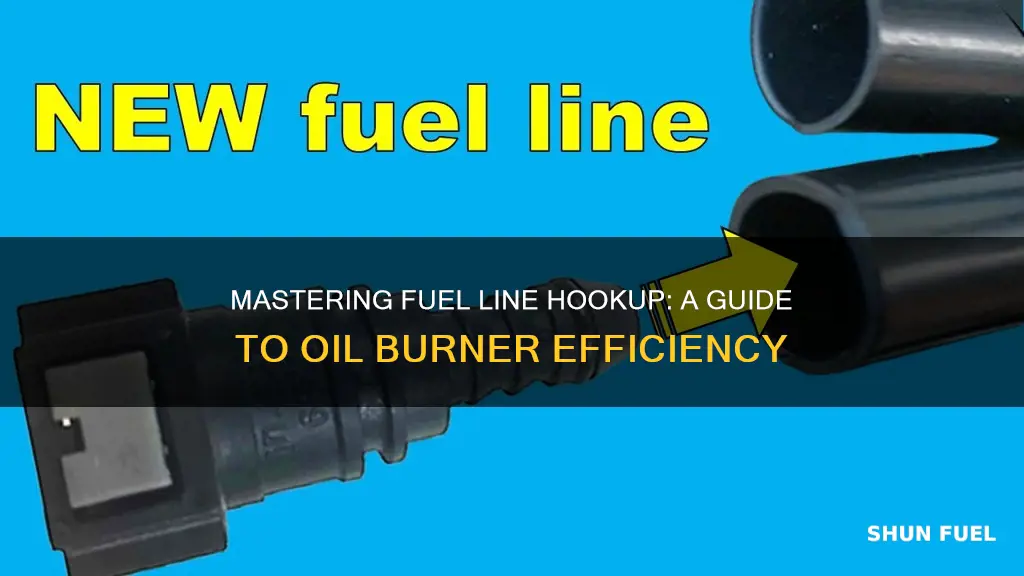
Hooking up a fuel line to an oil burner can seem daunting, but with the right tools and a bit of know-how, it's a manageable task. This guide will walk you through the process step-by-step, ensuring you understand the importance of proper connections and safety measures. By following these instructions, you'll be able to securely attach the fuel line, allowing your oil burner to function efficiently and safely.
Characteristics | Values |
---|---|
Fuel Type | Oil |
Application | Oil Burner |
Hooking Method | Direct Connection |
Fuel Line Material | Steel or Copper |
Size | 1/4" to 3/8" ID |
Pressure Rating | 15-20 psi |
Length | Varies based on burner location |
Fittings | Quick-Connect or Threaded |
Safety Features | Gas relief valves, pressure regulators |
Installation Steps | 1. Turn off power/fuel supply. 2. Disconnect old line. 3. Clean and prepare the fuel line. 4. Connect new line securely. 5. Test for leaks. |
What You'll Learn
- Fuel Line Material: Choose the right material for the fuel line, such as rubber or vinyl, to ensure compatibility with the fuel and burner system
- Fitting Selection: Use appropriate fittings, like quick-connect couplings or threaded fittings, for a secure and leak-free connection
- Fuel Pressure Regulation: Install a pressure regulator to maintain the correct fuel pressure, typically around 15-20 psi, for optimal burner performance
- Fuel Line Routing: Route the fuel line away from heat sources and sharp bends to prevent damage and ensure a stable fuel supply
- Leak Testing: After installation, perform a thorough leak test to identify and fix any potential issues before starting the burner
Fuel Line Material: Choose the right material for the fuel line, such as rubber or vinyl, to ensure compatibility with the fuel and burner system
When it comes to connecting a fuel line to an oil burner, selecting the appropriate material for the fuel line is crucial to ensure optimal performance and longevity. The fuel line serves as the conduit for transporting fuel from the tank to the burner, and its material must be compatible with the fuel type and the overall burner system.
Rubber and vinyl are the most commonly used materials for fuel lines due to their flexibility and durability. Rubber fuel lines are known for their excellent resistance to fuel degradation, making them a popular choice for oil burners. They can withstand the corrosive nature of some fuels and provide a reliable seal, preventing fuel leaks. However, it's important to choose a high-quality rubber material to ensure it can handle the temperature and pressure variations associated with fuel transport.
Vinyl fuel lines offer another viable option, especially for those seeking a more cost-effective solution. Vinyl is lightweight and flexible, making it easy to install and route through the burner system. It is also resistant to abrasion, which is beneficial when dealing with fuel lines that may need to pass through tight spaces or around various components. Additionally, vinyl's compatibility with a wide range of fuels makes it a versatile choice.
The choice between rubber and vinyl depends on specific application requirements. For high-temperature environments or when dealing with fuels that have a higher degree of volatility, rubber might be the preferred material due to its superior resistance to heat and fuel degradation. On the other hand, vinyl's affordability and ease of installation make it an attractive option for simpler burner systems or when a lightweight solution is desired.
In summary, when connecting a fuel line to an oil burner, it is essential to consider the fuel line material carefully. Rubber and vinyl are the go-to choices, each offering unique advantages. Rubber provides excellent fuel resistance and durability, while vinyl is lightweight, flexible, and cost-effective. Selecting the right material ensures compatibility, prevents fuel leaks, and contributes to the overall efficiency and safety of the oil burner system.
Rubber Hose for Fuel Line Fixes: A Viable Option?
You may want to see also
Fitting Selection: Use appropriate fittings, like quick-connect couplings or threaded fittings, for a secure and leak-free connection
When connecting fuel lines to an oil burner, the choice of fittings is crucial for ensuring a secure and reliable setup. The primary goal is to prevent leaks, which can lead to dangerous situations and costly repairs. Here's a detailed guide on why and how to select the right fittings:
Quick-Connect Couplings: These are an excellent choice for fuel line connections due to their ease of use and reliability. Quick-connect couplings feature a simple push-on/pull-off mechanism, allowing for a fast and secure attachment. They are typically made of durable materials like brass or stainless steel, ensuring they can withstand the pressure and temperature fluctuations associated with fuel systems. Look for couplings with an O-ring or gasket to create a tight seal, preventing any fuel from escaping. This type of fitting is ideal for temporary connections or when frequent adjustments are required.
Threaded Fittings: Threaded connections offer a more permanent and secure solution for fuel line installations. These fittings use male and female threads to create a tight seal when tightened. Threaded fittings are available in various materials, including brass, steel, and plastic, each with its own advantages. For instance, brass fittings are known for their corrosion resistance, making them suitable for indoor installations. Steel fittings, on the other hand, are stronger and more durable, often used in outdoor or high-pressure applications. When using threaded fittings, ensure that the threads are clean and free of debris, and apply a suitable thread sealant to prevent leaks.
The key to a successful fuel line connection is to match the fitting material and size to the fuel line's specifications. Using the right fittings ensures that the connection is tight enough to prevent fuel leakage but not so tight that it causes damage to the fuel line or fittings. Additionally, consider the environment in which the fuel line will be installed, as this may influence the choice of material to withstand potential corrosion or temperature extremes.
In summary, selecting the appropriate fittings is a critical step in the process of hooking up a fuel line to an oil burner. Quick-connect couplings offer convenience and speed, while threaded fittings provide a more permanent and secure solution. Both options should be chosen based on the specific requirements of the fuel line and the overall system design to ensure a safe and efficient operation.
Line Fuel Demand Valve: Unlocking Engine Efficiency and Reliability
You may want to see also
Fuel Pressure Regulation: Install a pressure regulator to maintain the correct fuel pressure, typically around 15-20 psi, for optimal burner performance
Fuel pressure regulation is a critical aspect of ensuring optimal performance and efficiency in oil-burning systems. When setting up an oil burner, it's essential to maintain the correct fuel pressure, typically ranging from 15 to 20 pounds per square inch (psi), to achieve efficient combustion. This range is crucial as it allows for proper atomization of the fuel, ensuring that it mixes effectively with air for complete burning, which in turn maximizes energy output and minimizes emissions.
To regulate fuel pressure, you can install a pressure regulator, a device specifically designed for this purpose. These regulators are typically located between the fuel supply and the burner, acting as a gatekeeper for pressure. When selecting and installing a pressure regulator, consider the following:
- Pressure Rating: Choose a regulator that can handle the maximum expected fuel pressure in your system. For oil burners, a pressure rating of 15-20 psi is common, but it's essential to check the specific requirements of your burner and fuel system.
- Flow Capacity: Ensure the regulator can handle the fuel flow rate of your burner. This is crucial to prevent pressure drops and maintain consistent performance.
- Material and Compatibility: Opt for materials that are compatible with your fuel type and system. Common materials include brass, bronze, and stainless steel, each offering different advantages in terms of durability and corrosion resistance.
Installing a pressure regulator involves a few steps. First, locate a suitable mounting point on the fuel line, preferably close to the burner but before any pressure-altering components. Secure the regulator to the fuel line using the appropriate fittings and ensure a tight seal. Then, connect the regulator's inlet to the fuel supply and the outlet to the burner, maintaining the correct orientation to ensure proper flow direction.
After installation, it's crucial to test the system to ensure the pressure regulator is functioning correctly. Use a pressure gauge to measure the fuel pressure at various points in the system, including the regulator's outlet and the burner. Adjust the regulator as needed to fine-tune the pressure to the desired range. Regular maintenance and periodic checks of the pressure regulator are essential to ensure the long-term reliability and efficiency of your oil-burning system.
Saturn Ion 2 Fuel Lines: Nylon or Steel?
You may want to see also
Fuel Line Routing: Route the fuel line away from heat sources and sharp bends to prevent damage and ensure a stable fuel supply
When setting up an oil burner system, proper fuel line routing is crucial to ensure optimal performance and longevity. One essential practice is to route the fuel line away from heat sources and sharp bends. This approach helps prevent damage to the fuel line and ensures a stable fuel supply to the burner.
Heat sources, such as hot water pipes, radiators, or even the exhaust system, can cause the fuel line to expand and contract rapidly, leading to potential damage over time. By keeping the fuel line at a safe distance from these heat sources, you minimize the risk of thermal stress and potential leaks. It is recommended to maintain a minimum distance of a few inches between the fuel line and any heat-generating components.
Additionally, sharp bends or kinks in the fuel line can restrict fuel flow and create pressure points, which may lead to fuel line failure. To avoid this, the fuel line should be routed in a straight and smooth manner whenever possible. If sharp bends are necessary, ensure they are gradual and well-radius to reduce stress on the fuel line. Consider using flexible fuel line adapters or elbows to create gentle bends, especially in tight spaces.
Avoiding sharp bends is particularly important when connecting the fuel line to the burner. The fuel line should enter the burner at a gentle angle, avoiding any abrupt changes in direction. This practice helps maintain a consistent fuel flow and reduces the chances of fuel line blockage or damage.
In summary, when hooking up a fuel line in an oil burner, it is imperative to route the line away from heat sources and sharp bends. By following this practice, you can ensure the fuel line's integrity, promote a stable fuel supply, and extend the overall lifespan of your oil burner system. Proper routing is a fundamental aspect of system maintenance and will contribute to efficient and reliable operation.
Black Fuel Line: Is It Superior to Yellow?
You may want to see also
Leak Testing: After installation, perform a thorough leak test to identify and fix any potential issues before starting the burner
After completing the installation of the fuel line for your oil burner, it is crucial to conduct a comprehensive leak test to ensure the system's integrity and prevent any potential issues. This step is essential to identify and rectify any leaks or connections that might compromise the burner's performance and safety. Here's a detailed guide on how to perform this critical test:
Preparation: Before initiating the leak test, ensure that the burner is turned off and disconnected from the power source. This safety precaution is vital to prevent any accidental ignition or damage during the testing process. Gather the necessary tools, including a soapy water solution, a spray bottle, and a clean cloth. The soapy water will be used to detect leaks, and the spray bottle will help in applying the solution effectively.
Leak Test Procedure: Start by inspecting all connections and joints where the fuel line is attached to the burner, pump, and other components. Apply a thin layer of the soapy water mixture to these areas, ensuring complete coverage. Then, use the spray bottle to gently mist the connections, allowing the soapy water to flow and create a visible bubble trail if there is a leak. Leaks will be indicated by the formation of bubbles, which will appear as a frothy, bubbly stream. If you notice any bubbles forming, it signifies a potential leak at that specific point.
Pay close attention to the fuel line's path, as leaks can occur at various points along the line, including where it connects to the pump and the burner itself. Inspect the line for any signs of damage, corrosion, or improper installation, as these issues can also lead to leaks. Once you've identified potential leak sites, carefully clean the areas and tighten any loose connections to ensure a proper seal.
Troubleshooting and Repairs: If you detect any leaks during the test, it is imperative to address them immediately. Start by identifying the source of the leak, which could be a faulty connection, a damaged fuel line, or a poorly installed component. Once identified, disconnect the affected part and replace it with a new, compatible component. Ensure that all connections are tightened securely and that the replacement part is compatible with the existing system. After each repair, re-test the system to ensure the leak has been successfully resolved.
Completing the Test: After addressing all identified leaks, re-connect the fuel line and power source to the burner. Turn it on and allow it to run for a short period to ensure that the system is functioning correctly. Monitor the burner's performance, and if no further leaks are detected, you can proceed with the final start-up procedure. However, if any new leaks appear, repeat the leak test and troubleshooting process until the system is leak-free.
Remember, a thorough leak test is a critical step in the installation process, ensuring the safety and efficiency of your oil burner system. It allows you to identify and fix potential issues before they become major problems, saving you from costly repairs and ensuring the longevity of your equipment.
The Mysterious Motive: Eugene's Fuel Line Fiasco
You may want to see also
Frequently asked questions
When hooking up the fuel line to the oil burner, it's crucial to ensure a secure and leak-free connection. Start by cleaning the fuel line and the burner's fuel inlet to remove any dirt or debris. Then, use a fuel line connector or clamp to attach the line firmly. Make sure the connection is tight and there are no bends or kinks in the line, as these can cause fuel leaks and reduce efficiency.
Before making any connections, inspect the fuel line for any signs of damage, cracks, or leaks. Check the burner for proper alignment and ensure that all components are in good working order. It's essential to identify and fix any issues with the burner or fuel system beforehand to prevent potential problems during the hook-up process.
You'll need a few essential tools for this job. A fuel line cutter or a pair of sharp scissors will help you trim the line to the correct length. Additionally, having a fuel line solvent or adhesive can aid in creating a secure connection. It's recommended to use a fuel line clamp or connector designed for the specific fuel type you're using to ensure a reliable seal.