
Step 5: Ensure a Secure Connection
When cutting the fuel lines, consider the type of connection required. If you're using quick-connect fittings, ensure you cut the lines at the appropriate length to accommodate these fittings. Test the connections to ensure they are secure and leak-free. For more permanent installations, you may need to use adhesives or heat shrink sleeves to create a tight seal.
By following these steps, you can accurately cut and measure new fuel lines, ensuring a precise fit during the installation process. This attention to detail will contribute to a successful and reliable fuel system setup.
Fuel Line Depressurization: Signs and Solutions for Your Vehicle
You may want to see also
Crimp Connections: Securely crimp fittings onto the new lines, following manufacturer instructions
When it comes to installing new lines on stock fuel lines, crimp connections are a crucial step to ensure a secure and reliable setup. Crimping fittings onto the lines provides a strong and permanent bond, allowing for a safe and efficient fuel delivery system. This method is often preferred due to its simplicity and the ability to create a robust connection without the need for additional tools or materials.
To begin the crimping process, gather the necessary tools and materials. You will typically require a crimping tool specific to the type of fitting you are using, along with the appropriate size of crimping dies. Ensure that the new lines are clean and free of any debris or contaminants before proceeding. Prepare the fittings by inserting the lines into the fittings, ensuring a snug fit. The key to a successful crimp is applying the right amount of force and using the correct technique.
Follow the manufacturer's instructions for your specific crimping tool and fittings. Generally, you will need to position the crimping tool over the fitting and line, then apply pressure to the handle, forcing the tool to compress the fitting onto the line. The amount of force required can vary, so refer to the guidelines provided. Hold the crimp in place for the recommended duration to ensure a solid bond. Repeat this process for each connection, taking care to align the fittings and lines properly.
After crimping, inspect the connections to ensure they meet the required specifications. Check for any signs of damage or imperfections in the crimp, and verify that the fitting is securely attached to the line. It is essential to double-check these connections, especially if you are working in a high-pressure environment. Properly secured crimp connections will provide a reliable fuel supply, minimizing the risk of leaks or fuel loss.
Remember, practice and attention to detail are vital when crimping connections. Take your time and follow the manufacturer's guidelines to achieve professional-quality results. With this method, you can create a robust and long-lasting fuel line installation, ensuring the safety and efficiency of your vehicle's fuel system.
Mastering Fuel Line Installation: A Guide to Fuel-Injected Car Success
You may want to see also
Test and Clean: Verify no leaks, then clean the system to prevent contamination
Before you begin the installation process, it's crucial to test and clean the fuel system to ensure optimal performance and prevent any potential issues. This step is often overlooked but is essential for a successful and safe fuel line installation.
Testing for Leaks:
Start by identifying the fuel lines and connections. Visually inspect the stock fuel lines for any signs of damage, cracks, or deterioration. Check for any loose fittings or connections that might cause leaks. You can use a soapy water solution to test for leaks. Apply the solution to the connections and watch for any bubbles, indicating a potential leak. If you find any leaks, tighten the connections or replace the damaged lines immediately. Ensure that all fuel lines are securely attached and free from any potential sources of leakage.
Cleaning the Fuel System:
Once you've verified that there are no leaks, it's time to clean the system. Contaminated fuel can lead to engine performance issues and potential damage. Here's a simple cleaning process:
- Drain the fuel tank: Start by draining the fuel tank to remove any old, contaminated fuel. This can be done by attaching a fuel pump or using a fuel transfer pump to pump the fuel into a clean container.
- Clean the fuel filter: Locate the fuel filter and remove it. Clean or replace the filter to ensure it is free from any debris or contaminants.
- Use a fuel system cleaner: Add a fuel system cleaner to the fuel tank according to the manufacturer's instructions. This cleaner will help dissolve any varnish, deposits, or contaminants in the fuel lines and injectors. Run the engine for a few minutes to allow the cleaner to circulate.
- Flush the system: After cleaning, flush the fuel lines and injectors with clean fuel. This step ensures that any remaining cleaner is removed, and the system is ready for fresh fuel.
- Reassemble and fill the tank: Reinstall the fuel filter and tank, ensuring all connections are secure. Refill the tank with fresh, clean fuel.
By thoroughly testing and cleaning the fuel system, you can ensure that the newly installed fuel lines will function optimally and that the engine receives clean, contaminant-free fuel. This process is a critical step often overlooked, but it plays a vital role in maintaining engine performance and longevity.
Nylon Fuel Line: Safe Usage Guide for Your Vehicle
You may want to see also
Frequently asked questions
Adding a fuel line can be beneficial for various reasons. It can improve fuel flow, especially in high-performance engines, by providing a dedicated path for fuel, reducing pressure drop and ensuring a consistent supply. This can lead to better engine performance, faster response times, and potentially higher power output.
There are a few signs that may indicate the need for an upgrade. These include fuel leaks, reduced engine performance, engine misfires, or a noticeable decrease in fuel efficiency. If you notice any of these issues, especially if they persist or worsen over time, it's a good idea to inspect your fuel lines and consider an upgrade.
While it is possible to install a fuel line yourself, especially if you have some mechanical experience, it is generally recommended to seek professional assistance. Fuel line installation requires precision and knowledge of engine systems to ensure proper routing, secure connections, and compliance with safety standards. A professional can also help identify any potential issues and ensure the work is done correctly.
Yes, you will need a few essential tools and materials. These typically include fuel line cutters or shears, fuel line connectors or fittings, a fuel line cleaner or solvent, and possibly a fuel line inspection camera for hard-to-reach areas. It's important to use the correct type and size of fuel line to ensure compatibility and safety. Additionally, having a workshop manual or guidance specific to your vehicle model can be very helpful during the installation process.